Extrusion and injection molding are vital conversion methods used by the thermoplastics processing industry. When extrusion or injection molding is being utilized, there are specific factors that should be deliberated prior to a thermoplastics material being processed.
These factors are inclusive of the hygroscopic behavior of the material (whether it picks up water), the granule characteristics, the thermal properties (such as heat transfer and the thermal stability), the flow properties, crystallization behavior, shrinkage, and molecular orientation.
Hygroscopic Behavior
When a polymer compound has water in it, or alternatively another material with a low boiling point, the heat needed for processing can raise its temperature higher than the boiling point. Noticeable bubbles then accumulate within the thermoplastic material when the pressure decreases, such as when it appears from the die of an extruder.
In general, the higher the processing temperatures, the smaller the amount of water that can be endured. This is a result of the higher temperatures that can create an increased volume of steam from the same quantity of water. Most of the time, commodity thermoplastics are not in danger of water-related problems compared to the engineering thermoplastics. For instance, PET and Nylon are materials that absorb water (they are hygroscopic) and must be thoroughly dried before processing. Additives are also a risk because they contain excessive water and this may be introduced into the system via the additives.
Characteristics of Granules
Several processes like extrusion, injection molding and blow molding often use material in granular form as their feed. Sometimes, the material is available in more than one feed form. In this case, where a mixture of feed forms is used, feeding problems can be encountered.
Undoubtedly, spherical granules (of approximately 3 mm (0.125 in) diameter) provide the highest efficiency and fine powder is most commonly the worst. If materials are regranulated, a range of particle sizes can be found leading to less efficiency.
Comparatively, cube cut and lace cut granules are much better, with lace cut leading the pack. These granules are made by chopping strands with a circular cross-section. Due to the feeding differences of the varying granulates, the machines must be fed with a steady raw material mix, particularly in the case of masterbatch mixes.
Thermal Properties and Heat Input
For a successful melting process, thermoplastic materials need large heat inputs in order to increase their temperatures. In order to bring them up to processing temperatures, the amount of heat energy that is needed for each material varies significantly.
There is no simple way to explain these heat differences, and it is not simply because of the differing processing temperature, but it is also due to the fact that different plastic materials have different specific heats. For example, the amount of heat that is required to increase the temperature of a specific weight of a material by 1 ˚C or F. Temperatures can be raised by a fixed number of degrees in different materials.
For instance, during the method of melt processing a semi-crystalline, thermoplastic material heat must be provided in order to melt the crystal structures. In comparison, this extra heat input is not necessary in an amorphous resin case. Both types of material will, however, require a large amount of heat to be put into the material quickly.
This results in issues because plastics are poor conductors of heat and limited thermal stability has been observed when employed at the processing temperatures. Due to plastic materials being poor thermal conductors, when the large amount of heat required to solidify a part is removed, it poses severe issues, especially if high-speed production is to be sustained. Table 3 gives information on the heat removal figures for several different thermoplastic materials.
Thermal Stability
In terms of their thermal stability, thermoplastic materials differ largely. An example material is UPVC. This material is extremely unstable even when it has been stabilized, and it is only possible to hold it at processing temperatures (175 oC/347 oF) for a few minutes. (Unstabilized PVC will present some degradation in boiling water.) In contrast, polysulfones require melt temperatures around 400 oC/752 oF to be stable.
The thermal stability of a material is determined by several factors; the temperature, the residence time at that temperature, the atmosphere surrounding the material (oxygen or inert) and the materials that are in contact with the plastics material. For instance, copper has been seen to cause rapid decomposition, or degradation of polypropylene (PP).
Consequently, one should refrain from using copper cleaning pads to clean rheological equipment used to test this material. Generally, the decomposition products resulting from plastics should be seen as being possibly harmful and any gases that are emitted should be properly ventilated.
Flow Properties
The processing temperatures used for thermoplastics are often limited to moderately low values because of the thermal stability issues. Subsequently, melt viscosities of the material are usually high and process melt viscosities are not uniform. These are different from one material to another, and from one grade to another of the same material. Although these differences may be associated to intrinsic differences in the nature of the polymers, affects may also be attributed to temperature and by molecular weight.
Generally, viscosity reduces when there is an increase in temperature and as the molecular weight is decreased. Minor variations of temperature, molecular weight, and molecular weight distribution can lead to huge differences to show up in melt viscosity. In turn, output and quality in both extrusion and injection molding are affected. Therefore, tight control over both the processing conditions, and the material used in the machine, must be adhered to.
This explains the extended interest in flow testing of thermoplastic materials. (On another note, it should also be emphasized that because the viscosity decreases with an increase in output rate, through a given die, the energy used per unit output, tends to decrease as the extrusion rate goes up).
Thermal Properties and Cooling
In order to raise their temperatures to those needed for melt processing, thermoplastic materials require large heat inputs. These materials are decent thermal insulators, and therefore the absence of a large amount of heat poses serious issues for fast production. Table 3 presents heat removal data for different thermoplastic materials. Changes in the cooling rate may have a distinct effect on the crystalline morphology of the product, and on aspects like molecular orientation and shrinkage.
Crystallization and Shrinkage
Commonly, a shrinking process occurs in all polymeric products that are cooled from processing temperatures. The shrinkage of an amorphous thermoplastic material, like polystyrene (PS), is a smaller amount compared to that for a semi-crystalline thermoplastic, like high-density polyethylene (HDPE). (For PS, the shrinkage amount may be 0.6%, while for HDPE it may reach 4%). This is due to polymer molecules crystallizing, in which they usually pack more proficiently compared to when they do in the disorganized amorphous state.
With the presentation of thick-sectioned moldings and extrusions, cooling rates will vary from the outside edges to the center. As a result, there are differences in the degree of crystallinity throughout, which elucidates why a shrinkage range is always cited for each material. This range is always higher for a semi-crystalline thermoplastic material than for an amorphous one. For example, the shrinkage of PS is listed as 0.02 to 0.08%, while that of HDPE is 1.5 to 4%.
Orientation of Molecules
Polymer melts are completely distorted during melt processing. After heating, the hot material is rapidly cooled in order to achieve the high output rates that are demanded of it. The shearing processes result in the molecules taking up a deformed, or oriented, shape and the rapid cooling results in this deformed shape being frozen-in the product. This orientation explains why the product has different properties in different directions, and is known as anisotropy.
This orientation is undesirable in many cases, but, can sometimes be introduced or enhanced to enhance the properties of a product. Deliberately orienting extrudates is performed in the production of fibrillated tape, many types of fibers, and in the extrusion blow molding of bottles.
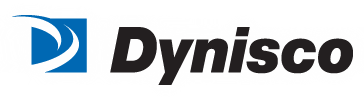
This information has been sourced, reviewed and adapted from materials provided by Dynisco.
For more information on this source, please visit Dynisco.