The prevention of metal contamination in food has long been of importance to the food manufacturing/packing industry. This is due to the fact that during the production process metal parts can enter food products such as baby food, fruit juice, frozen or canned vegetables, spices, flour, sauces, grain, powdered milk, sugar or chocolate. This can cause costly production interruptions, damage claims and product recalls. To prevent this, leaders in the magnetics industry Goudsmit Magnetics have developed new innovative ways to combat these issues.
.jpg)
There has been continuous research into the effectiveness of various magnet systems. Goudsmit Magnetics pride themselves on using advanced 3D modeling software and a powerful test center to optimize the systems. This is done for ferrous particles and also for AISI 304 and AISI 316(L) stainless steel particles. This is impressive as most suppliers continue to focus primarily on field strengths (gauss/tesla), but experience has shown that this is no guarantee for good metal separation.
.jpg)
The magnetic bar systems are optimized for ferrous particles to obtain the most effective bar diameter, magnet quality, pole thickness, and distance between the bars. It is known that some stainless steel particles can be captured with an air gap of 50 mm, however the result is much better if the particles contact a magnetic bar. In addition to this, AISI 316L particles are only captured when they contact the magnetic bar.
Dairy, milk and egg powder
.jpg)
Iron particles in viscous and pasty products like yogurt, cheese spread and desserts can be carried off after they have been captured. Hygienic magnetic filters have such powerful Neoflux® (neodymium) magnetic bars that they can remove the smallest iron particles from these products. These can hold them so strongly that they will not be pulled off again.
.jpg)
Fatty powders such as milk and egg powder can accumulate on the magnetic bars. Rotating Cleanflow magnets were developed to eliminate bridging on the bars. These magnets remove iron particles from fatty powders from as small as 25 microns. Pure product prevents expensive, image-damaging liability issues as well as expensive spoilage of finished products.
.png)
Cocoa & chocolate
In addition to dairy, iron contamination can be present in incoming raw cocoa beans and during the processing of the finished product. Various types of magnet systems are used to resolve this issue.
.jpg)
Nails and other metal objects can fall in among the cocoa beans during harvesting and packing. Throughout, large pieces of iron are removed from the flow of bulk beans by a magnetic drum separator, bullet magnet, cascade magnet, plate magnet or external pole magnet before the cocoa beans are ground into powder.
External pole magnets can be placed in the powder line and the sugar intake. However, they are also appropriate for the ‘cake dump.’ After the cocoa is pressed, it is removed from the press as large ‘cakes’. Magnetic grids, or Cleanflow magnets, remove the iron particles when the cake is ground.
.jpg)
During final inspection of the cocoa powder, rotating Cleanflow magnets are used. This is in order to prevent considerable damage to sieving machines and pulverizers. This also avoids costly production stops. By rotating the magnetic bars, it ensures that the fatty cocoa powder does not accumulate and stick on the rods.
Goudsmit’s double-walled magnetic filters are a good choice for liquid chocolate. The magnets capture fine iron particles from liquid chocolate, cocoa butter or cocoa liqueur. These filters are suitable for use under pressure. The warm liquid can be pumped between the two walls. This prevents solidification on the wall.
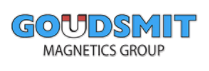
This information has been sourced, reviewed and adapted from materials provided by Goudsmit Magnetics Group.
For more information on this source, please visit Goudsmit Magnetics Group.