In the aircraft industry, the use of composites is becoming more and more popular; however, with rising build rates becoming the standard, composite part manufacturers are currently confronted with the challenge of finding new methods to produce higher part volumes.
.jpg)
Source: EVo plant, DLR Stade
At present, lay-up methods such as Automated Fiber Placement (AFP) are often used to develop monolithic designs. However, these AFP parts are usually very large and flat, for example, wing shells and fuselage shells. In order to develop more complicated geometric shapes, more creative solutions are needed.
Automatization is the Answer
With the aim of finding a new way for building complex composite parts both efficiently and rapidly, Evonik Industries (Germany) collaborated with the Deutsche ZentrumfürLuft- und Raumfahrt e. V. (DLR) and Composite Technology Center GmbH (CTC), both from Stade (Germany), and carried out a study which involved integrating a stiff core material for sandwich designs driven by high stiffness requirements, with a highly automated part pre-forming process.
The company’s project partners CTC and DLR Stade employed their very flexible EVo plant to show the concept by using a nose landing gear door as a demonstrator.
The outcomes of the study established the benefits of using ROHACELL® foam and automatization for constructing complex structures such as spoilers, flaps, gear doors, and others produced in high volumes. The advantages of reduced production times and cost reduction alone offer the reason for investing in automatization.
The Critical Process Steps
Cutting and Lay-Up
Typically, the technology for cutting and lay-up of fabrics uses a robot that accurately cuts the shapes. It subsequently lifts the fabric shape and positions it precisely in the tool for a quality control check.
Core Integration
The shapes department of Performance Foams of Evonik offers firm, machined cores that are easily lifted using a vacuum supported arm. The secure handling of the stable core by the robot ensures precise placement of the core above the fabric.
.jpg)
Robot lay-up process with ROHACELL® HERO
ROHACELL® HERO structural foam core offers several benefits to both the aerospace industry and for automatization:
- Low resin uptake for prepreg (AFP) and infusion method
- High-temperature resistance for pre-forming and one-shot curing
- Natural core stiffness in machining, transfer, and robot handling (set geometry data)
- High compressive strength for the fiber lay-up or the compaction at the pre-forming step
Conclusion
Automatization and sandwich design is an outstanding combination to decrease production steps and limit production costs.
By using the nose landing gear door as a demonstrator in the study, Evonik and its partners confirmed the successful combination of ROHACELL® foam core and automatization and also created a quality concept that guarantees a reliable process without additional quality NDI in between. Moreover, ROHACELL® HERO foam core was shown to be a highly stable material that can be moved easily and placed precisely throughout the production processes with the help of a robotic arm.
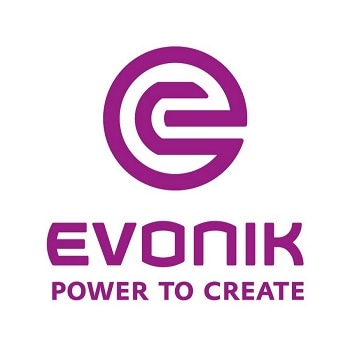
This information has been sourced, reviewed and adapted from materials provided by Evonik Industries - ROHACELL.
For more information on this source, please visit Evonik Industries - ROHACELL.