Viatran develops pressure transmitters with four different pressure sensing technologies. The company analyzes the requirements of an application and selects the technology that ideally serves that application. The four technologies are gage, bonded foil strain gage, ceramic piezoresistive, silicon piezoresistive, and variable capacitance. Each one is perfectly suited for different applications and has its own benefits and limitations.
Bonded Foil Strain Gage
Bonded foil strain gage technology works based on Wheatstone Bridge circuitry. A balanced Wheatstone Bridge is an electrical circuit having four branches, each with a resistor of equal value. Bonded foil strain gage pressure sensing technology involves bonding four metal foil strain gages to a metal diaphragm as illustrated in the accompanying diagram. These strain gages correspond to the four branches of the circuit and serve as the four variable resistors in the circuit. In the diaphragm’s undeflected state (zero pressure applied), the Wheatstone Bridge is balanced, and voltage output is not measured.
The diaphragm reacts to applied pressure by deflecting into a bell-shaped curve. The strain gages experience strain – the outer two gages experience compression, and the inner two experience tension (see Figure 1). Their values of electrical resistance alter when they are strained. When their resistance values change, the Wheatstone Bridge becomes unstable, and a voltage output can be measured across it.
.jpg)
Figure 1. Bell shaped deflection of strain gage sensor.
The greater the pressure applied to the diaphragm, the more it will deflect. The amount of strain on the foil strain gages and the variations in their electrical resistances are proportional to the deflection of the diaphragm. The voltage output across the Wheatstone Bridge is then also proportional to the deflection of the diaphragm. Viatran establishes the pressure applied by measuring this bridge output voltage.
Bonded foil strain gage is the most durable and reliable of the four technologies. It can be used in ultra-high pressure applications (0-100 through 0-100,000 psi). Its durability makes it ideal for applications which experience shock, pressure cycling, and vibrations. Another key advantage of this technology is that the foil strain gages can be matched and bonded with great accuracy; there is no need to add any temperature compensating devices within the transmitter.
The key limitations of bonded foil strain gage sensing technology are its poor performance in low (<0-100 psi) pressure ranges. If the diaphragm is very thin, the strain gages start to interfere with the diaphragm’s motion.
.jpg)
Figure 2. Strain gages on a machined sensor.
Silicon Piezoresistive
Silicon piezoresistive technology is similar in concept to bonded foil strain gage-like piezoresistive on a diaphragm in a Wheatstone Bridge circuit arrangement. However, this sensing technique utilizes silicon piezoresistive embedded in a silicon diaphragm. Silicon piezoresistive provide a strong output signal in lower pressure ranges. They also have better sensitivity to pressure inputs.
Though not as sturdy as foil strain gage technology, silicon piezoresistive technology is better matched for lower pressure uses. It is used in the pressure ranges of 0-2 through to 0-4 psi. Viatran uses this sensing technology in these low pressure applications as well as for liquid level measurements.
The silicon piezoresistive sensing technology is not matched for applications which undergo high level shocks, pressure cycles, or vibrations, because of the weakness of silicon piezoresistive. It is also constrained by its relatively low upper pressure limit, to applications that do not surpass 400 psi. An additional restriction of this technology is that it is tougher to match and bond silicon piezoresistive to the levels of accuracy that one can achieve in bonded foil strain gage technology. Therefore, electrical compensation must be used to preserve performance specifications.
Ceramic Piezoresistive
Ceramic piezoresistive sensing technology is also similar in concept to bonded foil strain gage technology. This sensing technique uses conductive ink deposition on the reference side of a ceramic diaphragm. The conductive ink forms the variable resistance strain gages in a Wheatstone Bridge circuit. Like ceramic piezoresistive, this technology provides a robust, sensitive output signal in lower ranges.
Ceramic piezoresistive technology is somewhat more rugged than silicon piezoresistive. It is used in pressure ranges of 0-15 psi to 0-1500 psi. The ceramic wetted face is beneficial in applications where one cannot use metallic wetted parts, such as level measurement of corrosive fluids. An additional advantage of this sensing technology is its cost effectiveness.
A disadvantage of ceramic piezoresistive sensing technology is its low upper pressure limit. The molecular structures of ceramics are such that they do not yield before they fail fully. Whereas the elasticity of metals allows the reuse of a transmitter that has been overpressured, the brittleness of the ceramics results in burst failures when they are overpressured. Ceramic piezoresistive sensing technology is not appropriate for use in applications which experience shocks, fast pressure cycles, or vibrations.
Another constraint of this technology is that similar to silicon strain gages, it is tougher to match and bond ceramic strain gages, to the levels of accuracy that one can achieve in bonded foil strain gage technology. Therefore, as with silicon piezoresistive, electrical compensation must be used to preserve performance specifications.
Variable Capacitance
Variable capacitance pressure sensing technology is essentially different from the first three. This technique uses variations in the capacitance of two plate capacitors to establish variances in pressure. It is suitable for applications that require “wet – wet” pressure input arrangements, i.e., where media exists on both sides of the transmitter.
.jpg)
Figure 3. Typical variable capacitance sensor (cross section).
This technology offers superior sensitivity in low-pressure ranges. Viatran uses variable capacitance sensing technology in its differential pressure transmitters, but it can also be used efficiently for gage and absolute pressure measurement.
Viatran’s variable capacitance pressure sensing technology employs three thin metallic diaphragms (see Figure 3). The outer two are passive diaphragms (meaning they do not have spring constant), and are the wetted surfaces of the transmitter. Splitting the two outer diaphragms is a silicon oil fill. Within this oil fill are two conductive ink-coated, ceramic plate electrodes and an active inner diaphragm.
The inner diaphragm is known as an active diaphragm as it is pulled taut in the manufacturing process and thus possesses a spring constant. It is hydraulically coupled, via small holes in the electrodes, to the outer diaphragms.
A charge is created between the electrodes and the inner diaphragm. Two capacitances then exist – one between each electrode and the inner diaphragm. As long as the outer diaphragms have equal pressures on them, the inner diaphragm is not deflected and those capacitances stay equal.
If a pressure difference occurs between the two inputs of the transmitter, the wetted diaphragm on the side with the greater pressure deflects inward. This deflection pushes more oil via the holes in the electrodes and against the inner diaphragm form that side, successfully moving the pressure on the wetted surface to the inner diaphragm. The inner diaphragm then deflects towards the opposite electrode.
Since capacitive storage is a function of the distance between each of the electrodes and the inner diaphragm, a greater capacitance develops between the inner diaphragm and the electrodes from which it is at a distance. The difference in capacitances provides a measure of the pressure variance in pressure.
There are numerous benefits to variable capacitance pressure sensing technology. First, it is very sensitive to small variations in pressure; down to 1 inch of water column pressure. Moreover, the outer diaphragms can only deflect the onset of the small oil-carrying holes, and there is not sufficient oil fill to deflect the inner diaphragm far enough to cause it to fail. In this fashion, Viatran’s variable capacitance pressure transmitters are engineered to prevent diaphragm ruptures and the requirement for repeat recalibrations caused by overpressures. The design is particularly well matched to applications where high overpressures take place.
Variable capacitance pressure sensing technology is more multifaceted and expensive than the other technologies. An additional problem is that signals from variable capacitance transmitters can have more noise compared to the other three suitable for low-pressure applications.
The low-level voltage output signals from all four of these sensing technologies can be amplified and/or conditioned to offer high level (0-5 volts, 0-10 volts, or 4-20 milliamps) outputs.
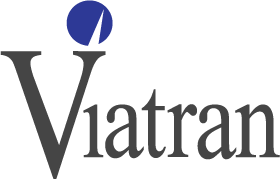
This information has been sourced, reviewed and adapted from materials provided by Viatran.
For more information on this source, please visit Viatran.