Automatic hydraulic or mechanical presses of 10 to 1000 tonnes capacity are used to produce ‘green’ or ‘as-pressed’ compacts at rates typically between 300 and 1200 per hour. Actual rates will depend on the press size and the component size and complexity.
A typical compaction cycle, shown in figure 1 is:
• The powder shoe initially moves over the die with the lower punch in such a position that the correct weight of powder is introduced
• After the shoe has withdrawn, the top and bottom punches move relative to the die to compress the powder at pressures between 400 MPa (58,000 lb/in2) and 800 MPa (115,000 lb/in2)
• After compaction the top punch is withdrawn and the bottom punch moves relative to the die to eject the compacted powder
• The filling shoe moves again across the top surface of the die where it refills the die with powder and pushes the green component away onto a moving belt which takes it to the sintering furnace
Generally, compaction tools are produced from conventionally hardened and tempered die steels, but for longer life, carbide inserts are often incorporated into the die.
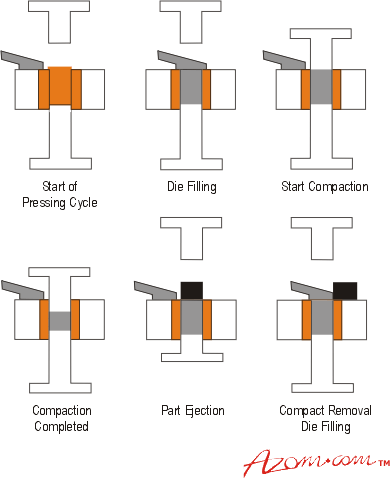
|
Figure 1. A typical compaction cycle.
|
Sintering
The mesh belt is the most widely used type of furnace for sintering. A continuous belt is pulled through a furnace with the as-pressed, or green, components on it. These furnaces usually have two temperature zones, a low temperature (de-waxing) zone to remove the pressing lubricant and a high temperature sintering zone. The maximum stress that the belt can withstand places operational limits on these furnaces, high belt loadings require higher tensions and with time at high temperatures and repeated thermal cycling, the belts stretch and eventually break. An upper limit of 1150°C is usual with loadings of about 20kgs of components per linear metre to ensure acceptable lives.
A reducing atmosphere is always used for sintering to dissociate any oxides present and promote the sintering process by creating clean, very active, powder particle surfaces. The technically appropriate, but most cost effective, atmosphere is used for the sintering process. These vary according to the materials being sintered. For simple iron-carbon or iron-copper-carbon materials endothermic gas produced by burning natural gas is used, whilst for sintering stainless steels with hard to reduce oxide coatings very dry hydrogen/nitrogen atmospheres produced from dissociated ammonia are necessary.
Higher sintering temperatures are used to promote interdiffusion of the constituents of the powder blend or to attain higher sintered densities. Pusher-type furnaces, in which flat ceramic or graphite plates loaded with green components are pushed end-to-end through a retort at 1300°C or higher temperatures are generally used.
Another alternative is the vacuum sintering furnace. These are inherently more expensive to operate so it is unusual to find such furnaces in use for mass produced, near nett-shape iron based components. However, for certain high added value components, it is economically viable to use such furnaces.
Sizing
Further operations may be necessary after sintering to ensure that a critical dimension is within the required tolerance e.g. a bore that has to mate with a precision ground shaft or an external diameter that is required to fit into a ground cylindrical bore. This is usually achieved by cold pressing in a die.
Finishing Operations
Machining
Wherever possible final machining operations are avoided to reduce costs. However there are features, such as re-entrant angles and cross holes, that cannot be developed in the pressed component and must be produced by machining, usually after final sintering. In some cases, where the fully sintered material is too strong to machine economically, the part is pre-sintered to give some strength, machined and then fully sintered to fully develop the properties. Where possible the material composition is altered to enhance its machinability.
Heat Treatment
Powder metallurgy components are usually heat treated, to develop the desired mechanical properties, in the same manner as conventional cast and wrought materials. However, it is important to remember that there is interconnected porosity in the components and that any gaseous process could well affect the core of the material as well as the external surface. The usual processes of carburising, nitro-carburising, carbo-nitriding, etc., can be carried out to provide hardened surfaces.
|