Nowadays, there are products like containers, valves, radiators, storage tanks, and drums that must be tested for leaks so as to ensure the highest quality. There are also processes such as bonding, welding, or gasketing that require leak testing. One of the most common methods for detecting leaks is pressure decay. While helium and ion leak detection methods are effective, they are more time consuming and demand expensive equipment.
With the help of a pressure sensor, pressure decay works well because of its simplicity. By pressurizing the test piece and then isolating it from the pressure source, any subsequent loss of pressure can most likely be attributed to a leak in the product.
There are two methods that can be used to measure pressure decay:
Method 1
Figure 1 depicts a plastic container being tested utilizing a gage type transducer. If the container is pressurized to 100 psi and then the valve is closed, the transducer will sense a leak/decay in pressure in the container, if given sufficient time.
.jpg)
Small leaks can be detected in this manner, although the process can take a long time. Due to hysteresis, nonlinearity, repeatability, etc., if the transducer’s total error band is 1%, then a leak cannot be accurately detected until the pressure drops to less than 99 PSI (100 PSI – 1% TTL Error band). It can take several minutes to detect very small leaks.
Method 2
Using a differential pressure transmitter enables a more sensitive leak detector. At the beginning of the test (figure 2), valves #1 and #2 are open. The supply pressure is applied to the test system, and both sides of the container and the transmitter are pressurized to 100 PSI. Valve #2 is then closed. The line pressure is at 100 PSI on both sides of the sensor because of which the output from the transmitter is zero. Valve #1 is then closed.
.jpg)
If a leak is present in the container, the low side of the transmitter will begin to lose pressure. If a 0-5” WC transmitter is used, and assuming that there is a 1% total error band, a leak will be detected when the pressure decays a minimum of 1% of 5” WC. This amounts to a drop of 0.05” WC.
As can be seen in the first example, one needs to wait until the pressure decays 1 PSI or 27.68” WC. The use of the differential system produces 500 times faster results, decreasing the total test time required.
Not every leak test application needs the rapid response time or the sensitivity provided by a differential transmitter. Viatran offers a solution for whatever is the need. For more information or assistance with their application, customers can contact a Viatran Applications Engineer.
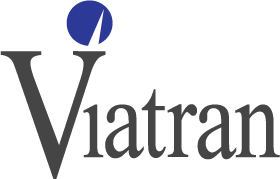
This information has been sourced, reviewed and adapted from materials provided by Viatran.
For more information on this source, please visit Viatran.