The home appliance market is growing at a rapid pace around the world. Increased levels of disposable income in many countries have made this possible. Yet, the home appliance sector is also evolving; the extensive production of “smart” home appliances is radically on the increase.
This is great news for those in the plating industry, as the electronics that make these appliances “smart” need additional plated parts. In this article, Hitachi High Tech’s Matt Kreiner gives his views on this growth opportunity and the significance of ensuring correct quality control processes.
What Makes an Appliance Smart?
Typically, a smart appliance involves some sort of functionality that enables users to interact with it via their smartphone. The connection is usually made through the household Wi-Fi.
Examples of this include seeing where in the washing cycle the washing machine is, looking to see if there is any milk by using the in-built camera in the fridge, or checking whether the dishwasher is running out of salt.
Driven by appliance manufacturers implementing new features to stand out in a competitive market, the ability to regulate the appliance via a phone promises to deliver ease of use and convenience to the consumer. This has resulted in homeowners buying into this technology in multitudes.
It is predicted that by 2020, there will be more than 470 million smart home appliances set up around the world, with China making up for half. This is an enormous increase over the global one million units fitted in 2014.
As more manufacturers integrate smart technology into their products, the take-up is expected to increase continuously. For instance, the smart washing machine market is forecast to see 22% growth over the next five years, with 131 million installed globally by 2020.
At the center of the technology is the ability to link the appliance to the household Wi-Fi connection. This depends on extra communication electronics integrated into the appliance. These electronics will require supported plated components, such as pins, harnesses, mounts, and connectors. This is increasing the already growing demand for plated connectors. In effect, by 2023, the worldwide connector market is projected to reach an estimated $80.4 billion.
These connectors and other supporting components are all usually plated with nickel, gold, silver, or tin, using immersion or electroless plating methods. These are proven methods within the plating sector, which means that plating suppliers can make the most of the increase in connector demand, without having to spend on adopting new plating technologies.
.png)
Improved Accuracy and Faster Throughput with XRF
The industry standard method for measuring plating thickness of deposited metal layers is XRF analysis. It is critical to properly measure the thickness of the plating — too little and the underlying material is in danger of corrosion, or if the plating is cosmetic, it will look unappealing; too much and the process becomes very costly.
The setup, detector type, calibration, and software of your XRF equipment all play a vital role in the accuracy and speed of your measurement process. One of the simplest ways to enhance both accuracy and speed is to use custom-made fixtures. This can make sure you place the sample in precisely the right position consistently, and on-screen guidelines make it stress-free for the operator to line up the sample. This makes setting up and lining up parts for thickness measurements quick and easy.
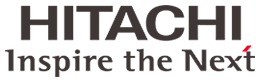
This information has been sourced, reviewed and adapted from materials provided by Hitachi High-Tech Analytical Science.
For more information on this source, please visit Hitachi High-Tech Analytical Science.