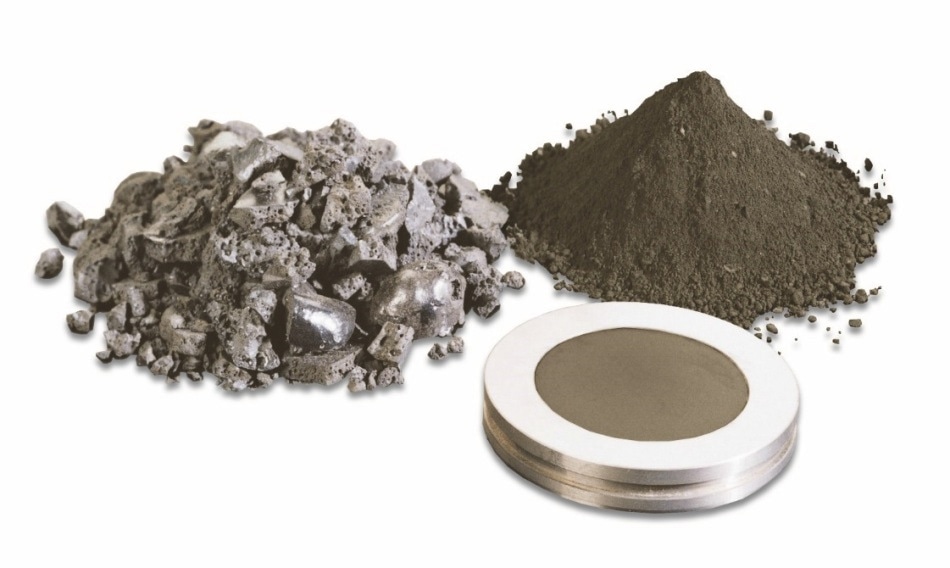
To produce high-quality cement, the mineralogical and chemical composition of raw materials, as well as of intermediate and finished products, needs to be determined. At each stage of the production process, samples have to be taken, prepared and analysed to guarantee quality control without any gaps. RETSCH offers a wide range of instruments for sample preparation during the complete production process.
Typically, a sample preparation process will involve preliminary size reduction, sample division, fine size reduction and, depending on the subsequent analysis, pellet pressing. This article focuses on the fine grinding step in which the RETSCH’s Vibratory Disc Mills are used for the production of fully homogeneous samples as a prerequisite for reliable results, and on how to produce smooth pellets for XRF analysis.
Sample preparation has become an increasingly important issue since the detection limit of XRF analyzers has shifted to trace level over the last few years. Moreover, accurate analysis of major light elements is only possible when finely ground and homogeneous samples are used.
Sources of Error
The overall procedure of X-ray fluorescence analysis may be divided into three different stages that include sampling, sample preparation and spectrometric analysis. Of these stages, mechanical sample preparation typically requires the most time to complete.
For XRF analysis, the laboratory sample consisting of a few grams will typically represent a total amount of several tons. To produce a homogeneous and representative pulverized sample from a bulk material, a fair amount of work is required through sample crushing and dividing, during which most accidental errors, and errors attributable to the system’s inadequacies, will occur.
Since XRF measurements are not difficult to perform, reliable sample preparation remains the most important aspect of this process, as it can lead to insufficient reproducibility and ultimately inaccurate analysis results. Aside from the quality of the spectrometer playing a major role in achieving accurate results, the quality of the sample preparation process also has great influence on the overall precision and reproducibility of the results of the XRF analysis.
Required Fineness and Homogeneity
As X-rays enter deeper into the sample, a greater amount of this radiation will be absorbed so that, above a defined thickness level, the X-ray light will no longer be able to penetrate the sample. This principle also applies to fluorescent light that leaves the sample to be detected.
The lowest sample layer from which detectable fluorescent X-rays are emitted is called saturation depth. Saturation depth is determined by the intensity of the X-rays, the type of detected atoms and the density of the sample’s surroundings, which are otherwise referred to as the matrix. If different elements are being analyzed within the same matrix, the saturation depth will increase as the atomic number of the element increases.
Similarly, elements of smaller atomic numbers are more difficult to detect, which also contributes to the difficulty in obtaining reproducible analysis results. For this reason, a fineness of at least 80 microns is required, e. g. for a mineral like dolomite, to ensure that reliable results are achieved when elements that are lighter than potassium are analyzed.
A second factor that affects the quality of analysis results involves the degree of homogenization, particularly when dealing with coated or inhomogeneous samples. Only if the sample is thoroughly homogenized, can it be ensured that also the inner core of the sample has been measured.
If different elements are analyzed in the same surroundings, then the saturation depth will increase as the atomic number of the element increases. Table 1 further describes this correlation for a selection of elements that are contained in cement clinker:
Table 1. X-ray saturation depth of different elements in a cement clinker sample.
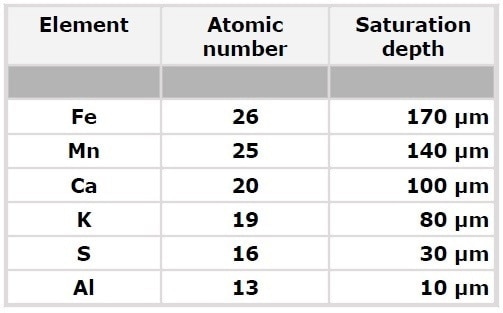
Sample materials typically come in large amounts and feed sizes which makes preliminary size reduction necessary, for example with jaw crushers. These are powerful instruments that crush the material through pressure and friction between a mobile and a fixed breaking jaw,.
Following the preliminary size reduction procedure, a representative part of the sample that exhibits identical properties as the entire sample is subjected to fine grinding. The selection of the sample division method and instrument will depend on the material and amount being analyzed.
For example, dry and pourable bulk samples can be fed to rotating dividers through vibratory feeders, whereas sample splitters are more suitable for heavily flowing materials. RETSCH offers a line of sample dividers that ranges from sample splitters in six sizes to rotating dividers extracting part samples from a bulk of 5 to 60 liters. Once a part sample is extracted, it is then subjected to pulverization.
Sample Pulverization with Vibratory Disc Mills
Vibratory Disc Mills, such as RETSCH’s RS 200 or RS 300 XL, are often the instruments of choice for the processing of hard and brittle samples, such as lime stone or clinker, prior to XRF analysis. As a result of centrifugal forces, the grinding ring and disc act with high impact and friction on the sample, enabling both mills to produce a final fineness down to 20 μm, depending on the specific sample material.
With this size reduction principle, the required analytical fineness is typically obtained within several seconds, which is particularly advantageous for quality control processes where the analysis results are needed quickly, e. g. for product approval processes.
The test grinding of materials such as tantalum oxide in quartz sand have shown that the pulverized samples exhibit an excellent homogeneity. Consequently, a perfectly representative sample for further processing procedures, such as pellet pressing or element analysis, can be taken from any spot in the grinding jar.
RS 200 for Sample Volumes up to 250 ml
Grinding sets are available in sizes of up to 250 ml and accept samples with a maximum initial particle size of 15 mm. These sets perform circular oscillations of 700 to 1500 rpm, which often results in extremely quick pulverization of samples.
For this specific model, available grinding sets come in a range of different materials, such as hardened steel, steel 1.1740 for heavy metal-free milling, zirconium oxide, tungsten carbide and agate to allow for neutral-to- analysis grinding processes. The mill recognizes tungsten carbide or agate grinding sets and automatically limits the maximum speed to 1200 rpm or 700 rpm, respectively, to reduce wear.
Operation of the mill is very ergonomic with carry handles for the grinding sets, a quick-action clamping system and a rail on which the grinding sets easily slide into the correct position.
Application example - fine grinding of cement clinker: 200 ml of a sample with particle sizes up to 12 mm were milled in the RS 200 at 1500 rpm, using a grinding set of 250 ml stainless steel. After 60 seconds, a fineness of 85 microns (D90 value) was achieved.
RS 300 XL for Large Sample Volumes
This mill is used for the same applications as the RS 200, however, this model accepts initial particle sizes up to 20 mm. Depending on the accessories being used, a maximum of four samples may be processed at the same time.
The high degree of homogenization of this system is achieved by the effective 3-D grinding principle of the RS 300 XL, which accepts grinding sets weighting up to 30 kg and sample volumes up to 2000 ml. The closed grinding system of the RS 300 XL ensures that complete processing of the sample will be achieved.
Additionally, the auto- reverse function of this system assists in decreasing any potential caking of the sample. A selection of grinding set materials is available for neutral- to-analysis milling. The pneumatic grinding-jar clamping and the optional AutoLifter for heavy grinding sets provide convenient and safe handling during all grinding procedures.
Application example - fine grinding of raw cement: 2000 ml
of a cement clinker sample were pulverized in the RS 300 using a grinding set of 2000 ml hardened steel. The initial
particle size of the sample was approximately 35 mm; however, due to the brittle nature of the material, it was easily processed in the RS 300 XL without requiring any preliminary size reduction. Following a 6 min period, a fineness of 100 microns (D90 value) was achieved. The RS 200 pulverizes this material at a more rapid rate but requires a much smaller initial grain size.

Figure 1. Vibratory Disc Mill RS 300 XL for large sample volumes
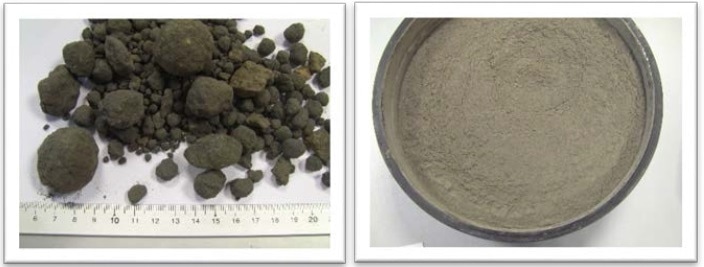
Figure 2. Cement clinker sample before (left) and after (right) grinding in the RS 300 XL.
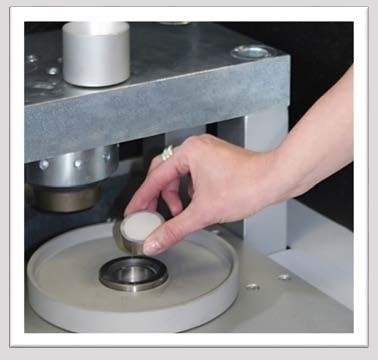
Figure 3. Smooth and stable pellet produced in a Pellet Press PP 40
Producing Pellets for XRF Analysis
Pellets with a plain surface are used for most XRF applications. . In contrast to loose powder, its compact size allows for the detection of lower element concentrations by X-rays. From an optical point of view, a pellet with a smooth surface is also preferable to one with a rough surface. Pellets are typically produced by either fusing the sample with salt or by pressing in a pellet press.
During the fusion process, volatile elements, such as thallium or cadmium, tend to escape and are therefore not detected, which is a limiting factor of this technique. Additionally, since the sample is heavily diluted with lithium salt, the detection limit is also impaired as compared to pellets. Certain elements including boron, iron and carbides could potentially damage the very expensive platinum crucible.
Another limitation of the fusion process is the long duration of this procedure that requires approximately 15 minutes, thus it takes much more time to produce a fusion bead than a pellet that only requires about two minutes to complete.
Hence, pellet pressing is the most common procedure for numerous applications, even though calibration of the spectrometer is more elaborate due to the sample matrix. A pressed pellet should basically fulfill the following quality criteria:-
- Homogenous
- Smooth surface
- Should not contain loose particles that could pollute the x-ray tube
- Stable
- Storable
Pressing the sample can be carried out with or without auxiliary materials. Free pressing of the pellet is not a very common process since the pellets are usually not sufficiently stable.
The most frequently used auxiliary materials are cellulose-based or paraffin-based, of which cellulose is particularly advantageous as it can act as a grinding aid in the homogenization process, thus helping to prevent caking of the sample inside the grinding jar. Cellulose can be used as grinding aid in vibratory disc mills as well as in mixer mills.
Wax is another option. It is added either manually or by mixing it with polyamide balls in a plastic jar in the mixer mill, after the sample has been ground
. The addition of wax makes the pellet’s surface indelible.
Moreover, wax is more inexpensive than cellulose and not hygroscopic which is important if the pellets are to be stored.
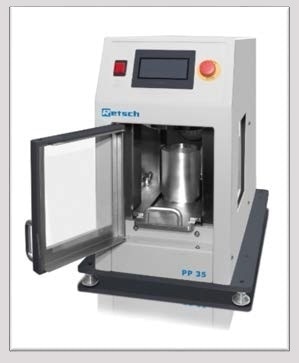
Figure 4. Benchtop Pellet Press PP 35
To further stabilize the pellets, steel rings or aluminum cups which are labelled on the reverse side are used for storing the pellets.RETSCH offers three different types of pellet presses:-
- Benchtop presses: PP 25 (pressure force regulation of 25 t) and PP 35 (pressure force regulation of 35 t)
- Floor model: PP 40 (pressure force regulation from 5 t to 40 t)
Conclusion
While a powerful technique, XRF requires a fully representative sample with suitable particle sizes. The sample preparation process prior to XRF analysis should neither change the characteristics of the material nor add unwanted trace elements. RETSCH Vibratory Disc Mills and Pellet Presses allow users to produce precise, reproducible and contamination-free samples for XRF with a minimum of time and effort.
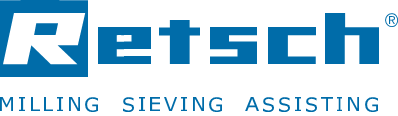
This information has been sourced, reviewed and adapted from materials provided by RETSCH GmbH.
For more information on this source, please visit RETSCH GmbH.