Drawn fiber is an enhanced monofilament fiber obtained from polymer extrusion. The term drawn fiber originates from industry and is used to define monofilament that has been stretched, pulled, or drawn down after extrusion. Draw down itself indicates the characteristic that the fiber has been made thinner due to the drawing process; in this fashion, the fiber has been drawn down in size (diameter). The additional step of draw-down makes drawn fiber different from ordinary monofilament. As a consequence of the drawing process, drawn fiber generally possesses better mechanical properties than ordinary extruded monofilament, thus greatly expanding the scope of drawn fiber applications.
The Drawing Process and Applications
How is Drawn Fiber Made?
Extrusion
Monofilament, including drawn fiber, is extruded from molten polymer resin materials. These resins include very-long-chain polymer molecules. In the melt phase, these molecules are arranged in a disordered and random manner (Figure 1 Left). Extrusion triggers orientation of the polymer chains from a disordered to a more ordered arrangement (Figure 1 Right).
This orientation takes place in the direction of extrusion.1-3 A material with a much higher degree of polymer chain alignment is the result of extrusion. This more aligned positioning has a considerable effect on the mechanical properties of the monofilament. 3, 4
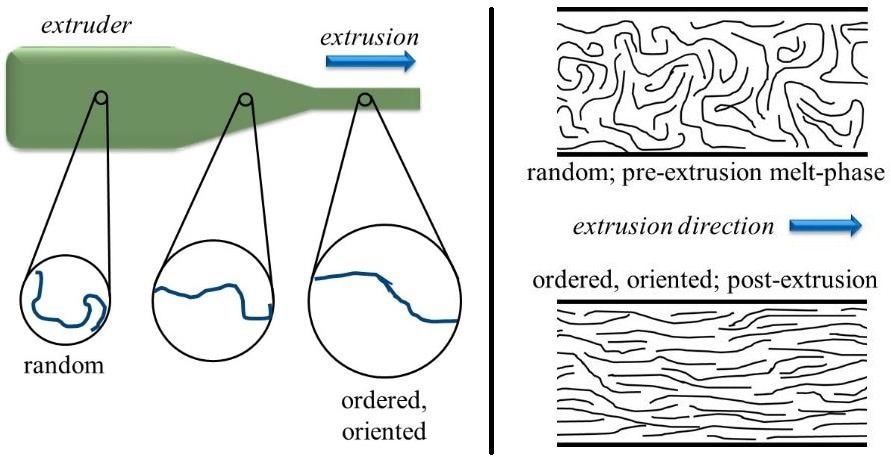
Figure 1. Schematic representation of the extrusion process. Left In the melt phase prior to extrusion, polymer chains are randomly oriented. As the melt-state material is forced through the extruder, the polymer chains become more oriented in the extrusion direction. Right Illustration showing the change in polymer chain orientation during the extrusion process. Pre-extrusion, the polymer chains are loosely packed; post-extrusion, the chains are more closely packed and oriented in the extrusion direction.
The Drawing Process
The process of drawing down the monofilament takes the extrusion process one step further. This stretching and pulling of the fiber even causes the polymer chains to be stretched at the molecular level. 2 This draw-down process is carefully controlled and performed at higher temperature to increase chain molecule alignment and facilitate polymer chain mobility. Draw-down is achieved by passing the extruded monofilament through heat such as a hot water bath or oven. At the time of stretching, the monofilament fibers are wound onto Godet rolls, which are also known as stands or draw stands (Figure 2).
Using this series of multiple off-aligned rolls, stretching is controlled by turning at various speeds. Moreover, Godet rolls themselves are generally heated to promote the drawing process. Godet rolls can be employed in a wide variety of combinations, set-ups, and other arrangements to precisely control phases of the drawing process. In addition, Godet rolls offer a way to control slippage of the monofilaments. The draw-down process additionally aligns the polymer chains in the machine direction enabling more close packing and increased density leading to a smaller diameter of the drawn monofilament fiber. 3-5
Fiber that has been drawn down in this way also has less elongation when compared to the same fiber that has been extruded only. This expected result is because the fiber is stretched or elongated in the drawing process before it cools to room or normal temperature. In the drawing process, maximum fiber strength is achieved only when the polymer chains have reached maximum alignment in the same (machine) direction (Figure 3). 5
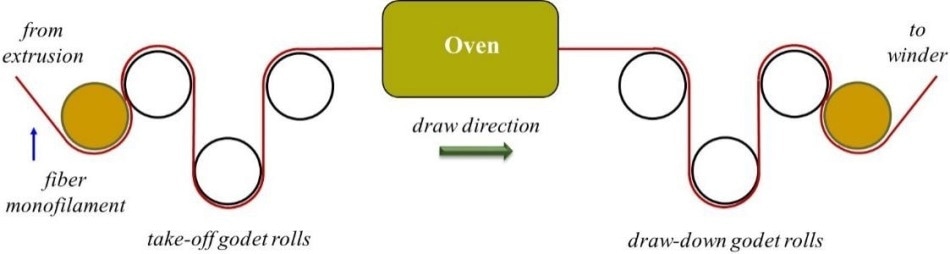
Figure 2. Schematic representation of the components in a monofilament draw-down line. Friction or pinch rollers are shown in gold. Godet rolls are temperature controlled and can be heated or cooled to give more precise control of the fiber draw-down process. A heat source such as an oven is commonly used between take-off and draw-down rolls. Multiple roll combinations, set-ups, and other arrangements beyond the simplified representation shown here can be used to regulate various aspects of the drawing process.
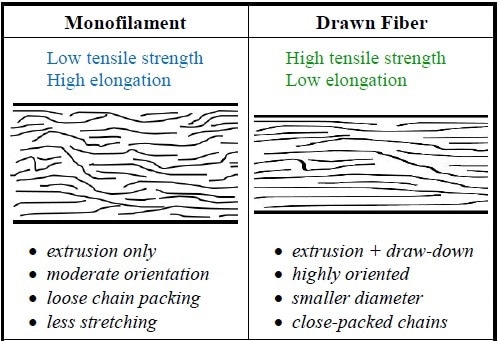
Figure 3. Comparison of extrusion-only monofilament and drawn fiber monofilament. Ordinary monofilament (left) typically possesses lower tensile strength and higher elongation than drawn fiber (right).
Applications
Drawn fiber, and particularly Zeus drawn fiber, can be best described as a performance fiber. This product is specifically targeted at more difficult or rigorous application environments. This type of drawn fiber is distinctive from more commoditized and inexpensive monofilaments as those widely found in the textile industry, as an example. In fact, Zeus drawn fiber can be found in an array of applications from automotive, aerospace, automotive, to medical industries and also in an amazing range of other fields.
Both the polymers and processes used for making drawn fiber can be directed to provide many favorable mechanical, physical, and chemical attributes to the monofilament. These traits make drawn fiber particularly versatile for unfriendly or high-stress environments. When these advances are coupled with the ability to be produced or woven in extremely fine diameters, there are extensive possibilities for drawn fiber. Some specific examples are mentioned here as an appreciation of the varied capabilities and application prospects of Zeus drawn fiber.
Braiding –A woven over-braiding for sleeves or hoses to wrap wire bundles (Figure 4A) is perhaps the most common application of drawn fiber. When braiding is used in this way, it provides protection from rubbing, abrasion, and also from physical trauma. In addition, drawn fiber over-braiding offers extra strength and increased burst pressure for fluid carrying hoses.
Weaves – Drawn fiber can be made into weaves that can be used for fine filtration and for applications like mist eliminators. It can also be used as scrims for backing of non-woven filter material. In addition, drawn fiber can even be woven to produce support structures for composite materials that are widely used in automotive and aerospace industries. A main consideration here is the chemical resistance of the particular drawn fiber polymer (Figure 4B).
Medical braiding – Medical braiding is another common application of drawn fiber monofilaments. This type of application is most often as reinforcing braiding for catheters. A more recent variation on this application also features drawn fiber braiding on gastroluminal bypass tubes for strengthening reinforcement. 6 Medical catheters and tubes using drawn fiber braiding are compatible with MRI, provided they do not contain other substantial metal parts – a highly favored feature in present medical sector (Figure 4C).
Instrument strings – Additionally, drawn fiber can also be used as strings for instruments, such as for a harp or guitar. Although it is common to use nylon strings for a classical style guitar, drawn fiber can be produced from a range of polymer materials such as PVDF, opening up the range of string applications (Figure 4D).
Racquet strings – Just like instrument strings, drawn fiber can also be used for racquet strings. Here, it holds a broad range of possibilities considering the number of racquet sports including badminton, squash, tennis, and many others (Figure 4E).
Belting – Drawn fiber can also be used for making unusual or new components. One such creation is a seam spiral used to join the ends of industrial conveyor-type belts. This type of belting can be found at grocery store checkouts. Furthermore, drawn fiber can be woven into ribbons and used as a strengthening layer in belt manufacturing (Figure 4F).
Brushes – Whether for scrub brushes or push-brooms, drawn fiber readily lends itself for this kind of application. Drawn fiber bristles are even used for making tooth brushes. The durability, resistance to abrasion, and chemical resistance of the drawn fiber make it suitable for these kinds of application (Figure 4G).
Chopped – In structural composites, drawn fiber is extremely adaptable for use when it is chopped or cut into minute pieces and included to the composite. For instance, the chopped fiber can be sprayed onto a surface to provide a random orientation and coated with a next layer of paint, resin, or other top coating. In this manner, the desired property resulting from the chopped fiber application would have less directionality and more uniformity. When compared to a thin film, this kind of application is relatively better, for instance, and is particularly useful in composite forming for enhanced structural integrity or weight savings.
Formed parts – The thermoformability of drawn fiber enables it to be used for making formed parts (Figure 4H). For example, drawn fiber can be wound or heat-formed to create a spring shape or changed to other shapes from its initial monofilament form.
Twisted cord or twine – When tying or lacing is needed, this application of drawn fiber is often employed. Compared to ordinary monofilament, the improved tensile strength of drawn fiber is particularly beneficial for drawn fiber twine and cord (Figure 4I).
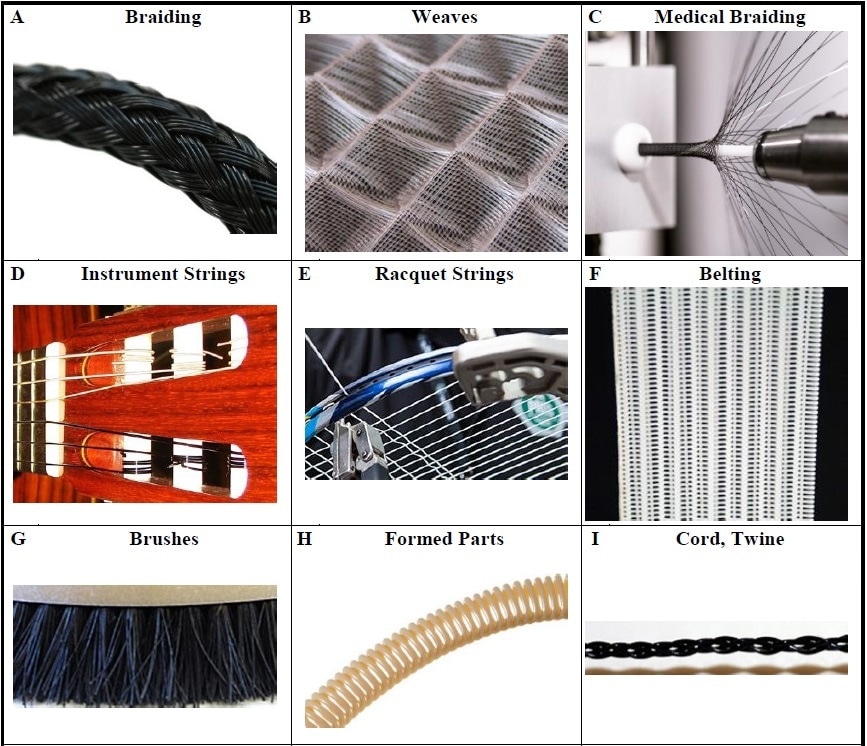
Figure 4. Overview of several drawn fiber applications and products. A) Black PEEK braided sleeve. B) Enlargement of ETFE weave used as a mist eliminator. C) PEEK drawn fiber being braided over a catheter. D) Instrument strings and E) racquet strings are also obvious applications of drawn fiber. F) PEEK drawn fiber used as a mesh in belting applications. G) Brushes can be made from multiple fiber polymers which have exceptional abrasion resistance. H) Formed parts such a seam spiral can be made from Zeus drawn fiber. I) Drawn fiber makes high-tensile twine for applications requiring tying or lacing.
References
- Carraher CE: Introduction to Polymer Chemistry, Third Edition: CRC Press; 2012.
- Mackley MR: Polymer processing: the physics of stretching chains. Physics in Technology 1978, 9(1):13.
- Giles HF, Wagner JR, Mount EM: Extrusion: The Definitive Processing Guide and Handbook: Elsevier Science; 2013.
- Ward IM, Sweeney J: An Introduction to the Mechanical Properties of Solid Polymers: Wiley; 2004.
- Levy S, Carley JF: Plastics Extrusion Technology Handbook: Industrial Press; 1989.
- Sandler BJ, Rumbaut R, Swain CP, Torres G, Morales L, Gonzales L, Schultz S, Talamini MA, Jacobsen GR, Horgan S: One-year human experience with a novel endoluminal, endoscopic gastric bypass sleeve for morbid obesity. Surgical Endoscopy 2015, 29(11):3298-3303.

This information has been sourced, reviewed and adapted from materials provided by Zeus Industrial Products, Inc.
For more information on this source, please visit Zeus Industrial Products, Inc.