Fluoropolymers are a ubiquitous part of modern life – used in everything from food packaging to the non-stick coatings on kitchen pans. Fluoropolymers have been able to satisfy many different industrial needs, making them a highly popular material.
The carbon-fluoride bonding present in fluoropolymers gives them their characteristic properties – burn and chemical resistance. C-F bonds are very strong and the synthesis of different fluoropolymers of slightly different C-F bonding modes has helped create the huge and diverse fluoropolymer industry that now exists.
Homopolymers, created by the chaining of monomer units, and copolymers, created by the chaining of two different monomers, are just two examples of the different configurations that allow so many different fluoropolymers to be produced.
This diverse industry began with just one original fluoropolymer: polytetrafluoroethylene, or PTFE.
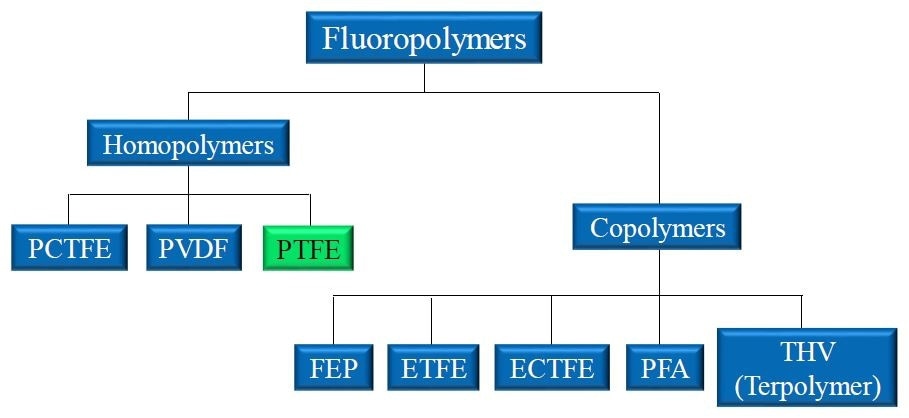
Figure 1. Landscape of popular fluoropolymers. Homopolymers like PTFE are produced through the polymerization of identical monomer units. Copolymers incorporate two or more monomers to produce the final polymer material.
PTFE was the result of years of a serendipitous development by chemists at DuPont, which was focused on the development of new refrigerants.1 The researchers had left low-temperature liquid tetrafluoroethylene (TFE) in a pressure vessel, and after some time left unattended, they found that the material had polymerized to form a waxy coating on the interior walls of the vessel. It was found that this coating was PTFE.
Whilst this finding occurred in 1938, PTFE was not commercialized until 1946. Before this PTFE was used in the Manhattan Project, America’s work on developing an atomic bomb, meaning the new material was kept secret. Provided most frequently as a polymer coating for metal surfaces TeflonTM PTFE (also known as just TeflonTM) is now most famous for its use as a non-stick coating for kitchen equipment.
PTFE synthesis involves the polymerization of monomers of TFE (Figure 2). The synthesis first involves the production of TFE using chloroform (CHCl3), hydrofluoric acid (HF) and calcium fluoride (CaF2), which are heated to temperatures exceeding 600 °C (1112 °F). The TFE gas produced by this reaction is then cooled to form a liquid which can then be purified.
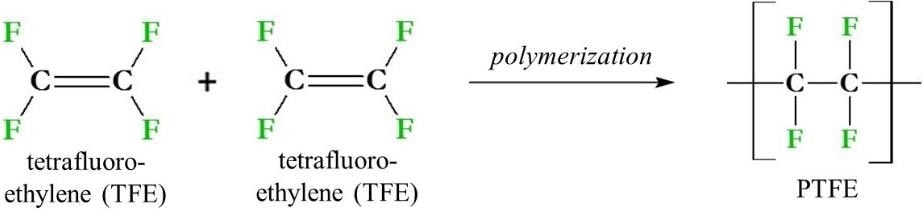
Figure 2. PTFE (polytetrafluoroethylene) and its immediate synthetic precursors. PTFE is made from the polymerization of tetrafluoroethylene (TFE) monomers via a radical reaction.
The liquid TFE is then polymerized via a radical mechanism, using an initiator such as peroxide (ROOR) to produce PTFE. This process can be adjusted in several different ways for the production of PTFE as a power, as an aqueous dispersion or as pellets.2
The powerful properties of PTFE when compared to other fluoropolymers means it is regarded as the best available. These properties come from PTFE exclusively having only C-F bonds, which are strong, short and inert, along it’s C-C polymer backbone (Figure 3), meaning the backbone is effectively protected by an outer layer of inert fluorine atoms.
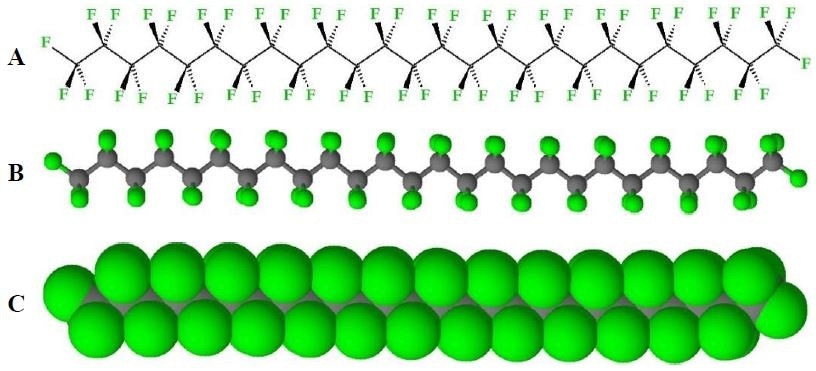
Figure 3. Structure of PTFE. A) Stereo bond-line drawing, B) ball-and-stick model, and C) space-filling model of PTFE (shown as zig-zag depiction). (Conformations of PTFE are variable during melt and amorphous phases).
This unique structure gives rise to the favorable properties that PTFE is known for – chemical inertness, low water absorption and an extremely low friction coefficient, which gives it a slippery feel.
Processing
The high viscosity of PTFE means that it is not melt-processable; however, methods such as paste extrusion, which involves blending powdered PTFE resin with a lubricant (e.g. a hydrocarbon), can be used for processing (Table 1). Blending methods can be used to produce a preform which can then be made into components such as tapes, tubing and sheets.
Table 1. PTFE processing suitability. Although PTFE is not melt-processable, it is amenable to several other production methods including paste extrusion and compression molding.
Processing Method |
Suitability |
Injection molding |
No |
Extrusion
(profiles, films, sheet, tubing, heat shrink tubing, and cable coating) |
Yes (as paste) |
Blow molding |
No |
Compression molding
(preform and sintering) |
Yes |
Impregnation and coating |
Yes (coating, as powder) |
It is also possible to produce PTFE components by molding or sintering it into a billet. The resulting billet can then be heated and ram-extruded for the production of pipes, roads or tubing. In addition, PTFE robs can then be calendared to make membranes and sheets, or molded components can be produced via compression molding.
The large variety of different ways that PTFE can be processed demonstrate that despite not being melt-processible PTFE components can still be easily produced for custom applications.
PTFE Properties
Physical and Mechanical
Many see PTFE as the ‘gold standard’ of fluoropolymers because of its range of excellent properties. As PTFE was already so desirable the following development of new fluoropolymers, such as PFA and FEP, were attempts to produce polymers with the same properties as PTFE but that could be melt-processed.
PTFE is the straight-chain perfluorinated polymer that has the highest level of fluorine saturation, and it is this that affords most of its beneficial properties (Tables 2 and 3). The C-C bonds along PTFE’s polymer backbone are strong and short and, when combined with the highly polymer C-F bonds extruding outwards, they result in a solid of high density and crystallinity.
Table 2. PTFE typical physical properties. PTFE’s physical properties place it in a small group of fluoropolymers whose traits are superior to almost all other polymer plastics. (Methods are ASTM test standards except where indicated by *).
Property |
ASTM |
Value (natural polymer) |
Appearance |
– |
Translucent |
Density (g/cm3) |
D792 |
2.17 |
Specific Gravity |
D792 |
2.16 |
Water Absorption (50% rh; %) |
D570/ISO 62-1 |
< 0.01 |
Refraction Index |
D542 |
1.35 |
Limiting Oxygen Index (LOI) |
D2863 |
95 |
Biocompatible |
*USP Class VI |
Yes |
Chemical Resistance |
– |
Excellent |
Sterilization |
– |
ETO, autoclave |
Table 3. Typical PTFE mechanical properties. While comparatively mechanically weak, PTFE exhibits very low coefficient of friction and very high hardness.
Property |
ASTM |
Value (natural polymer) |
Tensile Strength (MPa) |
D638 |
20 – 35 |
Elongation at Break (%) |
D638 |
200 – 550 |
Modulus Of Elasticity (GPa) |
D638 |
0.39 – 0.60 |
Flexural Modulus (GPa) |
D790 |
0.49 – 0.59 |
Flexural Strength (GPa) |
D790 |
No break |
Hardness (Shore D) |
D2240 |
50 – 65 |
Impact Strength (23 °C; J/m) |
D256 |
186 |
Coefficient of Friction |
D1894 |
0.02 – 0.20 |
The inert and hydrophobic fluorine atoms effectively coat the backbone; making PTFE chemically unreactive towards a huge range of chemicals and make it biocompatible to a medical grade of Class VI.
Although there are some limitations in the mechanical behavior of PTFE it tends to be better than all other fluoropolymers in terms of various different beneficial characteristics.
The mechanical properties of PTFE are related to its crystallinity; which is very high because PTFE molecules have an extremely homogenous, linear structure. Freshly produced PTFE tends to have a crystallinity above 90%, significantly more than the 40-50% crystallinity of PVDF, another highly homogenous fluoropolymer.
Materials of a high crystallinity tend to be brittle, with lower elasticity and tensile strength. To reduce the brittleness of PTFE it can be synthesized to contain a filler, or a different type of processing can be used, that selects for certain mechanical (or other) properties. That said, crystallinity can often be advantageous as it provides an improved impact strength and hardness, which is useful in high-wear applications.
The extremely low friction coefficient of PTFE results in a highly smooth surface which helps reduce the damage resulting from wear. Finally, also a result of its crystalline structure, PTFE is highly temperature stable meaning it displays similar properties over a wide temperature range.
Thermal
The strong C-F and C-C bonding modes in PTFE have a significant impact on its thermal properties (Table 4), with the C-F bonds having a higher bond strength (116 kcal/mol) than even C-H bonds (99 kcal/mol).3 These extremely strong bonds mean PTFE has a high operating temperature of up to 260 °C (500 °F), one of the highest of all of the fluoropolymers.
Table 4. PTFE thermal properties. PTFE exhibits the broadest temperature usage range of any fluoropolymer. PTFE is also highly resistant to burning and requires very high oxygen content to combust. (Methods are ASTM test standards except where indicated).
Property |
Method |
Value (natural polymer) |
Thermal Conductivity (W/m-K) |
D433/ISO 22007-4/C-177 |
0.17 – 0.30 |
Maximum Service Temperature (°C) |
UL 746 |
260 |
Minimum Service Temperature (°C) |
UL 746 |
-268 |
Melting Point (°C) |
D4591/D3418/ISO 12086/DOW Method |
327 |
Decomposition Temperature (°C) |
E1131 |
505 |
Coefficient of Thermal Expansion, linear (µm/m-°C) |
D696 |
100 |
Flammability Rating (UL 94) |
D2863 |
V-0 |
PTFE is incredibly difficult to burn, needing at least 95% oxygen concentration. (In comparison, normal air contains only about 21% oxygen). These flammability traits of PTFE are especially beneficial for PTFE components used in sensitive or critical applications such as aerospace and automotive environments.
It should be noted that PTFE can undergo an approximately 1.8% decrease in volume between the temperatures of 30 °C to 19 °C (86 °F to 66 °F), as its structure forms a tightly wound canonical helix when cooled.4,5 This decrease in volume is important and should be considered when producing PTFE components for environments that demand a fine tolerance. Once the helical conformation is formed, i.e. at a temperature below 19 °C (66 °F), PFTE displays excellent functional behavior to temperatures as low as -200 °C (-328 °F).
PTFE keeps many of its beneficial characteristics over a wide temperature range, more so than most other fluoropolymers.
Electrical
PTFE is a unique polymer in terms of its electrical behavior (Table 5). The extreme polarity of the C-F bonds in PTFE give it exceptional dielectric properties over a broad frequency range. The dielectric constant and dissipation factor of PTFE show good stability from room temperature to temperatures down to -250 °C (-418 °F), and at frequencies reaching 10 GHz.6,7 The minimization of void formation during PTFE production can be used to further improve the dielectric strength (i.e. breakdown voltage) of PTFE.
Table 5. PTFE electrical properties. PTFE’s perfluorinated nature containing strongly polar C–F bonds results in highly beneficial insulating characteristics. PTFE’s dielectric benefits remain almost unchanged across a very broad frequency range. (Methods are ASTM except where indicated).
Property |
ASTM |
Value (natural polymer) |
Dielectric Constant (1 MHz) |
D150 |
2.1 |
Dielectric Strength (V/mil) |
D149/IEC 60243-1 |
457 – 483 |
Volume Resistivity (Ω–cm) |
D257/IEC 60096 |
≤ 1018 |
The dielectric strength of PTFE is not strongly affected by thermal aging or heating.7 On the whole the insulating properties of PTFE tend to be better than most other solid materials.
Finishing
PTFE can be finished using most standard fabrication and machining methods. Solid processed PTFE can be used to produce a variety of different forms, types and products. Common machining methods, including tapping, turning, threading, drilling, grinding skiving and more, can be carried out without having to make any modifications to equipment.
Although it is a plastic, the hardness of PTFE means that it wears tools to a similar extent as stainless steel.7 However, this also means that PTFE components can be tuned to tolerences as low as < ± 0.001′′ (0.025 mm).7
It is also possible to pre-expand PTFE to form heat shrink tubing for encapsulations, which then sets/hardens to an almost solid form. These forms of membrane or sheet PTFE can then be mechanically expanded or stretched (using a different method to heat shrinking) in a controlled fashion to give expanded PTFE (ePTFE). ePTFE has a microporous structure and can be used in novel applications, in particular for specialized filtrations or in medical devices.
It is possible to bond finished PTFE components, though often this requires the chemical etching of the component using concentrated alkali metal hydrides or hydroxides.6 Pigments can be used to color PTFE, though the choice of pigments is limited to those that can withstand the high temperatures at which PTFE is processed.
The post-extrusion friendly behavior of PTFE is one of the key reasons it is favored for use in high-performance applications across a wide range of industries.
Applications
PTFE still remains as the most popular commercial polymer plastic,2 with its beneficial properties, namely its chemical and thermal inertness and crystal structure, making it ubiquitous in most commercial sectors (Table 6). These span across the chemical and electrical industries, to automotive and aerospace, where PTFE is used in specialized niches.
Table 6. Survey of PTFE applications. PTFE’s temperature tolerance, ability to be sterilized, and ability to be produced in forms such as ePTFE and PTFE heat shrink have made it one of the most widely used fluoropolymers .
Application or Industry |
Key Benefits |
Fluid handling
- tubing, piping
- joint seals
- vessel linings
|
Chemical resistance
Filtration |
Automotive
Aerospace |
Chemical resistance
Dielectrics
Temperature resistance |
Medical
- catheter mandrel
- catheter base liner
|
Biocompatibility, chemical resistance
- lubricity
- bondable (etched)
- microporous, cellular ingrowth
|
Electrical |
Dielectrics, insulation (as coating over wire) |
Heat shrink |
Encapsulation, protection (AMS-DTL-23053™/12 compliant) |
Fiber Optics |
Lubricity
Abrasion resistance |
PTFE that has been extruded can be used to produce extruded over wire, tubing, monofilaments (with or without profiles); it can be calendered into sheets or membranes, which can be followed by stretching to form microporous ePTFE or heat shrink PTFE, or compression molded.
PTFE can also be extruded to give forms that would be extremely difficult (if not impossible) to produce otherwise (Figure 4). Raw PTFE components can be modified or machined to produce specialized finished goods or to produce novel objects. The material traits and manufacturing versatility of PTFE has resulted in it becoming established as the most popular fluoropolymer there is.
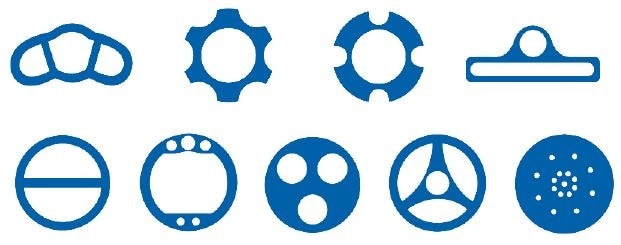
Figure 4. Extruded PTFE profiles. Zeus can extrude PTFE in nearly unlimited customized profiles (and multilumen forms) like those shown here which otherwise would be difficult to produce.
Summary
PTFE was the first of many fluoropolymers and has established itself as one of the most important commercial plastics there is. In part due to its homopolymer structure it is the most fluorinated of all of the fluoropolymers, resulting in a high chemical and thermal stability; with these properties allowing PTFE to beat almost all other polymers in terms of beneficial properties in different applications.
The strong bonding present in PTFE means it has a high melt temperature, and influences its high melt viscosity; which means it cannot be melt-processed and must instead be ram or paste extruded. The machining of PTFE can be carried out using standard techniques and methods, and sheets of PTGE can be extended to form microporous ePTFE or heat shrinks.
The non-stick surface of PTFE can be bypassed using chemical etching to allow PTFE to be bonded. The highly versatile nature of PTFE is one of the key reasons it is the most popular industrial plastic there is.
The exceptional properties of PTFE are another reason it is so popular. It’s fully fluorinated structure (excluding the C-C polymer backbone) makes it the template upon which other fluoropolymers have been developed. The strong C-C and C-F bonds in PTFE give it high chemical and thermal inertness, requiring an atmosphere of at least 95% oxygen to be combusted.
The insulating power of PTFE makes it desirable for use in electrical applications. Whilst it has some mechanical limits the extremely high hardness and low friction coefficient of PTFE means it is excellent in components that will experience high wear. When considered as a whole the advantageous properties of PTFE exceed those of almost all other polymers (Table 7).
Table 7. PTFE advantages and limitations. PTFE can be used in almost every application where mechanical strength is not required with the exception of radiological uses. Broad chemical, temperature, and weathering resistance place PTFE in a group by itself in the landscape of performance fluoropolymer extrusions.
Advantages / Benefits (+) |
Limitations (–) |
- Broad-spectrum chemical resistance
- High temperature tolerance (260 °C / 500 °F)
- Low temperature tolerance (<-200 °C / -328 °F)
- Low coefficient of friction
- Superior weathering
|
- Poor mechanical strength
- Not melt-processable
- Chemical etching needed for adhesive and bonding
- Limited radiation resistance
- High comparative cost
|
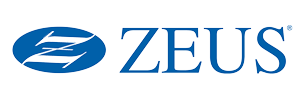
This information has been sourced, reviewed and adapted from materials provided by Zeus.
For more information on this source, please visit Zeus.