In this interview, Prof. Joly-Pottuz discusses her desire to advance our understanding of the behaviour of nanoparticles in ceramic materials - especially for ceramic materials used in biomedical applications.
How did you first begin studying the compression behaviour of nanoparticles?
I started my research into nanoindentation and nanocompression tests for ceramic materials back in 2008. In the beginning, we wanted to better understand the behaviour of nanoparticles in ceramic materials, and more specifically, for ceramic materials used in biomedical applications. We wanted to be able to produce nanocomposites from just a very small amount of powdered starting material.
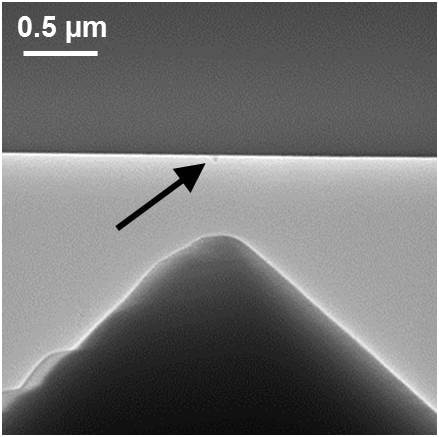
We observed a plastic deformation of nanoparticles during nanocompression experiments, which was surprising. Because these deformations were appearing at ambient temperature, we may be able to improve the density of the ceramic materials during the compression process before sintering.
We are now researching the nanocompression of single nanoparticles, to determine the relationship the structure and the nanoparticles properties. We use nanoindentation integrated with TEM to do this research.
Was it possible to do this type of research before you had a Hysitron nanoindenter?
We started our research using a non-Hysitron system, which we chose because it can be fitted in a high-resolution microscope. However, as our research progressed we found the system was not stiff enough and had other issues which meant we had to explore other options.
We then moved on to a Hysitron system fitted on a microscope that worked in environmental conditions. We did this because we wanted to be able to make nanocompression experiments under gas environment as this would allow us to mimic the behaviour of nanoparticles in their real environment.
We collaborated with Hysitron to develop the ability to perform nanoindentation experiments inside a ETEM. We worked with Hysitron directly and they visited us in Lyon where we spent three days working on the microscope.
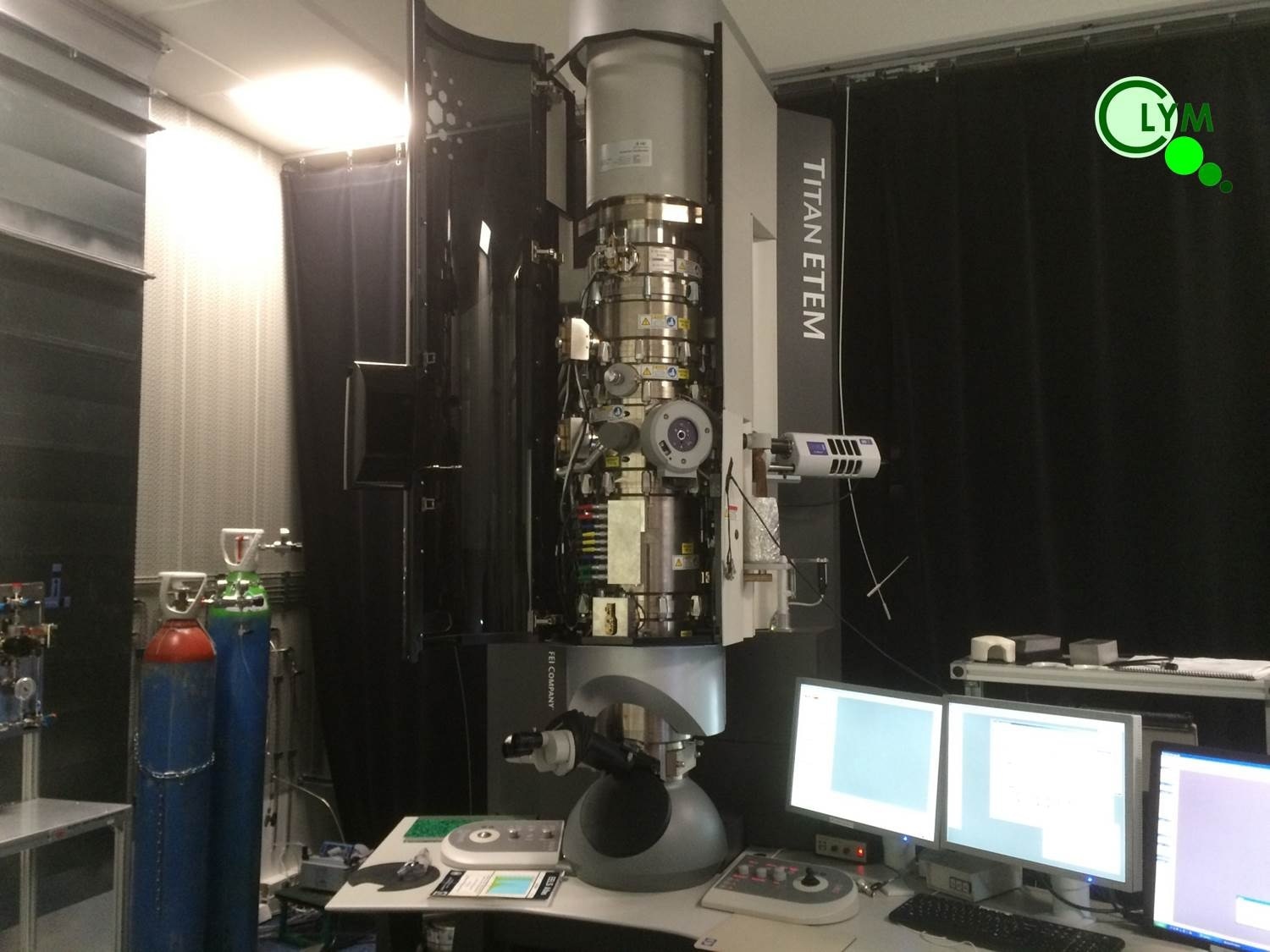
How have you been using nanoindentation to develop our understanding of nanoparticle compression behaviour?
We performed digital imaging correlation to produce load-displacement curves with reliable values. This is dependent on determining the correct contact area between the nanocompressor and the nanoparticle being compressed, this is difficult because the electron beam takes images in 2D. To compensate for this, we need to take precise measurements of the contact area.
Using these values, we can determine the mechanical properties of the nanoparticles like their yield strength and model the compression of nanoparticles. This can be very interesting for certain materials.
For example, we have done some research on alumina; when in a bulk form alumina has an ‘alpha-alumina’ structure. However, when the alumina is powdered into nanoparticles with a diameter less than 100 nm it is present in a different form, which has a different structure. This new structure had not been analysed before, and we could use our methodology to determine the mechanical properties of these nanoparticles and obtain values on the structure.
Has the software provided with the Hysitron nanoindentation system been useful in your research?
The Hysitron software is easy to use, and it allows us to correlate between the image and the load-displacement curves. This is very interesting because we didn’t have this function with our previous system, which meant analyzing the displacement curves was very complicated. Before, we couldn’t observe some points on the curve, and were therefore unable to determine the relationship between the movies and the displacement curve.
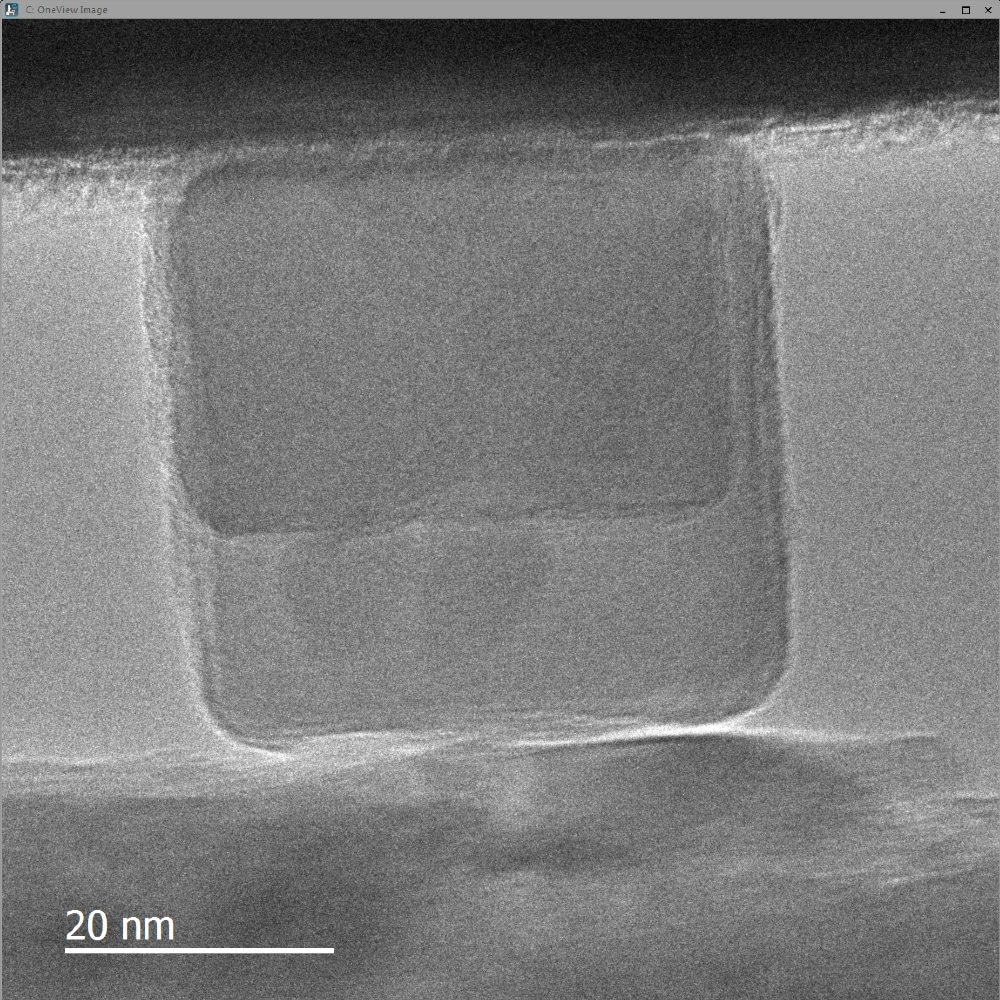
The Hysitron software automates this analysis and allows us to determine every point on curve, meaning we can calculate more accurate relationships.
What real world applications do you expect your research to have?
Our research will facilitate better comprehension on the grinding limits in nanoparticle based ceramics. Currently, when you have a powder, you’re not always able to create a composite with the required graining.
Being able to better understand the mechanical properties of nanoparticles may improve the sintering process of ceramic materials, thus leading to ceramic composites with the appropriate grain size.
Developing a Fundamental Understanding of Nanoparticle Compression Behaviour
Developing a Fundamental Understanding of Nanoparticle Compression Behaviour from AZoNetwork on Vimeo.
About Professor Lucile Joly-Pottuz
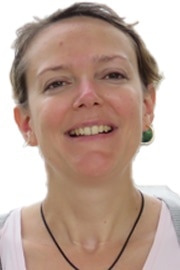
After graduating a Master degree from the University of Lyon in analytical chemistry, Prof. Joly-Pottuz worked 4 years in the field of tribology. Her PhD thesis dealt with the tribological properties of nanoparticles (carbon nanotubes, WS2 and MoS2 nanoparticles) used as lubricant additives for applications in severe contact conditions. Then she studied the tribological properties of carbon onions in mesotribology and nanotribology as a postdoctoral fellow at Kobe University (Japan).
While studying nanoparticles she gained skills in TEM and SEM characterizations and developed EELS spectroscopy tools in order to determine the properties of carbon materials. Since 2008 she is an associate professor at University of Lyon / INSA Lyon (MATEIS laboratory). Her field of research is the characterization of ceramic materials and her main research activity deals with the development of nanocompression experiments applied to ceramic nanoparticles.
She spent five months as invited researcher in Tohoku University (Japan) working on simulation tools to better model the behavior of ceramic materials and complete their characterization by electron microscopy. She is part of the Materials Science teaching department of INSA Lyon, giving lectures in crystallography and characterization techniques.
Disclaimer: The views expressed here are those of the interviewee and do not necessarily represent the views of AZoM.com Limited (T/A) AZoNetwork, the owner and operator of this website. This disclaimer forms part of the Terms and Conditions of use of this website.