Plastics retain a high added value throughout their life cycles. Much of this value is lost if a plastic article is discarded at the end of its useful life.
Zeus Industrial Products, Inc. is a manufacturer and processor of highly engineered polymers such as bioabsorbable polylactide (PLA) and lactide copolymers catering to a range of markets, including medical applications. Sustainability is a big part of the Zeus culture and end-of-life matters are progressively considered at the corporate level for all businesses. Recently, the Zeus Research team has created a unique technology for recovering monomers from recycled PLA, whether existing as clean industrial waste or commingled with other plastics. This depolymerization technology can be performed efficiently at comparatively mild conditions of pressure and temperature, and can be viewed largely as an effective enabling technology for dealing with PLA scrap cost-effectively.
As a biopolymer from renewable resources, PLA is one of the rapidly growing plastics in commercial use today particularly in the field of packaging. There is an increasing drive to finding economical approaches to dealing with its end-of-life issues in a manner in line with the principles of a circular economy [1]. In this article, the Zeus depolymerization process for PLA is described comprehensively together with potential applications to commingled plastic waste streams.
Customer Issues
- Tin Catalyst Utilization
- Low-temp/pressure
- Helps Circular Economy
PLA in Today’s Economy
Polylactic acid (PLA) is a plastic obtained from plant starch (usually corn). Of late, PLA has been growing in acceptance as a substitute to petroleum-based plastics such as low-density polyethylene (LDPE), polystyrene (PS), high-density polyethylene (HDPE), nylon (PA), and polyethylene terephthalate (PET). This growth has been driven partly by increased production efficiencies that have reduced costs, by enhancements in polymer properties that have made PLA ideal for a number of packaging applications, and by consumer wish to utilize materials from renewable resources [2].
All things from clamshells for fast food to bioabsorbable medical devices can be made from PLA, considerably decreasing the carbon footprint in these industries. The demand for PLA has increased as society embraces the significance of sustainability and of a circular economy. Global production capacity of PLA is expected to increase by 50% by the year 2022 to over 250,000 metric tons, with the bulk of the production going towards packaging applications [3].
Precedent
Scientists estimate that a PLA bottle could take between 100 to 1,000 years to decompose in a landfill.
Recycling Options for PLA
The predicted growth of PLA in consumer applications across the next five years means an increased presence of the resin in post-consumer waste streams. Table 1 illustrates the alternatives available to recover the added value of PLA after its useful life. There are crucial considerations to take into account before choosing an end-of-life strategy for PLA [4].
Although PLA does biodegrade, it does so extremely slowly in the environment. In a landfill, which is closely packed and designed to exclude oxygen and light, the degradation process is much slower. Experts estimate that a PLA bottle could take nearly 100 to 1,000 years to decompose in a landfill [5].
PLA may ultimately break down into its constituent parts (carbon dioxide and water) within three months in a “controlled composting environment,” that is, an industrial composting facility heated to 140 °F and fed a stable stream of digestive microbes.
Unfortunately, there are just a few hundred industrial-grade composting facilities available across the US.
Incineration recovers the polymer’s fuel value, while traditional (or mechanical) recycling reprocesses the material into an article with properties and value lower than the primary article. PLA serves as a contaminant within a stream of mixed postconsumer waste plastics because of its tendency for thermal degradation during reprocessing compared to other constituents of the recycle stream (such as nylons, polyolefins, and aromatic polyesters). It must thus be removed using expensive techniques before mechanical recycling.
Using chemical recycling, the polymer can be broken down into constituent monomers or oligomers (short chains of monomers) which can subsequently be recovered, reprocessed, and sold. Recovered monomers can be directly repolymerized into the original polymer, thus closing the loop.
The end-of-life recovery options presently available for plastics are summarized in Table 1.
Table 1. End-of-Life Value Recovery Options for Plastics
END-OF-LIFE OPTIONS |
RESOURCES RECOVERED |
VALUE |
Landfilling |
none |
- |
Composting |
biomass |
+ |
Incineration |
thermal energy |
+ |
Traditional Recycling |
polymer for reuse or re-forming |
++ |
Chemical Recycling |
constituent chemicals |
+++ |
Summary
Using recycled PLA frees up farmland to produce corn or other crops for human or livestock consumption.
Chemical Recycling of PLA
Resources in terms of capital equipment and energy are necessary to execute chemical recycling processes. Government incentives will also be available in numerous jurisdictions. For chemical recycling of a polymer to be feasible, resource costs should be comparable to or lower than the costs of manufacturing the oligomers or monomers from raw materials. For each pound of PLA produced, 2.5 pounds of corn are necessary [6]. Thus, the drive for attaining monomer from a waste source is definitely present. An additional benefit of utilizing recycled PLA as a source of monomer is freeing up of farmland to grow other types of crops, including corn, for livestock or for human consumption.
There are many processes available for chemical recycling of PLA by hydrolytic or alcoholytic depolymerization [7, 8, 9, 10]. However, these processes are inclined to be high-temperature, energy-intensive ones. In recent times, processes utilizing temperatures as low as 80 °C have been disclosed [11, 12, 13, 14], thus enhancing the economics of chemical recycling. The Zeus process further improves the economic feasibility of PLA depolymerization processes by using miscible systems of PLA/solvent/reactant to enable monomer recovery at even lower temperatures in a very efficient, environmentally-friendly manner.
The Zeus Waste PLA Depolymerization Process
Figure 1 below illustrates one possible configuration of unit operations in a depolymerization process to handle a stream of commingled plastic post-consumer waste that includes scrap PLA according to the Zeus process.
A schematic representation of a depolymerization process is shown in Figure 1.
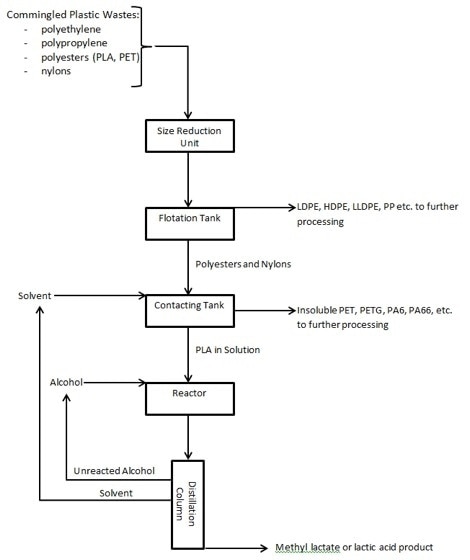
After a preliminary washing step, the commingled plastic stream is subjected to size reduction using standard techniques such as grinders and shredders to make flake-size granules that can be easily separated.
Separation of the different plastics can be done in a range of ways including infrared techniques, electrostatic separation, as well as flotation. This last technique is easily performed to separate polyolefins (with specific gravity below 1) from polyesters and nylons. The vital part of the process is dividing biodegradable plastics like PLA from reprocessable plastics like PET. In a mixed stream of polyesters, this splitting-up can be performed by contacting the stream with a solvent like chloroform to dissolve the PLA component. The undissolved PET can then be dried and sent for additional processing.
The PLA solution is then exposed to alcoholysis (reaction with an alcohol). High molecular weight PLA can be dissolved to around 15% by weight into chloroform. Alcohol is then included in stoichiometric excess to suit depolymerization. As long as the PLA stays dissolved, the scission reactions can take place without being restricted by interphase transport of the reactant to the polymer. Temperature can be raised to just below the boiling point of the mixture’s lowest boiling component to accelerate the reaction without requiring high-pressure equipment. The incorporation of a tin catalyst has been found to significantly increase the reaction kinetics at these mild conditions of temperature.
Since the depolymerization process takes place at low temperatures and atmospheric pressures, a range of reactors can be used. Plug flow reactors or continuous stirred tank reactors are instances of the more common types. Stirred tank reactors can be employed in series to make the process more efficient by increasing the concentration of alcohol in subsequent vessels to favorably drive the reaction to monomer while maintaining solubility of the oligomers.
Separation of the alcohol and solvent from the resultant monomers is also readily achieved. For the chloroform/methanol/methyl lactate system, the variances in boiling points of the components (61 °C for chloroform, 65 °C for methanol and 154 °C for methyl lactate) make distillation an ideal suitable process to eliminate the reactant and solvent from the product. The same is true of the THF/water/lactic acid system (66 °C for THF, 100 °C for water and 122 °C for lactic acid). In each case, the solvent can be recondensed and returned to the contacting tank, while the unreacted methanol or water can be blended with fresh reactant and sent back to the reactor vessel.
Solubility of the PLA in THF or methanol can be significantly improved by heating up the mixture to just below the boiling points of the respective solvents. The respective reactants are then incorporated into the PLA solution at reaction temperature.
In experiments performed at just below 60 °C and atmospheric pressure, molecular weight reduction of the PLA was obvious in each solution within a few hours. Depolymerization extent was deduced by measuring innate viscosity at varied reaction conditions. Size exclusion chromatography was used to establish changes in molecular weight distribution for designated reaction conditions. It was discovered that polydispersity remains fairly unchanged as the reaction continues, signifying that random chain scission is the main mechanism in the single-phase systems [15]. The presence of substantial amounts of methyl lactate monomer was established for the case of the PLA/chloroform/ methanol system using gas chromatography.
The ensuing monomer, either lactic acid or methyl lactate, can be used to synthesize PLA again. There are a number of proven routes to transforming these monomers into PLA, including azeotropic dehydrative polycondensation, polycondensation, or a multistep route that results in high molecular weight PLA [16, 17]. The multistep process polymerizes the monomer into low molecular weight PLA, also known as a pre-polymer, that is then depolymerized to produce lactide.
The methyl lactate is not required to be converted into lactic acid before the pre-polymerization step [18]. The lactide experiences ring-opening polymerization, typically in the presence of a tin catalyst, to produce a high molecular weight PLA resin. Alternately, the pre-polymer can be joined together using chain extending agents to yield a higher molecular weight PLA [16]. The preferred reaction route relies on the PLA characteristics required in the end use application. The reintroduction of monomers back into the PLA life cycle concludes the life cycle.
Table 2 below recapitulates two of the ternary systems that can be applied to depolymerize high molecular weight PLA into either lactic acid or methyl lactate monomers.
Table 2. Examples of Suitable Systems for PLA Depolymerization Process
POLYMER |
SOLVENT |
REACTANT |
CATALYST |
MONOMER |
PLA |
chloroform |
methanol |
tin(II) octanoate |
methyl lactate |
PLA |
THF |
water |
tin(II) octanoate |
lactic acid |
Conclusion
The process is versatile. Both commercial and medical grade PLA resins can be depolymerized.
Benefits of the Zeus Depolymerization Process
Key Benefits
- Cost-effective
- Easy to implement
- Supports sustainability
The low-temperature solution depolymerization process for PLA defined in this article has many advantages that would make it ideal for adding to industrial recycling operations.
The process is easy to execute and economical to operate. No high-pressure vessels are needed, therefore capital costs are low. High temperatures are not required in the reactor, so operating expenses are low. The contacting tanks and reactors can be simply added to a current post-consumer processing facility. A catalyst has been identified that significantly improves the depolymerization reactions at mild conditions, and that can be reused for ensuing polymerization reactions.
The process is versatile. Both medical and commercial grade resins can be depolymerized. Stringent control of PDI is possible during the reaction, so important intermediate products such as oligomers can be achieved. These could be beneficial as green solvents and coatings, or for pharmaceutical applications. Alternatively, various monomers can be acquired by stimulating the depolymerization reaction with either excess methanol or water to give methyl lactate or lactic acid, respectively. The process is insensitive to other polymers present in the mixed waste stream, but effectively removes a difficult component of that waste stream.
Sustainability initiatives are supported by the process. Using waste PLA to produce lactic acid, which is presently a corn-derived product, frees up this valuable crop for other markets such as livestock feed, foodstuffs, and ethanol production. The process can also be used to produce lactide for high purity, high molecular weight medical-grade polymers.
The process sticks to the spirit of a circular economy. The innate value of the waste biopolymer is generally recovered. Excess solvent and reactant can both be readily recovered to be reused in a closed loop process.
References
- https://www.ellenmacarthurfoundation.org/circular-economy, 2017
- M. Dusselier, P. Van Wouwe, A. Dewaele, P. A. Jacobs, B. F. Sels, “Shape-Selective Zeolite Catalysis for Bioplastics Production”, Science, 349, issue 6243 (2015), 78-80.
- Report Bioplastics Market Data 2017, http://docs.european-bioplastics.org/publications/ market_data/2017/, 2017.
- L. West, “Pros and Cons of PLA: Corn-Based Plastic”, ThoughtCo, Oct. 30, 2017, https://www.treehugger.com/pros-cons-corn-based-plastic-pla-1203953.
- J.A. Micales and K.E. Skog, “The Decomposition of Forest Products in Landfills”, Intern. Biodeterioration and Biodegradation, 39 (1997), 145-158.
- C. Kingsland, PLA: A Critical Analysis, Mohawk College, 2010.
- K.K. Bhatia, US5136057, 1992.
- H.E. Bellis, US5278256, 1994.
- K. Nakamura,US7985778, 2011.
- V. Thammonkol, N. Kaabbuathong, J. Junkasem, T. Thanpitcha, P. Lorjai, C. Katepetch, WO2015112098A1, 2015.
- P. Coszach, J.C. Bogaert, J. Willocq, US8481675, 2013.
- P. Coszach, J.C. Bogaert, J. Willocq, US8431683, 2013.
- P. Coszach, J. Willocq, US8614338, 2013
- G. Srinivisan, D. Grewell, US8895778, 2014.
- B. Anneaux, J. Campanelli, E. Foley, “Low Temperature Solution Depolymerization of PLA”, to be presented at ANTEC 2018, Orlando, May 2-5, 2018.
- D. Garlotta, “A Literature Review of Poly(Lactic Acid)”, Journal of Polymers and the Environment, 9 (2001), 63-84.
- S. Inkinen, M. Hakkarainen, A. Albertsson, and A. Södergård, “From Lactic Acid to Poly(lactic acid) (PLA): Characterization and Analysis of PLA and Its Precursors”, Biomacromolecules, 12 (2011), 523-532.
- P. Upare, Y. Hwang, J. Chang, D. Hwang, “Synthesis of Lactide from Alkyl Lactate via Prepolymer Route”, Ind. Eng. Chem. Res., 51 (2012), 4837-4842.

This information has been sourced, reviewed and adapted from materials provided by Zeus Industrial Products, Inc.
For more information on this source, please visit Zeus Industrial Products, Inc.