Several types of nuclear reactors are currently using uranium dioxide (UO2) as well as actinide mixed oxides such as (U,Pu)O2 MOx and these are still considered to be reference components for future concepts. If the sintering of these ceramics was extensively investigated for powder metallurgy methods, the latest emergence of new ways of preparation for actinides dioxides, primarily based on the precipitation of low-temperature precursors, requires caring about the role of chemistry during sintering and its effect over the final microstructure of the pellets.
In this article, the preparation of UO2 powders was undertaken from uranium(IV) oxalate in order to understand the effect of several parameters over the densification process, including the impact of the residual carbon content retained in the oxide following thermal conversion of the initial precursor.
The significant role played by the atmosphere of calcination was revealed by the extensive characterization of the powders obtained from the conversion of oxalate precursor under different heating conditions. The main differences seen arose from the oxidization of U(IV) under air in the particular case of uranium-bearing compounds. Indeed, this later leads to changes at the microscopic scale, specifically concerning diffusion coefficients that strongly influence the development of the powder microstructure. Besides dealing with the crystallite size, which considerably increased during calcination under oxidizing atmosphere, these changes were also concerned with the grains morphology at the macroscopic level through solarization-related processes.
Densification Processes and Final Microstructure
Densification processes and final microstructure of the sintered pellets prepared following sintering at high temperatures also considerably differ regarding to the conditions of preparation of the starting powder. Such modifications mainly occur from the in depth differences presented above, but also arise from differences in the residual carbon content of the oxide powders. Although expected from the data earlier reported in the literature for other actinide-bearing oxides prepared from oxalate precursors, the effect of the atmosphere of conversion on the residual carbon content was proved in this study. As a matter of evidence, the amount of carbon was systematically detected to be 4 to 5 times higher in the samples prepared under only reducing conditions. Additionally, thanks to a Hiden Analytical QGA analyzer, an original coupling between dilatometric measurements and MS analysis (Figure 1) was set.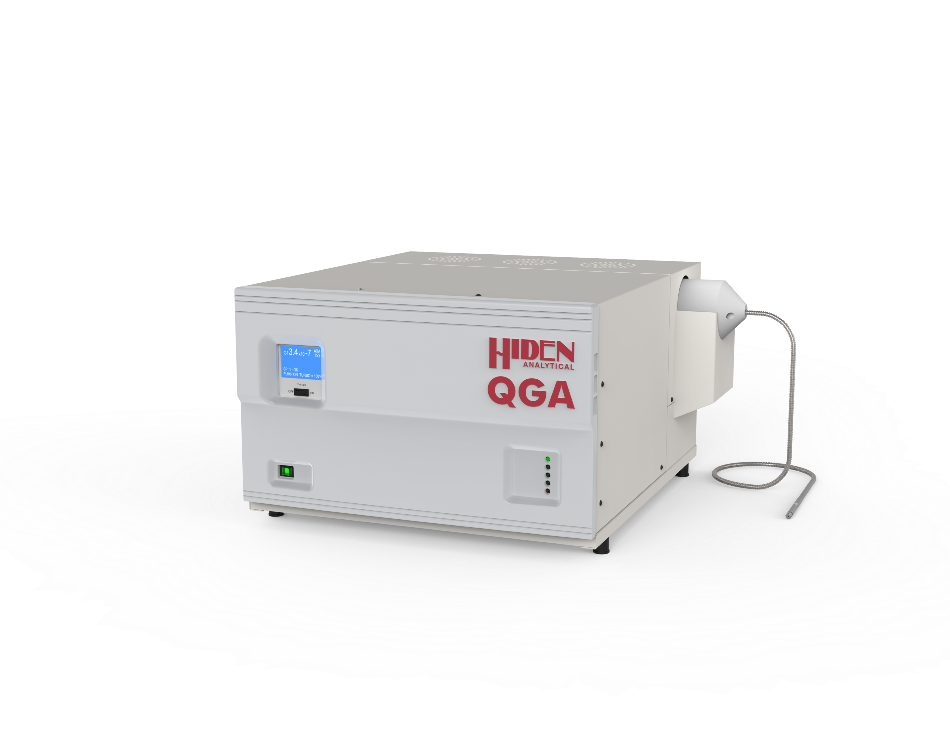
Hiden QGA Real-time gas analyzer
Conclusion
It showed that carbon was eliminated during the first step of the densification as gaseous CO2. However, the residual carbon content was observed to be more likely a second-order parameter to be taken into account in order to evaluate the behavior of the samples during the sintering process. Indeed, the more significant variations stated when studying the microstructure of the sintered samples came from redox or morphological considerations (presence of U3O8 in the starting powder, decrease of reactivity through improved crystallite growth, …). Conversely, despite the vital differences measured in terms of carbon content in the final samples, neither the relative density of the sintered pellets nor the average grain size were found to be considerably modified.
.jpg)
Figure 1. Dilatometry/MS study of the sample obtained after conversion of U(C2O4)2.2H2O under reducing atmosphere at 500 °C.
Project Summary By:
Nicolas CLAVIER / Julien MARTINEZ
ICSM, UMR 5257 CEA/CNRS/ESNCM/Univ. Montpellier,
Site de Marcoule Bât. 426,
BP 17171, 30207 Bagnols/Cèze cedex
France
Paper Reference
F J. Martinez, N. Clavier, T. Ducasse, A. Mesbah, F. Audubert, B. Corso, N. Vigier, N. Dacheux : "From uranium(IV) oxalate to sintered UO2 : consequences of the powders’ thermal history on the microstructure", J. Europ. Ceram. Soc., 35, 4535-4546, 2015.
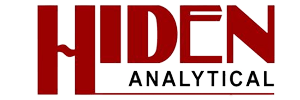
This information has been sourced, reviewed and adapted from materials provided by Hiden Analytical.
For more information on this source, please visit Hiden Analytical.