Cans for food and drinks have been changing rapidly over the past few years. Although each individual change may have been missed by many consumers, a direct comparison between the old cans and today’s state of the art will show the rate of evolution. The packaging has become lighter, more colourful, and less wasteful, whilst retaining strength and ease of opening. The cause of these changes in the steels sector of the packaging industry is the success of the ‘Ultimate Can’ project, a collaboration between, initially, British Steel Tinplate, Hoogovens and Rasselstein AG (and now Sollac) aimed at streamlining the steel drinks can and so competing more effectively with its counterpart. The Market The market is a large one. Around six billion drinks cans are opened in the UK alone each year, of which 80% are aluminium. In other countries, the proportions vary, but the share is almost 50:50 for Europe as a whole. (For food cans, the situation is different, with the need for high temperature cooking all but eliminating aluminium from the market, although the same technological improvements are also now being applied here.) Recently, some aluminium lines in Europe have converted to steel for can production, a trend which European steel producers expect to continue Lightweighting One of the major achievements of the project has been a 30% reduction in the weight of a standard 33cl steel two-piece can, whilst retaining superior strength properties over an aluminium equivalent. Such lightweighting should also be possible for larger can sizes. Weight Reduction in Steel Cans Steel cans were greatly over-engineered a few years ago, and due to this and some new design techniques, much thinner steel can now be used for can production, figure 1. Work at British Steel’s £4.5 million Packaging Steels Development (PACS) Centre, which contains a purpose built pilot can-making plant, has produced 19g steel cans with the desired mechanical properties from steel with a starting gauge of just 0.20mm. This compares with a typical starting gauge and weight of 0.27-0.29mm and 27-28g respectively. Aluminium cans are still much lighter, at just 11-13g, but must have thicker walls to obtain the strength required, and so work out more expensive than the lightweight steel cans due to the price of the extra metal used. 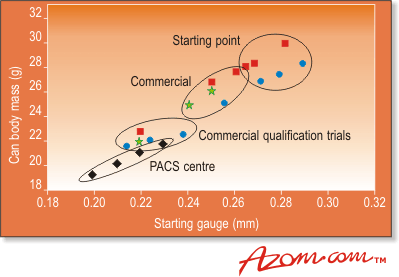 | Figure 1. Lighter 33cl can production using a thinner starting gauge of steel. | Softer Steels The other major advantage of aluminium was its softness. The harder steel caused more tool wear problems, leading to production down time. However, the soft-temper continuously annealed grade of steel produced especially for cans now is just as soft as aluminium but retains steel’s greater ductility. Work-Hardening and Bake-Hardening Properties Such thin steel can be used for can production because of the metal’s work-hardening and bake-hardening properties. During the DWI (draw-wall-iron) process, the metal is drawn to a thickness of just 60 gm in the mid-wall section of the can. This drawing increases the strength of the steel, allowing the wall to withstand the internal pressure, which can be up to 100psi, or 6.9bar. The various sections of the can, from the base (or ‘dome’), to the thicker top wall section, are also strengthened by these processes, and when lacquer is applied to the inside of the can and cured at typically 190°C, bake hardening results in a further strength increase of 60-70N.mm-2. Aluminium does not exhibit either of these properties, and such processing actually slightly weakens the aluminium can, figure 2. 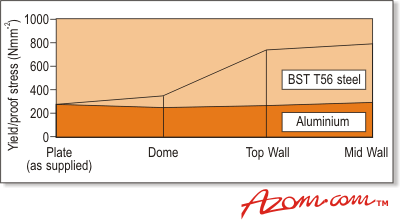 | Figure 2. Strength levels of steel and aluminium in different regions of a drink can. | Improved Steel Quality The DWI production process is extremely fast for current commercially produced cans, and any new lightweight cans must withstand the stresses they encounter. With thinner metal, any slight inconsistencies may cause the cans to rip, and so part of the project has focused on optimising the mechanical properties of the steel, and developing special clean casting to avoid the pick up of non-metallic contaminants during the casting process. With line speeds of up to 350 cans per minute at present, and the possibility of 500 cans per minute in the future, the steel used for lightweighting must be as uniform and free of defects as possible. Dome Design In the past, cans had straight wall designs, but these now look peculiar compared with the industry standard necked cans which stack one on top of each other. The ‘Ultimate Can’ project had to take into account dome design when attempting to produce a lightweight can, because the steel thickness partly determines the dome reversal pressure, or the threshold pressure above which the base of the can ‘pops out’ and becomes convex instead of concave: The profile of the can dome is also critical, and the production of a base ridge of the specified diameter must be incorporated. The finite element analysis technique allowed computer modelling of dome design, and showed that acceptable dome reversal pressures could be achieved with the thin steels required by lightweighting using new dome design profiles. Necking
At present, most of the opening devices on drinks cans are made from a special grade of aluminium, even if the main body of the can is steel. Since the move away from straight walled designs, the trend has been for the neck diameter of the can to shrink, using less of the costly aluminium in the top. Initially, a 211 neck was used (a diameter of 2 11/16 inches), but in 1986 the industry standard was reduced to a 206 neck, and now the first 202 lightweight steel cans have been produced at speeds of 1500-2000 cans per minute in the PACS centre. Multi-Die Necking To obtain a conventional 206 neck, the methods involved require can top wall thicknesses of over 0.14mm to prevent metal thinning, but with lightweight steel cans, the top wall thickness can be less than 0.11mm. New techniques have achieved both 206 and 202 necks with lightweighted cans. Multi-die necking, involving necking the can with smaller and smaller dies until the desired diameter has been reached, has proved very successful, as has the combined technique of die necking followed by a spin necking process, figure 3. Dome dimensions have also been adjusted to allow stacking of the new, thinner neck cans.  | Figure 3. The spin necking process. | Ecotop As an alternative to the aluminium stayon-tab end, British Steel Tinplate, in partnership with other European producers, have launched the Ecotop, a can end manufactured from a new grade of steel with the necessary properties to allow easy opening and to complement the development of the lightweight steel can. The Ecotop allows the production of an all steel can, with the environmental benefits of better recyclability and energy savings. The principle of the easy open facility is of two buttons completely cut through except at hinge points, which are then re-sealed. To open the can, the first button is pressed to release the pressure, and the second, larger button is then pressed into the can to provide the opening for drinking. There are no sharp edges, no detachable tab, and the metal cost is relatively low compared to the aluminium stay-on-tab design. To date, 206 ends have been successfully used commercially on Sainsbury’s own brand products, and a 202 end has also been produced to fit the new lightweight cans. A new lining compound has been developed, and coloured can ends have been made possible by the production of the Ecotop with pigmented lacquers, figure 4. Trials are also being carried out with film laminated steel. 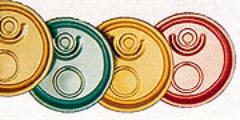 | Figure 4. Ecotop can tops made in a variety of colours from laminated steel. | Recyclability All-steel cans provide ultimate ease of recyclability. Food or drinks cans can simply be charged into the steel production furnace without prior stripping or treatment, and at present, 25% of every tonne of steel produced has to come from scrap such as cans. If an electric arc furnace is used, 100% recycled material can be used to produce new steel. Any additional materials in the can, such as lacquer and wall decoration, are burned in the furnace and reduce energy costs. Contrary to popular belief, over ten times as many steel cans are recycled each year in the UK as aluminium cans, due to the large volume of steel food cans reprocessed. Food Cans All the technique and production developments discussed for drinks cans are valid for food cans, although the traditional three piece design is still predominant as opposed to the two piece drinks can design. Lightweighting developments in food cans must take into account the need for high temperature processing to cook the food in the can, which results in large fluctuations in pressure as well as temperature. If the walls of the can are made thinner, improved bead designs must be introduced to give the necessary strength, but the depth, pattern and profile of this beading must be controlled. If the depth is too great, the can will concertina under the pressure when stacked. The lightest cans available are produced for food which requires pasteurisation only, such as milk products, where the starting gauge of steel used is as low as 0.12mm. Future Developments Current developments are focused not only on weight reduction, but also on improving the ease of opening, welding speed and quality, the can image, and the possibilities for decoration. The French now have available stackable, imaged food cans, with ring pull lids, eliminating the need for tin openers, although these are limited at present to the top end of the market. In the can production process, the latest high speed resistance welding works at up to 750 cans per minute, depending on the can size, and produces a highly consistent welded product. Computer Modelling Computer modelling techniques are being employed in the design of new cans, with a particular design possible for each particular application. The modelling can also produce the requirements for a new steel to be used in a certain application or design of packaging, allowing British Steel Tinplate, amongst others, to eliminate costly trial processes in producing a new can. The design of the dome, the opening system, and the necking process are all incorporated, giving the can maker a complete solution on screen before working with the steel. Pre-Coated Steels New pre-coated steels are being introduced in a number of packaging applications, to eliminate the need for lacquering after drawing. Ferrolite is one such material, being a steel coated with PET or polypropylene on one or both sides to protect the can interior and allow ease of external decoration, whilst Tulc cans use a similar material commercially in Japan. The use of these materials is expected to increase in the next few years. Summary The public perception of the can as a low-tech packaging device clearly needs revising. Vast savings have been achieved in energy, materials, and cost by the developments described above, and the ‘Ultimate Can’ of the project title is almost with us - a sophisticated, environmentally-friendly, precision engineered device to carry our food and drinks into the 21st century. |