A sensor is any device that can be used to measure a physical value. Sensors do this by converting a physical stimulus into an output signal that can be recorded by instrumentation and observed by a user. Pressure sensors are used by a wide range of different industries where they allow users to monitor and control different processes, and help ensure processing occurs safely.
Calibration of Pressure Sensors
This article explores the calibration of a melt pressure transducer, a type of sensor used in injection molding and plastic extrusion. The output of the sensor must be calibrated to work alongside instrumentation to ensure that pressure readings are taken correctly and at an adequate precision.
Calibration should take place when the transducer is in its resting state, i.e. not experiencing any pressure, and at its temperature of operation, to account for any temperature effects on measurement.
Pressure Transducers by Dynisco
All of the pressure transducers produced by Dynisco come with a rating which describes the temperature effect experienced at zero. This rating can differ depending on the fill media in the capillary of the transducer.
The physical properties of the capillary’s fill media changes where the signal’s zero level is, and this needs to be taken into account when determining the instrument’s range and what compensation must be carried out. This compensation is similar to running the ‘TARE’ function on scales, where the temperature effect is the same as the package of the product being weighed.
The established temperature effect for the 3 different liquid fill options are:
- Oil = 36 psi/ 100 °F or 65psi/100 °C
- Hg = 15 psi/ 100 °F or 27 psi/ 100 °C
- NaK = 30 psi/ 100 °F or 54psi/ 100 °C
From these values it can be seen that the system must be configured via calibration for the signal input to be read as zero.
Example: Process temperature = 400°F, Hg type sensor with a signal output of 60 psi @ zero pressure*
*Depending on the full scale pressure range of the transducer, this off set would be in addition to Dynisco’s normal combined error specification, so a 10,000 psi range that has a .5% combined error (+/- 50 psi) would actually appear to have an offset of 110psi or more at any time.
It is crucial to note that when carrying out calibration the signal output is not changed in any way with the verification that output sits within the tolerance of the model spec.
Dynisco Pressure Sensors Make Calibration as Simple as Possible
Sensors from Dynisco are designed to make calibration as simple as possible. Their sensors can be used to test the maximum and minimum limits of the output signal in just a few key strokes.
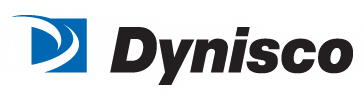
This information has been sourced, reviewed and adapted from materials provided by Dynisco.
For more information on this source, please visit Dynisco.