Introduction to Techniques Associated with Fluid Level Measurements
In Gangster movies of yesteryears, when the police were asking informants about information, they would ask this question, “Is that information on the level?” What they are asking is whether the information is accurate. Engineers with a large tank can relate to this: they need to know if their media is on the level. For a long time, engineers have been using floats and a site glass to gauge the level. Technology has advanced now. Today, an engineer can easily determine the level using technology.
There are several places to turn.
Hydrostatic head pressure: the level of a tank is measured by measuring the head pressure and converting that signal into a level output. Pressure sensors are a conventional sensing technology. Gage and differential pressure sensors are easy to use and install, and they are suited for various tank level applications and measurements. They can be either flush mounted on the tank or submersed in the media. Hydrostatic pressure sensing can be difficult in corrosive environments that destroy the sensor materials, or dirty liquids that clog small orifices. A submersible pressure sensor will be unaffected by foam or splashing, as it's in the media. However, the media density can influence accuracy.
A Bubbler level system uses compressed gas and submerged tubing in tandem with the sensor to measure the level of the fluid. Bubbler systems are best suited for level measurement of open channel run-off systems or duct and tank situations where foam, debris, surface turbulence, or steam makes standard methods of level measurement unfeasible.
.jpg)
Ultrasonic level sensors are rapidly growing sensor types. These sensors are mounted above the process vessel and they detect the surface by transmitting a series of ultrasonic pulses towards a surface. The time taken for the reflected echoes to reach the sensor face are measured and translated to distance for transmission as a current loop output. As they are separated by at least several inches from the process, they are not likely to be affected by the media type and are useful in sanitary applications.
Sound reflective objects inside the "beam angle" and range may have an effect on ultrasonic sensors, so the installation must be carried out carefully in order to eliminate "false echoes". Splashing, dust, foam, or even fog may lead to erroneous readings.
An extension of the ultrasonic level sensing is radar level sensing. Radar sensors make use of low power microwave radiation for detecting the liquid surface. Similar to Ultrasonic Sensors, this technology has benefits that are suitable for the requirements of special applications encountered in food, beverage or pharmaceutical production. Radar level sensors are used in reflective liquids that have vapors, a foaming surface, or a dusty condition beyond ultrasonic wave capabilities.
Capacitance sensors depend on the various dielectric properties of air and the media for level detection. With conductive liquids, an insulated active electrode and the tank wall form a capacitor. As the level varies, the dielectric property of this "capacitor" will vary linearly. A cable or a bare metal rod acts as the electrode in non-conductive media. Advanced measuring techniques using insulated concentric sensors enable interface level measurement of liquids containing differing foam, oil, or water levels. Tank grounding for capacitance is highly technical, so knowledge of the tank materials and grounding is very important.
An Engineer Can Determine Level Using Technology
Selection Criteria
Understanding the electrical and mechanical configuration of the vessel/tank in question is crucial to choosing the right level sensor. Does the sensor come in the required range or length to suit the application? Can the sensor be merely installed, or is it necessary to specify a unique mounting hardware?
Are any internal devices present inside the vessel, or conditions, such as spraying or splashing liquids, which will interfere with the sensor selected? For example, splashing can damage the accuracy of radar and Ultrasonic sensors. As a submersible or tank mounted sensors sits in the media, splashing has no depredating effect on accuracy. However, a submersible sensor might not work if the media is very harsh.
How important is the accuracy of the sensor in the application? If the media has a high cost per gallon, then accuracy is likely to be critical. Does the level measurement system need specific approvals for use? If users are interested in altering the manner in which they measure level, will the new solution offer the required electrical interface for present and future methods of operation? Does electrical installation demand additional enclosures to house intrinsic safety barriers, interposing control relays, etc.?
Installation Criteria
Almost all level sensors are designed for simple installation into standard fittings. Although float level sensors often have small process connections, the float may need a larger opening requiring adapters.
Recommendations
.jpg)
There are level sensing technologies to enable the level sensing of almost any fluid with high degrees of accuracy. Some are very inexpensive, while others are very simple. In the case of volatile media, approvals become a problem. Sanitary applications also demand certain approvals. Careful review of the specifications for installation and conditions to avoid will help users to establish the best sensor or group of sensors for their application.
As with all safety systems, never depend on a single piece of apparatus to prevent or warn against unsafe fluid levels. The wrong solutions or a bargain solution will prove to be more costly in the long run.
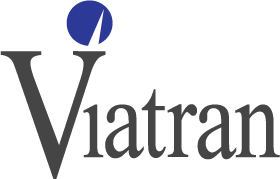
This information has been sourced, reviewed and adapted from materials provided by Viatran.
For more information on this source, please visit Viatran.