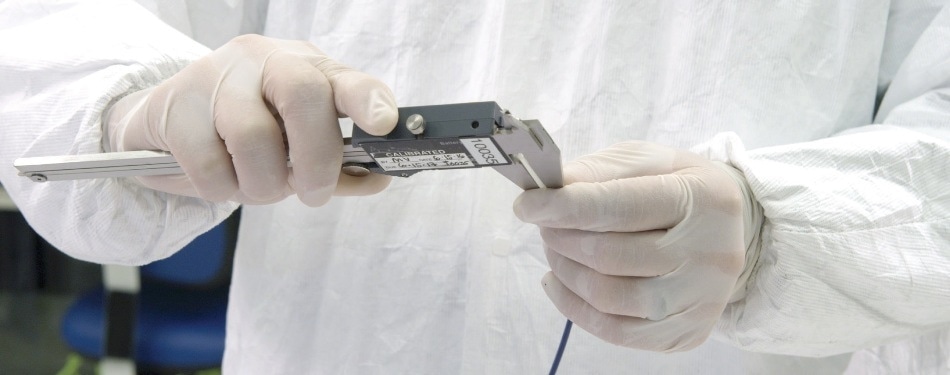
This article describes the development of a custom-made process for catheter manufacturing by the Zeus Z-team, saving the company $550,000 a year
The Challenge
A multinational company manufacturing medical devices was having problems with one stage of their catheter production process, namely the heat shrink recovery process.
The Heat Shrink produced by Zeus was functioning to inspection standards on the incoming stream. However, the reflow process was showing over-tight recovering of the product over the shaft of the catheter. Thus the reflowed thermoplastic was allowing the braid beneath to be seen. This resulted in the appearance of blisters over the whole length of the catheter.
The heat shrink recovery and reflow process was thus causing a loss in yield of about 65% for this particular component. This led to the following issues for the client:
- Increased costs of production
- Lower returns
- Frequent inspections needed
This problem was addressed by the Zeus Z-team who came to the client to find both immediate and long-term solutions for this manufacturing problem.

The Analysis
In this case the Z-team carried out a root cause analysis using their Six Sigma tools to examine what was happening during the heat shrink recovery process. The findings showed that the specifications required changing with respect to the inside diameter (ID) of the recovered and expanded heat shrink. As a stopgap measure, Zeus stepped up the strictness of inspection and made sure that materials which were shipped had these newly prescribed sizes.
Simultaneously, Zeus engineers tinkered with the in-house process to enable its capabilities to fit these new specifications for the heat shrink. Validations were carried out in an organized manner, following which both Zeus and the OEM observed that the best technique to ensure that yields were reliably over 95% was to increase the ID size of the recovered heat shrink and reduce the ID size of the expanded form.
In short, the solutions consisted of:
- Changing the ID size
- Increasing the number of inspections
- Changing the material
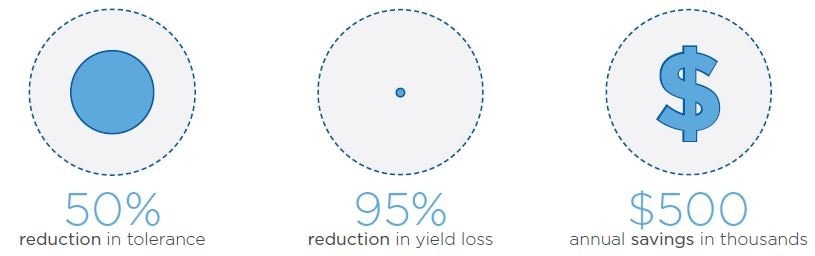
The Results
Following the adoption of these measures, tolerance was reduced by 50%, which reduced the yield loss by 95%. These changes thus teamed up to save the client more than $550 000 a year. The newly specified heat shrink ID sizes brought about a lower shrink ratio for the material and brought down its tolerance by 50%. The new heat shrink had an optimal window of performance which was tailored to the catheter production line for this client.
The cooperative management of this problem by the Zeus Z-team and the customer caused a greatly reduced loss in yield for this one production item, to below 3%, while the number of required inspections went down, as well as permitting lower inventory. The customer had increased performance, lower losses and less inspection time.
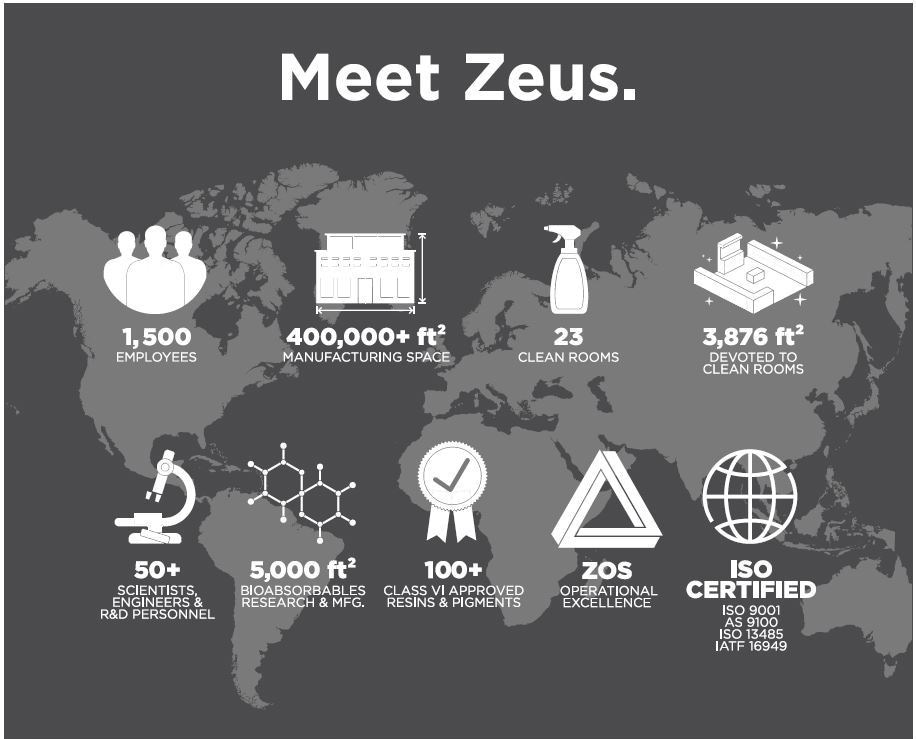
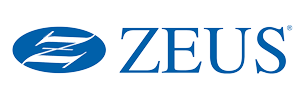
This information has been sourced, reviewed and adapted from materials provided by Zeus Industrial Products, Inc.
For more information on this source, please visit Zeus Industrial Products, Inc.