Interview conducted by Mychealla RiceDec 20 2016
In this interview, Jeff Roblee, VP of Technology, and Ed Freyenhagen, Director of Engineering, talk about key applications for ultra precision machining in the automotive industry and the enabling technologies that make realizing them possible.
Why are your customers starting to use ultra precision manufacturing techniques more these days for automotive applications?
There are many new features that automobile companies are developing into their products to enhance them and add functionality. Many of these new features require or can be made better by using ultra precision manufacturing techniques.
What are some of these new applications and how does ultra precision bring value to them?
The most interesting automotive applications that we commonly see are for head up displays (HUDs). Newer applications include ones such as infrared optics for LIDAR (light detection and ranging) systems for self-driving vehicles, animal and people detection systems.
Also cars are now coming with cameras for backup and parking assistance which require imaging optics. Other applications are being improved with ultra precision manufacturing techniques such as LEDs for enhanced interior illumination, signal lamp bezels, and head lamp optics.
What are some challenges that arise in making these types of parts using ultra precision manufacturing techniques versus making them with conventional machining methods?
For more common ultra precision applications such as infrared and imaging optics the first challenge is cost. Competitiveness in the automotive market requires lower cost lenses, which means they need to be made faster. This can make programming a challenge.
Additionally, with ultra precision we program our tools to 1 nm and most CAD systems do not create programs to this accuracy. For freeform applications, for which the surfaces to be made cannot be defined by a formula, CAD models are needed. The freeform shape of many LED lighting and signal lamp bezel applications push the limits of existing CAD tools. For these reasons advanced methods must be developed.
.jpg)
What ultra precision manufacturing techniques can be used to make parts faster?
Turning processes are much faster than milling processes and two technologies come to mind that that can benefit the turning of freeform surfaces. The first is called fast tool servo (FTS).
This method of manufacturing rapidly moves the tool in coordinated motion with the spindle and axis positions allowing parts to be manufactured faster. Second is software called Adaptive Control Technology (ACT). Anytime you are moving the axis of a machine tool in a coordinated way to manufacturer a freeform (non-rotationally symmetric) part the dynamic errors of the machine contribute to deviations from the ideal shape of the final part.
ACT is a learning algorithm that detects and eliminates repeatable errors in this type of manufacturing method. Both the Precitech FTS and ACT software help make parts faster than with traditional techniques.
How can the programming challenges associated with the CAD system accuracy be overcome in the applications you mentioned above?
DIFFSYS software which has historically been used to create tool paths for all brands of ultra precision machine tools has made several advances in the area of freeforms.
One of these is with the integration of tools that allow programmers to use a cloud of points from a surface defined in a CAD model to create tool paths. This is critical for freeform surfaces that cannot be defined easily by optical equations.
What types of material are typically used to create molds for automotive applications and can steel be used?
Traditionally, since steel is a ferrous metal, it cannot be machined with a diamond. However, there are many reasons why one would want to use steel due to its hardness, which makes it resistant to damage during the molding process. Typically nickel plated steel or aluminum are used, which are not as robust.
On the other hand, there have been advancements recently in ultra-sonic assisted machining that have started to change the traditional rule that only non-ferrous metals can be diamond turned.
What key technologies enable ultra precision machine tools to be used for automotive applications?
As Jeff mentioned two key technologies for turning operations are fast tool servo (FTS) and adaptive control technology (ACT). One that Jeff did not mention is ultra precision milling which is another method to make freeform shapes on molds required for head lamp optics. For some mold patterns due to physical limitation in the shape of diamond tools, milling may be required instead of the faster turning process.
With regards to fast tool servo (FTS) and milling technologies what are the key considerations one should be aware of when manufacturing head lamp molds?
For FTS applications it is all about speed and accuracy. With a peak acceleration of 30 Gs and a fully integrated programming and operating interface the Precitech fast tool servo with Fastcom III control has benefits in both these areas. The story for milling is the same, speed and accuracy are critical considerations.
The Levicron milling spindle has a top speed of 80,000 rpm which is faster than other ultra precision milling spindles. It is extremely thermally stable and has low error motions, making it accurate.
How does Adaptive Control Technology (ACT) enable better manufacturing of head-up display molds?
In XZC turning, which is often referred to as slow tool or slow slide servo, the dynamic errors of the machine can be significant. By going slower these errors are reduced. However, going slower decreases productivity which increases cost. Also thermal errors can be introduced as temperature cycles effect the accuracy of the machine.
This is more predominant on parts that take a long time to make such as freeforms. Ultimately ACT reduces the dynamic errors of the machine in XZC turning applications allowing you to go faster than you could without ACT, which has obvious benefits.
This is one of the reasons we refer to this method as XZC turning instead of using the word slow. With ACT it does not need to be slow.
Most people in the precision manufacturing field are aware of automated tool changing when it comes to milling precision components. How has this concept been applied to ultra precision machining and what have been some of the challenges?
Like everything in ultra precision it comes down to the sub-micron level. With automated tool changing the challenges are making tool holders that are balanced enough for ultra precision applications and a tool changing system that is repeatable enough so that the new tool is in the same place as the previous one.
Levicron has solved both of these challenges with their milling spindle and custom build HSK tool holders.
How does automated tool changing help with the ultra precision manufacturing of automotive components?
Specifically for corner cube applications used for signal lamp bezels and reflector molds. In order to make these productively and also finish them with an optical surface and sharp corners several tools are required.
Using a milling system that allows for tools to be changed quickly without multiple tool setups makes the process viable for automotive applications.
What’s in store for the future of Precitech?
We are always working on exciting new things. Specific to automotive applications, we plan to continue to make enhancements to DIFFSYS that make programming the tool path for complicated freeforms more accurate.
We also plan to further integrate the operation of our fast tool servo system to speed up the process of making some of the molds used in automotive applications.
Where can our readers go to find out more?
We have applications notes, videos, and brochures dealing with many automotive applications. These are all available on our website. www.precitech.com.
Or come see us at the Photonics West show in San Francisco, CA from 31 Jan-2 Feb 2017. Booth 2035C.
About Ed Freyenhagen
Ed Freyenhagen is the Director of Engineering at Precitech. In this role he oversees all mechanical and electrical engineering associated with sustaining and new product development at Precitech.
Before Precitech Ed worked at Markem Imaje working as an electrical engineer.
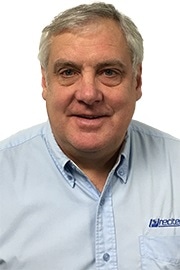
About Jeff Roblee
Dr. Jeffery Roblee joined AMETEK Precitech in 2002, and he is the Divisional Vice President of Technology.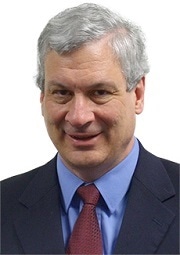
Dr. Roblee began his engineering career at Lawrence Livermore National Laboratory in 1977.
Dr. Roblee holds a number of patents and awards, and he has presented numerous papers on temperature control, machine dynamics, air bearing design, optics fabrication and optomechanics.
He is an active member of the European Society of Precision Engineering and Nanotechnology, and the American Society of Precision Engineering.
From 2007 to 2009, he has been a member of the Board of Directors of ASPE, and he served as its President in 2008. Jeffrey W. Roblee has a M.S. and Ph.D., both in mechanical engineering, from the University of California at Berkeley
Disclaimer: The views expressed here are those of the interviewee and do not necessarily represent the views of AZoM.com Limited (T/A) AZoNetwork, the owner and operator of this website. This disclaimer forms part of the Terms and Conditions of use of this website.