Computerized systems are those which comprise the components shown in Figure 1.1, namely, a computer system and a controlled function which is operating within its specified working environment.
The elements of the computer system include:
- Hardware, which means the computer platform on which the applications software is run, and includes a workstation, server, clients, hubs, routers, switches, bridges and cables. It may occupy one segment of a whole network, and may be linked to peripheral devices including printers or plotters and the connecting cables.
- Software, which has multiple layers, including
- the operating systems used by the workstation clients and connected server
- the system that operates the network in the switches and routers that keep it running
- typical business applications such as Word and Excel
- software for computerized system applications
- utility software linked to the above, like a database or a reporting language
.jpg)
Figure 1.1. Elements of a Computerized System.
The controlled function consists of two parts:
- The equipment connected to the computerized system such as the thermal analysis setup, with its firmware, which should ideally be validated whenever the software is validated to ensure high-quality results
- Trained operators and written procedures such as SOPs and equipment operating manuals, or data system software
Validation does not mean simply testing the computerized system and calibrating it, but much more. Failure to qualify the computerized system’s software could lead to regulatory action even if the instrument has been validated.
Calibrating and Adjusting Equipment
This function must be carried out by the vendor, and is defined by Parridt as follows, “The term calibration implies that adjustments can be made to bring a system into a state of proper function. Such adjustments generally cannot be made by analysts and are best left to brand service engineers who for, or support, the instrument manufacturers.”
Calibration is thus a process by which it is confirmed that the values shown by the measuring instrument are correct. The number of sensors determines the type of calibrations required. Calibration of equipment may thus be classified as calibration and adjustment.
- Calibration means determining the extent of deviation of an instrument parameter
- Adjustment means changing the instrument parameter so that it will meet the specification
Calibration and adjustment are both dependent on a material for reference, or a standard. These are derived from known values in literature, or from values that have been recognized as international standards.
These are essential to preventive maintenance to keep the machine in good working order, and in turn to qualification of analytical instruments. Documentation is important when calibration includes adjustment functions, as in this case it should not be mistaken to be qualification of the analytical instrument.
Analytical Instrument Qualification (AIQ)
AIQ, formerly termed equipment qualification, EQ, is the process by which an apparatus is demonstrated to be fit for its use. All the instrument parameters such as accurate temperature or linear response that are used by the techniques for which the machine is used are then expected to be within accepted limits.
In the ideal case these parameters follow international or recognized standards, though this is not always so in real life. The instrument parameters which are to be qualified may differ between organizations because many laboratories use their own specific methods. EQ is vital for any equipment used in a controlled environment and forms the foundation for any other validation of analytical methods.
It was the Pharmaceutical Manufacturers Association (PMA) which brought this term into use. For users, it has four phases, and the user’s role is shown in Table 1.1 below.
Table 1.1. Overview of the different phases relevant for the user in the qualification of an instrument.
.jpg)
Computerized System Validation (CSV)
As with other equipment, CSV is meant to demonstrate that the system operates in a way that is appropriate for its use. As with AIQ, IQ, OQ and PQ are different, but their actual meaning in this context is slightly different which may confuse the understanding of these terms, as recognized by the FDA, which has led to its exclusion from the Guidance for Industry on the General Principles of Software Validation document. Table 1.2 below compares the qualification steps in AIQ and CSV and Figure 1.2 shows more differences in the way these three terms are used in the two procedures.
Table 1.2. Differences in qualification terminology between Analytical Instrument Qualification and Computerized System Validation.
.jpg)
.jpg)
A special problem in this case is that the computerized system which is being validated is part of the measurement instrument, and therefore needs to be qualified as well. The user will therefore carry out AIQ on the instrument via IQ and OQ, as well as CSV on the software via IQ, OQ and PQ.
Any validation plan must detail how this is to be achieved, whether the software and instrument qualification will be separate or as part of the same approach. In thermal analysis, most instruments require the computerized system for data processing and acquisition, making the second option the only feasible one.
.jpg)
Figure 1.2. Differences between Analytical Instrument Qualification and Computer System Validation terminology.
Reconciling AIQ and CSV
Table 1.2 shows the essential similarity between the DQ and IQ stages in CSV and AIQ. Both of these reveal whether the system is qualified and installed properly. The major variation is in the OQ and PQ stages, partly due to the increased complexity of a computerized system compared to an analytical instrument. The OQ stage shows the fitness of the item for its intended objective, and should be carried out by the laboratory, as only then is the instrument permitted to be put into operation.
CSV however involves two more stages, the OQ which confirms that the system works according to the vendor’s claimed operating ranges, and the PQ to show that it works in the actual operating setup defined by the user. This last stage is to be done by the laboratory, and is the last step before the computerized system can be used in a regulatory environment.
In real life, this means that thermal analysis systems which are typically or inevitably computerized must always undergo testing of the thermal analysis instrument, either explicitly or implicitly, as part of CSV. These are so closely connected that EQ and CSV are performed at the same time.
Differing Objectives of CSV IQ and OQ
The aims of these two phases of CSV are shown in Figure 1.3, which shows the IQ of the computerized system at the top and the IQ of each layer of the system from the bottom upwards.
- Computer hardware installation and qualification
- Installation and configuration of the operating system, such as putting the Internet Protocol address of the computer on the computer network and turning operating system functions off and on as is required
- Installation and qualification of the database
- Installation and qualification of thermal analysis software
The concept of this type of testing is that each layer can be reached only by successful termination of the one just below it.
.jpg)
Figure 1.3. Differences between Installation Qualification and Operational and Performance Qualification.
Analytical Method Validation (AMV)
This is a method to ensure that a method of analysis is fit for its purpose, which means the analyst should know the reason for using the method and the acceptable values for the validation parameters for that method.
The Relationships between AIQ, CSV and AMV
Figure 1.4 shows how these terms are related. The first three are to be done by the equipment vendor, while the rest should be done by the end user or laboratory.
.jpg)
Figure 1.4. Relationship between Analytical Instrument Qualification, Computer System Validation and Analytical Method Validation.
The foundation of the whole structure is to test that the analytical system or instrument has been designed and built or maintained properly. This is the responsibility of the vendor who builds and tests it including the software, and thereafter maintains and upgrades it as required.
The user should, of course, choose the right kind of instrument and software for the analytical task. This is the job of the laboratory, which should have a clear specification for the functions to be carried out by the instrument as well as the requirements for the software. Attention must be paid to compliance with health authority regulations as well, such as GMP or 21 CFR part 11.
The next step is laboratory responsibility for AIQ and CMV. The URS defines the operating parameter range against which the instrument is qualified, such as using a digital thermometer that is calibrated to national standards to measure the set temperature of the instrument, and thus confirming the actual temperature is the one that is set. After instrument qualification and software validation, the next step is individual validation of each analytical method.
Application of Validated Methods with Qualified Instrumentation
After system qualification is complete, it is ready to be used in a regulatory environment and can itself be part of developing, validating and applying methods. The qualification assures the analyst that the system is working as expected so that the analysis is free of major variables.
AIQ vs Method Validation
Analytical instruments cannot be qualified by method validation, but AIQ enables method development, validation and operation within the operating range of the instrument. If any method has parameters that go beyond this range, the analytical instrument must have a requalification performed before the method can be validated. Thus method validation and AIQ are not the same, and validating a method does not mean the equipment is qualified.
.jpg)
Figure 1.5. Relationship between Analytical Instrument Qualification and Analytical Method Validation.
AIQ tests module or system performance over the whole range of operating parameters of an instrument which is in use or will be used by the laboratory. By way of illustration, if a thermal analyzer has an operating range of 100-300 oC, any method that is performed between these limits is safe for use as shown in Figure 1.5, where both methods 1 and 2 are acceptable for this instrument in a regulatory setup.
On the other hand, a temperature of 350 oC falls outside the qualified range and means that the instrument must be requalified before the analysis can be accepted from the regulatory point of view. Figure 1.5 shows this in method 3 which has its upper end of analysis well beyond the range for which the instrument is qualified.
Thus it is most important to specify the laboratory requirements before the thermal analyzer is purchased so that the qualification parameters and the operating range can be ensured. If the method exceeds this range for any parameter there is a need to requalify the instrument and even in some cases to update the specifications for the user requirements.
AIQ vs AMV
The aim of PQ is to ensure the instrument functions according to the requirements of the user and not of the vendor, but AMV is meant to assure that the method performed with the qualified instrument is able to achieve the purpose intended.
AIQ will therefore demonstrate proper instrument function such that the system generates the right measurement value and curves. Certified materials and substances like certified pure metals and inert materials, certified gauges and weights, are used independently to calibrate all critical user parameters such as:
- Temperature, by the use of pure metals
- DSC heat flow and enthalpy, using the enthalpy of fusion of pure metals
- TGA weight by using internal and external calibrated weights
- TMA/DMA force and displacement by calibrated gauges
How AIQ Affects Method Transfer
It is important to qualify instruments if a method is to be transferred from one laboratory to others. This is because even if differing models or those from different vendors are used, provided they are qualified over the same operating range it is more probable that the method will be transferable with much less trouble than otherwise.
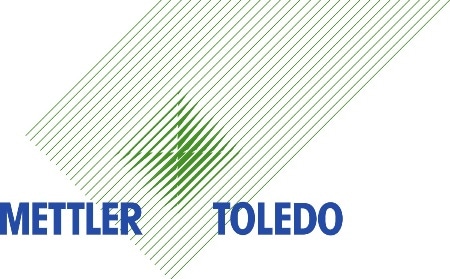
This information has been sourced, reviewed and adapted from materials provided by Mettler Toledo - Thermal Analysis.
For more information on this source, please visit Mettler Toledo - Thermal Analysis.