Incinerators, furnaces, crucibles and kilns are used in a wide variety of industries, combusting anything from solid and liquid fuels, to solids, sludges, organic products and liquid wastes, some of which may be toxic or radioactive. For maximum energy efficiency and thermal insulation, the refractory linings should be as porous as possible, but conversely for resistance to slag penetration and wear-damage, the linings should be as dense as possible. At present, all refractory linings are based on materials with sintered structures, which are naturally porous and thus allow corrosive liquid and gas penetration. The life of such linings in an industrial incinerator can be less than two years and the expense involved in replacement, waste disposal and interruption of production can exceed £250,000. Refractory Damage As an example of the extent of damage that can be suffered by refractory lining, a dense 85% alumina brick removed from the rotary kiln of an industrial waste incineration plant, after one year's service can lose several centimetres of material. Closer examination reveals residual slag on the surface of the brick, while EDX analysis has detected iron penetration (from the slag) to depths of about 5mm. The average rate of loss of refractory over one year was approximately 3.5μm/hour, while the residual brick was full of holes and cracks and was completely porous to liquids at room temperature. Surface Treatment of Refractories At UMIST, in Manchester, an interdisciplinary project is being carried out involving the Laser Processing Research Centre and the Corrosion and Protection Centre to try to extend the life of refractories. Together they are investigating techniques for the generation of dense solidification phases on the refractory lining surface, while keeping the bulk material properties unchanged. The bi-structural furnace lining material has the dual purposes of thermal insulation and prevention of penetration by corrosive species. High power lasers and arc lamps have been identified as suitable tools for developing dense surfaces on these high melting-point (above 2,000°C) refractory materials, with differing results. Process Overview The surface treatment process involves melting the surface of the refractory with a high-energy beam and densification of the surface on rapid cooling. The trick that the UMIST group has developed is to avoid, without use of a furnace, the formation of cracks oriented parallel and perpendicular to the surface. These often occur due to relief of the thermally-induced stresses, which can in turn lead to break-up and spallation of the treated surface. Heat Sources In the initial research, emphasis was placed on achieving surface-sealing of 85% alumina refractory lining bricks, to a depth of over 0.5mm, without inducing cracks or spallation, and without involving a furnace to relieve the thermal stresses. Various heat sources, including a 1kW C02 laser, a 400W Nd: YAG laser, a 120W diode laser and a 150W arc lamp were used for surface sealing. In some cases, in situ preheating and post-heating of the bricks, using an oxygen/acetylene torch, helped to release stresses. High temperature exposures in molten salts and in simulated waste incinerator environments, together with thermal cycling and thermal shock tests, have enabled the success of the treatments to be determined, with some treated bricks currently being exposed in an industrial waste incinerator. Structure of CO2 Laser Treated Refractories After establishing optimum processing conditions, the surface processing of refractory bricks, without preheating, using the C02 laser, resulted in successful sealing of the surface porosity and a smooth surface finish when compared to the untreated surface, figure 1(a). However, some vertical cracks were observed in the treated surface. As shown in cross section figure 1(b), the treatment reduced surface porosity and resulted in a columnar grain structure, together with variously shaped grains adjacent to the laser tracks. EDX analysis and X-ray diffraction confirmed that the surface was essentially Al2O3. However, the presence of chromium in the brick resulted in the surface taking on a ruby-like pink colour, associated with Al2O3/Cr2O3. 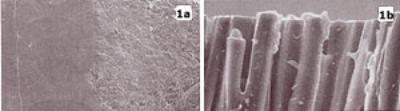 | Figure 1. Typical morphology and microstructure of CO2 laser treated alumina-based refractory in (a) plan view and (b) cross section | Structure of Other Treated Refractories Further studies have shown that treatment with the Nd:YAG laser is less effective than with the C02 laser. Moreover, the diode laser is the most successful of the three lasers in terms of sealing the surface and producing a surface microstructure consisting of fine, needle-like grains in a multi-directional lattice, figures 2 (a) and (b). Surface treatment using an arc lamp results in a surface microstructure similar to that for the diode laser - some of the grains are long, circular and multi-directional in orientation, figure 3. 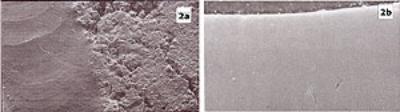 | Figure 2. Typical morphology and microstructure of diode laser treated alumina-based refractory in (a) plan view and (b) cross section | 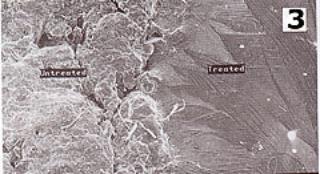 | Figure 3. Typical morphology and microstructure of an arc-lamp treated alumina-based refractory in plan view. | Thermal Cracking Although the various treatments have been effective in sealing porosity in the refractories, the thermal gradients result in some vertical cracks in the surfaces. To overcome this a novel method has been developed, via this programme, to reduce the gradients. An oxygen/acetylene welding kit has been used to preheat and post-heat the CO2 laser material interaction zone with particularly good results. Under optimum conditions and a preheating temperature of 1,400°C, dense, pore-free and crack-free laser-treated zones, about 0.5mm thick, have been produced for the first time, figure 4, with the surface morphologies being dependent on the physical and chemical properties of the material and on the processing parameters. 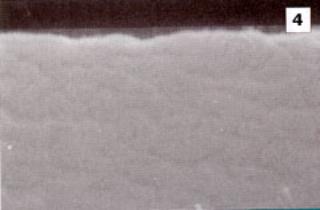 | Figure 4. Typical microstructure (in cross section) of the densified laser/flame-treated zone. | Performance of Treated Refractories Specimens that have been treated with the diode laser or with the CO2 laser, both with and without preheat, have been exposed under thermal cycling and thermal shock conditions and, in every case, the treated layer remained in good contact with the bulk substrate. Exposures in the molten salt or simulated waste incineration conditions showed that the rates of penetration were about 20 times less for the surface-treated areas than for the untreated areas, indicating that these treatments are very effective in sealing porosity, without extensive damage due to thermal gradients. Other Areas of Research Research is continuing, with emphasis on enhancing the performance of refractories by local surface modifications using controlled cooling rates and thermal gradients. Other areas under investigation include determining the main factors that control nucleation and growth of crystals during solidification of the melt pool, identifying the factors that control the compositions, structures and properties of new materials produced by laser/arc lamp melting, and optimising surface compositions and structures for resistance to corrosion and erosion-corrosion. This is being investigated by using coating methods combined with laser treatments producing superior surfaces, in terms of chemical and physical characteristics, on low quality substrates using lasers or arc lamps. The Future Future research will explore the potential for the technique to cause homogenisation and purification of low-grade refractories, arising from the segregation of impurities - this has exciting possibilities in terms of development of novel methods for generating new refractory materials, as well as for sealing the surfaces of low-grade substrates. |