All plastics contain one or more polymers, in addition to additives. Usually, polymers are not sold without some form of additive compounded into them. In the thermoplastics industry, it is commonly understood that the materials used also have small amounts of additives in them. An example of these thermoplastics are heat stabilizers and lubricants, which cannot be commercially used when additives have not been added.
It is possible that polymer properties used in plastic products can be changed significantly by the processing conditions used and by adding additives. Varying formulas of basic materials are accessible with additives and they provide, for example, enhanced heat resistance, or weatherability and some formulations even offer better impact strength.
On the other hand, in cases where a greater modulus, flexural strength and heat distortion temperature is required, other formulas, that contain fillers, are used. In addition to this, processing and performance modifiers, like antistatic and nucleating agents, may be added. Often, the additives form part of a color masterbatch.
Masterbatches
Injection molding machines are types of processing equipment, and are often fed with a combination of a plastic material plus a masterbatch. A masterbatch consists of a mixture of one or more additives that is added to a base polymer material. There are benefits to using this mixture, an important one being that it frequently produces large cost savings because a compounding step can be removed.
In general, the only use for a masterbatch is to color a finished product. However, they may also comprise of other additives as well, sometimes leading to issues. The issues that occur most often are related to color shade differences between different machines and separation of the masterbatch components from the plastic in the hopper. In turn, this may lead to inconstant properties in the molded parts.
Materials Modification
The term ‘materials modification’ often refers to the adding of greater amounts of additives. An example of these additives include elastomers, flame-retardants and fillers.
Fillers and Reinforcements
In order to obtain a desirable combination of properties, materials modification, such as with fibers or with fillers, is largely used with engineering thermoplastics. For instance, it is commonly known that the use of fibrous fillers, like glass fiber, enhances the modulus. Although cost saving is beneficial in most cases, these modifications are rarely produced in order to save money because of similar prices between a molding made from a filled compound, and one made from the unfilled plastic material. This is the case because of the high density of most fillers and large compounding costs.
Utilizing fillers means there is potential to lift a plastic material from one category to another, like the commodity resin polypropylene, which can be changed into an engineering plastic through enhancing materials.
Impact Modification - Elastomer Addition
Strictly speaking an elastomer or rubber that imparts added toughness when used with a thermoplastic material is called an impact modifier. Said additives are largely used in engineering thermoplastics for applications where high impact strength is required (for example, automotive bumpers).
Additionally, commodity resins’ impact strength can also be upgraded through the addition of impact modifiers. If rubber is added to styrene, prior to the mixture being polymerized, a thermoplastic material named high impact polystyrene (HIPS or, TPS, or, IPS) is created. Rubbers are often added to other materials, like polypropylene (PP), with the aim of improving the low temperature impact strength.
To achieve this, a specific material is required that can be processed like a thermoplastic yet additionally, has several of the properties of a cross-linked material. This makes polymer alloying and thermoplastic elastomers an attractive possibility.
In order to make such thermoplastic materials, cross-linked rubber particles can be dispersed in a thermoplastic matrix. Acrylonitrile Butadiene Styrene (ABS) copolymer is just one example of this, in which butadiene rubber is used to enhance the impact properties to SAN copolymer. Thus, producing a commonly used plastic material. In addition, methacrylate-butadiene-styrene polymers (MBS) can be added to such UPVC bottles to improve impact strength.
When utilized at approximately 10% addition, these thermoplastic rubber materials still produce transparent bottles. However, because they are comparatively expensive, alternative cheaper solutions are now commonly used.
Flame Retardants
Most polymers will burn because they are based on carbon and it is a natural reaction for a carbon-based material to react (burn) with atmospheric oxygen and to form carbon monoxide and carbon dioxide. On the other hand, halogen atoms, like bromine and chlorine, create compounds that are naturally fire or flame retarding. A noteworthy example is PVC, in which the halogen atom is “built-in” the plastic material molecular structure.
In comparison, other plastics require the halogen to be added in the form of compounds like tribromotoluene. To improve efficiency further, these compounds can be improved by adding antimony trioxide.
One of the drawbacks, however, is that the use of halogens can emit toxic smoke and fumes. This leads to other flame-retardants to be favored, such as aluminum trihydrate. Unfortunately, large amounts of this material are required to make a difference, which can alter the properties of the plastic material, like its flow properties. Processing issues may also arise because aluminum trihydrate decomposes at processing temperatures. As a result, some silicones and phosphorous-based compounds are becoming more widely used as flame-retardants.
Plasticizers
Plasticizers, which are usually liquids, were first added to plastic materials, such as cellulosics and PVC, in order to allow them to be processed at temperatures below that at which they thermally degrade. Almost all commercial plasticizers are phthalate compound which contain dioctyl phthalate (DOP) and di-iso-octyl phthalate (DIOP).
Adding these materials to PVC produces plasticized PVC (PPVC). A benefit of this material is that it flows easier compared to unplasticized material (UPVC) and is softer with more flexibility. “Primary plasticizer” and “secondary plasticizer” can be used. “Primary plasticizer” specifies that a compound is more well-matched with the basic plastic material compared to a “secondary plasticizer.”
Softeners and Extenders
The rubber industry often uses the term “softener” to describe products like hydrocarbon oils, which are used as additives for hydrocarbon rubbers/elastomers. They create soft compounds, which can flow with relative ease. “Liquid fillers” is the term used to refer to extenders, which are commonly associated with PPVC. Their use decreases compound costs and as well as this, the chlorinated waxes utilized in this application can act as flame-retardants.
Anti-Aging Additives
Anti-aging additives are commonly used with polymeric materials because heat and light will often change their properties during normal use, or during processing. Oxidation, ozone attack, dehydrochlorination and ultraviolet (UV) attack are all chemical reactions that occur within a material, or on its surface, and are triggered by heat and light. The type of chemical attack that occurs is dependent on the type of polymer and the specific circumstance it is in.
Polyolefins (PO) are readily degraded by oxidation, thus antioxidants are frequently used in polyethylene (PE) and polypropylene (PP). Luckily, PVC degrades faster through dehydrochlorination and additives, which limits this type of attack, and are more commonly used in PVC compounds and ultra-violet (UV) attack is seen to be most common with several polymeric materials. Due to this, UV stabilizers are often found in products that are to be used outdoors and thus, exposed to sunlight. Aging by ozone is odd to the rubbery class of materials, and is reduced through the controlled use of anti-ozonants.
Lubricants
Lubricants are often added to polymers. The reason behind this is to prevent the polymer from adhering to processing equipment, or to allow a better flow of the polymer compound. An example of a lubricant used is stearic acid and it is added to PVC in order to stop the compound from sticking to the processing equipment. This kind of lubricant is named an “external lubricant” because it rises to the surface of the molten polymer.
On the other hand, an “internal lubricant” is primarily used for flow increase. For example, glyceryl monostearate, commonly used with UPVC. Several plastics materials have lubricants added to them to aid with friction reduction while in use. For instance, the addition of 2% graphite will reduce the friction between two molded gears and silicone oils may also be used for the same goal.
Colorants
Coloring techniques involve the use of a coloring system which is dispersed throughout a polymer and is used as the technique for most plastic components. During this process, it is possible to color only the skin with the result of saving on colorant and compounding costs. For example, this can be done through sandwich molding and extrusion.
In general, colorants are divided into two major types: dyes and pigments. Dyes are soluble, generally organic, coloring systems that produce transparent colors. Pigments are dispersed insoluble solids that produce opaque colors. Pigments are the most widely used. The most widely used colors are black (carbon black) and white (TiO2).
Blowing Agents
Several polymeric products are cellular materials occupied with gas cells. A gas (usually nitrogen) can be added in two ways; during processing, or through a chemical compound, also known as a blowing agent, in order to produce the gas when needed. A largely used class of blowing agents is the azo compounds, which are organic materials that have the ability to be structured, so they can decompose over a relatively narrow temperature range at the melt processing temperatures.
Cross-Linking Additives
A number of polymers can be cross-linked, meaning they are cured, vulcanized or set, and after shaping, which occurs during processing, can result in either a vulcanized rubber (an elastomer) or a thermosetting plastic material. Two renowned cross-linking systems are sulfur, which is used with diene rubbers, and peroxides which are used with specific rubbers and polyolefins. Accelerators speed up the cross-linking reaction, and are often related to cross-linking systems. In turn, an accelerator may only function efficiently in the presence of an activator.
Degradants
Litter is often seen to be a problem when producing plastic because once a plastic part has fulfilled the function it was needed for, it frequently becomes a nuisance, and the once-valuable constituent is thrown away. This issue is most severe for plastic materials used in packaging. In order to combat this issue, the plastic material is subject to decomposition, or degradation through introducing a filler into the plastic material, for example, starch.
Another way to help this issue is to use a biodegradable plastic material such as polyhydroxybutyrate (PHB). This can be used either independently, or in combination with other plastics. PHB is created via a bacterial action on glucose and is a semi-crystalline, thermoplastic material. It is somewhat similar to polypropylene (PP).
Reclaimed Material
The most frequently used additive combined with thermoplastic materials, is reclaimed (or recycled) material. This additive can be added to decrease component costs. It is imperative that this additive (as with any additive) is added at a steady, pre-selected ratio to ensure the flow properties of the blend remain constant. Additionally, it should be noted that the reclaimed material needs to be clean, dry and of even particle size.
Good Dispersion
To gain successful results from additives they have to be very well dispersed within the basic polymeric material. This is why melt mixing is very important to the polymer industry. Such melt mixing is carried out at relatively low temperatures to keep the polymer viscosity at a high value and so increase the shear input, which improves dispersion.
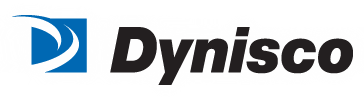
This information has been sourced, reviewed and adapted from materials provided by Dynisco.
For more information on this source, please visit Dynisco.