
The things often prioritized in the list of requirements of design engineers from the precision automation sector are different from those of their colleagues in the instrumentation industry.
Dynamic performance and minimum dimensions may be trumped by robustness to achieve higher throughput, which goes hand in hand with 24/7 reliability. With regards to the integration of the precision positioning equipment with machine vision, lasers, dispensers, and so on, flexible network protocols like EtherCAT, which facilitates real-time multi-axis synchronized motion and the potential to synchronize with external events, are beneficial.
Advanced Precision Motorized Positioning Stages | High Throughput Laser Machining, Micro-Processing
XYZ configuration of two V-417 Linear Motor Stages in XY configuration and one L-412 ball-screw driven linear stage as the vertical axis.
Linear motors satisfy the high dynamics and low maintenance requirements, such as no friction, low inertia, and no wear. High accuracy and resolution are offered by a broad array of linear encoder options — for instance, absolute encoders add functional safety and save time since they make homing procedures obsolete and prevent run-away situations brought about by problems related to incremental encoder signal transmission. Advanced linear encoders have the ability to measure motion in increments smaller than 1 nm.
Ball-screws with powerful servomotors and the potential to run directly on 110/240-V AC servo drives are readily available for high-force applications. One of the greatest advantages is the fact that the ball screw rails can be lubricated by the end users without the need to dismantle the stages.
Linear Motors - How Does a 3-Phase Motor work in a Linear Motor Slide | Direct Drive Motors
3-Phase linear motor operating principle
In the laser industry, machine builders also require positioning stages such as these to provide improved resistance to ingress of debris and tolerance to hot particulates, so the linear stages are equipped with air purge connections, side sealing strips, and hard covers. Since it may be difficult to handle the size and mass of the manufactured parts, it is essential for the system components used to be robust, highly precise, stiff, and to provide reliable performance.
Other sought-after features are standard high flex cables, easy-to-handle and easy-to-adjust industrial motor connectors, and the potential for the ball screw to be lubricated by the end user without dismantling the stages.
Design engineers who look for ease of installation highly value the machined reference edge that comes with the new-generation linear stages for effortless placement and alignment on their machine base. Other benefits are the flexible motor cable exits and standard cable management options. The potential to offer error correction mapping, metrology data, or aligned XY or XYZ multi-axis combinations are other crucial requirements for the linear stage manufacturer.
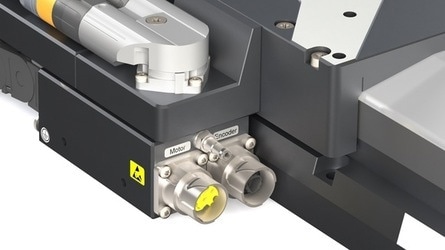
The new generation of linear stages (V-412, V-417, L-412, and L-417) is equipped with robust connectors according to industry standard. The new connectors are equipped with bayonet lock, which can be handled without the need to use tools and is also secured against inadvertent removal.
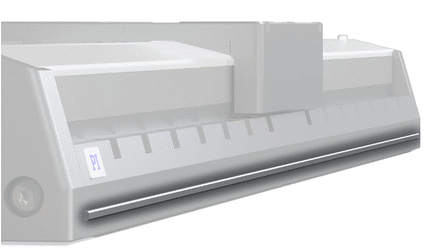
Machined reference edges facilitate the alignment of the linear stages on the machine base
EtherCAT Motion Controller Synchronized Motion, Position-Event-Generator (PEG)
With Machine Code (M-code) and Geometric Code (G-code) languages being the current standard for CNC machining and with CAD/CAM systems also generating G- and M-codes, it is advantageous to employ precision motion controllers that can understand commands in these languages, while exploring laser machining applications.
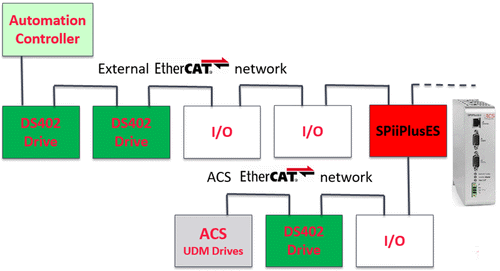
ACS motion subsystems can be integrated in third-party EtherCAT networks
EtherCAT®-based motion controllers, for example, the ACS distributed architecture, have the ability to easily handle G-code support and multi-axis synchronized motion applications. In addition, they offer Position-Event-Generator (PEG) functionality to achieve precise synchronization of laser control with motion and other specific motion-related commands intended for tool and offset compensation commands, as well as look-ahead algorithms used for processing the segments.
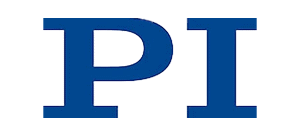
This information has been sourced, reviewed and adapted from materials provided by PI (Physik Instrumente) LP, Piezo Nano Positioning.
For more information on this source, please visit PI (Physik Instrumente) LP, Piezo Nano Positioning.