Polymers are also called macromolecules, being very large organic molecules composed of an extremely high number of repeating smaller units called monomers. Their applications are widespread, and include rubber, plastics and adhesives, among others. A polymer molecule is generally anywhere between 10 nm to 1000 nm long, with molar masses going above 10000 g/mol. Polymers invariably contain mixtures of macromolecules which are of a range of sizes, which means their average molar mass is cited.
At low temperatures, the nature of polymers is that of glassy solids. Once they are heated above their glass transition temperatures, they soften and show elastic characteristics. Polymers may be classified in several ways, such as the type of polymerization the monomers undergo, their structure, such as linear, branched or a network, or their properties such as thermoplastics, elastomers or thermosets.
Thermosets
These are highly crosslinked network polymers that occur as three-dimensional networks which are very dense. They fail to melt on heating, instead decomposing. They are rigid and cannot undergo plastic molding, nor can they dissolve. They are synthesized from liquids but during molding they cure to form the final polymer. Once the glass transition temperature is crossed, they show rubbery and soft characteristics.
Elastomers
These are network polymers but show a smaller degree of crosslinking, so that cooling causes them to become glassy. Heating does not produce melting nor viscous flow due to the crosslinking. If they show very low glass transition temperatures, below room temperature, they appear soft and rubbery under normal conditions, but deform markedly under mechanical force.
However, the removal of the force causes them to return almost completely to their original shape. The crosslinking or vulcanization of the chains of the polymer prevents molding or dissolution, which means molding must take place before the starting materials undergo crosslinking.
Thermoplastics
These are linear molecules or branched molecules without crosslinking. They form filamentous macromolecules which are attracted together by intermolecular forces or simply entangled. They undergo softening when they are heated, or melt, lending themselves to easy molding and recycling.
Cooling below the glass transition temperature causes them to assume a glassy character. By building up the strands in a uniform manner without very many side chains, partial crystallization may be achieved, causing them to have both amorphous and crystalline regions. Once the crystallite melting temperature is crossed they melt and become liquid. Linear polymers often dissolve in some solvents and may therefore form films from the solution.
.jpg)
Figure 1. Schematic diagrams of different polymer molecules. a: Amorphous thermoplastic. The two macromolecules are shown in different colors in order to distinguish them more easily. b: Semicrystalline thermoplastic. In the center of the diagram is a chain folded crystallite. The remainder of the molecule and the red colored molecule are not able to crystallize because of the randomly occurring side groups. c: Elastomer. The two macromolecules are linked at two points (colored blue). d: Thermoset. The red molecules (resin) are three-dimensionally crosslinked by the blue curing agent.
Polymer Synthesis
A polymer is formed by linking thousands of monomers end to end by covalent linkage. The monomers themselves are molecules that react with each other because they have one or more bonds that do not require much energy to cleave, leaving room for monomer linkage via chemical bonds.
Polymerization
In the process of polymerization the macromolecules are formed by monomers which link successively to form a giant chain. With a single monomer type a homopolymer is formed, but with multiple monomers a copolymer is the result. Polyethylene is a homopolymer of ethylene, C2H4, a molecule with two carbons joined by a double bond.
If the pressure and temperature are right and there is a molecule such as benzoyl peroxide to initiate free radical formation, the double bond is broken to form a single bond, so that the carbon atoms can now form free radicals with one unpaired electron each, to bond to another molecule of ethylene.
H2C=CH2 → H2C.-C.H2
H2C.-C.H2 + H2C=CH2 → H2C.-CH2 - CH2-C.H2
This causes the dimer itself to form but as a free radical itself, promoting further polymerization. This is the most important among the polymerization chain reactions.
Other mechanisms of polymer formation include ionic polymerization. The reactive atom here is an ion, at the growing polymer end. The ion may be anionic or cationic in character. If the monomer has a side groups such as propylene (CH3-CH=CH2) or an inorganic atom like vinyl chloride (CH2-CHCl), these may be found to be randomly distributed in the polymer in some cases, forming an atactic polymer which does not crystallize well, or have a regular arrangement, either syndiotactic, occurring on alternate sides, or isotactic, on the same side.
Copolymers are characterized not only by the nature of the monomers themselves but by the distribution of the monomers. Randomly arranged monomers cause the formation of a random copolymer with a single glass transition. Block copolymers, and in particular graft copolymers, have glass transitions which correspond to the homopolymers found in them.
.jpg)
Figure 2. The monomers can be randomly distributed in the copolymer molecule or be present in blocks. Side chains can also be grafted onto the main chain.
Polyaddition
This term refers to the chemical reaction of compounds with low molecular weight (MW) but with reactive groups such as hydroxyl, isocyanate, amino, epoxy or acid groups. The monomers are linked by oxygen or nitrogen in these groups. The following shows an epoxy resin reacting with an amine:
.jpg)
The progression of the reaction is due to the fact that each monomer retains one more reactive group. A thermoset material forms crosslinking because the secondary hydrogen atom of the amine can react with an epoxy group, so that each molecule of the amine can attach at any of four points.
Molecules with two attachment points typically produce linear polymers, but three-dimensional crosslinked polymers form when there are three or more attachment points.
Polycondensation
In the polycondensation reaction, one or more types of monomer bond by eliminating a compound with low MW, typically water. A common example is hexamethylene diamine, or 1,6-diaminohexane, polymerizing with adipic acid or hexanedioic acid, to produce polyamide 66 (PA66) or nylon 66.
The following figure shows the elimination of a water molecule formed by a hydrogen atom from the hexamethylenediamine and an OH group from adipic acid, with the reaction progressing at both ends of the new polymerizing molecule to form a chain. Nylon 66 is so called from the number of carbon atoms in the two monomeric units.
.jpg)
Figure 3. Polycondensation of hexamethylenediamine and adipic acid to polyamide 66.
Thermoplastics
Thermoplastics demonstrate weak binding forces between the polymer chains, such as van der Waals forces, and entanglement of the chains, but no crosslinking. This allows the polymer chains to stretch and to turn with ease when exposed to a load. A semicrystalline thermoplastic is a polymer with both crystalline and amorphous regions, and the crystallite melts with heating to melting point. Thermoplastic materials show marked variation in properties with change in temperature.
If the thermoplastic is below its glass transition temperature, Tg, the properties are those of a glassy rigid material. At Tg it becomes leathery, above it the thermoplastic turns rubbery and becomes liquid at last, giving them their characteristic moldability and recycling fitness. Temperature affects the Young’s modulus of amorphous thermoplastic as seen in the following figure. The table shows the melting temperatures and glass transition temperatures of many common thermoplastics.
.jpg)
Figure 4. Influence of temperature on the elastic modulus and the behavior of a thermoplastic.
Table 1. Glass transition temperature and melting temperatures of various thermoplastics.
.jpg)
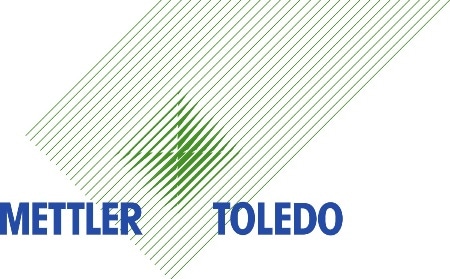
This information has been sourced, reviewed and adapted from materials provided by Mettler Toledo - Thermal Analysis.
For more information on this source, please visit Mettler Toledo - Thermal Analysis.