Amulya Das, Director of Business Development and Corporate R&D at Mid-Mountain Materials, Inc., talks to AZoM about their advanced coated fabrics used in the aerospace industry.
Please can you give us a brief introduction to Mid-Mountain Materials?
Mid-Mountain Materials, Inc. is a global company committed to manufacturing high quality products that protect our environment and people. We are the industry’s leading manufacturer of very advanced, high-performance coated fabrics and industrial textiles which are used in many applications across a broad range of industries. Our company is committed to creating a product that is unlike any other: heat and flame resistant material that not only lives up to industry standards but exceeds them.
Mid-Mountain Materials, Inc. has been dedicated to industrial fabrics for over 40 years. With this focus, the business is supported by modern weaving, knitting, finishing, coating/laminating and complete fabrication facilities, as well as a state-of-the-art research and development center.
The long history of Mid-Mountain is marked by innovation, quality and commitment. Mid-Mountain is well positioned to continue its leadership role in industrial textiles by delivering tomorrow’s expectations today through an intense customer focus, the relentless pursuit of innovation, and the assurance of fail-safe products.
What products do you have that are used in the aerospace industry?
Mid-Mountain’s high quality engineered products are fabricated into jet engine components and other critical aerospace parts. Our polymer coated fabrics, high temperature textiles and fabricated parts are used in various aerospace applications. The following products are currently being used for various applications in aerospace industry:
Coated Fabrics
- Armatex® NWF 14/602 (Cargo liner) White, meets BMS 8-343 Type I & III class
- Armatex® NGF 14/602 (Cargo liner) Gray Neoprene Coated Fiberglass Meets BMS 8-343 Type I class 2
- Armatex® SAF10 Silicone Coated Fabric No Flame, meets BMS & ASTM Flame tests
- Armatex® SBKG21.5 Silicone Coated Kevlar®-Glass
- Armatex® SRF45 Silicone Coated Fiberglass
- Armatex® SAF17 Silicone Coated Fiberglass
- Armatex® SF22 Silicone Coated Fiberglass
- Armatex® QF40 Refractory Coated Fiberglass
High Performance Textiles
- Hytex® 1000 Fiberglass Fabric, Ropes, Tapes and Sleevings
- Hytex® 1200 Mineral Oxide Fabric
- Hytex®1400 High Performance Fiberglass Fabric, Ropes, Tapes and Sleevings
- Hytex® 2200 Ceramic Fiber Fabric, Rope and Sleeving
- Hytex® 2500 Ceramic Fiber Fabric and Sleeving
- Siltex® Woven Silica Fabric
- Aluminum foil laminated fabrics
Thermal Insulation Materials
- Cermex® Thermal Insulation Blankets & Mats
- Cermex® Thermal Insulation Papers

Figure 1. MID-MOUNTAIN’S COATED FABRIC FOR SIAD-E (supersonic inflatable aerodynamic decelerator) for NASA LDSD program (low density supersonic decelerator)
Can you tell us about your coated fabrics in more detail? What types of coatings and fibres do you use, and how are they made?
Mid-Mountain manufactures a complete line of coated fabrics that are high temperature resistant, chemical resistant and abrasion resistant. A wide variety of base fabrics are coated with different types of coatings to create a coated fabric suited for aerospace application. In addition to fiberglass and silica fabrics, we also use woven and non-woven fabrics including Nomex®, Kevlar®, Polyester, Carbon, Aramid blends, Quartz, Basalt and Ceramic. We use a direct coating method to apply various coatings onto the fabric using the knife mechanism. The thickness of coating depends on the gap between the knife and the surface. There are various techniques in which this mechanism can be used:
- Knife over roller
- Knife on air
- Knife over table
- Knife over rubber blanket
Many of our standard coated fabrics are manufactured in accordance with a variety of specifications including ASTM, FAR, BMS and MIL. We also offer several coated and uncoated fabrics that are ANSI/FM 4950 approved. Our standard coated fabrics include:
- Silicone Coated Fabrics
- Silicone/Refractory Coated Fabrics
- Intumescent Coated Fabrics
- Refractory Coated Fabrics
- Vermiculite Coated Fabrics
- PTFE Coated Fabrics
- Ceramic Coated Fabrics
- Neoprene Coated Fabrics
- Urethane Coated Fabrics
- Hypalon Coated Fabrics
- Acrylic Coated Fabrics
What are some of the unique technical challenges faced when designing products for use in aerospace applications?
The aerospace industry demands materials of the highest quality to perform reliably and predictably under extreme operating conditions for long periods of time. Mid-Mountain specializes in concurrent engineering. Each project presents unique requirements. Our extensive background working with a wide variety of materials and fabrication techniques allow us to overcome these challenges.
The first challenge we face when developing new products is choosing a concept that has potential. A good idea is only the first step, and often isn't viable because of cost, production difficulties or regulatory limitations. These are the unique technical challenges faced when designing products for use in aerospace applications.
We establish a clear understanding of the structure-property relationship and their dependence on processing techniques to ensure consistency in production. We also meet the rigorous standards for quality and reliability through our ISO Quality system. The biggest and most important challenge we face today is the issue of qualification and certification of new products from the aerospace industry, which is always a very lengthy and costly process.
Can you give us some specific examples of current aerospace applications your products are used in?
Mid-Mountain’s high quality engineered products are fabricated into jet engine components and other critical aerospace parts. Our polymer coated fabrics, high temperature textiles and fabricated parts are currently being used in the following applications:
- Air grill Decompression Baffle (Ref Image 5&6)
- Jet Engine Components
- Cargo liners
- Vapor Barriers
- Sound Insulation
- Engine Firewall cover (Ref Image 2,3 & 4)
- Fabric for Aircraft Loading Walkways
- Gaskets
- Insulation Blankets
- Seals
- Smoke Seals
- Back Panel for luggage bin
- Fireproof cable cover or sleeve
- Airframe Seals
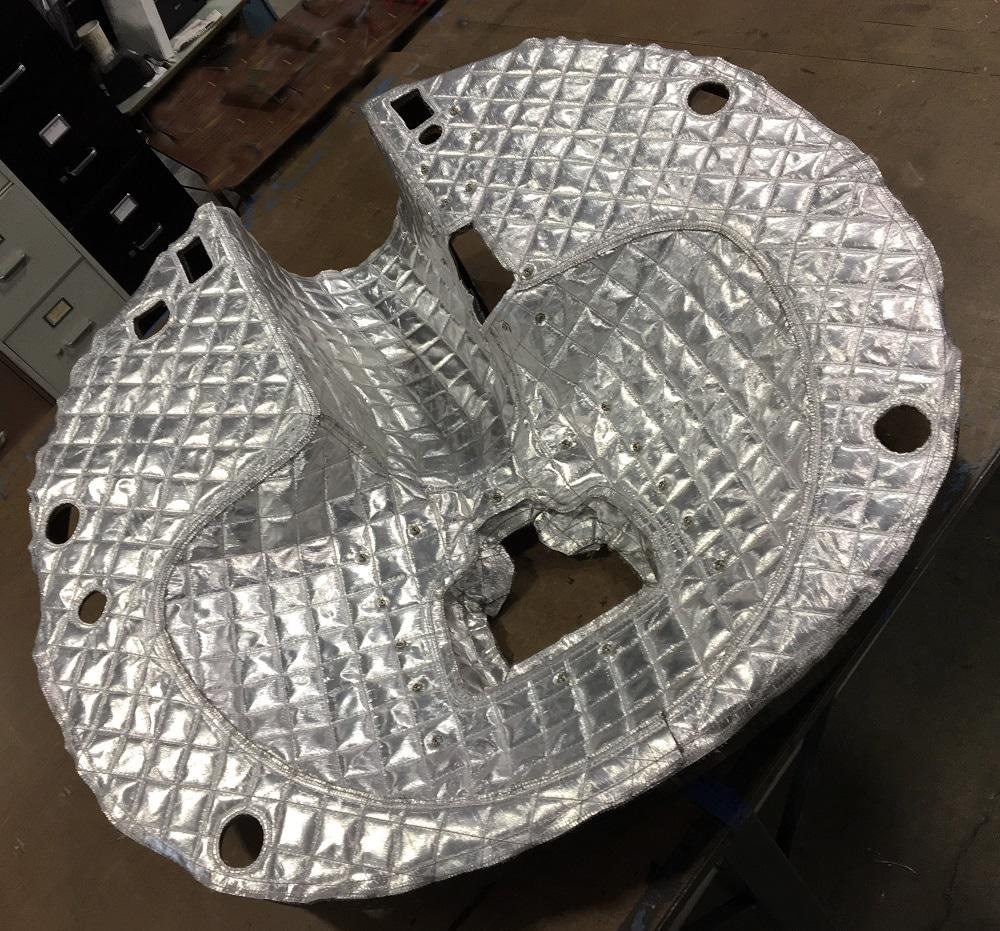
Figure 2. Firewall Blanket
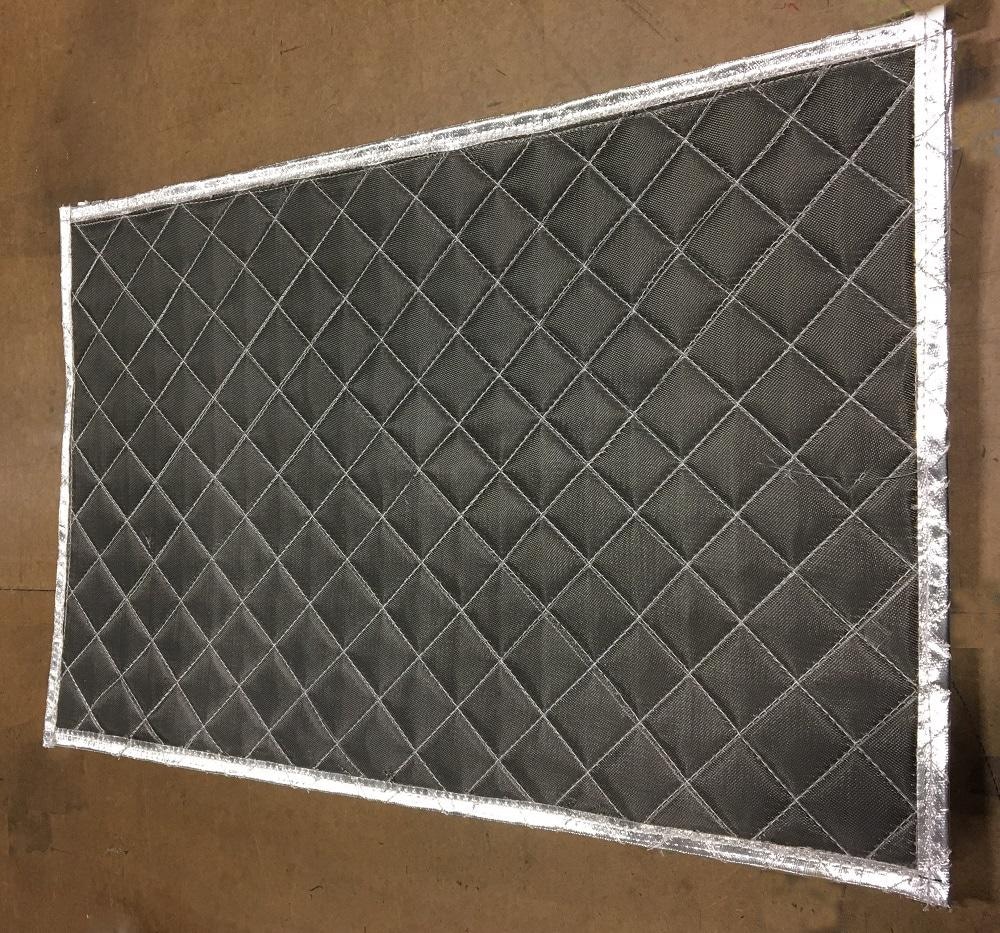
Figure 3. Firewall Cover
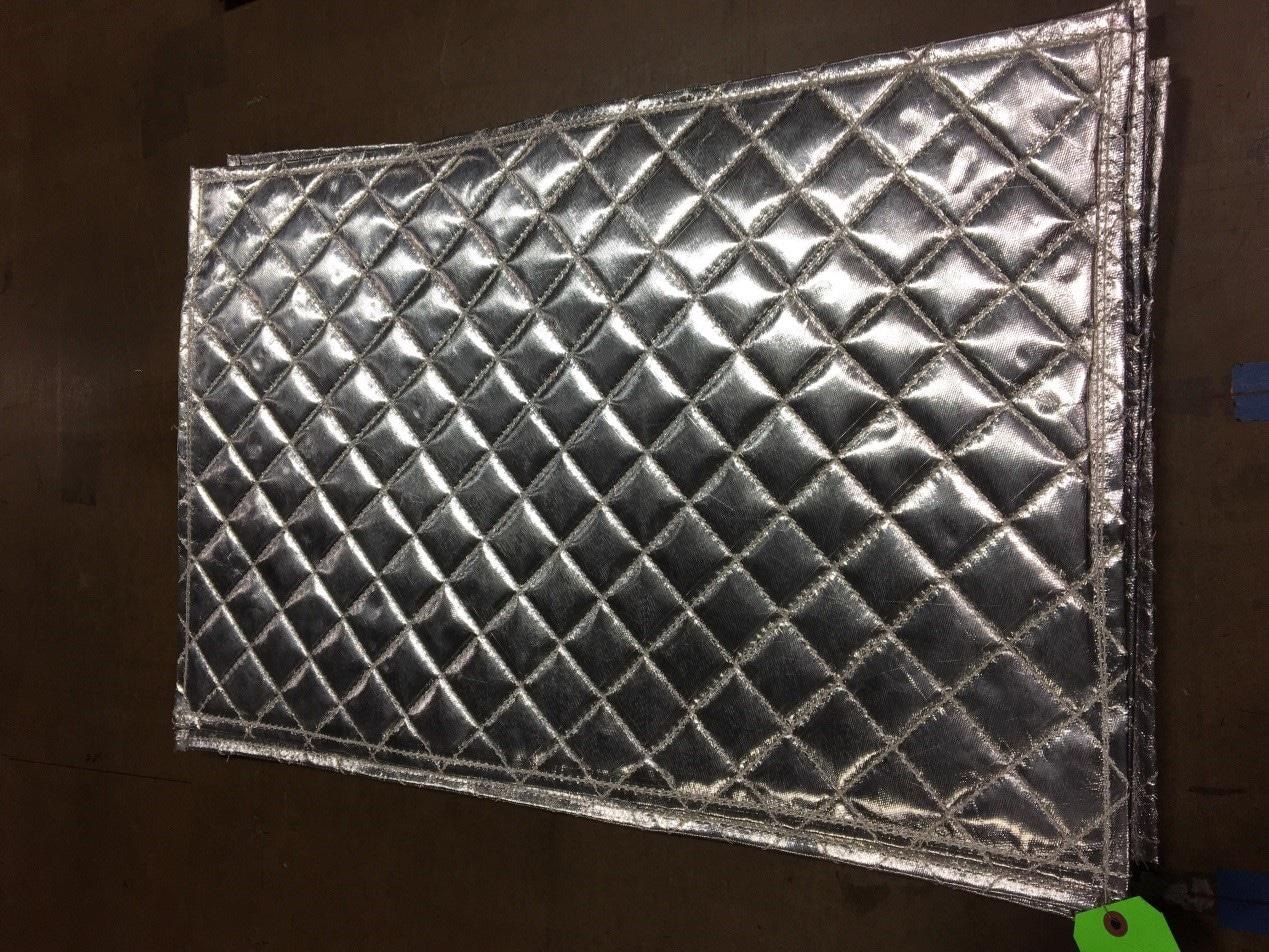
Figure 4. Firewall cover
Are your aerospace products developed from the ground-up for each use, or are they adapted from more general purpose products?
Mid-Mountain’s core technologies are frequently used to create new materials for aerospace safety and process-specific applications. Among others innovations, Mid-Mountain has contributed to revolutionary breakthroughs in flexible industrial coated fabrics, covers and removable insulation blankets. Many of these highly specialized products were developed in response to customer specifications. Most of our aerospace products are custom designed from ground up. Our wide range of chemical formulation, fabric coating, weaving and fabrication experience and abilities allows us to offer a solution to all aerospace manufacturing needs. We can provide input on material selection and fabrication techniques as well as create custom products to serve specific needs & meet specifications.
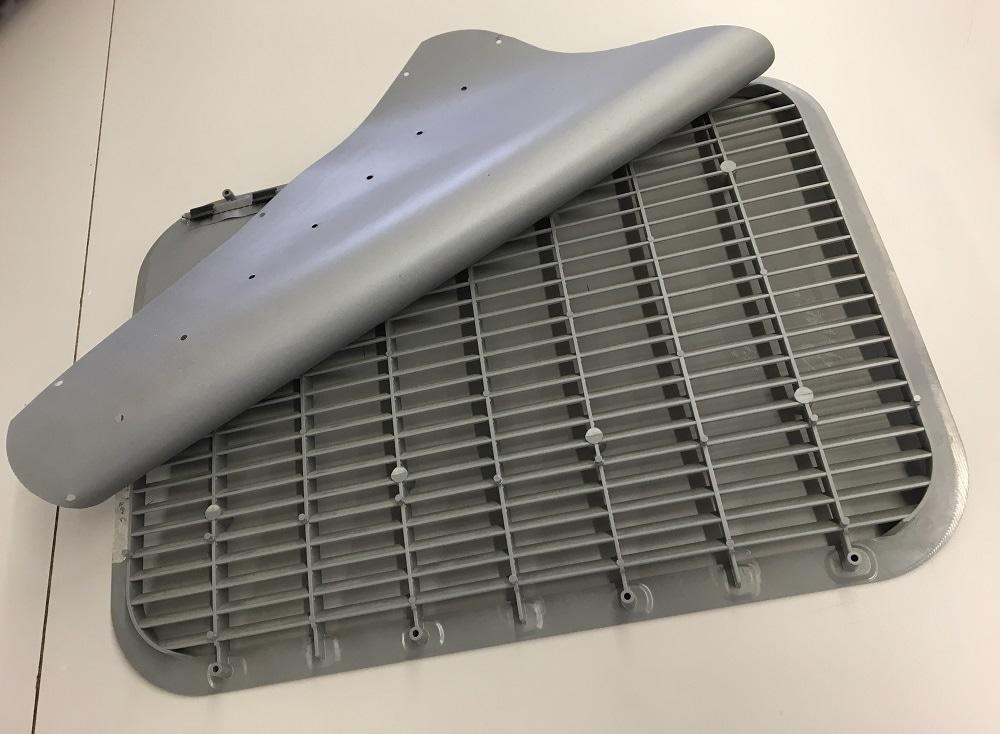
Figure 5. Air grill Decompression Baffle
Have you found the aerospace industry challenging to tackle, in terms of the regulatory environment or testing standards?
In a market driven by demand for greater aircraft performance and commercial return, we understand the aerospace industry’s need to innovate and push the envelope of material performance, application and manufacturing. Mid-Mountain has a proud track record of helping the world’s leading aerospace companies to achieve competitive advantage through the provision of technically demanding product solutions.
Innovation is the driving force of Mid-Mountain, and more than ever, we are providing the solutions for aviation’s sustainable future with the least possible impact on the environment.
To ensure a successful product for aerospace, our team always designs products that have functionality and are attractive to the target market. We are able to manufacture the product at a reasonable cost, and the product meets safety regulations and testing standards. The challenge is for our engineers to keep all these aspects in mind while creating a product that will sell to a very highly advancing aerospace industry. We have been very successful in achieving those goals and overcoming challenges throughout the years. We are very confident that we will continue to do so in future.
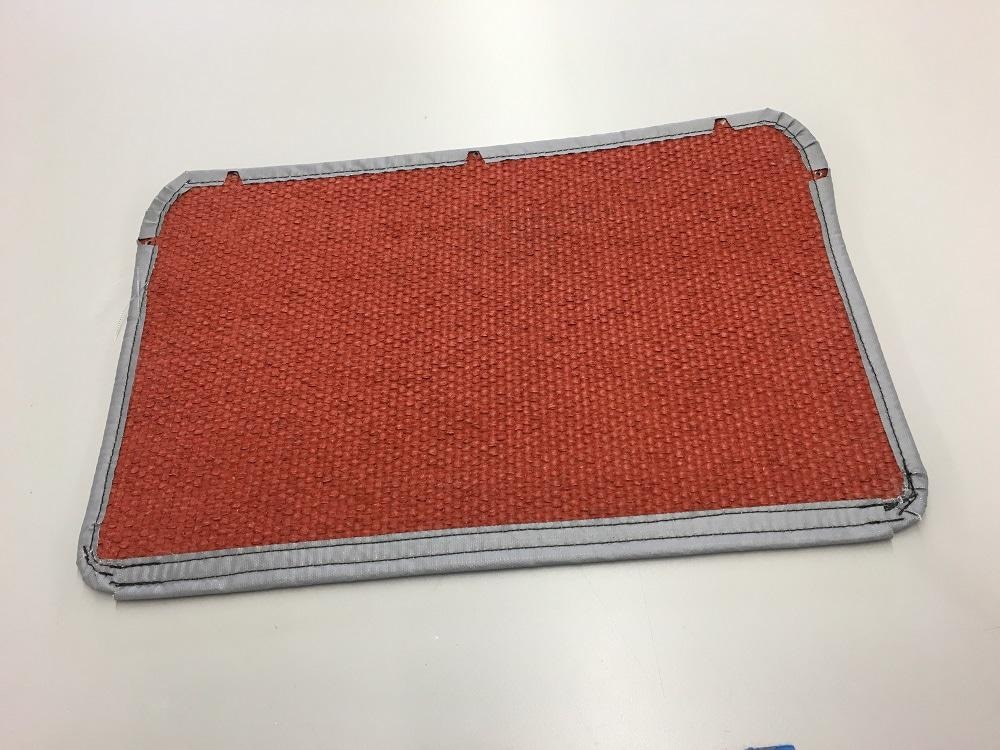
Figure 6. Air grill Decompression Baffle
What future developments can you tell us about? Are there any new product ranges planned, or further applications you would like to address?
Today, Mid-Mountain Materials remains committed to the goal of being the preferred provider for innovative rubber and silicone coating and fabric technology. We strive to accomplish this by continuing to offer our customers a diversified line of quality products for a broad range of applications.
Mid-Mountain Materials has been supporting JPML/NASA’s technological advances by developing advanced coated fabrics for very high thermal protection systems in several sizes and material combinations for various flight programs, and we are continuing to work with them for their future programs, which feature new materials capable of performing at even higher temperatures.
We have recently developed and manufactured the following aircraft parts which have been successfully tested and qualified by FAA for aircraft use:
- FIREWALL BLANKET: To protect the firewall structure and aircraft occupants from fire.
- INERTIAL SEPARATOR SEAL: To seal the connection of the inlet to the inertial separators while also preventing fire from penetrating the plenum.
- PLENUM SEAL: To seal the plenum housing and prevent fire from penetrating the plenum.
- ENGINE SEAL: To seal the plenum to engine connection and prevent fire from penetrating the plenum.
We are also developing a very high heat resistant fire and smoke seal for various parts of engine cover which can handle temperatures up to 2500° F • 1371°C.
We are now working in association with a leading aircraft parts manufacturer on a new type of cargo lining material which will be incredibly durable and lightweight.
We have successfully developed fabric for Fire Resistant Aircraft Unit Load Devices and Fire Containment Covers for Air-Cargo container and equipment.
Our recently developed ARMATEX® Silverstar products are being evaluated by an aircraft manufacturer for various applications. They are not only of high strength, high-temperature and fire-retardant, but they are very aesthetically appealing products. We are currently further developing our ARMATEX® Silverstar for use in aircraft loading walkways. Our ARMATEX® SF 37 Jetstar is the product we currently sell for this application.
We are in the process of developing true skin and low surface energy silicone coated fabrics for non-sticky and dirt resistant applications.
Our future work on the improvement and development of materials for aviation applications is developing on three main fronts: the development of new materials; the improvement of current material properties by refining composition and novel processing methods for new applications; and the application of current materials in new and novel structures.
Kevlar® and Nomex® are registered trademarks of the E.I. DuPont Company, Wilmington, DE USA.
About Amulya Das
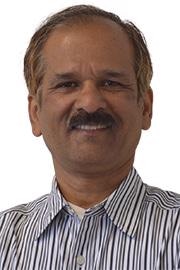
Amulya Das is the Director of Business Development and Corporate R&D at Mid-Mountain Materials, Inc., and is based at the company’s manufacturing facility in Arlington, Washington, USA.
Amulya is a Materials Scientist with a degree in Chemistry, and a Master’s in Chemical Technology with specialization in Textile & Polymers Science. As Director of Business Development and R&D, Amulya works closely with engineers and project managers to develop unique solutions that will address their application challenges.
Amulya has 30 years of hands-on working experience in manufacturing, engineering, design, and Research & Development with textiles, chemicals, coatings, refractories and polymers as well as high performance materials.
Disclaimer: The views expressed here are those of the interviewee and do not necessarily represent the views of AZoM.com Limited (T/A) AZoNetwork, the owner and operator of this website. This disclaimer forms part of the Terms and Conditions of use of this website.