A key element in any specification of stainless steel, despite its intended use, is surface finish. Finish is an important design element and should be specified for those applications where appearance is significant.
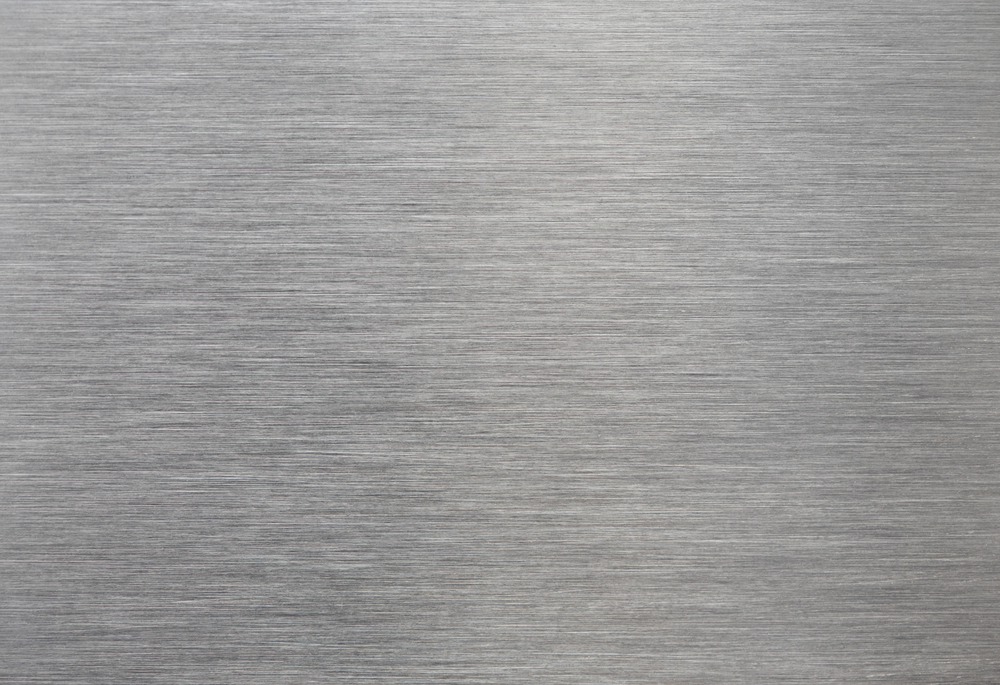
Image Credit: Shutterstock/Bragin Alexey
For applications that are non-decorative, the surface finish may have implications for corrosion resistance, wear, friction or maintenance, and so must be carefully selected and specified clearly. The specification should never be loosely worded, or the choice of finish be left to the supplier, e.g. ‘Type 304 with a 180 grit finish’. It must be correctly identified by a standard industry designation or by a trade name, e.g. OPTISHEEN®.
Finishes and Design
There are a large variety of decorative finishes available, so it is key to find out the most suitable finish for the application needed. The appearance of stainless steel is a critical design element for highly visible applications, an error in when choosing the finish can change the intended effect.
Properly finished stainless steel is easier to keep clean for hygienic and commercial applications, such as hospitals and restaurants. In consumer products, such as catering equipment, the aesthetic of a well-polished sheet of stainless steel has high sales appeal.
There are numerous functional considerations, in addition to the visual appearance of polished stainless steel. Properly polished stainless steel looks good and helps to reduce the risk of bacteria being retained by the material when it is utilized in sanitary applications.
A smooth surface is less likely to accumulate deposits, and is stainless, which generally become focal points for localized corrosion. A correctly polished stainless steel surface has a better resistance to corrosion than a surface that is roughly or badly polished, for use in aggressive environments, such as in the offshore or nuclear industries. All stainless steel finishes perform better when maintained and cleaned correctly.
Finishes and Fabrication
Some fabrication tasks, for example grinding prior to gluing or painting could need a rough surface finish but usually, a smooth, well-finished sheet takes less physical effort than a rough, coarse one when it comes to blending. Some finishes are harder to recreate manually than others, which leads to fabrication difficulties. ‘Special’ finishes which cannot be replicated easily in a fabrications workshop are a prime example. Due to this, a fine satin finish (such as Optisheen®) is practical and popular for fabrication shops worldwide.
Polished Finishes
The term “polished” lends itself to a variety of finishes which are typically two types:
- Satin or grained
- Brightened and mirror polished
Polishing improves consistency and appearance, helps practicality to fabricate and repair/blend after welding and to mask minor damage, it also makes cleaning easier. Satin Polished stainless steel is widely available, relatively low cost, practical in use, and the most frequently employed.
Optisheen has acquired a reputation for being the highest quality satin-polished stainless steel finish for a number of years, many well-known brands specify it when ordering checkout counters and kitchen and hospital equipment. A true polished finish, attained by a unique 'wet cut' process using a polishing belt impregnated with a special polishing compound - made to a secret formula, is what differentiates Optisheen from others.
Most other 'polished' finishes are actually ground finishes produced by grinding the dry surface with an abrasive belt. The contrast is similar to having your jewelry polished by a jeweler, using professional jewelers' rouge, or trying to polish it yourself using emery paper or sandpaper. The results would be unavoidably different in surface character.
Dry ground material has a torn grain structure caused by direct contact with the polishing belt, with microscopic voids, laps, and tears in the surface that are concerning for two reasons:
- They cause hygiene problems by providing 'traps' in which bacteria and contamination can reside. In addition, the surface tends to be rougher and strongly directional, making it more difficult both to clean and to keep clean.
- They promote corrosion by breaking the protective oxide film, leading to discoloration and staining.
Optisheen, having long and shallow graining that is non-directional, does not suffer from this torn grain structure (see diagrams). This difference makes it much easier to clean and more hygienic and, as well as more corrosion resistant, this can be felt easily by running a finger across the grain.
The sheet is not in direct contact with the belt during the process, only the lapping paste. Furthermore, the consistency of finish, both from sheet to sheet and from batch to batch, is unparalleled, which makes 'matching up' really simple, even over a number of years.
Users of installations and equipment and in service applications, which are made with Optisheen, have discovered that cleaning times are lowered by up to 75%. Equipment surfaces are also a lot lower in harmful bacteria, which has increased the popularity of the product tremendously.
It is widely chosen for external and internal use by a long list of familiar names – including McDonald's. They hold the importance of appearance and cleanliness standards so highly that they even run advertisements in the trade and national press encouraging consumers to inspect their kitchens at any time.
OPTISHEEN® is a fine satin finish with a smooth texture and an attractive lustre. It is made using a special cutting compound and fine abrasives, which enables a clean, smooth ‘wet’ cut surface. The smooth surface ensures minimal entrapment of surface debris from polishing or in use, making it fitting for many applications, especially catering and architectural uses. Due to its long, shallow grain and less prone to staining in external or critical applications, it is also much
easier to clean. The finer grain blends more easily after fabrications than coarser finishes which require more physical effort.
The “wet” cut abrasive system gives a high degree of consistency from sheet to sheet,
and grit size can be altered to preserve the correct levels of reflectivity and roughness. This finish is pleasant to the touch and has a pleasing appearance, making it suitable for a vast range of products or components.
Typical uses include:
- Shop fronts
- Architectural panels
- Catering equipment
- Restaurant equipment
- Lifts
- Luggage handling equipment
- Control panels
.jpg)
OPTISHEEN® Feature |
OPTISHEEN® Benefit |
Cleans quicker, easier more hygienic |
Cleaning time reduced as much as 75%. Important where large surfaces are involved. Minimal disruption. Multi- directional wiping. Less smears. Simple cleaning regimes. |
Less prone to staining |
Minimal maintenance. Retains appearance. Good for high profile locations. Less cleaning required. Minimises build-up of biofilms. |
Better corrosion resistance |
Effective in harsh environments. Good for outdoor applications: architecture, street furniture etc. hot and cold or humid conditions. |
Looks good, provides consistency |
Always matches simple replacements. Decorative. Product enhancing. |
.jpg)
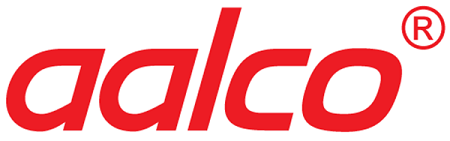
This information has been sourced, reviewed and adapted from materials provided by Aalco - Ferrous and Non-Ferrous Metals Stockist.
For more information on this source, please visit Aalco - Ferrous and Non-Ferrous Metals Stockist.