Magnesium Fluoride (MgF2) possesses outstanding transmission in the UV domain, and is regularly utilized in electro-optics research, development and production. In this respect, MgF2 is typically employed in the production of windows with high transmittance, extending from less than 150 nm across the visible spectrum. This material is quite supple and somewhat fragile, and therefore polishing and handling are reasonably sensitive procedures. Submitted for precision thickness dimpling are 5mm circular diameter MgF2 windows.
The quality of a UV window is exceedingly important. It must possess a highly polished surface finish so as not to disturb the optical structure and generate light scattering artifacts. In addition, around the outer perimeter of the window, flat edges of 0.1 to 0.2 mm are needed; these are integrated to create a vacuum seal when paired with the glass tubing lamp body. The exact target thicknesses required are 200 microns, 80 microns and 20 microns.
Materials
The equipment and consumable items which were utilized during the preparation are as follows:
Equipment |
Description |
Model 84000 PELCO® Dimpler™ : with 3i Dimple tool, 4iT dimple polish tool 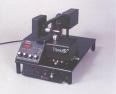 |
The model 84000 PELCO® Dimpler™ is a precision electro-mechanical lapping and polishing instrument. With the ability to continuously monitor and control dimpling parameters. The only system existing in today’s market to offer features such as electronic damping, measuring, force, fine balance adjustments. |
PELCO® Quickstick 135 mounting wax 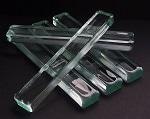 |
This high hardness and acetone solubility make this wax the ideal choice for abrasive suspension lapping & polishing |
6 um, 3 um, 1 um, 0.25 m, 0.1 um Polycrystalline diamond suspension. 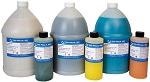 |
Permanent polycrystalline diamond suspension offering best finish and polishing times versus alum oxides. |
Model 145-Lapping Fixture Model 180-Lapping Tray 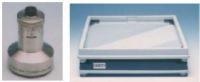 |
The Model 145 is a small versatile hand lapping fixture for sample up to 0.5” diameter, used in conjunction with the Model 180 stackable lapping tray for securing abrasive paper or films onto a 12’’ flat glass square. The area under the glass plate serves as a reservoir to contain polishing fluids if used. |
0.5 um Diamond abrasive film 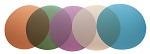 |
Used to give window samples flat edge with good finish w/o compromising hand-polishing time |
Method
1. MgF2 windows, given ID numbers 1, 2, 3 and 4, were separately placed onto a sapphire flat with PELCO® Quickstick 135 mounting wax. The flat and window were then inserted into the specimen platen assembly, and the dimpling process could subsequently commence.
2. Sample processing was undertaken utilizing the model 84000 PELCO® Dimpler™ tool. The table below illuminates the fundamental procedure:
Step |
Dimple Tool |
Abrasive |
Time (approx) |
Comments |
1 |
3i dimple tool |
6 um MicroDi |
55 minutes |
Remove stock material |
2 |
3i dimple tool |
3 um MicroDi |
15-20 minutes |
Removal of 6 um scratches |
3 |
3i dimple tool |
1 um MicroDi |
5 –10 minutes |
Removal of 3 um scratches |
4 |
4iT dimple polish tool |
1 um MicroDi |
30-60 minutes |
For near optical finish |
5 |
4iT dimple polish tool |
0.25 MicroDi |
5-10 minutes |
Optical finish |
6 |
4iT dimple polish tool |
0.10 MicroDi |
5-10 minutes |
Optical finish |
3. To ensure that a flat edge was achieved around the perimeter of the window, each sample was placed onto the Model 145 Lapping Fixture. Hand lapping with the Model 180 lapping tray utilizing the 0.5 μm Diamond film permits economical processing in less than five minutes.
Results
Three of the twelve sample windows were polished to the desired thickness. Window ID 3 was subjected to process made changes as a means of enhancing process time. Eight samples (Window ID’s 5-12) were retained for additional processing, conditional on the final test results from the window supplier. Following these, the process can be agreed or altered to fit correspondingly.
Window |
ID Status |
Thickness |
Comments |
1 |
Good |
200 um |
|
2 |
Good |
80 um |
|
3 |
To Thin |
-0- |
|
4 |
Good |
20 um |
|
Conclusion
The model 84000 PELCO® Dimpler™ enabled the Magnesium Fluoride UV windows to be processed to thicknesses with optical quality surface finishes. Final testing should be undertaken by suppliers, so that South Bay Technology can then conclude process parameters and accomplish a material processing solution in the impending future.

This information has been sourced, reviewed and adapted from materials provided by Ted Pella, Inc.
For more information on this source, please visit Ted Pella, Inc.