The compressed gases industry, which relies on the use of gas cylinders, is an essential pillar in many sectors of everyday life. A huge number of transportable gas cylinders (TGCs) are in use throughout Europe. Considering the vast number of filling operations undertaken (approximately 70,000 high pressure cylinders per day in UK alone), they are incredibly safe. Ensuring Safety of Gas Cylinders Despite their wide field of applications, ranging from off-shore use to hospitals, pubs, garages, and semiconductor laboratories, very few serious accidents occur with gas cylinders. When one does occur it is analysed to establish the cause, and means of avoiding such a failure in the future. Excellent safety statistics have been achieved in many European countries due to good, sound practices based on well founded national standards. This safety is of paramount importance - a 50 water litre cylinder has the equivalent explosive power of 0.4kg of TNT if it discharges suddenly from a pressure of 20 MNm-2. Establishing Pan-European Standards Until recently, each European country had its own approved standards, detailing materials, design codes, and testing. This meant that if a cylinder was intended for use in several countries, it was an inefficient package, with a low weight of gas carried per unit weight of cylinder, and incurred additional costs of multiple approvals/ inspections. To develop a pan-European standard, CEN (Comite European de Normalisation) provided countries with a platform allowing nations to share experiences, to create a portfolio of safe, mutually acceptable standards. This platform involved the reactivation of CEN technical committee (TC) 23. Issues to be Covered in Establishing Pan-European Standards The principal player in the initiation process was the British Standards Institution (BSI) which was awarded the secretariat of CEN TC23. Initial work involved gas cylinder users from the UK, where the British Compressed Gases Association was a major force, and from the European Industrial Gases Association (EIGA). The goal set by TC23 was to overcome a deficiency in the three current European directives dealing with seamless steel, seamless aluminium alloy and welded steel gas cylinders. These directives only cover aspects related to an empty cylinder shell, and not its free trade throughout Europe as a filled gas cylinder. TC23 undertook the task of creating standards for filled gas cylinders and getting agreement between community members. This article looks at technical standards being produced by TC23 - some EN standards are appearing which will ensure that TGCs are manufactured, filled and used safely across Europe. Many standards will eventually be cited in European legislation. The intention is to remove barriers to the free trade of filled gas cylinder packages throughout CEN countries. Best Operating Practice The principal objective of current gas cylinder standardisation efforts in Europe is for a cylinder manufactured and tested in one CEN country to be freely used and filled in another CEN country, without additional tests, requirements or approvals. The standards have been drafted by groups of nationally appointed experts, which have tried to ensure a best operating practice approach - for example, the mandatory ultrasonic inspection of seamless steel cylinders. Existing Standards Widely approved standards from ISO and EC directives were used as starting points in formulating the new standards. Some standards are far less prescriptive and more flexible than before, allowing manufacturers and users of TGCs to cater for potential future needs. An example is the work undertaken for the numerous types of composite cylinders. Other Issues to be Covered TC23 has also tried to create standards for advanced gas packages (greater weight of gas carried per unit weight of the cylinder) such as the high strength alloy cylinders, which are just beginning to enter the European market place in the form of 30 MN.m-2 charging pressure TGCs. TC23 has also kept environmental concerns to the fore at all times, and attempted to conserve energy and material resources where possible. Materials, Design and Testing To date 15 major projects have been undertaken by over 60 people from across Europe. The experts have included TGC users such as BOC Gases Europe and other EIGA members, manufacturers, and inspection/ regulatory bodies including the UK’s Health & Safety Executive. Almost 10,000 hours have been spent creating the various draft standards, and the principal challenges facing the relevant gas cylinder categories are highlighted here. Seamless Steel Cylinders This is the most commonly used high pressure gas cylinder, and is usually manufactured using either a solid billet, a plate, or a tube as the starting material. TC23 refined existing standards, reflecting current European practices and concerns. A low alloy chromium-molybdenum based steel will continue to be the primary steel used for the foreseeable future. Consensus was achieved on acceptable materials, heat treatment, design criteria, safety factors and testing procedures. The technically accurate Lame von-Mises design formula, which has been experimentally proven to predict the elastic behaviour of a TGC, replaces the mean-diameter formula, which has been used in the UK standard for over 20 years. Ultrasonic Inspection A mandatory ultrasonic inspection test has been inserted. This will prevent a number of potentially troublesome cylinders from entering service. Ultrasonic inspection will reject gas cylinders with below the guaranteed minimum wall thickness and those with materials or manufacturing defects greater than 5% of the wall thickness. The additional costs of this test are outweighed by the extra safety offered. Acceptable Cylinder Designs Dedication to maintaining a safe scenario has meant that certain cylinder designs with weldments in the base of nominally seamless cylinders have been excluded from this umbrella, and even those made from tube stock have to be tested more rigorously than cylinders manufactured from billet or plate, which are truly seamless. These changes will mean that a typical high pressure seamless steel cylinder will weigh about 6% less than at present - with a million high pressure cylinders manufactured in Europe each year, a total of almost 3000 tonnes of steel will be saved. Seamless Steel Cylinder Standards A pair of seamless steel cylinder standards cover seamless stainless steel cylinders and the likely 21st century ‘workhorse’ cylinder with a guaranteed minimum tensile strength of 1100 MN.m-2. Material toughness requirements have been considered, as TGCs are often used in hostile industrial environments, where abuse or misuse is beyond the control of the owner. In order to maintain toughness, attention was focused on steel chemistry, to eliminate or minimise the effects of potentially embrittling elements such as sulphur and phosphorous. Two rival compositions emerged - one has extremely low sulphur and phosphorous contents, while the other transforms existing sulphur and phosphorous into non-isotropic inclusions using calcium additions. The new alloys, heat treatment schedules and manufacturing routes have been tested. Tests have included novel burst and cyclic fatigue tests in the presence of controlled defects, which attempt to simulate service damage. Acceptance criteria have been agreed, based on experiments performed by a number of organisations. These flawed cylinder burst/ cyclic fatigue tests are now specified as prototype test requirements, while stringent inspection/ quality checks have been incorporated to maintain a high degree of integrity during routine TGC production. Cylinder Maintenance Despite these rigorous requirements, high efficiency cylinders need careful maintenance. In particular, the internals have to be kept free from moisture or other contaminants by using non-return and positive pressure valves. If the internals do get corroded, then due to the nature of the steel and the high hoop stresses in the barrel, failure is likely within a few months. Welded Steel Cylinders TC23 is responsible for most types of welded steel cylinders, used for transporting liquefied gases such as ammonia, refrigerant gases, and sulphur dioxide. Again, the Lame von-Mises formula was adopted. The basic standard involves varying degrees of non-destructive testing, and covers specific high volume cylinder families with their gas related requirements. Conventional mild steels are used, and a controlled heat treatment of the finished vessel is mandatory. Sensible batch sizes have been agreed, bearing in mind the huge quantities of cylinders being manufactured throughout Europe. A related agreement in the draft has eliminated the need to incorporate a safety relief device in the cylinder shell, for cylinders with a test pressure of at least 6 MNm-2. Aluminium Alloy Cylinders Standards for both seamless and welded aluminium alloy cylinder shells have been formulated. The Lame von-Mises design formula is used, and the standards include current alloys used in the gases industry, such as those based on the 5000 ,and 6000 series, together with a family of high strength aluminium alloys based on the 7000 series. The latter give weight savings of almost 30% compared to conventional 5000 / 6000 series alloys, and are intended to compete with high strength steel cylinders. The technical efficiency of the 7000 series alloy cylinders is not in dispute, but the high copper content (up to 4 wt%) could mean they are not as versatile as the 5000 / 6000 series due to restricted chemical compatibility with some aggressive speciality gases. A major concern with some grades of 6000 series alloys is a potential metallic creep related phenomenon known as sustained load cracking. This results in cracking of the most heavily stressed regions of the cylinder, i.e. the neck and shoulder areas. Following a detailed test programme, appropriate materials tests are incorporated to eliminate all unsafe materials at time of manufacture. However, successful continued use also depends on carefully controlled service conditions. Composite Cylinders Composite cylinders should actually be called reinforced cylinders. There are two main types – hoop-wrapped and fully-wrapped, fig 1. The two standards, one for each category, are probably the least prescriptive of all the drafts from TC23, because they define performance requirements for such cylinders, and have been developed to permit a whole range of construction combinations. For example, metallic and non-metallic liners are acceptable, as are cylinders with no liner. In all cases, a number of different fibre reinforcing materials can be used including glass, carbon and polymeric materials, either alone or in combination. 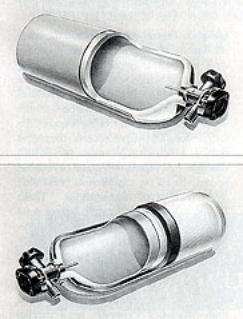 | Figure 1. Hoop wrapped cylinder (top) consisting of a composite overwrap over the metal liner terminating at the shoulder of the liner. A fully wrapped cylinder (bottom) where the composite overwrap encloses the entire metal liner up the neck. | The life of the cylinder is determined by the design and test criteria applied during manufacture, and previous concepts for conventional gas cylinders have been relaxed. For example, fragmentation is permitted (though only for fully-wrapped vessels, and only into three pieces), and depending on the gas, some permeation is permitted from cylinders with a non-metallic liner. Such cylinders will have the highest gas carrying efficiencies, being up to 50% lighter than conventional cylinders. Periodic Inspection and Maintenance After TGCs have been in service for a number of years, they have to be retested to ensure continued safe use. TC23 has developed a number of draft periodic inspection and testing standards for each major family of TGCs. These standards cover seamless steel cylinders, seamless aluminium alloy cylinders, welded steel cylinders, and composite cylinders. A standard for acetylene cylinders has also been drafted to include the special features related to the porous mass present in such cylinders. Test Frequencies Statistical data based on actual operating experiences were collated and studied to establish best operating practice, and an agreed time interval between tests was arrived at, often with alternative intervals for the same gas. Longer time intervals are to be used if certain operational procedures have been in place. For oxygen use in steel cylinders a 10 year retest period can be used if the internals of the cylinder are dry at all times, otherwise a 5 year cycle is required. Test Options Many features in the test regime are well known, including visual inspection of all surfaces of cylinders and a hydraulic pressure test. However, a major breakthrough has been established. Following expert advice from European organisations employing non-destructive methodologies, an ultrasonic inspection test has been incorporated for the seamless cylinder standards. This is an alternative (not mandatory) to the hydraulic pressure test. Elimination of water from the internals of a gas cylinder will be of great benefit where high gas quality is required. The ultrasonic technique is an objective test - the location and size of a defect greater than the permissible size can be quantified and the cylinder rejected. This gives gas cylinder users advanced warning of failure, enabling cylinders to be rejected before the defect has propagated and connected the inner and outer walls. Ultrasonic inspection therefore provides a greater degree of safety than the hydraulic test, which only rarely results in a rejection, i.e. a rupture or a leak. Conclusions Though much of the initial drafting work has been completed, TC23 is now entering a critical phase of its standards development programme, in which technical comments from CEN member states are being assessed by various expert groups. A measure of the drafts’ success will be the degree of acceptance at this stage. The flexible and pragmatic approach adopted by TC23 will ensure that the eventual standards are not just for the 1990s but will have a long shelf-life. Both manufacturers and, more importantly, users of TGCs will be using this portfolio well into the 21st century. |