A polymer is a chemical compound that contains a large number of identical molecular repeating units. A plastic material is a polymer, typically modified with additives, which can be molded or shaped under reasonable conditions of pressure and temperature.
It is generally a solid at room temperature and can be differentiated from a rubber/elastomer by a lack of reversible elasticity and having a higher stiffness/modulus. A thermoplastic is a plastic material that will melt when heated and harden when cooled. This hardening by cooling and melting by heat can be repeated, which enables thermoplastic materials to be recycled.
Synthetic Polymers
Most commercially available rubbers/elastomers and polymers are made up of molecules based on the element carbon; which means they are organic. They are produced or synthesized from simple, oil-based raw materials known as monomers.
A process, called polymerization, connects these simple low molecular weight materials together to produce polymers, which comprises of long chains made up of many identical repeat units. Rubbers and polymers based on one monomer are called “homopolymers”, while those based on two (or more) monomers are called ‘copolymers’.
These materials may be branched, linear or “cross-linked” (two or more polymer chains are linked together). Usually, polymer chains of a broad range of lengths (chains of different molecular weight) exist in commercial materials.
As the final molecular weight (and size) is usually large, these materials are often called “macromolecules” or “high polymers”. While a high molecular weight is essential to acquire practical properties (such as strength and stiffness) in a plastic material, it also means that the material is not easy to process.
All polymers are not plastics; but all plastics are polymers. For instance, cellulose is a polymer; but, it cannot be processed in the same way as a plastic material unless it is modified.
Long Chain Structure
The “macromolecules” or “high polymer molecules” that are used in plastics are very long. There may be, for instance, 50,000 atoms connected together in a long chain-like structure or molecule. Due to the structure of the carbon to carbon bond on which they are based, the chains are not often straight, but are coiled or twisted. The chains also have a distribution of varied lengths because of the nature of the polymerization reactions.
When there is no order present in the system (an amorphous material), the chains choose to exist in a random, coiled-up state (similar to the shape acquired when a piece of string is dropped on the floor). The separate long chain molecules (or “chains”) are also normally intertwined together.
If polymer crystallization is possible, then the chains, or parts of the chains, may either lie side-by-side in a highly orderly fashion or fold back on themselves. The enormous length of the chains and the entanglements between them stop thermoplastic materials from crystallizing fully upon cooling. This is the reason why they are known as “semi-crystalline thermoplastics”. Such materials have both amorphous and crystalline regions.
Amorphous Thermoplastics
Thermoplastic materials can be split into semi-crystalline materials and amorphous materials. An amorphous thermoplastic is typically a glassy, hard material that becomes rigid and transparent in the unfilled state. This kind of plastic material lacks a sharp melting point, but softens to a melt across a wide range of temperature.
Therefore, it can be processed or molded across a comparatively broad temperature range. A key advantage of amorphous polymers is their low and steady shrinkage, relative to that of semi-crystalline materials. As the natural color of an amorphous material is usually a clear, water-white, a very broad range of opaque or transparent colors may be produced.
Typical amorphous polymers include polymethylmethacrylate (PMMA), polystyrene (PS), styrene acrylonitrile (SAN), polysulfone (PSU or PES), polycarbonate (PC), and polyvinyl chloride (PVC). Acrylonitrile butadiene styrene (ABS) and modified polyphenylene oxide (PPO-M), while not usually transparent, are based on amorphous thermoplastic materials.
Semi-Crystalline Polymer
The quantity of crystalline material (% crystallinity), in an extrudate produced from a polymer that forms crystals, is typically not 100%. Amorphous areas are constantly present, so these materials are called semi-crystalline.
Typical semi-crystalline polymers are polyphenylene sulfide (PPS), polyamides (PA 6 and PA 66), polyacetal (POM), polybutylene terephthalate (PBT), low-density polyethylene (LDPE), polyethylene terephthalate (PET), high-density polyethylene (HDPE), and polypropylene (PP).
Semi-crystalline polymers are generally tough, malleable, durable, and possess a good chemical resistance. These polymers are usually not clear as their crystal structures contain scatter light. Semi-crystalline polymers could have a sharp melting point or, more typically, a moderately narrow melting point range.
Considerable care is needed in their processing. The properties of formed components may be significantly affected by the crystalline morphology (structure) and the degree of crystallization that occurs during solidification. Additionally, semi-crystalline polymers display greater shrinkage variations compared to amorphous polymers. Therefore, a greater stress on the uniformity of cooling is needed when forming a semi-crystalline material.
Orientation
Melt processing techniques are used in the most commercially important polymer conversion processes, where the polymer is heated and allowed to flow. All polymers in the melted form are amorphous, meaning they do not have any structure.
When the polymer flows, the polymer chains begin to slip, or slide, over each other while rotating around the carbon-to-carbon bonds. Layers slip one over the other and this is called shear or laminar flow. As the individual polymer molecules move relative to each other, they may change their orientation or direction due to friction between layers and chain entanglements.
In the direction of flow, the chains become “drawn out”. Due to rapid cooling frequently used in polymer processing, this orientation could be “frozen-in” and the product will contain frozen-in strains or frozen-in stresses. Therefore, these products contain molecules that are orientated in the direction of flow, which signifies that there is a “grain effect” present – similar to that present in wood. Due to the grain, the wood is stronger in a single direction than it is in another.
As a result of orientation, thermoplastic products may be a lot stronger in one direction than in another; meaning the product is anisotropic. Commercial use is composed of this “uni-axial” effect in extrusion in the development of the tape used for strapping packages. Biaxial orientation (orientation in two perpendicular directions) enables the formation of stiff, strong, film from brittle polymers, such as polystyrene (PS).
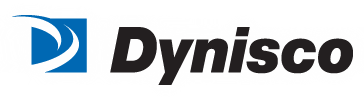
This information has been sourced, reviewed and adapted from materials provided by Dynisco.
For more information on this source, please visit Dynisco.