Temperatures
The measurement and control of temperature plays a significant role in injection molding, but most injection molding machines do not have enough temperature measuring points or circuits, despite the relative simplicity of making the measurements.
Temperature Sensing
Temperatures are sensed using thermocouples on most injection molding machines. A thermocouple consists of two different wires joined at each end. A small electrical signal is generated if one end is made hotter than the other: the more it is heated, the greater the electrical signal.
The thermocouple can be calibrated if one end is kept at a stable temperature (reference temperature), enabling simple and accurate measurements of temperatures. The measurement can be displayed in either digital or analog form. The temperatures are generally displayed in either °F or °C.
Temperature Control
Thermocouples are also extensively used as the sensors for temperature control systems. The required temperature is set on the control instrument (the set point) and this is followed by comparing the output from the sensor with that generated at the set point.
In the simplest systems, when the set point is reached the power is turned off and then turned on again when the temperature falls below the set point. This type of a system is referred to as 'on-off' control as it is either on or off.
P & I & D
P & I & D are three initials that stand for 'proportional, integral and derivative' and this is used in temperature control in order to improve control accuracy. In the case of a simple on-off system, the electric power is turned off at the set point when the required temperature is reached. This type of system can result in several issues, for instance, poor control and/or temperature overshoot - the temperature differs from what was actually set.
These three terms - P & I & D - are often put together to create a three term controller: as the set point is approached the indicated temperature enters the proportional band. To ensure that overshoot does not occur, the power is steadily and progressively reduced within that band. If the actual temperature differs from the set temperature then, for instance, the proportional band is shifted to eliminate the error (droop).
Melt Temperature
The melt temperature is important, and the quoted injection cylinder temperatures are only guidelines. The melt temperature is measured by an air shot technique or in the nozzle. If the measurement is done using an air shot technique, then extra care should be taken during the measurement to ensure that purging of the hot plastic does not result in an accident.
For a given machine, the actual injection cylinder settings to achieve this melt temperature will rely on, for example, the molding cycle, shot size, back pressure, and the screw rotational speed.
Temperature Settings
Users are recommended to start with the lowest settings suggested if they do not have experience of processing a specific grade of material. Injection cylinders are divided into zones for easy control, however all temperatures can be set to the same value.
The first zone temperature can be set at a lower value if working at high temperatures, or if the cycle times are long. This will prevent premature bridging and melting. Before starting the molding process, users must ensure that the barrel, mold, hopper block and the hydraulic oil are all at the correct temperatures.
Temperature Recording
What temperatures need to be recorded will be indicated by the machine setting record. Included are melt temperatures, mold temperatures, water temperatures and oil temperatures. An increasing number of temperature measuring points should be available.
A variety of probes together with an electronic, portable, temperature sensor or thermometer are also useful in the injection molding shop. This type of instrument allows effortless checking of oil temperatures, melt temperatures etc.
Pressures
High injection pressure must be employed in order to fill the mold rapidly and before the plastics material sets in the feed system. This means that high clamping pressures must be used so that injection molding machines can generate, and use, large forces.
This also means that high injection pressure must only be handled by people who are aware of what they are doing as they can be extremely dangerous.
The Hydraulic System
Most injection molding machines are powered, or driven, by a power unit which is placed in the base of the machine. The power unit is often an electric motor that drives a hydraulic pump or pumps.
Fluid is circulated through the system by these pumps and pressure builds up when there is resistance to the flow of hydraulic fluid; the pump tries to sustain the flow rate and so, in order to protect the pump against the pressure which it itself generates, the pressure in the hydraulic system is restricted with relief valves. Pressure is usually measured in either megaNewtons per square meter (MNm-2), pounds per square inch (psi), or bar.
Injection Pressure
This is the pressure that causes the material to flow, and it may be approximately measured by a transducer located in the hydraulic line or in the nozzle. It does not have a constant value but increases as mold filling becomes more complex. There is a direct relationship between injection pressure and injection line pressure.
First Stage and Second Stage Pressure
High injection pressures may be required during mold filling part of the molding cycle in order to maintain the preferred mold filling speed. This high pressure may not be necessary, or even desirable, once the mold is full.
In many cases, a high, first stage pressure may be followed by a lower, second stage pressure. When molding some semi-crystalline, thermoplastics materials, for instance acetal and nylon, the use of second stage pressure may not be needed as sudden changes in pressure can result in undesirable changes in crystalline structure.
Clamping Pressure
A clamping pressure must be applied in order to oppose the injection pressure. What is required should be estimated from a consideration of the projected area, instead of automatically using the maximum available. The projected area of a molding is considered the largest area that can be observed if the molding is observed from the direction of clamp force application.
For most molding jobs, it is approximately 2 tons per square inch (2 tsi) or 31 megaNewtons per square meter (31 MNm- 2). However, this is just a low figure and should only be treated as an extremely rough rule of thumb because, for instance, once the molding has any depth, then it is also necessary to consider the side wall forces.
Back Pressure
The screw must generate, and exceed, this pressure before it can move back. This back pressure is generated by rotating the screw against the restriction of the plastics material, which is contained in the barrel, or cylinder. Back pressures may reach 250 bar or, 25 MNm-2 or 3600 spi.
Material melting and color dispersion can be improved with the use of such high back pressures, but it is paid for as it increases stress on the injection molding machine, reduces fiber lengths in filled systems and increases the screw retraction time.
Users should keep this pressure as low as possible and in any event should not go beyond 20% of the machines (maximum rated), injection molding pressure. Some back pressure may be required to simply stop the screw pushing itself (auguring) too easily out of the barrel, or cylinder; for example, 5 bar or 0.5 MNm-2 or 73 psi.
The back pressure can also be programmed on some machines in order to compensate, for instance, for the efficient reduction in screw length which takes place during plasticization; this type of reduction means less heat input and therefore a drop in temperature. Conversely, on several machines it is difficult to sensibly set the machine, as there is no simple way to measure the effects of the changes.
Cavity Pressure
This is the pressure exerted by the plastics material inside the cavity and the pressure that tries to open and distort the mold. It may be sensed using a transducer and the produced signal that is used to actuate the switch from first stage pressure to second stage, holding pressure. This process is known as cavity pressure control (CPC).
Line Pressure
This pressure is also known as gage (gauge) pressure as it is frequently measured by means of a gage which is set in the hydraulic pipe or line. This pressure is not the injection pressure, but is actually the pressure present in the main supply line from the pump. Line pressure can usually be altered and line pressure should be modified in order to suit the specific molding run.
Nozzle Pressure
Nozzle pressure refers to the pressure measured within the nozzle. It is approximately the pressure that causes the material to flow. This pressure does not have a constant value but increases based on the growing complexity of mold filling.
There is a direct relationship between injection pressure, line pressure, and nozzle pressure. In screw machines, the nozzle pressure is about 10% lower than the injection pressure (as calculated from the gage in the hydraulic line). Pressure losses in ram machines are much greater and can reach 50%.
Screw Cushion
Screw cushion is the amount of material left in the barrel after the injection is done. The amount of screw cushion is either measured in millimeters or in inches; on small machines it is usually 0.118" or 3 mm. It is vital to precisely control the amount of screw cushion as it directly influences the amount of pressure sent from the hydraulic system into the mold.
Also, a gage pressure may be present yet the material may not have pressure if there is insufficient screw cushion. This is because the screw has come up against stops or restraints and yet, there is often no way of knowing this. This highlights the importance of an accurate measurement of screw cushion.
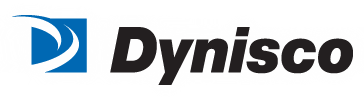
This information has been sourced, reviewed and adapted from materials provided by Dynisco.
For more information on this source, please visit Dynisco.