Aluminium extrusions are used widely within the building industry. The strength, low density, corrosion resistance and design flexibility of aluminium make it an ideal material for building applications ranging from a louvre blade in an air conditioning system to a structural support in a roofing system. About half of all aluminium extrusions produced in the UK are used in building. This amounts to around 60,000 tonnes each year. Of this, approximately 27,000 tonnes are used in applications such as commercial windows, shopfronts, partitioning, curtain walling, patent glazing, conservatories, glasshouses, roofing, scaffolding, road furniture and signs, architectural hardware, heating and ventilation, expansion joints, and car park barriers. A further 20,000 tonnes are dedicated to the home improvement sector of the market for replacement windows and secondary glazing, domestic and entrance doors. The remaining tonnage reaches the building industry via stockholders.
Grade 6063 Aluminium - The Mainstay
The main aluminium alloy used within the building industry is 6063 (a magnesium-silicon alloy with 0.45-0.9% Mg, 0.20.6% Si). The strength, design flexibility and corrosion resistance of this alloy are well in excess of the requirements of most major construction projects. Indeed, 6063 extrusions have been used on North Sea oil rigs. Research effort within the aluminium industry has therefore been largely devoted to creating new finishes and to developing new processes to exploit aluminium's versatility, to allow architects and builders to make full creative use of the material without compromising its practical advantages.
Aluminium Windows
The first extensive use of aluminium extrusions in buildings was window sections during the aluminium replacement window boom thirty years ago. The potential of aluminium for other sectors of the building industry was recognised, and use of aluminium extrusions has steadily increased. The window market has developed and diversified. The high strength and low overall weight of aluminium extrusions make them suitable for a wide variety of window styles, with slimmer profiles than would be possible with either wood or UPVC, without compromising safety, security or durability. In public sector housing, many local authorities specify aluminium to replace timber or steel because it can be used for a variety of styles while retaining the architectural integrity of anything from a high rise apartment block to a listed building. Further advantages in such applications are its minimal maintenance requirements and high resistance to vandalism and fire damage.
Aluminium is also incorporated into many windows and doors constructed largely from other materials. Windows and doors made from UPVC are made rigid with aluminium inserts, and locks and frame furniture are made secure by screwing them directly into aluminium located within the profile. The material is also widely used in conservatory roof structures, even in wooden and UPVC conservatories, as its strength and lightness ensure that wind and snow loading regulations are met, while retaining the slim glazing bars typical of Victorian and Edwardian styling.
Curtain Walling
Over the past ten years, the largest advances in the building industry have been in curtain walling, which has increased the demand for shaped extrusions. To satisfy the need for consistently creating bends to close tolerances, Indalex has developed its own stretch form bending machine. This first stretches the extruded section until it approaches its ultimate yield point, then wraps it around a plywood former to achieve the specified radius. This is a radical improvement on traditional roll bending, offering a greater ability to hold dimensional accuracy, a high degree of consistency between bends, no deterioration of surface finish, and an ability to produce radii up to eight times the depth of the section in the plane of curvature. However, its successful operation requires the metal to be in its unaged condition. Problems associated with natural ageing are avoided by delivering aluminium extrusions for stretch forming immediately after extrusion.
Recent examples of applications of curved aluminium extrusions include Sage Group plc's corporate headquarters in Newcastle-upon-Tyne, which features extrusions in the atrium and curtain walling elements of the building, figure 1. The 6000 m2 building includes offices grouped into eight areas, on two storeys, each centering around an atrium reception space. The atrium is covered with a long hooped roof of tinted double glazing set in aluminium frames. The atrium’s curved roof, fire screen walls and exterior curtain walling are based on a structural box system, essentially a glass envelope supported by aluminium and rubber gaskets which are in turn supported by reinforced concrete or steel.
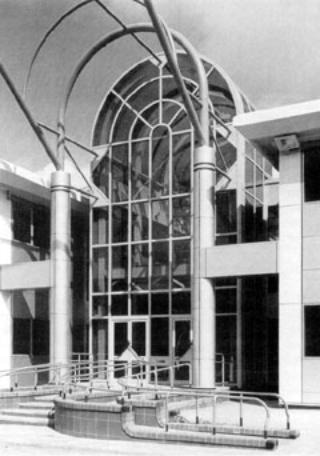
|
Figure 1. The Sage Group building.
|
Curved extrusions also feature significantly in the North Terminal extension at Gatwick Airport, figure 2. The profiles form the curtain wall grid work, and house the 6 mm grey antisun outer pane as well as an 8.8 mm clear laminated inner pane, to create a 25 mm thick double glazed panel. The curved sections are incorporated at roof level and comprise three parts - a mullion which is the main supporting member, a pressure plate which holds the exterior panels in position, and a capping extrusion to cover the pressure plate.
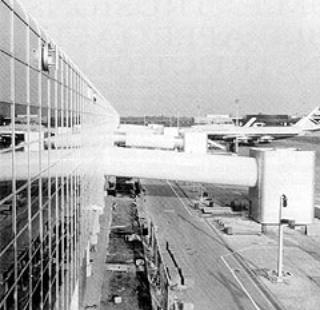
|
Figure 2. Over 200 tonnes of aluminium extrusions were used in Gatwick’s Pier 4.
|
Thermal Barriers
One of the potential drawbacks of aluminium is its high thermal conductivity, which can lead to significant heat loss through a window or door. One method widely used in the building industry to minimise this problem involves pouring a polyisocyanate resin into a channel designed into the extrusion; the back of the channel is then cut away to create a thermal barrier between what are now separate sections. Indalex has developed its own rigid thermal barrier (RTB) system, figure 3, for use in specialist commercial glazing and curtain walling installations to provide improved (and specifiable) thermal performance in line with building regulations.
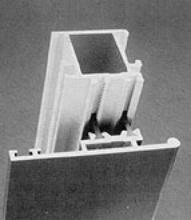
|
Figure 3. A specially designed aluminium thermal barrier system.
|
The RTB system is based on two different extruded sections, each with two slots for an extruded polyamide strip. The first operation knurls the edges of these slots where they will meet the polyamide, which is then inserted along the length of the section. The slots are rolled together to form a firm joint between the two polyamide strips and the extruded sections. This joint is tesed in shear to ensure minimum value of 25 MN.m-2 on a 100 m sample at ambient temperatures. Various size of thermal gap are available.
The Future
Continuing co-operation between extruders and specifiers aims to ensure that aluminium can meet the demands placed upon it in the future. Aluminium extrusions will continue to feature extensively in building applications particularly as their ease of recycling is likely to become increasingly significant.
|