With the increasing shortage of natural resources, innovative technologies that provide for the sustainable use of raw materials are increasingly sought after. Mineralogist Dr. Robert Moeckel is currently researching mineral and metallic raw materials at the Helmholtz-Institute for Technology of Resources in Freiburg, Germany that is part of the Helmholtz-Center Dresden- Rossendorf.
Dr. Moeckel's research is focused on the pulverization and homogenization of mineral samples prior to X-Ray Diffraction (XRD) analysis, which is an analytical technique that utilizes X-rays that are diffracted at the atomic structures in specific angles (Bragg's Law) to provide information on the atomic spaces in the crystals.
XRD allows the user to accurately determine the order of different atoms towards each other. Hence, XRD is a useful technique for determining the differences that exist, for example, between coal and diamond, two pure carbon samples, based on their different crystal lattices.
Samples are pulverized to homogeneous powder prior to XRD analysis. The individual crystalline phases are then identified with the help of a data base. The data is quantified, for example by Rietveld-Analysis, which specifically matches theoretical diffraction diagrams to the measured data.
XRD has become an increasingly useful tool over the last several years, and is utilized in various areas of research and development, as well as in quality control procedures in many different industries, including construction materials, minerals, cement or mining.
Sample Homogenization in the XRD-Mill McCrone
RETSCH's XRD-Mill McCrone is designed for sample homogenization prior to XRD analysis. The main applications include both research and development, as well as quality control processes related to mineralogy, cement industry, chemistry, geology or material sciences. The unique grinding principle of the XRD-Mill McCrone is based on cylindric grinding elements and gentle homogenization of the sample with friction, thus ensuring that the crystal structure is preserved to obtain reliable X-ray diffractograms.
The McCrone Micronizing Mill, which is the previous version of the XRD-Mill McCrone, has been cited in numerous publications [e. g. 1-4]. The 125-ml polypropylene grinding jar is filled with 48 identical grinding elements of agate, zirconium oxide or corundum. After grinding volumes that range from 2 to 4 ml for 3 to 30 minutes, the sample is perfectly homogeneous. Dr. Moeckel has recently tested different types of mills for sample preparation to XRD analysis, using a mixture of fluorite, barite and quartz in a known ratio for the tests. The best results were achieved with the XRD-Mill McCrone (Table 1).
Testing Sample Mixtures for Comparison of Mills
The XRD-Mill McCrone is characterized by agentle grinding mechanism with a low energy input that is based on friction. The Planetary Ball Mill PM 100 or the Mixer Mill MM 400 (both RETSCH mills) work with friction and impact and thereby generate a
significantly higher energy input compared to the XRD-Mill McCrone.
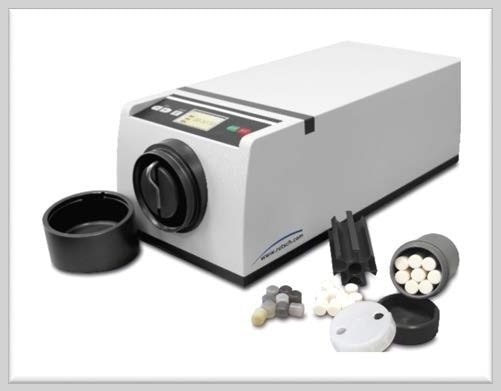
Figure 1. XRD-Mill McCrone from RETSCH
The particle size distribution of samples ground in the XRD-Mill McCrone is extremely narrow, while the crystal lattice structure of the sample remains intact as required for XRD Analysis. A mixture of minerals with 50% fluorite, 43% barite and 7% quartz (w/w) with particle sizes that are suitable for the XRD-Mill McCrone (barite and quartz: 100 - 200 μm, fluorite < 400 μm) was ground to a fineness < 10 μm with the XRD-Mill McCrone, the Planetary Ball Mill PM 100 and the Mixer Mill MM 400.
The samples were then analyzed (Rietveld analysis) with the X-ray diffractometer PANalytical Empyrean (Co-Kα-rays; Detector: PIXcel3D-Medipix3 1x1, 35 kV/35mA, angle 5-80°2θ, increment 0.0131°2θ, total time of measurement 2.5 h).
Due to the high contrast difference for the applied X-rays between barite with high absorption and quartz or fluorite with low absorption, the particle size and particle size distribution have a great influence on the XRD results. Consequently, ingredients that exhibit higher absorption rates are underrated if the particle size is too big.
Moreover, some sample materials may react with partial glass formation on the particle surface if too much energy is applied during the grinding procedure. Those parts are not detected by XRD and are therefore underrated, such as quartz in the study discussed here.
As shown in Figure 2, the height and the width of the peaks of the samples exhibit an increased variance as a result of the described physical effects. While the particle sizes are too large for analysis by XRD, glass formation has started to show on the surfaces (Table 1). The analysis results of the samples ground in different mills under different conditions also show variations in these results.
Conclusion
The gentle homogenization of samples analyzed by XRD is an important prerequisite to ensure accurate results. RETSCH’s XRD-Mill McCrone has been used for decades for the preparation of samples prior to XRD analysis. The unique grinding principle helps to preserve the crystal lattice of the sample much better than other mills, for example ball mills.
Table 1. Results of grinding tests with a sample 50% fluorite, 43% barite and 7% quartz (w/w)
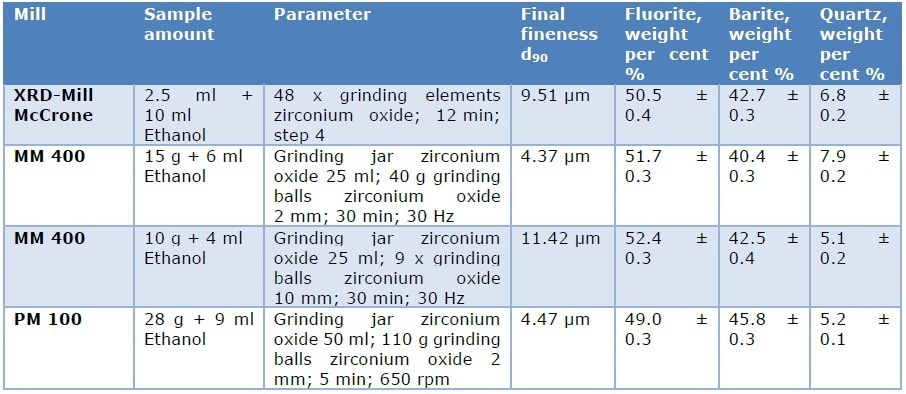
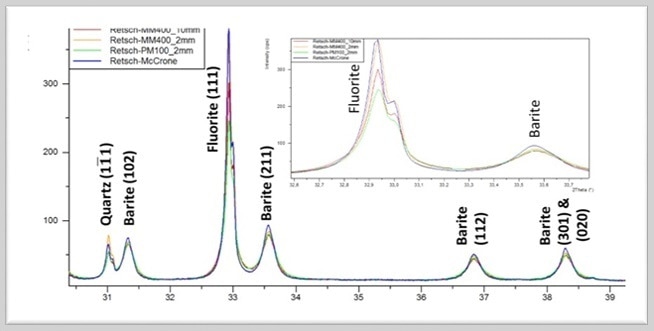
Figure 2. Partial result of the diffraction analysis of the test mixture. The height and the width of the peaks differ clearly, depending on the previous sample preparation. Also, the integral intensities, which are used for quantification, vary.
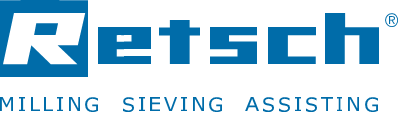
This information has been sourced, reviewed and adapted from materials provided by RETSCH GmbH.
For more information on this source, please visit RETSCH GmbH.