For more than 60 years pressure sensors produced by Dynisco have been used globally in many different applications. As the holder of the first patent for an extrusion melt pressure sensor, Dynisco has been there from the start and has continued to work with customers to hold their position as industry leaders in the face of the constantly evolving needs of the plastics industry.
Choosing Diaphragm Material for Dynisco Pressure Sensors
The choice of diaphragm material for a Dynisco pressure sensor depends on the application that the sensor will be used in. The first question to ask is if the sensor comes into contact with a pure material or a blend of different materials. Once this has been established the properties of the materials that the sensor comes into contact with should be evaluated in terms of their polymer classifications.
Polymers can be broadly grouped into elastomers, thermoplastics, thermoplastic elastomers and thermosets; with the different polymer families within these groups being polyesters, polyolefins, amides and urethanes.
The processing of elastomer and thermoplastic polymers involves steps such as injecting molding, extrusion and compression molding. All of these steps must use pressure sensors as a means of controlling the process.
Pressure sensors from Dynisco are produced to be resistant to the conditions used in these processes and to accurately and reliably provide the pressure readings required.
More important questions to ask are what temperatures do the processes run at and is the material that the sensor will come into contact with corrosive or abrasive.
For example, if the application involves a material such as polypropylene it is recommended that a standard diaphragm option, Dymax®, is used. This standard is formed from coated stainless steel (15-5PH) which has good abrasion resistance and can be used in most extrusion applications.
If the application involves a material which can adhere to the standard diaphragm, for example an elastomer such as TPE, the diaphragm should be coated in titanium nitride (TiN) as this offers adhesion resistance and also reduces the chance of diaphragm deformation.
Applications which involve corrosive materials, e.g. those that use fluoropolymers (PTFE or FEP), should use an Inconel or a Hastelloy coating to ensure that the diaphragm is not damaged by oxidation.
Coatings and Materials Available for Dynisco Diaphragms
.jpg)
The different coatings and materials available for Dynisco diaphragms are:
- Hastelloy – Highly corrosion resistant but not recommended for extended use in high temperature environments
- 15-5 PH Stainless steel with Dymax ® coating – The standard material for most sensors, provides abrasion resistance and toughness
- Inconel 718 – Improved abrasion and corrosion resistance. Suggested to use for temperatures at and above 750 °F.
- Borofuse – The toughest abrasion resistance coating available, can only be applied on Inconel
- Dymax® - Tough surface coating that provides protection from abrasion
- Titanium Nitride – Provides resistance to both adhesion and abrasion, can be applied on the majority of diaphragm materials
- Titanium Aluminum Nitride – Provides even better resistance to adhesion and abrasion, comes as standard on Dynisco Echo sensors (Inconel diaphragm material)
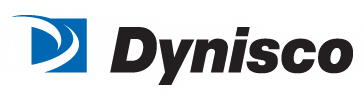
This information has been sourced, reviewed and adapted from materials provided by Dynisco.
For more information on this source, please visit Dynisco.