Prior to developing the best methods for manufacturing and predicting the performance of polymers that will be used for useful products, it is imperative to have the required knowledge of the thermal properties of these materials, as well as any information that may be required to troubleshoot when the material does not performed as expected. The thermal analysis of polymers provides important information on the following material properties:
- Identification of an unknown polymer
- Determining the best processing temperature
- Cure
- Injection molding
- Extrusion
- Heat welding
- Comparing quality
- Monitoring the effects of aging on the material
- Determining the phase separation
- Estimating percent crystallinity
- Measuring heat capacity
- Determining the stability of the material when exposed to certain thermal environments
- Determining residual cure and Tg as a function of cure temperature/time
- Estimating the degree of cure
- Setting the specifications to meet the material’s needs or limits for end-use conditions
- Designing devices; choosing materials for specific applications
- Evaluating the device performance under operating temperatures
- Analyzing cure or crystallization kinetics
Differential scanning calorimetry (DSC) is a useful technique to address each of the requirements above, as this tool technique possesses various powerful techniques to study the thermal properties of polymer materials. Additionally, DSC also the polymer industry and users with essential information on polymer-based products.
Basics of DSC Analysis
A heat flux DSC contains a single heating block that is comprised of a thermal cell with a sensor that detects the difference in temperature between the sample-filled pan and a similar reference pan that is denoted as ‘empty,’ as it only contains air. When the sample evolves heat through a defined thermal process, such as during a crosslinking reaction, the DSC plot will show an increase in the heat flow that is indicative of an exothermic event. This occurs because the sample sensor detects that the temperature is higher than that which was sense for the reference. If the sample is undergoing a thermal event that causes it to absorb a greater amount of heat than the reference, such as if the material were to melt, the DSC plot will show a decrease in the heat flow that is otherwise known as an endothermic event. During an endothermic event, the temperature sensor will measure a lower temperature for the sample as compared to the reference.
DSC is capable of heating a given material at a controlled rate, such as 10 °C per minute, and monitor the heat flow in an effort the characterize the thermal events of a sample as a function of increasing temperature.
.jpg)
Figure 1. A DSC plot for a polyethylene terephthalate (PET) sample that has been cooled from the melt at an extremely high rate. The plot illustrates both exothermic and endothermic thermal events that occurred during a temperature scan from 50 °C - 300 °C. The endothermic step change, which is otherwise defined as the glass transition, is shown to occur in the first scan, whereas the exothermic peak follows as a result of the cold crystallization process that is then followed by the endothermic peak due to melting.
Most modern DSC instruments are equipped with the ability to measure absolute heat flow by dividing the signal by the measured heating rate, which thereby converts the it into a heat capacity signal. The monitoring of this heat-capacity related signal is a function of the applied experimental conditions in an effort to determine how the heat capacity of the sample may change as it undergoes a phase change or chemical reaction.
The direct measurement of the heat capacity by DSC instruments involves thermodynamic calculations that are automatically performed by the instrument, accompanied by other calculations that must be performed by the operator. The quantity of heat flowing into and out of the DSC sensor is dependent upon the applied temperature, the properties of the sample, as well as the thermal resistance and capacitance of both the reference and sample sides of the DSC cell. A DSC is equipped the technology TzeroTM by TA Instruments Inc., that allows for the instrument to possess the mathematical capability to measure these parameters, thereby allowing this technique to be even more powerful in accurately measuring the heat capacity of organic compounds and polymers. The baseline of the instrument is determined by the heat flow signal in the absence of a thermal event, and by using TzeroTM, the baseline is much flatter and more reproducible for required studies. A more accurate baseline provides users with the ability to identify weak thermal events, as well as improve the accuracy of the heat capacity measurements.
.jpg)
Figure 2. A DSC plot of a heat capacity of a phase change material (PCM) that was measured directly during a temperature scan. The heat capacity (Cp) of the PCM increased by approximately 560 J/(g x °C) during the melt transition that began at -0.3 °C. The peak area of this plot represents the heat of fusion per gram of the PCM material. The plot shown here shows that once the PCM has been cooled below the freezing point and reheated, that the magnitude of the Cp increases at an identical rate. This phenomenon is reproducible as shown by this plot.
Advanced Techniques: Modulating Temperature DSC
Modulating the temperature of a DSC instrument is especially important in improving the measurement capabilities of the instrument. The technique of modulating a DSC is often referred to as MTDSC or MDSC, and involves the application of a sinusoidal temperature modulation that is superimposed over a linear heating rate. During the modulation experiment, the instrument performs a series of mathematical procedures that separate the properties, such as polymer transitions that significantly affect the molecular mobility, that respond to the cyclic heating rate two different components including the reversing and non-reversing signal.
To better understand this procedure, when a polymer in the glassy phase is heated to a specified temperature it can begin to undergo a phase change that induces a liquid-like flow. As the glass transition increases molecular mobility and heat capacity, the ability of the material to be processed in molding and extrusion operations is determined. The glass transition temperature for a particular polymer is denoted as Tg, whereas the change in heat capacity is denoted as ΔCp. To accomplish both Tg and ΔCp in a given experiment, the MSDC signals can be plotted as reversing heat flow vs. Temperature for analyzing Tg, or as reversing heat capacity vs. temperature to analyze the change in Cp.
Some polymer properties that do not respond to the temperature modulation experiment include those that involve time-dependent kinetic transitions such as crystallization, decomposition, evaporation and chemical reactions, such as curing. Any heat flow properties that are associated with these types of thermal events are found in the MDSC plots of the non-reversing signal, in which the MDSC technique separates overlapping events, such as Tg and curing, into two distinct plots to make a powerful analytical tool.
.jpg)
Figure 3. An illustration of the higher resolution achieved using MDSC. The upper portion of the figure shows data for a non-modulated DSC of a petrolatum sample scanned at 10 °C/minute, whereas the lower part of this figure shows the MDSC data obtained for the same sample scanned at 3 °C/minute. Both plots shown here exhibit the same Tg step change at approximately -70 °C, however, the melting peak shown above the Tg shows dissimilarities that exist between DSC and MDSC.
The DSC plot shown in Figure 3 does not have a well-defined peak shape, which limits the ability to pinpoint the exact location of the peak maximum, as well as the start and end points of the experiment that are important in identifying both the melting point and melting range, respectively. On the other hand, the MDSC data shown in Figure 3 demonstrates the complex melting behavior of the sample that can provide useful information on the melting peaks and subsequently the crystalline fractions that exist within the material.
The storage of polymers below Tg for extended periods will typically result in a gradual process of molecular relaxation, which is a phenomenon that occurs when the amorphous polymer chains form abnormally denser regions within the sample. The densification of the polymer can subsequently affect the performance of the material by causing embrittlement, dimensional change and/or the development of internal stresses. DSC is therefore a useful tool in identifying this phenomenon that is otherwise known as physical aging of polymers.
An initial DSC heating scan of physically aged polymers will typically reveal an endothermic peak, which is otherwise referred to as the “enthalpy of relaxation” or “enthalpic recovery” and denoted as ΔHR, that is close to the trailing edge of the Tg step-change. By heating the Tg, the polymer chains are able to move to a more relaxed condition in which the chains spring back to a pre-aging volume and density condition. This movement of the polymer chains will allow for a transition of the ΔHR to occur, in which the magnitude of this peak determines the extent of the aging.
.jpg)
Figure 4. A conventional analysis of the physical aging of a plasticized polyvinyl chloride (PVC) sample using DSC, as well as the Tg and ΔHR overlap. The Tg of the PVC combined with the ΔHR peak illustrates a transition overlap as shown above.
.jpg)
Figure 5. MDSC analysis of a PVC sample, in which an effective separation of the transitions is shown as follows: Tg is separated into the reversing heat flow plot and the ΔHR is separated into the non-reversing heat flow plot. The ΔHR peak can be utilized for the calculation of the magnitude of the physical aging present within the sample.
Quasi-isothermal DSC (QiDSC) is a useful and powerful MDSC technique that utilizes quasi-isothermal conditions to expose the sample to a temperature modulation that is cycled around a single temperature. Depending upon the amount of time that the sample is held at a particular temperature will determine the amount of transitions the material undergoes. This point of the QiDSC will be demonstrated by a plot of Cp vs. time, in which a flat line at the given time point where these transitions occur will be visualized. The end point of this steady state conditions is determined to be the heat capacity of the sample at that specified temperature. This powerful technique can also be used to monitor the isothermal cure of thermosetting polymers, such as epoxy resins, in which the heat capacity of the epoxy decreases as it transitions from an uncured liquid to a solid network. The constant monitoring of the Cp signal will show that the initial drop in the curve will reach a plateau that indicates the reduction in the speed of a cross-linking reaction.
The QiDSC can be used to determine the amount of time the curing network requires to reach the vitrification point that can be calculated from the midpoint of the Cp step change. The vitrification point represents the time at which a given cure temperature requires the Tg of the network to reach the applied curing temperature. Beyond the vitrification time point, the reaction becomes slower and can subsequently require extra processing time or post-baking that will reduce the throughput of cured parts. Acquiring information on the vitrification point can be useful for a comparison between several isothermal curing temperatures in an effort to determine the best curing conditions requires to achieve a maximum cure with the highest throughput.
.jpg)
Figure 6. A plot of the Cp of aluminum oxide at 6 °C, 16 °C, 26 °C and 36 °C. The steady-state end point is labeled according to each temperature as the Cp values. This experiment verifies the accuracy of the DSC technique as it compares the resulting Cp values at the same temperatures according to a number of references in the literature.
Case Studies for DSC Analysis
Case Study I: Identification of Unknown Polymer Using DSC
It is often necessary to identify an unknown polymer, particularly in situations where plastic parts have been purchased from a supply chain that is not directly affiliated with the manufacturer and must therefore be verified through analytical procedures. In these types of situations, most manufacturers will outsource these materials to labs equipped with an infared spectrophotometer (FT-IR), as the data acquired through this technique can identify the chemical family of the polymer. Further analysis of the subclass of the polymer material can be identified by using a DSC temperature scan of the polymer to detect the thermal transitions of the material.
An example in which a DSC temperature scan was used to analyze the polymer subclass is discussed here, in which a molded part designed for use in hot humid conditions was analyzed. In this experiment, FT-IR analysis showed that the plastic was consistent with nylon, a polyamide material, however, since several different types of polyamides are currently available on the market, the IR information was not capable of identifying the precise material. DSC testing was therefore used, in which a small slice of the material was taken. The results of the DSC plot are shown in Figure 7. The final determination of the specific type of polyamide material present in the plastic part was attributed to the following experimental determinations:
- No crystalline melting peak of the unknown material was found, which therefore ruled out the possibility that the unknown base polymer was derived from the commercial aliphatic polyamides, such as nylon 6, as these materials are semi-crystalline in their structure.
- The Tg was found to be consistent with a material that was not only non-crystalline, but also completely amorphous in its structure. This narrowed the unknown polymer to several commercial semi-aromatic polyamides that contain high levels of benzene ring that are known to be completely amorphous in their structure.
The results of this DSC experiment performed here demonstrates that the primary polymer composition of the unknown material was a semi-aromatic polyamide, however the Tg of 188 °C was found to be significantly higher than most commercial grades. By determining these properties of the unknown material, the researchers determined that the material was a possible blend of semi-aromatic polyamide and a reinforcing agent, such as fiberglass.
.jpg)
Figure 7. The DSC plot of an unknown material.
Case Study II: Thermal and Morphological Variations of Different Lots of Material
Any variations in the thermal and/or morphological properties of a polymer material can affect its performance and processability. As these properties can vary depending upon the type of polymer, it is necessary to find and qualify the source of a polymer material to avoid these negative effects. DSC is a powerful tool that can be used to investigate the quality of new stocks of polymer materials, as well as to compare lot-to-lot variations in the Tg, which determines the softening and flow of the material, melting crystallization and the percent crystallinity.
The DSC experiment studied here compared two different lots of poly(tetrafluorethylene) (PTFE), which is a semi-crystalline polymer. Prior to the testing of the material, each lot of PTFE was thermally treated under identical conditions in order to ensure that all materials exhibited the same thermal history to the crystalline phase. Table 1 presents the melting point data and the heat of fusion as calculated from the area of the melting peak. While the melting properties were shown to be practically identical to each other, the heat of fusion values for these lots were different. Of particular interest included the variance in the percent crystallinity of the material, in which PTFE Lot 1 showed a 72% crystallinity, which was significantly lower as compared to the PTFE Lot 2 of 82%. The lower crystallinity value for the PTFE Lot 1 maybe attributed to a reduced material density, and the combination of these properties could therefore have a limited performance ability as compared to the PTFE Lot 2. The higher crystallinity and density of the PTFE Lot 2 is attributed to a lower moisture permeability and higher mechanical strength, thereby allowing this material to be more advantageous for material applications.
Table 1. DSC Data comparing the properties of different PTFE Lots.
.jpg)
Case Study III: Polymer Contaminant Investigation by DSC
Cross-contamination of a resin with a foreign polymer can result from use of a melt processing equipment, such as when an extrusion equipment is not purged currently between the runs, or in the case that a certain type of residual polymer is carried over into the new patch of polymer being processed. While the initial appearance of the mixture may appear to be acceptable, the products that are derived from the contaminated resin may fail quality control testing in the future, or otherwise fail when used in their specified application.
DSC is a useful tool to identify the presence of contaminated polymeric materials, particularly when the thermal properties of the contaminant and base resin are significantly different from each other. The control raw materials are suspected to be the contaminant, and can therefore also be analyzed by use of a DSC technique. Using the DSC technique, the contaminated resin can be identified by comparison of the control data with the data of the tested polymer.
An example of DSC being used to identify the presence of contaminated polymeric materials is discussed here, in which a part that was manufactured from a poly(arylether sulfon) (PAES) resin exhibited a low hydrolytic stability that subsequently led to a deformation of the material when used in hot and humid external conditions. A DSC analysis of a small piece of this material showed the presence of two thermal transitions that are further described in Figure 8. Previous analysis of this material by IR did not detect the presence of this contaminant since the spectral signals of the PAES dominated over the contaminant levels.
.jpg)
Figure 8. A DSC analysis of a small piece of a PAES resin that showed the presence of two thermal transitions, in which the transition at 220 °C was the Tg of PAES, whereas the transition at 73 °C showed evidence that a polymeric contaminant was present.
Conclusion
The case above studies represents just a few experimental uses of DSC in which relatively quick results were achieved to answer required questions on the quality of the specified polymeric materials. The DSC results shown here were obtainable in a timely manner without requiring a large amount of samples, controls or method development prior to the analysis procedure. These advantages of the DSC analysis technique allow for it to be a much more powerful analytical tool capable of providing a greater accuracy in measurement and melting point determination.
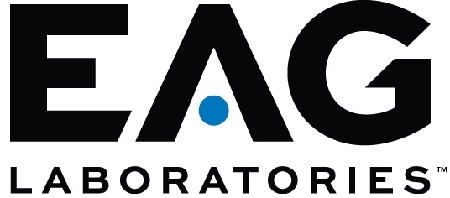
This information has been sourced, reviewed and adapted from materials provided by EAG Laboratories.
For more information on this source, please visit EAG Laboratories.