It is almost impossible to acquire total identification of most polymer products. Though this is not normally required in the majority of cases; what is normally required is the identification, or separation, of a number of molding materials whose identity has been lost, or some clue as to the kind of material employed to create a component. It is justified to use simple tests in such cases.
Simple Tests
Simple tests are made up of an initial examination of density, melting point, and behavior during heating. The tests have to be carried out in that order; for instance, if the density value is high at more than 1.7 gcm3 (SG greater than 1.7), it is a possibility the material is a fluoropolymer, so heating tests must not be undertaken because of the danger posed by the fumes which would be released.
Only a minimal amount of any sample should be utilized for any heating test for that exact reason. The use of a fume cupboard is also recommended.
Density
A material’s absolute density is not needed in most instances; just an approximate value. This is easily achieved by finding out if the material sinks or swims in a limited scope of liquids. These could include saturated magnesium chloride and water; the former.
Preliminary Examination
The component, or material, must be examined for transparency, color, its resistance to cutting, method of manufacture and so on. The reason for this is, for example, such an examination can give a strong hint as to the sort of material which has been utilized to manufacture a certain component. A component’s dimensions and weight should also be considered, plus any ejection marks, flash lines, etc.
The density will normally be higher if the material is filled, than if the material is unfilled because many of the most common inorganic fillers have a relatively high density. The inorganic filler content can be estimated easily if a weighed sample of the material is burnt completely.
Melting Point
Usually a very accurate value is not required here. To attain an estimated value, the simplest technique is to heat a small sample of the material on a metal hot plate and record the rise in temperature plus the temperature of the hot plate just under the plastics material. It is recommended to set a heating rate of around 50 °C/hour, or 90 °F/hour.
An amorphous, thermoplastic material does not possess a sharp melting point, but a semicrystalline, thermoplastic material usually has a sharp melting point. A glass rod is helpful to prod or move a sample during heating.
Behavior on Heating
Thermoplastics soften during heating, whilst thermosetting plastics (thermosets) do not – when the temperature hits a certain point they decompose. An amorphous, thermoplastic material will soften over a broader temperature range in comparison to a semi-crystalline, thermoplastic material; these have sharp melting points. This test can be combined with the first test.
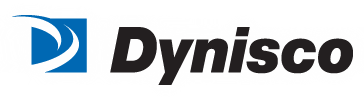
This information has been sourced, reviewed and adapted from materials provided by Dynisco.
For more information on this source, please visit Dynisco.