Running blast furnaces is expensive, as they are generally uneconomic to run at anything less than full capacity, they are inflexible too. As market conditions wax and wane, oversupply of steel is a real problem, leading to price fluctuations and pressure on steel producers to reduce running costs to maintain margins. With a predicted pickup in steel demand in South East Asia, many steel producers are restructuring and re-engineering in order to remain competitive in the market. Others are seeking cheaper raw material suppliers and turning to new technology as an option to lower the cost of production.
The HIsmelt Iron-Making Process
Rio Tinto has for many years been a trusted supplier to the world’s iron and steel industry, particularly in South East Asia, where its Australian mines offer cost-effective raw material. The company has recently developed a new iron-making process, called HIsmelt, which reduces the costs still further, while at the same time reducing the environmental impact of the iron-making process.
What is HIsmelt?
HIsmelt is an innovative air-based direct smelting technology. The process occurs under pressure within a vertical smelt reduction vessel (SRV) which has a refractory lined hearth and a water-cooled topspace. The refractory hearth contains the molten iron bath, which has a thick slag layer situated above it.
How Does it Work?
The process works like this - iron ore fines, coal and fluxes are injected directly into the melt in the SRV On contact, the coal breaks up, and the carbon reacts with the oxides in the iron-bearing feeds and forms carbon monoxide. The rapid heating of the coal cracks the coal volatiles, releasing hydrogen. The rapid expulsion of the carbon monoxide, hydrogen and nitrogen carrier gas from the molten iron bath propels a fountain of molten material, consisting largely of slag, into the topspace. As this happens, hot air at 1200°C is blasted into the topspace through a water-cooled lance. The oxygen content of the hot air post-combusts with the carbon monoxide and hydrogen, and the heated metal and slag fall back into the bath, providing the energy for direct smelting of the iron ore.
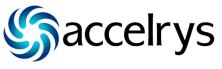
|
Figure 1. A cutaway view of the HIsmelt furnace.
|
Slag and Other By-Products
Ejected slag coats the water-cooled panels, so reducing energy loss. The offgas is cooled via a water-cooled hood and cleaned in a scrubber. It can be used as fuel for hot blast stoves and other equipment, such as a co-generation plant.
What are the Process’ Main Advantages?
The biggest advantage of the process to iron makers is the fact that it produces hot metal without the need for coke ovens and sinter plants. The direct use of low-value grades of iron ore fines without pre-treatment increases the flexibility of raw material supply for steel producers, ensuring greater competitiveness. The use of non-coking coals also brings substantial cost advantages, and the flexibility to vary feedstock with productivity demands allows the operator freedom to continuously optimise operating costs.
Process Flexibility
Raw material selection along with operating parameters (e.g. hot blast rate and level of oxygen enrichment) can be adjusted to maximise the efficient use of the process in line with steelmaking requirements. The ease with which the process can be started, stopped and idled provides flexibility to the integrated steelmaker that is currently unavailable.
Economic Performance
The economic performance of the process at relatively low production capacities allows the use of multiple units to replace large blast furnaces. This, coupled with the potential for significant increases in productivity of each unit through raw material selection, means that the impacts of downtime and relines can be more easily accommodated.
How Does HIsmelt Metal Compare to Blast Furnace Metal
The metal can be mixed directly with blast furnace iron or alloyed to provide precise low silicon content for the BOF charge. So, compared to a blast furnace hot metal, HIsmelt hot metal:
• Reduces flux consumption
• Increases liquid steel yield
• Increases productivity due to a reduced blowing time
• Produces higher quality (low phosphorus) grades
• Reduces re-blows reduces refractory consumption
• Decreases consumption of ferro-alloys
• Allows production of ultra-clean steel.
Retro-Fitting a HIsmelt Plant into an Existing Plant
A further advantage is that a HIsmelt facility uses much of the same equipment as a blast furnace, enabling a HIsmelt plant to be easily retro-fitted into an integrated site.
Environmental Impact of the HIsmelt Process
The environmental benefits of the HIsmelt process are considerable. By reducing the demand for coke, sinter and pellets, and improving the energy efficiency of the iron making process, it reduces emissions of greenhouse gases and other damaging environmental pollutants such as SOx, NOx and dioxins.
Overall, a commercial HIsmelt facility, equipped with ore preheating, can reduce carbon dioxide emissions per tonne of hot metal by close to 20% when compared to the typical blast furnace route. Furthermore, the operating conditions within the SRV generally preclude the formation of dioxins - a fact substantiated at the pilot plant.
The Use of Waste Materials
The use of steel plant waste uprisings and stockpiled wastes allows further improvements in the environmental footprint of the plant. High recovery of iron and carbon credits has been demonstrated - iron unit losses were no different to that of an ore only operation (2-3%). Zinc and lead were found to partition to dust, suggesting that reverts high in zinc and lead would probably be acceptable in a HIsmelt plant. With appropriate recycling, it is possible that a marketable zinc-lead material could be produced for sale to zinc smelters. In the demonstration plant trials there was no sign of zinc-rich accretions in the offgas system and no dioxin was detected at any stage.
Variations in Feedstocks
Blast Furnace Feedstocks
Due to the implications on blast furnace performance, the modern integrated pig iron plant has a finely-tuned supply chain to keep the feed raw materials going into the blast furnace with the minimum chemical and physical variations. Considerable effort is made to ensure that coke quality is consistent - even small variations in physical properties can have a significant impact. Similarly, when sinter is made, each plant uses a particular blend of iron ore fines that is aimed at giving consistent physical and chemical properties.
HIsmelt Feedstocks
Although changes in raw materials specifications do have some impact on HIsmelt performance, these are easily costed and suitable adjustments made in purchase prices. HIsmelt also has the inherent advantage in that it can take iron ore feed material and coal less than 6mm in size, a product that already sells at a discount compared to premium lump. It can also process fine-ground concentrates, without the added costs of pelletising, and use a broad range of coals that are currently not suitable for blast furnaces.
Blast Furnace Production Rates
At the same time, blast furnaces are also not capable of much ‘turn down’ (ability to run at lower than optimum design capacity) because of the rapidly increasing coke consumption that increases operating costs. The response time of a blast furnace to changes in raw material as shown in the final product can be several hours, and the pig iron product needs very close monitoring for its chemistry, temperature, and other variables to detect trends and then take appropriate action to keep operations at a steady state. Extensive computer models based around silicon levels in the pig iron and temperature measurements are essential tools on large modern facilities.
Flexibility of Blast Furnaces and HIsmelt Plants
This makes blast furnaces inherently inflexible and so stops them reacting quickly to delays or problems in the steel plant. This may result in the necessity to plate or produce cold pig iron. Conversely HIsmelt has reactions that take place in fractions of a second and can be instantaneously stopped, simply by turning off the hot air blast. Restarting after delays is simply a case of injecting some coal and reheating the bath to operating temperature and then recommencing smelting.
Coping with Changes in Demand
With changes in demand, output can be altered by for example, reducing the oxygen content of the hot air blast, or by using a cheaper higher volatility coal, or a cheap coal with higher ash content. Naturally there are some cost implications, but these may self compensate, so the cash costs of operation do not significantly change.
HIsmelt Pilot Plant
The HIsmelt process works well enough at pilot-plant scale, but has not yet been tested at production scales. This will change with the building of a commercial HIsmelt facility at Kwinana in Western Australia, on the site of the current demonstration facility. Construction will commence from the beginning of 2003 with completion expected by the end of 2004.
As well as being designed to meet commercial objectives, the plant has been designed to have a neutral energy balance, with a small export of electrical energy. The plant will also be the platform from which further scale-up and development of the process and engineering can be made for plants of capacity greater them 1.5 million tonnes per annum.
Summary
Overall, the HIsmelt process is revolutionary for the iron and steel industry, and will make restructuring of the steel industry easier and provide an attractive option for developing countries. A HIsmelt facility can directly replace a blast furnace within an integrated mill, eliminating the need to upgrade or replace sinter plants, pellet plants and coke ovens. The technology significantly improves iron making environmental performance and could well become the iron making technology of choice in the 21st century.
|