The use of plastic materials globally has greatly increased over the past five decades, and currently more than 100 million tons of these materials are used. In terms of tonnage, thermoplastics are considered the most significant, as they are roughly 80% of all plastics used around the world.
Advantages of Plastics
Plastic materials are used extensively as they can be molded into complex components, or shapes, fairly easily. They also have a useful combination of properties that can be altered for use in a broad range of applications.
Some of these appealing properties (which are not possessed by any one single plastic) include resilience, physical strength, corrosion resistance, electrical insulation, elasticity, chemical resistance, broad color range, lightness in weight, thermal insulation, and moldability.
Therefore these materials are versatile in their applications. Their use often makes production simple, because they allow a number of discrete parts to be added into a single component. The simplicity with which intricate parts may be manufactured from plastic compositions at high speed, in many cases outweighs the drawbacks of plastic materials. Eye-catching decoration of such products enhances their sales appeal.
However, thermoplastic materials sometimes lack stiffness, strength, fire resistance, and temperature resistance. Certain plastics not only burn fairly easily, but also evolve large quantities of fumes and smoke when they do burn. Many plastic components will change their dimensions or will creep if subjected to moderately small loads for extended periods of time.
Environmental stress cracking (ESC), changes in dimensions with humidity and temperature, and an unexpected change from tough to brittle behavior are the other factors that must be examined before using thermoplastics.
Major Thermoplastic Materials
Thermosetting plastics (thermosets) and thermoplastics are the two main categories of plastic materials. Due to the commercial significance of thermoplastic materials, this article will focus on their extrusion processing.
This key group of materials has been divided into four categories:
- Bulk or commodity thermoplastics
- Engineering thermoplastics
- Thermoplastic elastomers or rubbers
- Blends and/or alloys
Commodity thermoplastics, such as the polyolefins (polyethylene and polypropylene), styrene-based plastics, and polyvinyl chloride plastics comprise of the main tonnage of material produced.
Commodity or Bulk Thermoplastics
The use of polyolefins has increased dramatically in recent years due to their cost-effectiveness and versatility, and their relative simplicity of manufacture from readily available monomers. Both copolymers and homopolymers in this group are available, as are thermoplastics and rubbers materials.
The members of the polyethylene group include low density polyethylene (LDPE), linear low-density polyethylene (LLDPE), very low density polyethylene (VLDPE), and high-density polyethylene (HDPE). The term polyethylene (PE) covers a wide number of materials.
A new group of these resins has been produced recently using “single site constrained geometry” or “metallocene” catalysts. These catalysts enable the development of copolymers and homopolymers with molecules of a more even structure and size.
The term polyvinyl chloride (PVC) plastic refers to copolymers and homopolymers, both of which can be used with or without plasticizers. This creates plasticized grades (PPVC) and unplasticized grades (UPVC).
Styrene-based plastic also refers to a variety of materials such as the copolymer styrene-acrylonitrile (SAN), the homopolymer polystyrene (PS), acrylonitrile-butadiene-styrene (ABS), and the rubber-toughened material called high impact polystyrene (HIPS).
The significance of commodity thermoplastics cannot be overstressed because of their high volume of production and application. The introduction of new catalyst systems (for instance, metallocenes) will further boost the usage of bulk thermoplastics, as new varieties of polymer may be manufactured.
It is also being realized that the properties of this group of materials can be upgraded, so they can contend with many more high-end engineering thermoplastics.
Engineering Thermoplastics
Engineering thermoplastics commonly refers to materials that can be used to substitute glass, metal, or wood in manufactured products. They include both semi-crystalline and amorphous polymers.
These plastics, characterized by features such as high strength, impact resistance, stiffness, fire resistance, and temperature resistance are extensively used in transportation, automotive, electronics, appliance, aerospace, and communications applications.
These materials are manufactured in smaller volumes than commodity plastics, but they demand a much higher price. Materials that fall under the engineering thermoplastics category include: polyethelene terephthalate (PET), polycarbonate (PC), polyoxymethylene (acetal), polybutylene terephthalate (PBT), polymethylmethacrylate (PMMA), polysmide (nylon), and acrylonitrile-butadiene-styrene (ABS).
New Material Supply
Manufacturers or distributors of raw materials can deliver a material as, for instance, either transitional material or as prime grade material. Some may also deliver reclaimed material. Prime grade material or virgin material (or as first grade material or as first pass material) is a thermoplastic material (in the form of granules or pellets) that has not been subjected to use, or processing, other than what was needed for its original manufacture.
A transitional material is something that does not adhere to the specification of a manufacturer for prime grade material: it is a substandard or off-spec material. This type of material may be obtained from a nonstop compounding line when a change is done from one grade to another. This means that the base color and the melt flow rate may be fairly variable. The price of virgin material is more than that of these off-spec materials.
Thermoplastic Grades
One material may have several grades. These grades may vary in molecular weight distribution, molecular weight, purity, chain branching, and the presence of modifiers or additives. Therefore, any properties mentioned in the literature should be used only as a general guideline, as each of the many plastics available consists of a family of materials.
Therefore, for each material group, a broad range of properties can be obtained. Also, the properties of these thermoplastics can be changed considerably by the processing conditions used. Processing may change the material’s physical properties, color, amount of molecular orientation, and also the type, and amount of crystallinity.
Additives
It is commonly considered in the thermoplastics sector that a most plastic materials used contain small quantities of additives, as most of these materials cannot be commercially used without them. The properties of a specific material are modified with the use of these additives.
As additives are necessary in commercial plastics, the scope and size of the additives sector is now huge. It is estimated that about seven million tons of additives of different kinds are used in plastics every year. In the thermoplastics sector, the largest quantity of additives is used in polyvinyl chloride (PVC).
With most thermoplastic materials, variations of the basic formulas are available to provide improved properties, such as, enhanced weatherability or heat resistance, with the application of additives. Processing and performance additives such as nucleating, antistatic, and mold release agents may also be incorporated to an existing material.
These additives could be part of the color masterbatch (a masterbatch is a concentrate). Also, concentrates with foaming agents, for structural foam molding, are available for several materials.
Examples of other additives are fillers, reclaimed material, reinforcements, impact modifiers, antioxidants, colorants, light stabilizers, lubricants, heat stabilizers, flame retardants, cross-linking agents, coupling agent, extenders, antistatic agents, nucleating agents, plasticizers, and blowing agents.
Material Modification
The term “materials modification” is typically used to refer to the addition of larger quantities (greater than a few percent) of an additive. An additive used in comparatively large concentrations may be called a modifier. Modifiers may include flame-retardants, elastomers, and fillers.
Material modification with fibers, rubber impact modifiers, or fillers has been widely used with engineering plastics to obtain an attractive blend of properties. These formulations may provide better impact strength, heat distortion temperature, and tensile strength along with ease of flow.
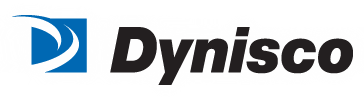
This information has been sourced, reviewed and adapted from materials provided by Dynisco.
For more information on this source, please visit Dynisco.