Interview conducted by Mychealla RiceJun 29 2018
Offering reliable performance coupled with low installation costs, the Wedge Meter II flow element is the next step for downstream chemical, oil and gas applications.
In this interview, Paul Wilson, lead sales of DP Flow Primary Products, and Oscar Artica, Product Manager for the Variable Area, Differential Pressure and Vortex/Swirl flowmeter lines, both from ABB, talk to AZoM about the benefits of the WedgeMeter II and how it is designed to meet almost any process condition.
Please tell us about the WedgeMeter II?
The flow element consists of a body and wedge flow restriction. This restriction creates a differential pressure in proportion to the square of the volumetric flow rate. The wedge restriction has no critical surface dimensions or sharp edgesthat will affect measurement accuracy as the result of normally expected wear. Other primary element designs such as orifice plates suffer accuracy degradation once their sharp edges wear.
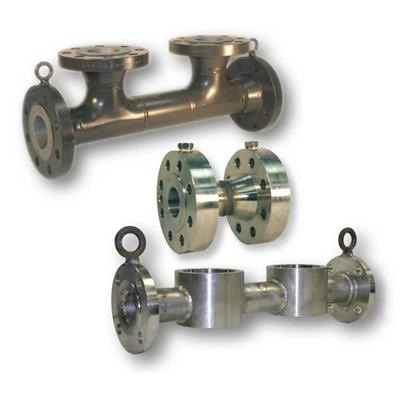
Why did you decide to develop the WedgeMeter II? Was there a gap in the market?
ABB originally designed the wedge meter in the 50s and held the first patent for it. Since then it has evolved in its design to ensure that it is a commercially attractive product. Relying on the proven technology of differential pressure flow metering, the WedgeMeter II flow elements take the next steps in offering reliable performance coupled with a low installation cost when compared to other technologies.
Having no moving parts and a unique wear resistant ‘V’ shaped restriction, initial accuracy is maintained throughout the life of the meter, virtually eliminating routine maintenance schedules. Whether the measured process is dirty, viscous, hot, clean, abrasive or tends to foul, wedge
Tell us about the benefits and features of the WedgeMeter II?
It measures virtually any process and is often the only flow metering technology capable of handling very aggressive conditions.
Some of the key features and benefits of the WedgeMeter II include:
- High accuracy +/- 0.5% of rate with a 0.2% repeatability.
- Can be used in bi-directional flow applications
- Low Reynolds number measurement (as low as Rd 500) for higher flow rangeability.
- Minimal upstream and downstream piping requirements
- Engineered specifically every time for every customer
How is the WedgeMeter II designed to meet almost any process condition?
The wedge meter is an extremely robust flow meter designed to work in gas, liquid, and steam applications. Every wedge is engineered specifically for the application the customer intends to use if for. For example, the material of construction can be carbon steel all the way through to exotic materials like Inconel or even tantalum!
The taps which connect to the differential pressure transmitter also vary in design to alleviate concerns with entrained solids blocking the connection to the transmitter. These devices are also designed to work in some of the most demanding applications such as coker units where the process is high temperature, high pressure, and very unpleasant for other metering devices.
Steam jackets can be provided to keep the wedges warm in some applications which ensures the product passing through does not solidify and block the process. In addition, the WedgeMeter II can be used for bidirectional flow.
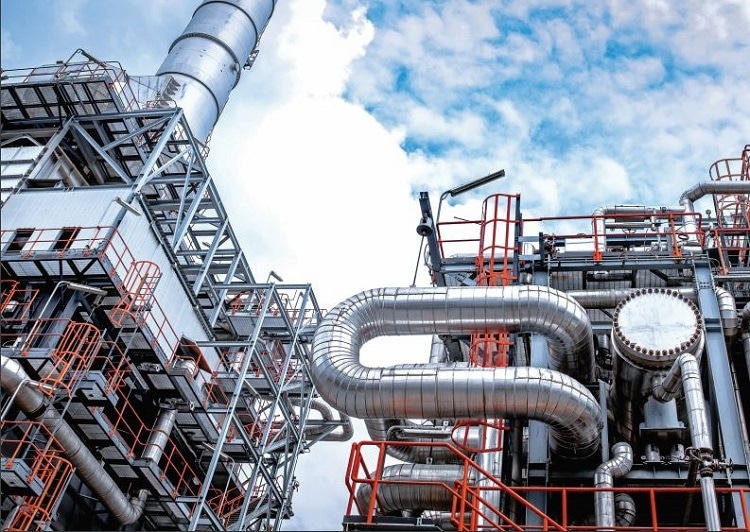
Why is the WedgeMeter II the ideal metering solution for challenging process applications? Tell us about the obstacles it can help overcome?
The meter is designed to handle high temperature, high-pressure applications, as well as those considered more standard. It overcomes concerns with measurement of viscous fluids and operates down to low Reynolds numbers. Certain designs eliminate the plugging of impulse lines that other meters may experience.
Tell us about the benefits downstream chemical, oil and gas applications will see using the WedgeMeter II?
The WedgeMeter II is designed for the most challenging of applications.
The below table outlines how the WedgeMeter II can benefit downstream chemical, oil and gas applications.
Clean fluids |
Whether liquid or gas, mass flow rates can be attained using the multi-variable technology offered with today’s differential pressure transmitters |
Erosive, abrasive slurries
|
Withstands erosive conditions that would normally wear sensitive measurement surfaces found in orifice plate, turbine metering or positive displacement meters |
Low conductivity fluids
|
Fluids such as hydrocarbons that cannot be measured using magnetic flow metering devices |
Viscous and NonNewtonian fluids
|
Positive performance in flow regimes not attainable by other head loss meter types, oscillatory and mechanical meters. |
Fluids that will gum or foul
|
Takes advantage of a unique flow restrictor to reduce fouling that occurs in meters employing vanes, moving parts or small diameter tubing |
Fluids at extreme limits
|
Easily adaptable to a wide range of fluid temperatures from cryogenic to 427 °C (800 °F)
|
Molten sulfer is a by-product of crude oil refining and natural gas processing and is used in many applications. Tell us why the WedgeMeter II is the best product for this application?
Molten sulfur is a by-product of crude oil refining and natural gas processing and is employed in the production of insecticides, synthetic fibers, plastics fertilizers, solvents, pigments, resins and various other products. Depending on the process temperature, viscosities can range from 6-100 cSt. and maintaining a steady flow is challenging as the fluid can plug lines and cause production outages.
The solution to this metering problem is ABB wedge flow elements, coupled to a suitable secondary transmitter with high temperature remote seal technology. The unique profile of the wedge restriction allows linear and accurate flow measurement at Reynolds numbers (Rd) down to 500.
Most other differential devices are limited to Rd of 20000 and above. Integration of the remote seals into the wedge element eliminates problems of plugging associated with conventional impulse lines and allows the application of higher process temperatures to keep the fluid from solidifying.
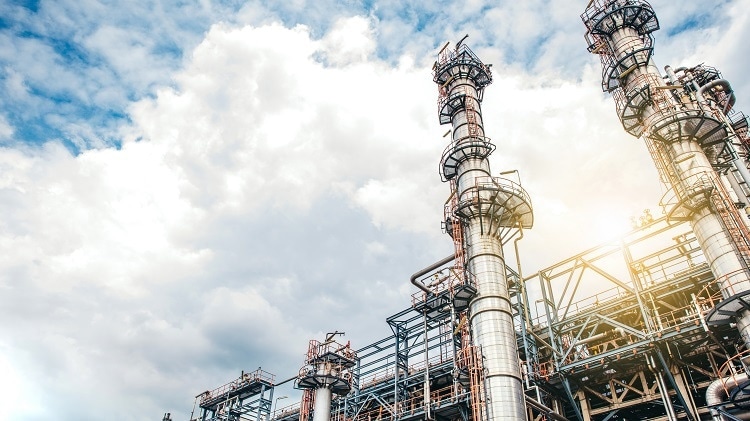
Image Credit: shutterstock.com/Vacancylizm
Can you tell us other applications that the WedgeMeter can be used in?
Applications such as Molten Sulphur, enhanced oil recovery, delayed coker applications, downstream oil and gas applications and municipal applications will all benefit from the WedgeMeter III.
How is the WedgeMeter II used in enhancing oil recovery?
The WedgeMaster design offers reduced installation and maintenance costs and improved meter performance and life cycle. WedgeMaster products also offer a wider flow range capability over conventional DP products, and can therefore streamline the measurement process into one flow stream as in the diagram below.
Using the advantages of today’s multi-variable transmitter technology, pressure and temperature points are combined and the secondary pressure electronics offer greater resolution compared to using discrete components. Additionally, wedge flow meters require far less up- and down-stream piping than orifice and turbine technology.
Coupled with the fact that only one flow meter is now required, purchase and installation costs fall by as much as 40 to 50 % of the original two-stream measurement system. Looking towards increased performance, wedge meters have no moving parts or sharp measurement edges that are prone to wear, eliminating the periodic replacement of orifice plate or turbine internals.
To further meet the rigorous demands of this application, WedgeMaster solutions are available in almost any configuration with regard to wetted materials, flange rating and process connections while continuing to meet traditional and accepted measurement principles.
What does the WedgeMeter II mean for the future of downstream chemical, oil and gas applications?
The wedge meter provides an extremely robust meter combined with longevity of service, reducing the need for maintenance when compared to other devices.
Low cost of intial ownership
|
Easily sized using advanced software tools, simplified order code; reduces engineering efforts |
Low installed cost
|
May be installed with a minimum of five diameters upstream and three diameters downstream, significantly reducing pipeline material requirements |
Improvement in operating costs
|
Energy efficient design supports increased productivity – as much as 40 % over conventional head loss meters |
Maintenance free
|
Lack of moving parts or wear sensitive edges eliminates downtime and need for routine inspections |
The WedgeMeter II provides many industry benefits;
- Durability, stability and simplified maintenance are huge benefits to an industry.
The wedge flow element has no moving parts (unlike a turbine meter) or critical surface dimensions or sharp edges that must remain within strict tolerances for maximum accuracy (like an orifice plate). The wedge restriction inside the element has been designed to last the life of the installation, without replacement and without recalibration. For most applications, a wedge flow element can be installed directly in the process piping, without blocking valves and without any by-passes, since it almost never requires removal.
- Lowers the cost of ownership
An important factor in the deciding which flowmeter to use for any application is the cost of ownership. Cost of ownership includes the initial cost to purchase the meter (and any ancillary equipment), the cost to install the meter, the maintenance cost and the operating cost. Initial cost and installation cost are one-time upfront expenses. Maintenance and operating costs are incurred every year for the life of the meter. Under the proper process conditions, the wedge flow element is an “install and forget” type of meter that minimizes the end users cost of ownership.
Availability of elements in different materials of construction (carbon steel, stainless steel, Hastelloy and Monel) allow the lowest cost product to be bid given the rigors of the application.
When factory assembled with an ABB transmitter, the installed cost to the user is reduced by eliminating the need to integrate all the individual components associated with a head device on site. In the case of the pipe tap wedge element (WMP), the block manifold and a multi-variable transmitter can be integrated at the Warminster factory and shipped as a complete flow system, eliminating separate devices for static, differential pressure.
- High accuracy and wide rangeability
When ordered as an option, the wedge flow element is calibrated on water at the Warminster factory to an accuracy of +/- 0.5% or better, and supplied with a report containing the calibration test data. When coupled with the proper secondary device, system accuracy can be ± 1% of rate or better for a flow range of 3.5:1 (differential pressure range of 12:1), or ± 2% of rate or better for a flow range of 5:1 (differential pressure range of 25:1). The same accuracy is available for flow in the positive or reverse directions. This accuracy is based upon installation with the recommended runs of straight pipe upstream and downstream of the meter.
- Insensitivity to flow profile distortion and /or swirl
Wedge elements are highly insensitive to piping effects and generally require only 5D to 10D of straight pipe upstream, and 3D to 5D downstream. This insensitivity was demonstrated in the 1980s in a test conducted on a 4 in. pipe tap wedge element by Du Pont Engineering. Copies of the Du Pont test report are available from ABB (contact Paul Wilson) The wedge element was evaluated for calibration accuracy, repeatability and operation under a variety of upstream / downstream piping configurations including:
- Two elbows in the same plane 5D, 11D and 19D upstream
- A single elbow 5D upstream
- Three elbows close coupled 5D upstream
- A 6 by 4 in. concentric reducer 5D upstream
- A half open gate valve 6D and 13D upstream
- A tee 5D upstream
The conclusions from the test report were:
- Results were all well within the 0.5% specification
- Repeatability was 0.19 % of rate
Most conditions tested the effects of the value of the discharge coefficient was 0.5 % or less (this corresponds to the error margin quoted for orifice plates installed with piping recommendations made in ASME “Fluid Meters”)
- Ability to solve the toughest application using special design configurations
Some flow meters can be limited to certain materials of construction, pipe id’s, pressure ratings etc. due to manufacturing processes and costs. Meters employing castings or fixed dimension components cannot provide cost-effective solutions based on special designs. With the wedge flow element, virtually any material, pipe schedule (40>) and flange ratings to class 1500 or higher can be designed to meet specific applications. Redundant pressure taps for safety purposes and internal corrosion/erosion resistant coatings are available for the most demanding situation. Pressure taps can be configured to meet almost any mating seal or impulse piping requirement.
Where can our readers go to find out more?
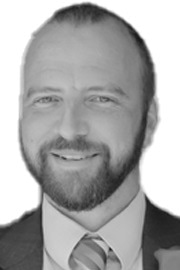
To find out more about the WedgeMeter II please visit https://new.abb.com/products/measurement-products/flow/differential-pressure-flowmeters/wedge-elements
About Paul Wilson
Originally from the UK, Paul started his career with ABB 20 years ago in the ABB UK factory where he worked as a service engineer for ABB Ireland. He later returned to the UK to work outside sales for ABB covering the major engineering firms.
Paul is now based along the Gulf Coast USA and leads sales of DP Flow Primary products within the USA and Canada.
About Oscar Artica
Initially hired as a Proposal Engineer, Oscar was posed with a career path in Product Management since 2012. He has a Master of Science degree in Mechanical Engineering with a focus in Thermo-Fluid Dynamics and Discrete
Control Theory.
Oscar has since devoted his time to tailoring solutions that are aimed towards increasing channel and customer product knowledge to consequently build trust and comfort with the excellence of ABB Flow Products.
Oscar is responsible for the development and financial stability of the Variable Area, Differential Pressure and Vortex/Swirl flowmeter lines.
Disclaimer: The views expressed here are those of the interviewee and do not necessarily represent the views of AZoM.com Limited (T/A) AZoNetwork, the owner and operator of this website. This disclaimer forms part of the Terms and Conditions of use of this website.