Existing proximity sensors tend to rely on magnetic induction, reluctance or Hall effect devices for their performance characteristics, which in applications such as automotive ignition sensors can lead to poor running performance. Now, researchers at Oxford University’s Physics Department have developed an extraordinarily versatile proximity sensor that uses RF signals to detect the motion of a wide variety of metals and non-metals and has a wealth of potential applications from position or speed sensors in automotive suspension, gearbox and engine management systems, to detecting changes in the flow of inhomogeneous liquids, such as blood/saline, water-in-oil or oil-in-water mixtures. How the RF Sensors Differ from More Conventional Sensors ‘Most types of proximity sensor used for position sensing in the automotive industry use either optical or magnetic fields for operation,’ explains Dr Robert Adams, Physical Science Project Manager for Isis Innovation Limited, Oxford University’s technology transfer company. ‘Over time wear products such as dust, grease or dirt can cover the sensor, degrading its performance. If wear products cover part of our sensor they should not degrade its performance as they will produce a static background signal, which will be ignored by the electronics - it is only changing parameters that cause a signal.’ Components of the RF Sensor The RF position sensor consists of three principal parts encapsulated into a single compact unit - a coil shaped radio frequency antenna, an RF oscillator circuit, which drives the antenna, and a monitoring circuit, which determines whether a change has occurred in the behaviour of the coupled antenna and oscillator. A prototype of the sensor is shown in figure 1. While the sensor did not require the use of any special materials for its initial patent application, Adams points out that if it was used purely to measure magnetic field strength in an area, then a piece of magnetic material would need to be placed adjacent to the coil. ‘The only other instance in which special materials may be required is if the sensor is used to measure motion in extremely hot environments, i.e. 1,000°C, in which case the RF antenna coil is mounted remotely to the electronics and the coil is made of some high-temperature tolerant metal,’ he says. 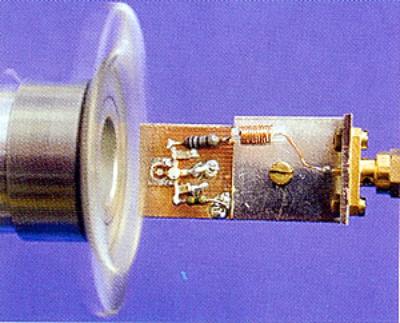 | Figure 1. Close up of the RF sensor being used to detect a metal toothed wheel. | How the RF Sensors Work The sensor functions by detecting a change in the electromagnetic properties of the volume forming its ‘sensitive region’, which is located just outside the mouth of the coil and forms an approximate cube with sides of a similar diameter to the antenna coil. An object moving through the sensitive region, or the presence of a different material can cause such a change. ‘Because the sensor uses an electromagnetic field rather than either a purely magnetic or electric field,’ explains Adams, ‘it is sensitive to both magnetic and electric properties of materials intruding into the sensitive volume at the same time, for example, the teeth of a rotating metallic cog moving through the sensitive region.’ Other examples include homogeneous liquid flowing within a pipe located in the sensitive region, which contains small bubbles or pieces of solid debris carried along in the flow. As the liquid passes through the sensor a signal is produced that is proportional to the size or mass of the debris and for which the signal type is characteristic of that particular material. Application of the RF Sensor In Materials Recycling The characteristics of the electronic signal output from the sensor can be used to discriminate between different types of materials depending on their magnetic or electric permittivity characteristics. ‘In plastics recycling, for example, the sensor could be used to discriminate between different types of plastics from their electrical properties,’ says Adams. ‘Similar things could be done for metals.’ Advantages of the RF Sensor The sensor has advantages over competing devices in that: • It requires no additional components such as magnets, coils or magnetic circuits • It can be very small and the electronics may be accommodated on 100μm square of silicon wafer • It has a high signal-to-noise ratio, which can be maximised by optimising the sensor design for a particular application • Unlike inductive sensors, its output is speed independent. Summary A prototype has already been tested as an ignition-timing sensor on an internal combustion engine, and Isis Innovation has been approached by a couple of general bearings manufacturers, an aerospace maintenance equipment company and a couple of car component manufacturers with a view to evaluating the technology. ‘To date, no licences have resulted from our discussions,’ says Adams. ‘However, we are currently in the process of producing a few demonstration devices to showcase the capabilities of the technology to these potential licensees.’ |