The combustion of residues obtained from refinery processes can effectively be used as an alternative fuel to process steam, supply power, usable heat and process water for the refinery. Therefore, an energy circulation is formed which efficiently deals with environmental aspects and reduces operational costs in the refinery.
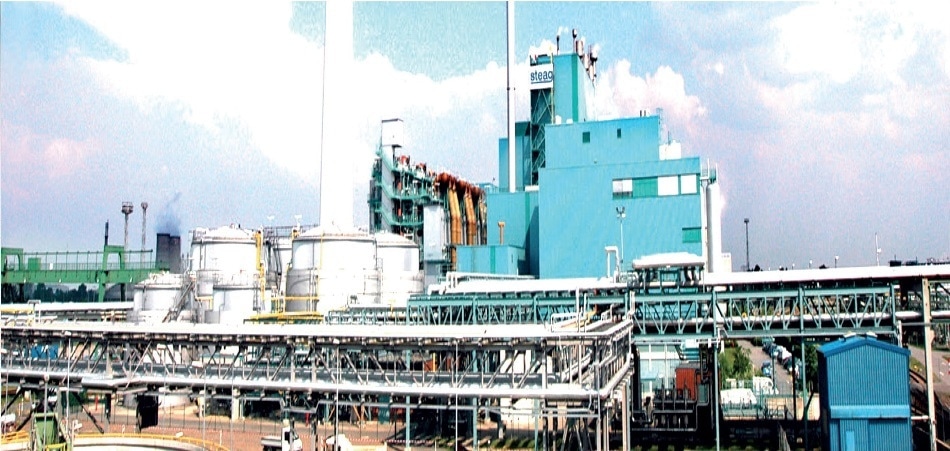
Power plant in a refinery
The Combustion Process
Before entering the boiler, the refinery residues, the so-called black material like bitumen and other long-chained hydrocarbons with a high viscosity need to be liquefied and cracked to smaller hydrocarbons at 260 °C in a Visbreaker. The subsequent combustion process is controlled by monitoring carbon monoxide and oxygen, generally using in-situ measurement technique.
DeNOx
In flue gas treatment, the first step is to reduce NOx from 600 mg/Nm3 in an SCR process at 360 °C (high-dust installation). At the outlet, NH3 and NOx are measured, where NH3 denotes the efficiency of the SCR process and NOx is merely monitored.
Note: Sometimes NO is also measured before DeNOx for controlling purposes.
Flue Gas De-sulfurization (FGD)
Downstream of the SCR, the flue gas is cooled down in two steps: passing an air preheater and a quench cooler. The preheater is used to heat fresh air before it enters the combustion process in the boiler, thereby increasing the efficiency of combustion. The quench cooler effectively lowers the flue gas temperature to approximately 55 °C by direct dosing of water. The flue gas passes through the electro filter for removal of dust and then through the scrubber for desulfurization. Upstream of the FGD, right before the quench cooler, there are important gas measurement points for the O2 and SO2 reference value. At this point, SO2 concentrations are notably high, with values exceeding 5 g/Nm3.
Stack Emissions
The last step is to draw the cleaned saturated gas through a steam gas heater and introduce it into the stack, where the emissions of NOx, SO2, O2, and CO are measured and reported.
Measuring Task – Measuring O2 Before Flue Gas De-sulfurization
Upstream of the FGD, along with SO2, the O2 reference value is also measured for calculating normalized emissions. At this measurement point, special requirements for the analytical equipment are robustness and drift stability, as calibrations are only performed every four weeks. Robustness is especially important at this point, as the formation of SO3 has to be expected and SO2 concentrations are higher than 5 g/Nm3.
ABB Solution: Magnos28
The Magnos28 represents the future of paramagnetic oxygen measurement, leveraging ABB's pioneering technology leadership and more than seven decades of innovation in the field of continuous gas analysis. This innovative product completely transforms the paramagnetic oxygen analysis, replacing the glass dumbbell with a ground-breaking new silicon sensor, the microwing, and automating traditional manual manufacturing processes leading to levels of quality and reproducibility above anything that is presently available on the market.
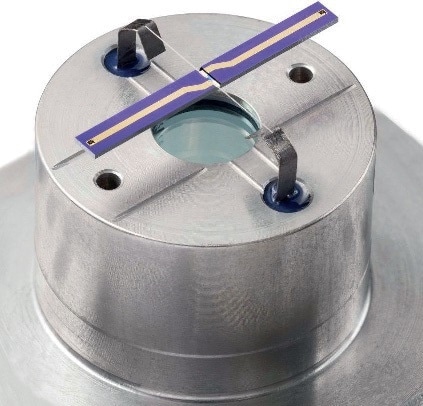
Magnos28. Sensor with microwing
Revolutionary New Microwing Technology
The Magnos28 introduces a basic revision of the sensor design. The glass dumbbell with its mirror, circuit path, mounting and taring weights is replaced by the patent-pending microwing as an all-in-one device with no additional attachments. By the application of the latest semiconductor based production technologies, multiple sensors are manufactured on a wafer slice which is completely a new approach to magnetomechanical oxygen measurement.
Absolutely reproducible silicon sensor elements, the microwing, are the basis for a product which shows potential for greatly improved precision and repeatability. As the microwing sensor has a high width-to-thickness ratio, very low mass, and optimized magnetic field distribution in the measurement position, it reacts very accurately to oxygen concentration changes.
Refined for Challenging Applications
Magnos28 provides robustness and reliability in this measurement environment. Neither lead solders nor glue, which could react with the gas matrix, affect the reliability of the measurement. Specially selected coatings give protection to the sensitive parts of the internal chamber like the pole shoes.
Thus, excellent measurement properties are obtained with improved drift stability even if high SO2 concentrations are present. Since Magnos28 measures the pure magnetic properties of dia- and paramagnetic gases - matching the physical values almost with no deviation, cross-sensitivity behavior to other gases like CO2 is under control.
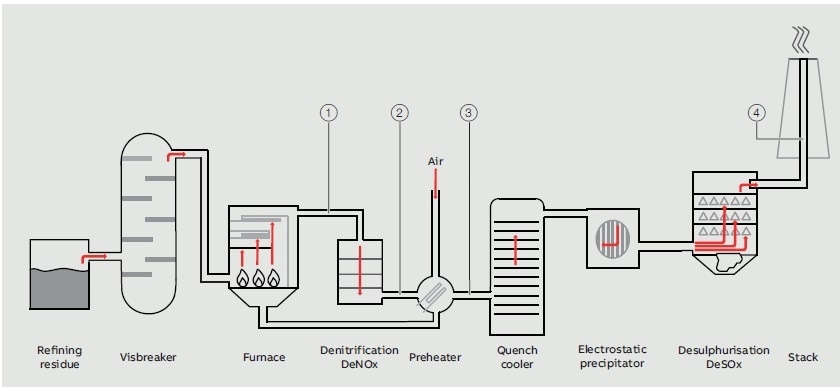
Schematics of the flue gas line in a refinery’s power plant
Summary of Measurement Points and ABB Offer
Table 1. Measurement points in a refinery’s power plant.
Sample point |
Components |
Analyzer / principle |
Remark |
Combustion process |
1 |
O2 , CO |
AZ40
Magnos28, Uras26 |
In situ
extractive |
DeNOx |
2 |
NH3
NOx
NOx |
25 ppm
600 mg/Nm3
100 mg/Nm3 |
LS25, LS4000
Limas21 UV |
|
Flue Gas De-Sulfurization (FGD) |
3 |
SO2
O2 |
5250 mg/Nm3
4,5 Vol% |
Limas21 UV
Magnos28 |
Quartz cell |
Stack Emissions |
4 |
SO2
NOx
CO
O2 |
175 mg/Nm3
100 mg/Nm3
5 mg/Nm3
5 Vol% |
Uras26
Magnos28 or electrochemical cell |
EN15267
EN15267 |
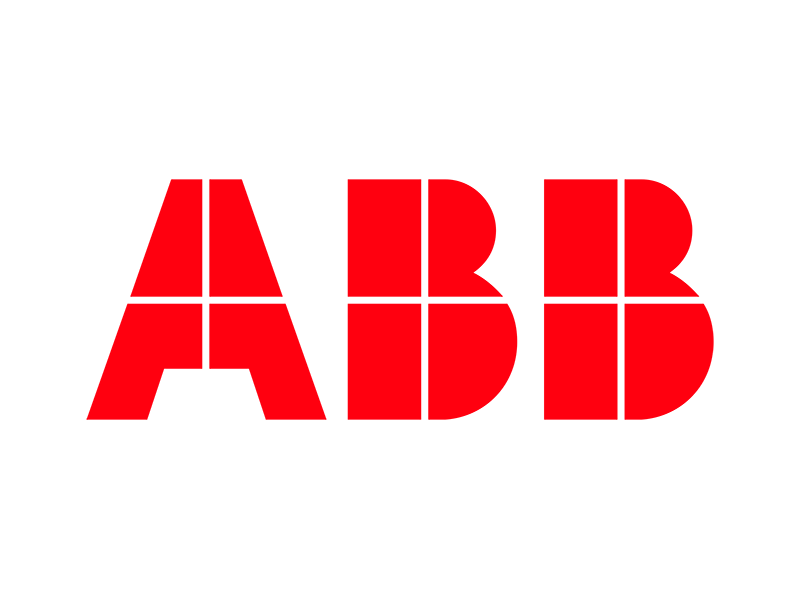
This information has been sourced, reviewed and adapted from materials provided by ABB Measurement & Analytics.
For more information on this source, please visit ABB Measurement & Analytics.