In any chemical analysis, the most important step is sample preparation. The purity of the sample should be ensured before taking a measurement to obtain the optimum results when using any elemental alloy analyzer, irrespective of the technology. Otherwise, the results are always affected at least to a certain extent. There are variations in the effect of dirty surfaces, and certain technologies are more tolerant to sample surface conditions when compared to others.
.jpg)
The extent to which an analyzer can tolerate dirty surfaces is reliant on different variables such as the type of the contamination on the sample surface, the penetration depth of the excitation, analysis spot size, and the nature of physical phenomenon behind the technology.
X-ray fluorescence (XRF), optical emission spectroscopy (OES), or laser-induced breakdown spectroscopy (LIBS) is generally used to perform elemental alloy analysis. Not only is each technology distinctive but the amount of sample preparation required is also different. While XRF can tolerate even very dirty sample surfaces, spark OES mandates proper sample preparation to obtain quality results. LIBS technology is mid-way between the other two.
Since LIBS is a surface analysis method, penetration of the laser beam is essentially only a couple of microns deep. This indicates that the sample surface should be relatively clean to obtain precise results.
Surface Analysis
Essentially, sample preparation is not needed while measuring stainless steels or nickel, aluminum, magnesium, or titanium alloys because a clear patina or thick oxide layer is not formed on the sample surface in these types of samples. In general, even anodized aluminum samples can be directly measured without the need for sample preparation. In the case of a dusty sample or if the sample has cutting fluid, oil, or water on the surface, it is always advisable to wipe it clean using a piece of cloth or something similar.
However, the case is different for copper-based alloys, manganese steels, and low alloyed steels. Heavy patina or thick rust significantly affects the results of the analysis and has to be removed before the analysis, specifically using a laser analyzer. Moreover, any coating, lacquer, or paint is very thick to be burned through using the laser. At times, the coatings cannot be spotted so easily. For instance, alloy wheels are always covered with a relatively thick protective lacquer layer, which has to be ground away before an analysis. Otherwise, the results will not be reliable.
Choosing the Right Sample Preparation Tools
Sample preparation tools can be chosen from a wide variety of tools, for instance, small multi-tools to heavy-duty angle grinders. The following three tips have to be taken into account before choosing an appropriate tool:
- The sample preparation tools must be cordless while operating the instrument at a scrap yard. Hence, the most suggested tool is an angle grinder that has a powerful 18 V lithium-ion battery. Although multi-tools of smaller size are convenient to use and can even fit into the pocket, they might, at times, lack the power while attending to a large number of samples.
- Selection of a suitable grinding material is very important because some grinding material residue will always be left back on the sample surface and certain materials lead to more problems with the analysis when compared to others. Aluminum oxide (Al2O3) is the recommended grinding material.
- Although the effect on the results of the analysis is very minimal while using sandpaper or aluminum oxide grinding discs, it is always advisable to wipe the surface clean of dust before carrying out the analysis. It is not advisable to use grinding tools developed using silicon, tungsten carbide, or zirconium oxide since they might affect the results.
About Vulcan
Hitachi High-Tech’s Vulcan handheld laser analyzer is one among the fastest metal analyzers available in the market. Results can be obtained in one second by just pulling the trigger. Moreover, it is also the lightest and easiest to use. The simple user interface of Vulcan considerably reduces user error, thereby delivering consistent and accurate results than ever.
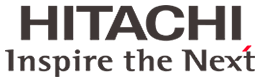
This information has been sourced, reviewed and adapted from materials provided by Hitachi High-Tech Analytical Science.
For more information on this source, please visit Hitachi High-Tech Analytical Science.