Internal field calibration (cal) signal is a significant feature of several Viatran pressure transmitters. This feature allows rapid field set-up as the transmitter is not removed from service and a precise pressure source is not needed. The field cal signal “simulates” a known pressure that enables zero and span adjustment, and in turn, guarantees accurate transmitter measurements. It can be subsequently used for calibrating safety limit alarms and data acquisition equipment, as well as for ranging units to read lower pressures at Full-Scale Output. This article describes how the calibration feature works and how to use it.
The “Cal” Signal
A block diagram of a pressure transmitter is represented in Figure 1. The pressure sensor provides an electronic linear output which is proportional to the applied pressure. The slope of the input/output line is the sensor’s sensitivity and is expressed as a ratio of signal to pressure, i.e., Volts/PSI.
The calibration signal is a fixed, stable electronic signal that is added to the sensor output upon activation. As the cal signal is constant, the electronic signal it generates is equivalent to a constant pressure. For instance, assume that the sensor generates 1 Volt for each PSI of pressure applied. In case the cal circuit is designed to generate 1 Volt, activating the cal feature would be equivalent to applying precisely 1 PSI to the sensor.
Converting the sensor signal to the electronic format required, such as 0-5 VDC or 4-20 mA, is the function of the signal conditioner. The signal conditioner is also capable of performing radio frequency interference protection, temperature compensation, error correction, and enable zero and span adjustments.
.jpg)
Figure 1. Block diagram of a pressure transmitter.
Activating Field Cal
The specific Viatran product controls the activation of the cal signal. Some of Viatran’s pressure transmitters use a two pin calibration connection (see Figure 2). The calibration circuit is activated by shorting these pins together.
Other Viatran transmitters use a special signal conditioner with all internal controls connected to magnets (see Figure 3). When the external magnets are driven with a screwdriver, the internal magnets follow and adjust the controls. Turning control magnet number 3 on this “magnetic module” 1/4 turn (to about three o-clock) activates the cal feature.
Safety and reliability are the major advantages of magnetic coupling. Thanks to the permanent hermetic seal, the electronics are protected from penetration of fluids or explosive gasses, preventing a failure or explosion. This feature makes it possible to calibrate the transmitter without operation shutdown.
.jpg)
Figure 2. Connection diagram for a typical pressure transmitter.
.jpg)
Figure 3. Magnetic coupling safety drives control.
.jpg)
Figure 4. Connection diagram for a typical magnetic module transmitter.
Using Field Cal
Tools Required:
The only materials required are a calculator to help compute the calibration current, a screwdriver to activate the cal, and a meter that measures transmitter output.
The calibration pressure is laser etched onto the body of every transmitter. This value’s accuracy is within 0.1% of the value stated.
General Procedure:
- Remove the pressure from the transmitter
- “Zero” the transmitter by adjusting the zero control
- Establish the calibration current (or voltage) by the ratio:
.jpg)
- Activate the cal signal
- Adjust the span control until the output of the transmitter equals the calibration current
- De-activate the cal signal
The original zero is subject to change owing to the interaction of the zero and span controls. This is particularly true where high ranging or suppressed zeroes are concerned. After re-zeroing the transmitter, the process has to be repeated until the zero does not considerably change. Generally, pressure transmitters can be span adjusted ± 10% of the standard pressure range of the transmitter.
Example 1: Simple Ranging of a Transmitter
Based on the specific model, Viatran transmitters can be ranged 3 to 5 times which means a 10,000 PSI pressure transmitter can be adjusted to generate a full output at 2,000 PSI. In this example, a 10,000 PSI transmitter is adjusted to provide a 4-20 mA signal from 1 to 3,500 PSI. The cal pressure stated on this specific unit is 2,042.4 PSI.
In short, the preferred output of the transmitter is:
PSI Input |
|
Signal Out |
0 |
= |
4 mA |
2,042.4 |
= |
Cal Current |
3,500 |
= |
20 mA |
With the help of the above formula, the calibration current is determined by:
2,042.4 |
|
Cal Current |
3,500 |
= |
16 mA |
Hence, the cal current is 9.3367 mA. This value must be added to the 4 mA zero current, making the cal current 13.3367 mA.
- Insert a current meter into the 4-20 mA loop as depicted in Figure 4 given above
- Remove pressure from the transmitter
- Adjust the Coarse and Fine Zero controls (#1 & #2 respectively) until the output is 4 mA
- Activate the cal signal by turning control #3 to 3 o’clock - output will increase
- Adjust the span control (#4) until output is 13.3367 mA
- De-activate the cal signal by turning control #3 to twelve o’clock
- Re-zero the transmitter if required and repeat until the zero pressure output and cal pressure output are as calculated
The transmitter is now calibrated to 0-3,500 PSI with a 4-20 mA output.
Example 2: Non standard Zero
When pressure cannot be removed from the sensor, the sensitivity of the transmitter can still be adjusted by the cal signal.
In this example, a 0-100"WC tank level transmitter has to be ranged to 0-80", yet the tank contains 12” of water. While the transmitter cannot be removed or the tank emptied, the unit can still be calibrated. 34.1"WC is the calibration pressure stated on the transmitter.
In this example, consider the 12"WC pressure on the sensor a “fake zero” pressure. In order to accurately calibrate the unit, it is necessary to determine the “fake zero” output. Add the FZ current to the “true zero” current (4 mA) and then add this sum to the calculated cal current to acquire the correct calibration output. Summarized, the output of the transmitter is:
Level in "WC |
|
Output |
0 |
= |
4 mA |
12 |
= |
“Fake Zero” |
34.1 |
= |
Cal Current |
80 |
= |
20 mA |
- Determine the “fake zero” output by the ratio:
12" WC |
|
FZ mA |
80" WC |
= |
16 mA |
- FZ = 2.4 + 4 mA
- Adjust the zero to 6.4 mA
- Calculate the cal current:
34.1" WC |
|
Cal mA |
80" WC |
= |
16 mA |
Cal = 6.82 mA. Activating the cal signal should shift the output by 6.82 mA. Since the transmitter is at a “fake zero” of 6.4 mA, activating the cal results in a 6.82 + 6.4 = 13.22 mA output.
- Activate the cal and adjust span for a 13.22 mA output
- De-activate cal and readjust zero for 6.4 mA
- Repeat if necessary - when the tank is empty, the output should be at 4 mA
Calibrating Data Acquisition Equipment
After calibrating the transmitter’s zero and span to the preferred range, the cal feature can be subsequently used to confirm the operation of data acquisition equipment “down the line.” Upon activation of the cal, the display which should have been adjusted for special ranging should read the calibration pressure. The panel meter can then be adjusted so as to read the calibration pressure stated on the transmitter body.
The cal feature can also be used to observe if certain limit alarms are activated. In case the limit alarm is set to the calibration pressure or below, then activating the cal should trip the alarm. Using the cal in this fashion is a rapid way to check the functionality of the emergency shut down equipment.
Caveats
While this cal feature offers several advantages, there are precautions to consider.
Use of the cal signal presumes that the sensors’ response to pressure does not change over time. Sometimes, environmental factors influence the sensor characteristics, such as long-term exposure to corrosive media, which may erode the sensing diaphragm until it is oversensitive.
The cal signal only simulates a pressure and may vary from its stated value up to 0.1%. Applying a known pressure to the sensor, such as that from a dead weight pressure generator, will simulate the actual operation more closely.
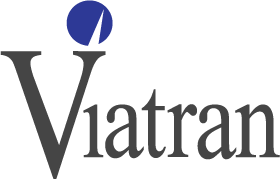
This information has been sourced, reviewed and adapted from materials provided by Viatran.
For more information on this source, please visit Viatran.