The term ‘pressure vessel’ signifies a wide range of different systems, all constructed with the express purpose of confining a large quantity of fluid to a small space. This definition includes remarkable feats of engineering such as airplanes and nuclear reactors, to humbler everyday products such as a deodorant canister.
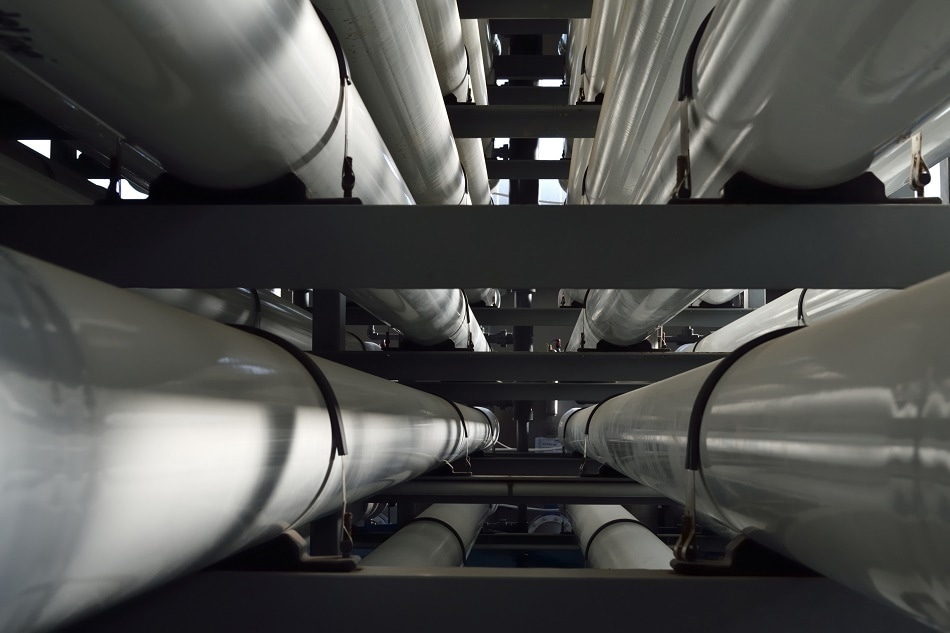
shutterstock.com/Jose Manuel Macias
Technologies that depend on the reliable containment of pressurized liquids and gases are not new. However, the design and manufacturing of pressure vessels poses an exciting engineering challenge: Persuading a fluid to occupy smaller volumes than it ‘naturally’ would often require using a huge amount of energy, and consequently, compressed liquids and gases exert a lot of strain on their containers.
Containing the Strain from Pressurized Fluids
The challenge of containing this strain must be handled in two ways: firstly, by the application of strong materials (steel’s toughness and relative abundance make it the preferred material for many applications), and secondly, by building the container such that the strain exerted on it by its pressurized contents is minimized.1
Mathematically, the solution to the issue of minimizing strain has an easy geometric solution: a sphere. Obviously, the engineering solution is not so easy. Spherical pressure vessels are extremely hard to make. While NASA may choose to meticulously manufacture perfectly spherical, carbon fiber cryogenic tanks,2 most applications demand a cheaper, more pragmatic solution. Something that spreads strain realistically well, and can be manufactured economically and reliably.
The resulting vessel shape is one that anyone who has ever visited a petrol station or used a camping stove will be familiar with: a primarily cylindrical vessel with a convex “head” at each end.
The steel cylindrical pressure vessel matches the demands of various pressure vessel applications, but customers should not be taken in by the familiar appearance – regardless of being commonplace, these vessels are meticulously engineered to favor ease-of-production, while retaining a robust and resilient geometry.
The cylindrical middle section can be easily developed from a rectangular piece of steel, while a lack of abrupt edges guarantees strain is distributed well. Although hemispherical heads offer better strain distribution, shallower heads are often used instead.3 Recognized in the industry as “dished” heads, they are an effective compromise between strain minimization and manufacturability.4 These heads are far easier to create and can achieve the same resistance to pressure by being made somewhat thicker.
The Different Geometries of Dished Heads
Dished heads usually have one of two geometries: semi-ellipsoidal or torispherical. Torispherical heads, (also referred to as Klopper or Decimal heads) consist of a fixed-radius dish, coupled to the cylinder by a toroidal “knuckle”. The relative ease of manufacturing has made torispherical heads the most widespread pressure vessel head shape, finding application in recompression chambers, distillation towers, petrochemical plants and a range of storage applications.
Semi-elliptical heads are another regularly used option – deeper and more spherical than a torispherical head, they are more tough and thus more expensive to create, but can handle more challenging applications. Semi-elliptical heads are better matched to marginally higher-pressure applications where entire cylinder length is still crucial.
Manufacturing Steel Dished Heads
Manufacturing steel dished heads has two key stages. Firstly, the steel is manufactured to the correct thickness and cut to shape, typically using numerically controlled plasma cutting machines or industrial circular shears. Once cut to shape, the steel is shaped into a head using either “flanging” or “spinning”. In the spinning approach, the steel is spun on a hydraulic lathe and pressed to a tool.
The tool shapes the steel to the preferred head shape and can regulate both the knuckle and dish radius, allowing the whole head to be manufactured in one go. Flanging is a two-step process engineered to expedite the final assembly of the cylinder: The steel is cold pressed into a shaped cap, then formed with a pressure roller so that it displays a straight flange at the point of connection with the cylinder.
Liquids and gases at higher-than-ambient pressures are uncooperative even at the best of times, and extreme caution must be observed in the production of cylindrical vessel heads to guarantee resistance to corrosion, and adequate tensile strength to endure the pressures of the proposed application. The history of pressure vessel development and operation is fraught with accidents– and consequently, pressure vessel manufacture is closely regulated and compliance to strict guidelines is important.5,6
The efficient and reliable production of dished heads for pressure vessels requires both a detailed knowledge of the infrastructure and the materials involved to precisely manufacture and market them.
Steel Dished Heads Provided by Masteel
Masteel UK is keen to remove the problems involved in dished head production by leveraging its expertise as a global steel manufacturer. Working with many worldwide manufacturers, Masteel supervises all elements of the production of dished heads, from steel production to shipping of the final product. Masteel stocks pressure vessel grade steel that has been strictly tested to meet the demands of the industry, including testing for resilience to the effects of hydrogen induced cracking (HIC)[7]. Masteel is able to manufacture steel and supply it to a manufacturer faster than normal dished head producers can procure it, enabling fast production of dished heads that adhere to precise specifications.
References and Further Reading
- Lei Zhu & J T Boyle 2000. Optimal Shapes for Axisymmetric Pressure Vessels: A Brief Overview. Journal of Pressure Vessel Technology. 122 (443)
- https://www.nasa.gov/news-release/nasa-tests-game-changing-composite-cryogenic-fuel-tank/
- Sourabh Lawate & B. B. Deshmukh. 2015. Analysis of Heads of Pressure Vessel. International Journal of Innovative Research in Science, Engineering and Technology. Vol. 4, Issue 2.
- http://pveng.com/comparison-between-head-types-hemi-se-fd-and-flat/
- http://www.iaeng.org/publication/WCE2010/WCE2010_pp1120-1123.pdf
- http://www.legislation.gov.uk/uksi/2016/1092/pdfs/uksi_20161092_en.pdf
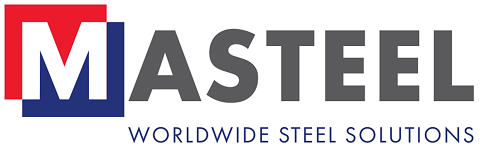
This information has been sourced, reviewed and adapted from materials provided by Masteel UK Ltd.
For more information on this source, please visit Masteel UK Ltd.