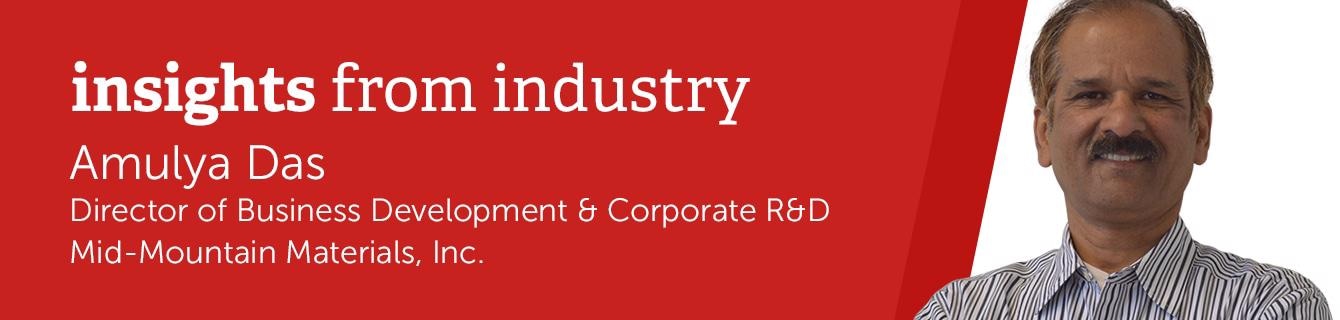
Amulya Das, Director of Business Development at Mid-Mountain Materials, Inc., talks to AZoM about their vertical integration during the fabrication process of fabricated thermal insulation products.
Many companies claim to offer vertical integration during their fabrication or manufacturing processes. Why is it so important for Mid-Mountain Materials, Inc. to offer vertical integration?
At Mid-Mountain, we feel that our vertical integration gives our customers an extra layer of customer service and quality, which sets us apart from our competition. It has always been important to us to provide our customers with the highest level of service. Part of that is having a very diverse product line that meets several applications needs for our customers, which saves them time. Having to source from multiple companies takes time, and as they say, “time is money.” To provide as much as we can to our customers, Mid-Mountain has developed four manufacturing divisions: Coated Fabrics, Fabricated Components, Textiles Formation, and Refractory Moldables. And quite often, products from each division come together to make one product, offering a price and lead time advantage to our customers.
What specifically sets Mid-Mountain apart from other engineered thermal insulation manufacturers?
To begin with, as a company we believe that there is no application challenge too great for us to overcome. When a customer comes to us with a unique application, we use our extensive materials knowledge and the experience of our team to devise a solution. Mid-Mountain has a team that has over 200 years of combined experience. Not only do we value our customers, but we value the knowledge, expertise, and loyalty of our team tremendously. Their pride shows in the quality of the products they manufacture.
Where does your vertical integration come into it? Can you give us an example?
Being vertically integrated with coated fabrics and textiles gives us more to work with, thus we can engineer the most innovative solutions for our customers. We don’t have to source many of the raw materials we use in our engineered thermal insulation products, so we can provide our customers with faster lead times, and more competitively priced products.
A great example of this would be our THERMOPAK® Tadpole Gasket. Tadpole gasket is often comprised of a core material, and a cover material. Based on the application, a tadpole gasket could be made from a fiberglass rope (the core) and a silicone coated fabric (the cover), both of which we manufacture at our plant in Arlington, WA. Another example would be our THERMOPAK® Crucible Lid Seals which are used in Primary Aluminium smelters to seal the crucible. We manufacture the dense round or square braid rope, and then coat the rope with silicone rubber. Lastly, our THERMOPAK® External Cathode Bar Seals illustrate our vertical integration very well. These are comprised four products that we manufacture: two ARMATEX® Coated Fabrics, a HYTEX® Kevlar cord, and our THERMOSEAL® Moldable which is used in the installation.
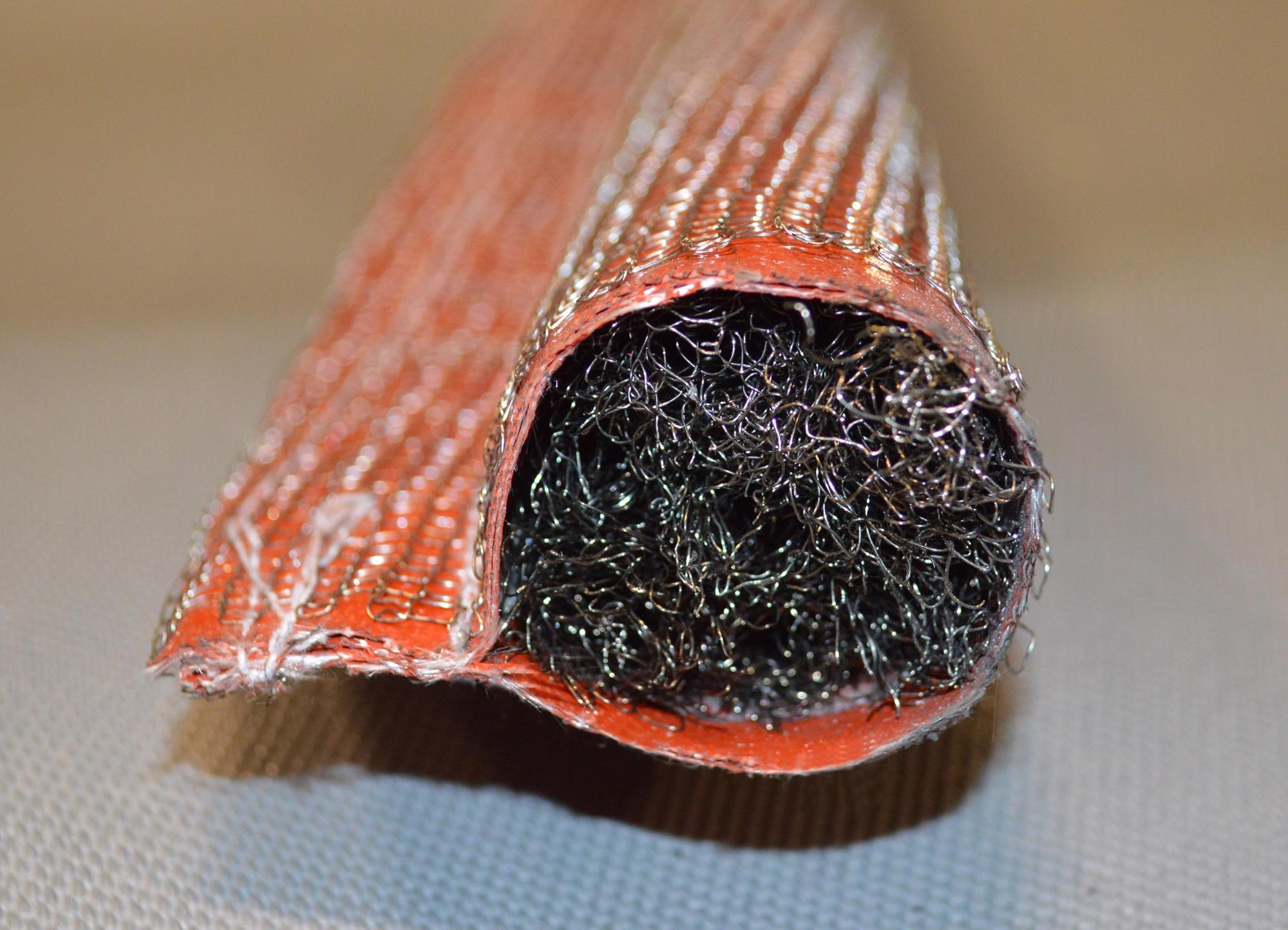
Image Credit: Mid-Mountain Materials, Inc.
Any industry involved in using engineered materials is constantly looking for more cost-effective solutions without compromising on quality. What does Mid-Mountain do to achieve a competitive advantage on price and lead time for your clients?
To begin with, being vertically integrated gives us a tremendous advantage on price and lead time. The use of our own products as a raw material in a component gives us the advantage of lower cost over a company who would have to buy that raw material. In addition, we go to great lengths to source the global market for the highest quality raw materials that are very competitively priced. We have an advantage on lead time as well, as many of the components that are engineered into our thermal insulation products are standard products for us, and are readily available.
Successful vertical integration involves a high level of quality control of the finished products. What does Mid-Mountain Materials, Inc. do to ensure high-quality products are delivered?
Mid-Mountain is an ISO 9001:2008 (soon to be 2015) certified company. The quality procedures and processes we have in place per ISO ensures the quality of every component we manufacture in our thermal insulation products. And what we do outsource is also subject to the same quality guidelines.
Are there any case studies you are particularly proud of that demonstrate how your vertical integration process provides high quality finished products?
In collaboration with the U.S. Department of Energy, GeoSafe and Batelle Engineers NW, we manufactured a Geodesic Dome Tent that was used to contain emissions and retain heat during the in situ-vitification of the ground to eliminate hazardous waste, including both nuclear and industrial waste at the Hanford Nuclear Plant in Richland, Washington, USA. The tent was manufactured from our ARMATEX® Coated fabrics and assembled by our fabrication team. As aforementioned, our THERMOPAK® External Cathode Bar Seals are another example of a high quality product made from a variety of components we manufacture. It was our goal to design a product for Primary Aluminum that would replace an older technology with one that was more innovative, and would provide our customers with the benefit of a longer lasting solution that was easier to install. Through our vertical integration we were able to design and patent THERMOPAK® External Cathode Bar Seals which are used in the largest primary aluminium smelters around the world.
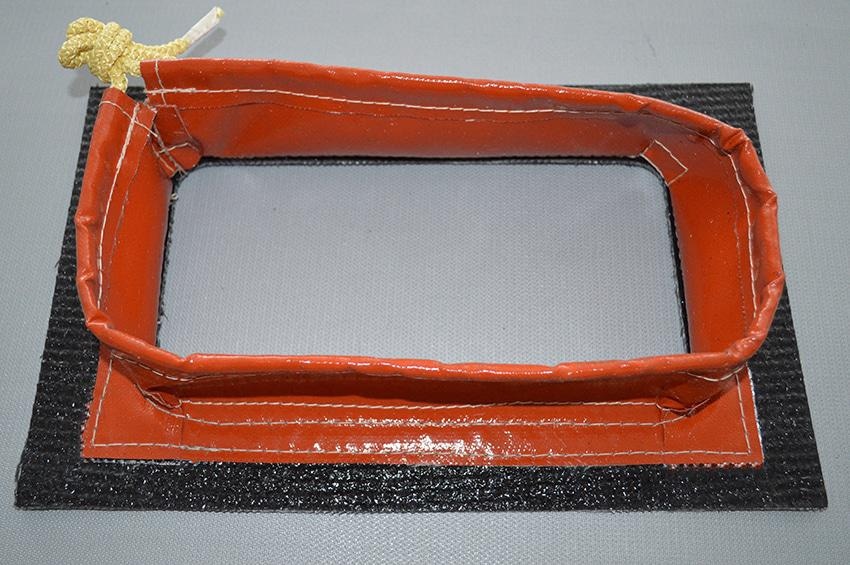
Image Credit: Mid-Mountain Materials, Inc.
What industries benefit the most from solutions produced using your vertical integration method?
Any industry that is needing a competitively priced, fabricated thermal insulation product would benefit from our vertically integrated solutions. Industries that have used our vertically integrated products include aluminium, aerospace, rail, power generation, welding, and more. There really isn’t any industry that couldn’t benefit!
What are the biggest challenges your customers face and how are you able to solve them?
We believe that the biggest challenge our customers face is greater performance from their processes and products as well as higher commercial return in their markets. At Mid-Mountain, we face the same challenges. Continuous improvement in both our processes and products are always at the forefront of everything we do. When we find ways to do things better, that translates to higher-performing, more cost-effective products for our customers.
How do you see the key industries you serve developing over the next few years and how will Mid- Mountain Materials, Inc. adapt to these changes?
I believe the key industries we serve will continue to grow, and companies will continue to seek the most competitively priced, advanced solution for their applications. Our company has always been at the forefront of providing innovative products for all of the industries we serve. Staying current on the advanced materials that are available in the market is very integral to our innovation, and gives us the opportunity to provide products that will evolve right alongside our customers’ requirements.
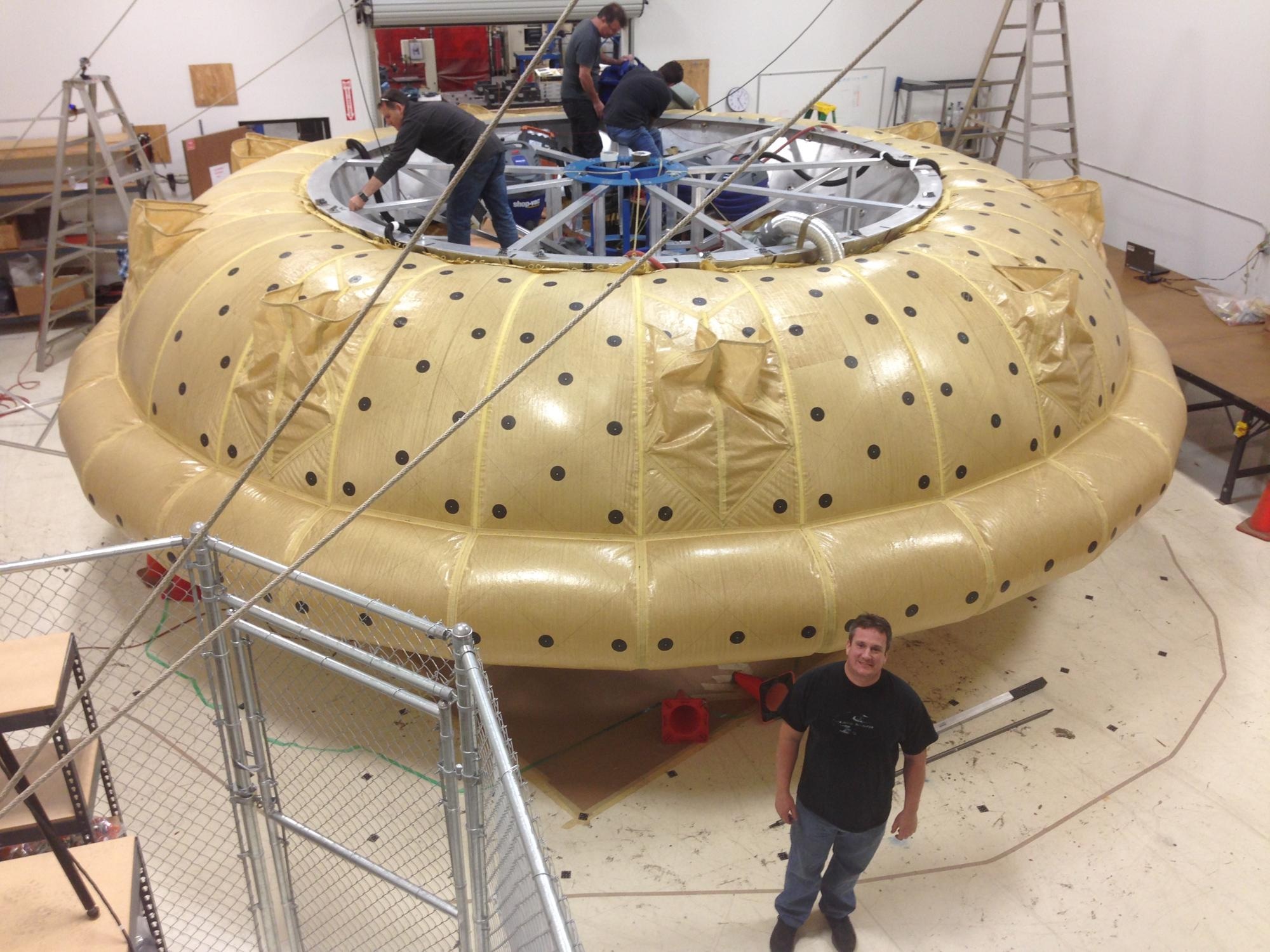
Image Credit: Mid-Mountain Materials, Inc.
Where can our readers learn more about your vertical integration?
The best way to learn about our vertical integration is to call us and discuss the requirements of a specific application. While we have tried to capture all of our capabilities on our website, there is always so much more to be discovered through the conversations we have with customers and inquiries.
Our ARMATEX® Spacetex Fabric for the Mars 2020 Lander project is a great example of this type of interaction. A NASA engineer called describing the very technical aspects of a ballute (balloon/parachute) for the Mars Lander, and it was from that discussion we determined we could provide a highly advanced coated fabric for that application. Having the one-to-one interaction is very important to us, as we really value the relationships we have with our customers.
About Amulya Das
Amulya Das is Director of Business Development at Mid-Mountain Materials, Inc., and is based at the company’s manufacturing facility in Arlington, Washington, USA.
Amulya is a Materials Scientist with a degree in Chemistry, and also has a Masters Degree in Chemical Technology with a specialization of Textile & Polymers Science from The Institute of Chemical Technology, Bombay, India. As Director of Business Development, Amulya works closely with engineers and project managers to develop unique solutions that will address their applications challenges.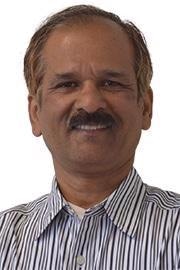
Prior to this role, Amulya served as the Manager of the Coating Division at Mid-Mountain, overseeing the manufacture of all standard and custom coated products. Amulya has 28 years of hands on working experience in manufacturing, engineering, design, and Research & Development with textiles, chemicals, and polymers as well as high performance materials.
Disclaimer: The views expressed here are those of the interviewee and do not necessarily represent the views of AZoM.com Limited (T/A) AZoNetwork, the owner and operator of this website. This disclaimer forms part of the Terms and Conditions of use of this website.