A crucial physical property of volatile liquids — particularly crude oil, gasoline, gasoline-oxygenate blends, and LPG — is vapor pressure. Vapor pressure is accurately determined because of several — partially coinciding — reasons, detailed below.
Governmental Regulations
Vapor pressure offers a clue of how a fuel will perform when exposed to diverse working conditions: Whether a fuel will cause vapor locks at high altitude or at high ambient temperature, or will deliver easy starting at low ambient temperatures. Petroleum product specifications are controlled by numerous governmental agencies, and maximum vapor pressure restrictions for gasoline and crude oil are legally directed in various areas as a measure of environmental pollution control.
Official vapor pressure restrictions for spark-engine fuels are based on ambient conditions, typically referred to as winter-graded or summer-graded fuel. In a number of countries around the world, it is mandatory to mix gasoline with biofuels, which in turn influences the vapor pressure of the fuel. Maximum vapor pressure limits are regulated in compliance with various EN, ASTM, and IP standards.
Safety for Transportation and Storage
Pipeline operators, fuel depots, terminals, offshore platforms, or oil tankers detect the vapor pressure, before conveying crude oil or other petrochemical items such as LPG or gasoline for subsequent processing. It is necessary to know the vapor pressure of the conveyed substance to avert expensive damage done to the transportation system. Damage prevention is not restricted to the supplier only: Customers need their supplier to ensure a maximum vapor pressure before accepting delivery of fuel.
The following examples offer a clear picture, why it is essential to regulate the vapor pressure:
a) Offshore platforms establish the vapor pressure of crude oil to define the bubble point, before transporting the crude via tanker or pipeline to a distribution platform/terminal.
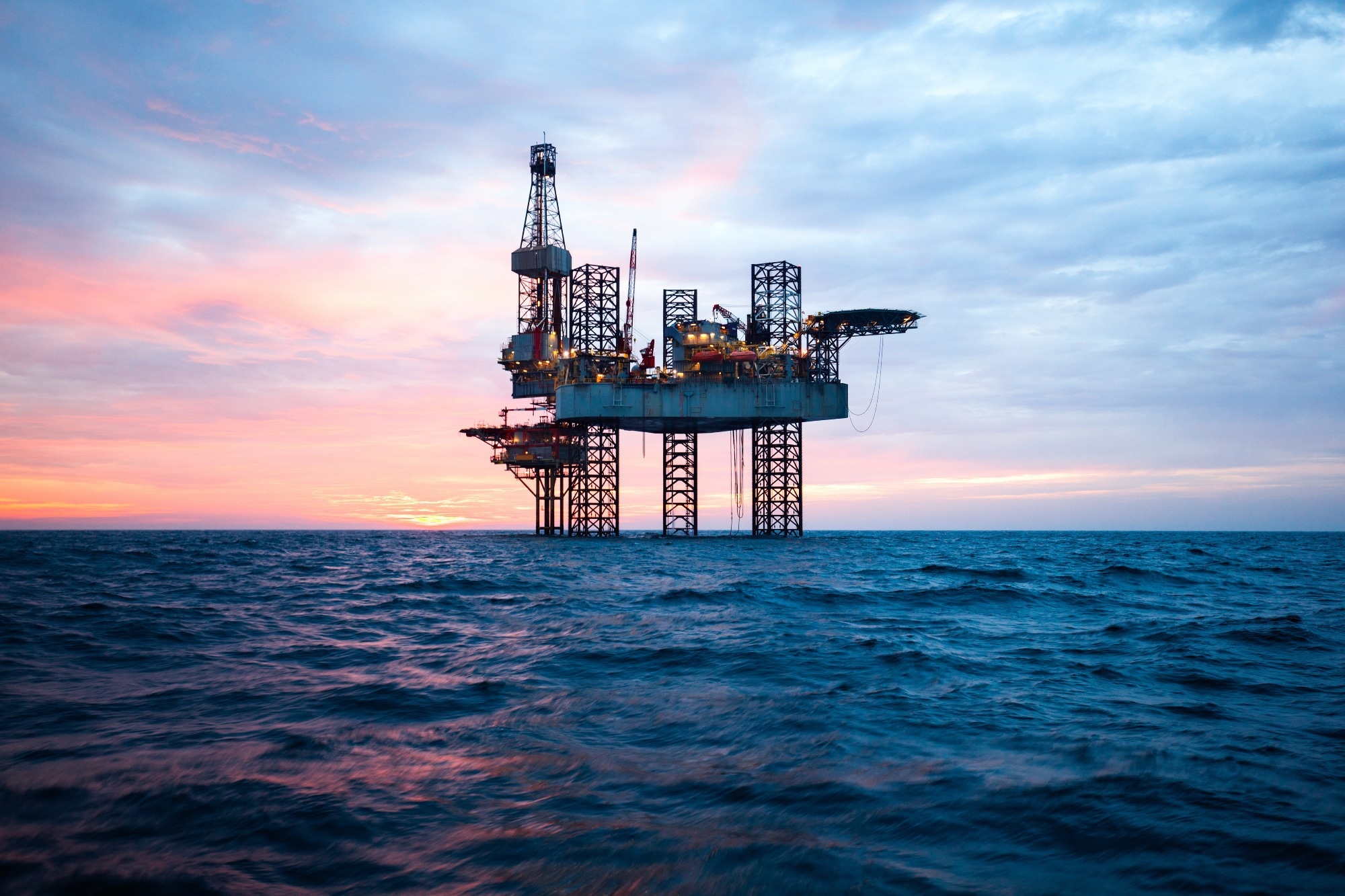
Image credit: Shutterstock / Lukasz Z
Therefore, surplus gas is burned to avoid damage done to the transportation medium. If the crude case’s vapor pressure is very high, pump cavitation might occur during transfer operations. It is, thus, advisable for a platform operator to have their platform fitted with a vapor pressure analyzer. As a result, the operator is able to provide proof that the released crude is delivered in compliance with specifications — and to avert expensive damage.
b) Liquid terminals are used as a buffer or for storage, before petroleum products are shipped or moved for delivery or further processing. Fuel depots are used, each time petroleum products from various oil production sources are moved to a central storage area. Vapor pressure is a crucial property to establish the quality of the products supplied from various sources.
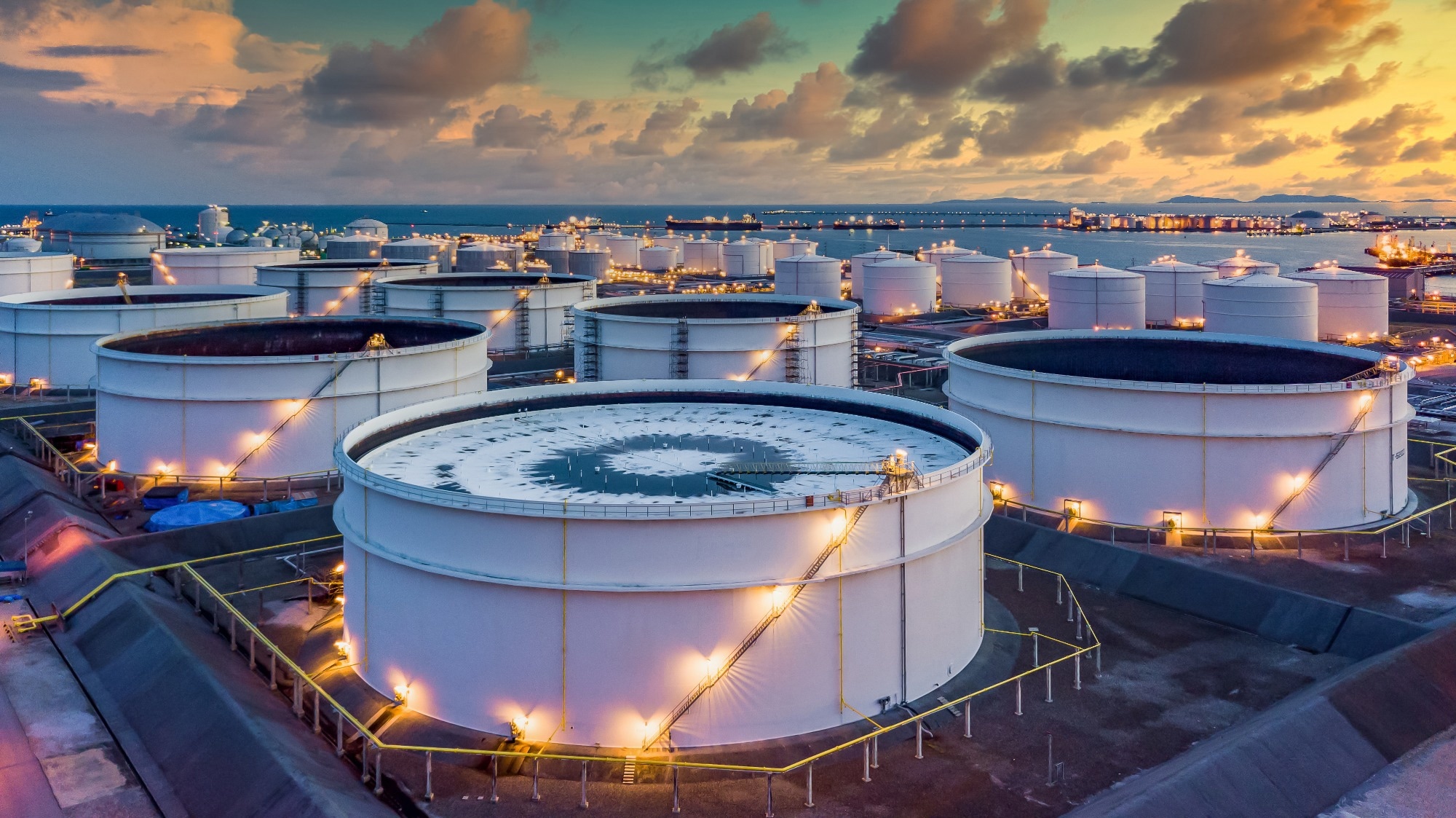
Image credit: Shutterstock / Avigator Fortuner
Safety of personnel and the facility is a paramount concern. For example, most floating roof tanks are used for storage, and occasionally, fixed roof tanks are used. In the case of fixed roof tanks, vapor pressure limits are fixed as a means of explosion protection: When crude oil or gasoline is released, the volume has to be substituted by gases. This is regulated by testing the vapor pressure. In floating roof tanks, very high vapor pressure will cause bubbles under the roof, which can result in an overturn of the roof.
Besides the costs, a failure might cause environmental protocols to limit maximum vapor pressure in floating roof tankers, to avoid air pollution control by outgassing of petroleum products.
Profit Optimization in Refineries and in the Pipeline
In the refinery, crude oil is made into gasoline with varying quality (octane numbers). Naphtha is mixed with oxygenates, octane, and butane boosters to obey with governmental and environmental protocols, to guarantee better performance of the fuels and to decrease production costs. To preserve a specific quality level of the refined product, refineries have to monitor the vapor pressure carefully during the entire refining process.
The following examples show how to profit from precise vapor pressure testing:
a) Refineries:
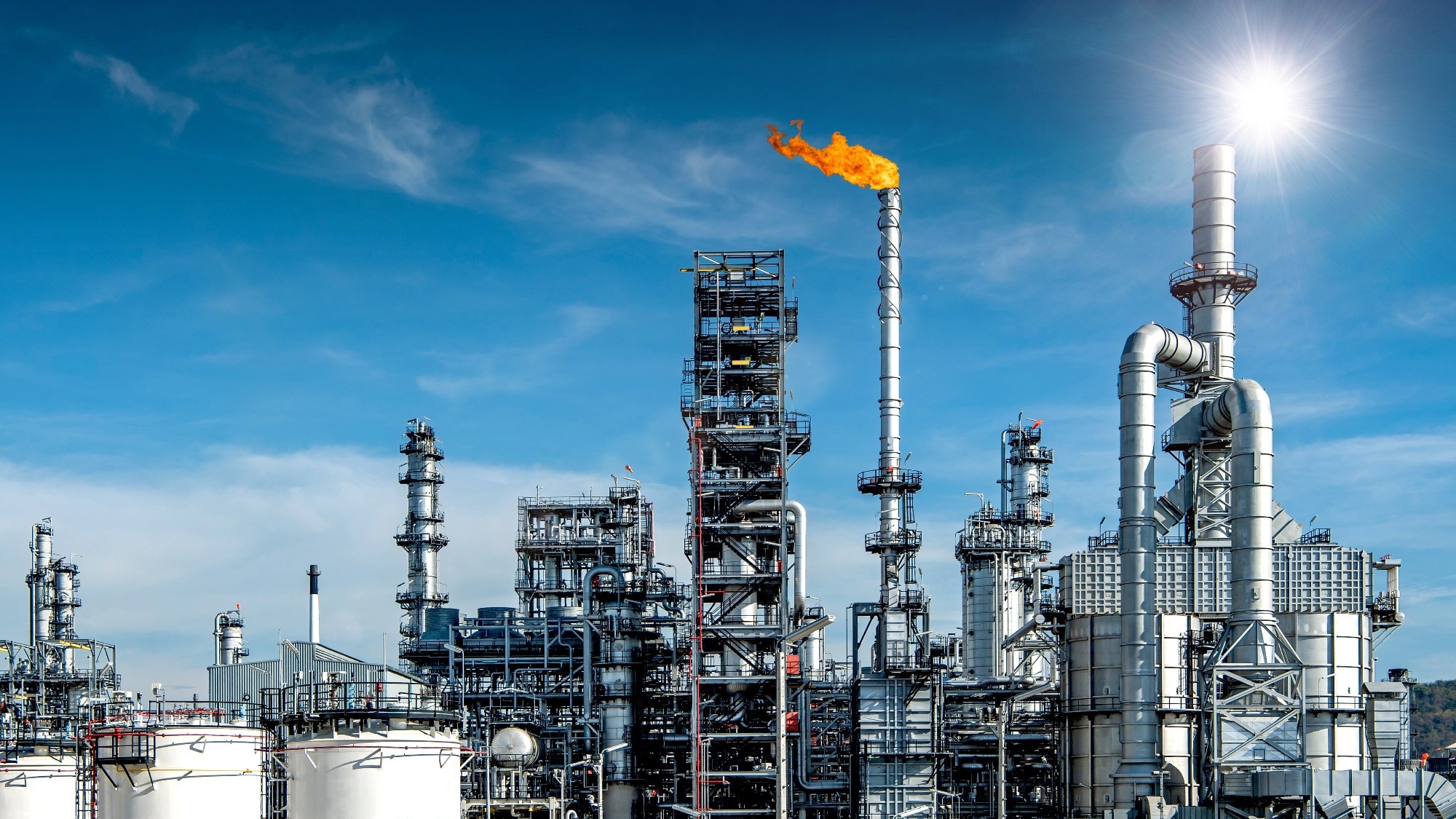
Image credit: Shutterstock / Red Ivory
By mixing C4-compounds with gasoline, profit margins can be improved, while the heat of combustion stays unaffected. Similar to butane, C4 is a lot cheaper than crude oil, but also increases the vapor pressure. Refined gasoline has to adhere to maximum vapor pressure limits for summer- and winter-graded fuel. Thus, maximum profit can be achieved when blending as close as possible to authorized limits. This necessitates an analyzer that can test vapor pressure as precise as possible.
b) Pipeline Operators, plants, and transportation:
Typically, supplier and customer agree over maximum vapor pressure limits of gasoline or crude oil supplied to a terminal or plant. This is essential to confirm safety for transportation and storage, and to ensure that the customer receives a particular quality of fuel.
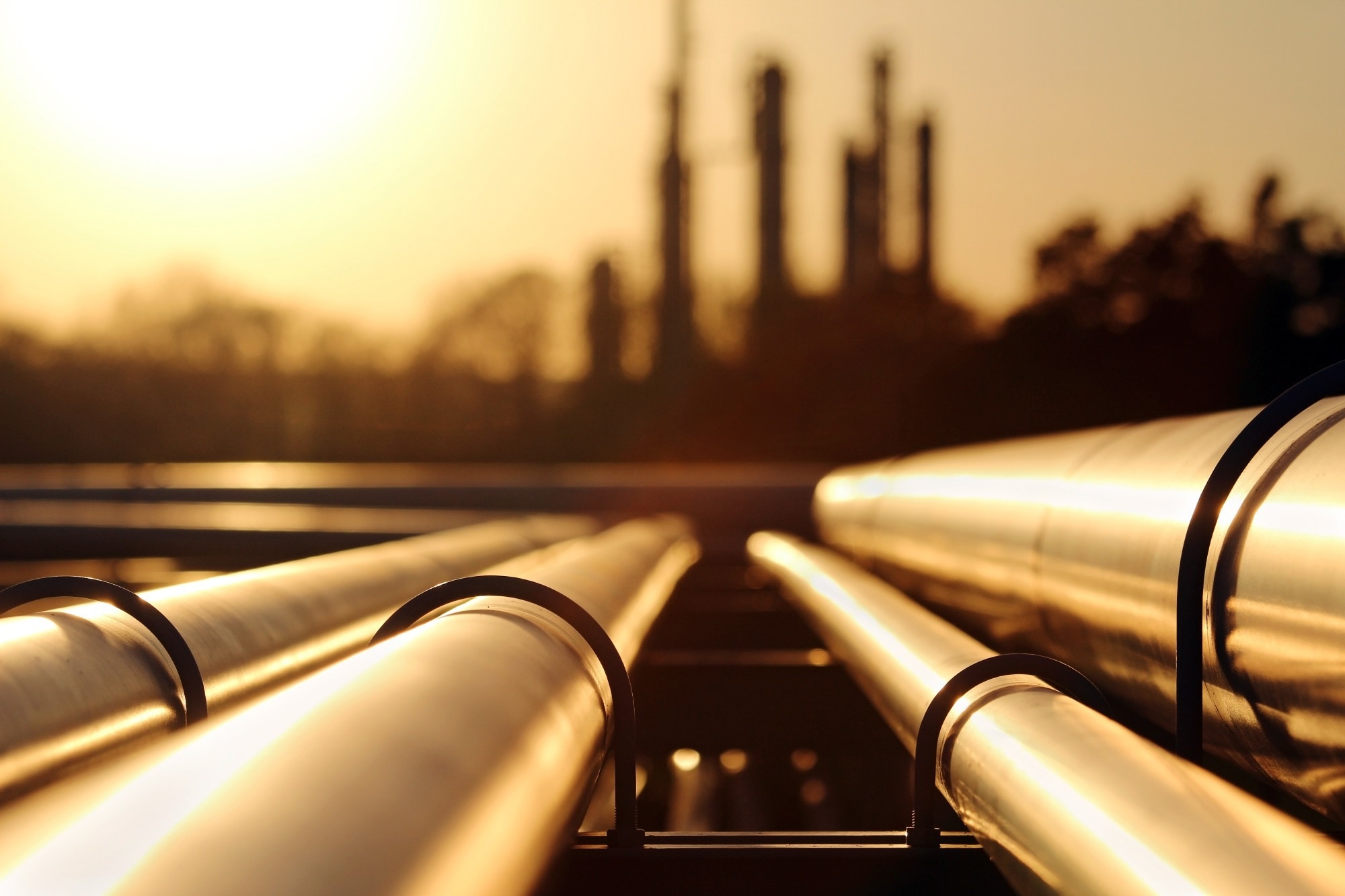
Image credit: Shutterstock / Kodda
One of the most popular applications for vapor pressure testing is C4-blending: The price valuation of crudes can be raised when propane or butane is mixed into the crude. The incorporation of these hydrocarbons is restricted by the maximum Reid Vapor Pressure (RVP). Based on the RVP prior to blending, normally ratios of 1% to 5% of hydrocarbons are mixed into the crude. Thus, even a small plant undertaking some 10,000 m3 per month can anticipate up to $50,000 through C4-blending. Therefore, blending of low-priced butane into crude oil, while keeping a check on product quality via vapor pressure detection, can substantially enhance profit for operators of pipelines and plants, paying down vapor pressure analyzer equipment expenses quite quickly.
Method/Solution
Method
Grabner Instruments MINIVAP ONLINE functions with the same smart, rapid, and precise technique for vapor pressure determination like the Grabner Instruments laboratory vapor pressure testers. MINIVAP laboratory testers are U.S. EPA reference instruments for maximum precision. Based on the detail that the vapor pressure of liquids stays constant and that all components — such as dissolved air — follow the ideal gas equation, an expansion takes place in three steps at constant temperature. Three total pressure values are established. From these three total pressure values, the liquid’s solubility factor, the partial pressure of the air, and the liquid’s absolute vapor pressure are calculated.
MINIVAP ONLINE is the only vapor pressure process analyzer 100% compliant with all applicable EN, ASTM, and IP specifications for gasoline, crude oil, and LPG. MINIVAP ONLINE adheres to ASTM D5188, D5190, D5191, D6377 and D6378, D 6897, EN 13016 1+2, IP 394, 409, and 481 and offers ASTM-approved correlations for D4953, D1267, D323, and D5482.
Measuring Principle
The stream product is conditioned in the sample conditioning system that permits the measuring system to function. Pressures of up to 70 bar in stream are decreased between 0 and 7 bar filling pressure modifiable by a pressure regulator subject to the applied sample. The filling pressure has to be higher than the vapor pressure of the sample to achieve correct filling of the system. The sample conditioning system assures a typical sample in the measuring unit like in the stream line.
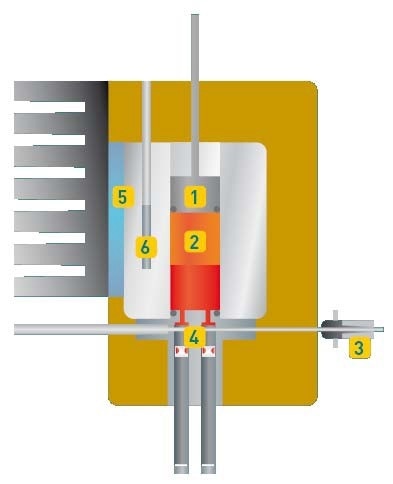
Figure 1. Measuring Cell of MINIVAP ONLINE
The sample is added via the Luer sample inlet (3) and the sample inlet valve (4) into the measuring chamber. The automatic sample addition and the volume modification are realized by a piston with an in-built pressure transducer (1). The measuring chamber (2), with a total volume of 5 mL, is rinsed with 3 x 2.5 mL and filled with the right amount of sample. After closing the valve (4), single or triple expansion to 5 mL (with vacuum formed by piston removal) is obtained by extra piston strokes. The measuring cell’s temperature is regulated by a high-power thermoelectric module (5) and measured with a precision Pt100 RTD sensor (6).
Data are output via usual MODBUS digital signal or typical 4–20 mA analog signal; the analyzer is ATEX and UL certified and includes an explosion-proof Class I housing.
The MINIVAP ONLINE analyzer can deal with up to two diverse sample streams, both regulated by an automatic sample conditioning system. Accuracy allows mixing as close as 0.3 kPa (0.05 psi) to authorized limits within a cycle time of 7 minutes.
Analytical Performance
The exceptional performance of the MINIVAP ONLINE has been established in numerous round robins in refineries and autonomous laboratories. The following figures offer the results of measurement of gasoline and pure components.
Accuracy of MINIVAP ONLINE vs. ASTM D5191 standard
As per Standard ASTM D5191, cooling and air saturation of the sample is necessary before the measurement of the vapor pressure. Using the triple expansion technique, sources of error — such as operator bias — are eliminated, delivering very precise results. Figure 2 illustrates characteristic sample behavior, when testing in compliance with ASTM D5191 against measurements according to ASTM D6378 by MINIVAP ONLINE.
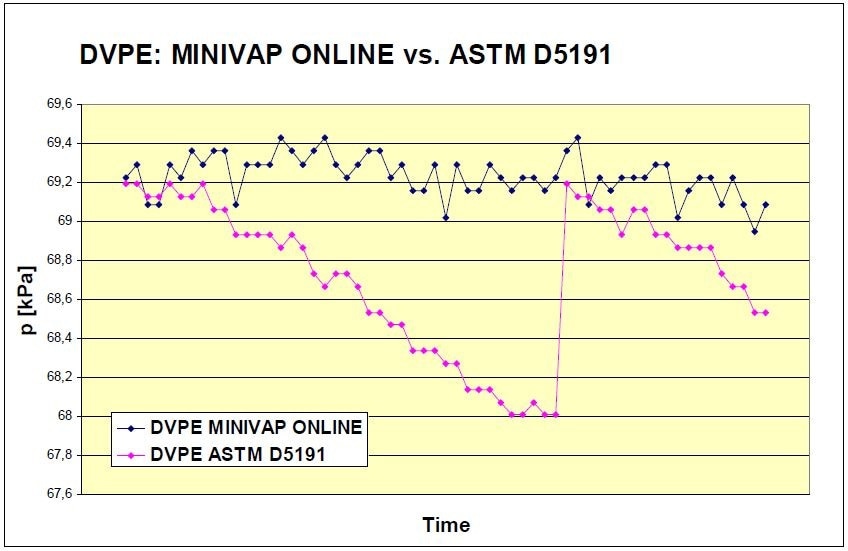
Figure 2. DVPE of gasoline — MINIVAP ONLINE vs ASTM D5191. Jump in the D5191 line indicates that chilling and air saturation of the sample has been performed as per standard requirements.
Performance comparison (liquids): MINIVAP ONLINE vs Lab Analyzer
While the majority of Vapor Pressure Process Analyzers correlate to a particular standard, the MINIVAP ONLINE offers direct vapor pressure testing, without any read-modifiable, unreliable, and unconfirmed correlations to standard methods. Tables 1 and 2 reveal the high accuracy of MINIVAP-ONLINE measurements in comparison with lab analyzer measurements.
Table 1
Sample |
Pabs - Lab Analyzer
[kPa] |
Pabs – Process analyzer
[kPa] |
Delta
[kpa] |
neo-HEX |
68.2 |
68.6 |
-0.4 |
neo-HEX |
68.3 |
68.6 |
-0.3 |
neo-HEX |
68.3 |
68.6 |
-0.3 |
Cyclopentane |
68.4 |
68.8 |
-0.4 |
Cyclopentane |
68.2 |
68.8 |
-0.6 |
Cyclopentane |
68.4 |
68.8 |
-0.4 |
91 octane |
84.8 |
84.5 |
0.3 |
91 octane |
84.9 |
85 |
-0.1 |
91 octane |
84.8 |
84.9 |
-0.1 |
95 octane |
86.6 |
86.4 |
0.2 |
95 octane |
87.1 |
87.2 |
-0.1 |
95 octane |
86.8 |
87 |
-0.2 |
Average |
77,1 |
77,3 |
-0,2 |
Min |
68,2 |
68,6 |
|
Max |
87,1 |
87,2 |
|
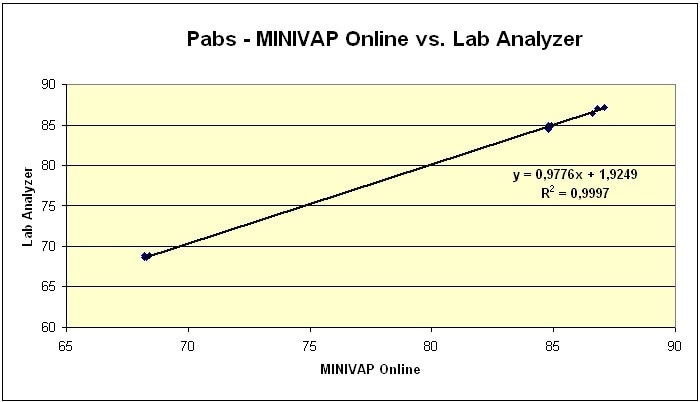
Figure 3. Pabs of MINIVAP ONLINE vs Lab Analyzer, various samples, method: ASTM D6378
Performance comparison (LPG/NPG): MINIVAP ONLINE vs Lab Analyzer
Besides Gasoline and Crude Oil VP-determination, the MINIVAP ONLINE can test LPG and NPG, too. Tables 1 and 2 reveal the normal LPG measurements according to the standard ASTM D1267, compared to MINIVAP ONLINE (ASTM D6897).
Table 2
Measurement |
VP-ASTM D-1267
psig |
MINIVAP ONLINE
psig |
DELTA
psi |
1 |
195,5 |
195,4 |
-0,1 |
2 |
195,5 |
195,5 |
0,0 |
3 |
195,5 |
195,4 |
-0,1 |
4 |
195,0 |
194,8 |
-0,2 |
5 |
195,0 |
195,0 |
0,0 |
6 |
195,0 |
194,9 |
-0,1 |
7 |
195,5 |
195,8 |
0,3 |
8 |
198,0 |
197,9 |
-0,1 |
9 |
198,0 |
198,1 |
0,1 |
10 |
198,0 |
198,1 |
0,1 |
11 |
197,5 |
197,7 |
0,2 |
12 |
197,5 |
197,9 |
0,4 |
13 |
197,5 |
197,7 |
0,2 |
14 |
197,0 |
197,1 |
0,1 |
15 |
197,0 |
197,5 |
0,5 |
16 |
196,5 |
196,4 |
-0,1 |
17 |
196,5 |
196,7 |
0,2 |
18 |
196,5 |
196,7 |
0,2 |
Average |
196,6 |
196,7 |
0,1 |
Min |
195,0 |
194,8 |
-0,2 |
Max |
198,0 |
198,1 |
0,5 |
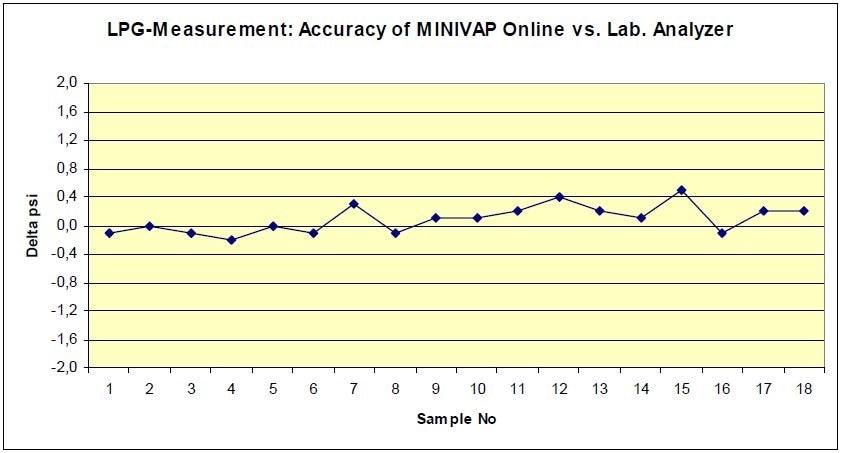
Figure 4. Psig of MINIVAP ONLINE vs ASTM D1267, sample: LPG
Repeatability and Reproducibility
The MINIVAP ONLINE r/R conforms to the most stringent vapor pressure standards. Even better measurements than mandated by the standards are feasible when analyzing pure substances. Therefore, precision with the MINIVAP ONLINE is higher than precision of other Vapor Pressure Process Analyzers.
Instrument precision:
Repeatability r = 0.3 kPa (0.04 psi)
Reproducibility R = 0.7 kPa (0.10 psi)
Table 3 shows the repeatability for MINIVAP ONLINE, tested in accordance with ASTM D6378.
Table 3. Repeatability of MINIVAP ONLINE, method: ASTM D6378
Measurement |
Pabs [psi] |
Pabs [kPa] |
Pgas [kPa] |
P1 |
P2 |
P3 |
1 |
9.91 |
68.3 |
3.1 |
83.8 |
76.0 |
71.4 |
2 |
9.91 |
68.3 |
3.1 |
83.4 |
75.9 |
71.4 |
3 |
9.88 |
68.1 |
3.2 |
83.6 |
76.0 |
71.3 |
4 |
9.91 |
68.3 |
3.1 |
83.6 |
76.0 |
71.4 |
5 |
9.91 |
68.3 |
3.1 |
83.6 |
76.0 |
71.4 |
6 |
9.89 |
68.2 |
3.2 |
83.5 |
76.0 |
71.4 |
7 |
9.91 |
68.3 |
3.1 |
83.7 |
76.0 |
71.4 |
8 |
9.91 |
68.3 |
3.1 |
83.7 |
76.0 |
71.4 |
9 |
9.91 |
68.3 |
3.1 |
83.8 |
76.0 |
71.4 |
10 |
9.91 |
68.3 |
3.1 |
83.7 |
76.0 |
71.4 |
11 |
9.91 |
68.3 |
3.1 |
83.4 |
75.9 |
71.4 |
12 |
9.91 |
68.3 |
3.1 |
83.6 |
76.0 |
71.4 |
13 |
9.89 |
68.2 |
3.2 |
83.4 |
76.0 |
71.4 |
14 |
9.91 |
68.3 |
3.1 |
83.6 |
75.9 |
71.4 |
15 |
9.89 |
68.2 |
3.2 |
83.5 |
76.0 |
71.4 |
16 |
9.93 |
68.5 |
3.0 |
83.8 |
76.0 |
71.5 |
17 |
9.91 |
68.3 |
3.1 |
83.6 |
76.0 |
71.4 |
18 |
9.88 |
68.1 |
3.2 |
83.2 |
75.9 |
71.3 |
19 |
9.88 |
68.1 |
3.4 |
84.4 |
76.4 |
71.5 |
20 |
9.91 |
68.3 |
3.1 |
83.8 |
76.0 |
71.4 |
21 |
9.91 |
68.3 |
3.1 |
83.7 |
76.0 |
71.4 |
22 |
9.89 |
68.2 |
3.2 |
83.5 |
76.0 |
71.4 |
23 |
9.91 |
68.3 |
3.1 |
83.2 |
75.9 |
71.4 |
24 |
9.91 |
68.3 |
3.1 |
83.3 |
75.9 |
71.4 |
25 |
9.92 |
68.4 |
3.0 |
83.5 |
75.9 |
71.4 |
26 |
9.91 |
68.3 |
3.1 |
83.4 |
75.9 |
71.4 |
27 |
9.89 |
68.2 |
3.2 |
83.4 |
76.0 |
71.4 |
28 |
9.91 |
68.3 |
3.1 |
83.7 |
76.0 |
71.4 |
29 |
9.88 |
68.1 |
3.2 |
83.3 |
75.9 |
71.3 |
Average |
9,90 |
68,27 |
3,13 |
83,58 |
75,98 |
71,40 |
Min |
9,88 |
68,1 |
3,0 |
83,2 |
75,9 |
71,3 |
Max |
9,93 |
68,5 |
3,4 |
84,4 |
76,4 |
71,5 |
Repeatability |
0,029 |
0,197 |
0,167 |
0,521 |
0,204 |
0,093 |
Conclusion
Due to governmental regulations, the vapor pressure measurement of gasoline is the most important application. However, depending on its modular arrangement, the MINIVAP ONLINE can be used for all varieties of liquids manufactured by industries where the determination of vapor pressure is mandatory for quality control or for manufacturers’ safety data sheets.
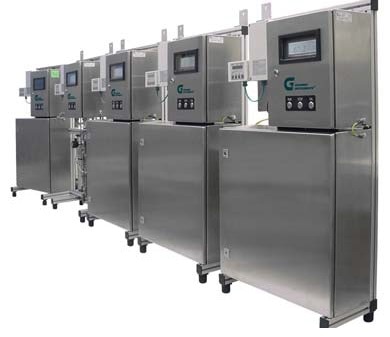
The exclusive expansion technique makes the MINIVAP ONLINE an unmatched analyzer for the determination of vapor pressure of different types of liquids. The MINIVAP ONLINE is the only vapor pressure process analyzer that is 100% compliant with all applicable EN, ASTM, and IP specifications, using the same technique as the laboratory instruments, which are the U.S. EPA reference for maximum precision. Quick and direct vapor pressure testing saves customers money and time.
Regardless of the application it is used for, choosing the MINIVAP ONLINE will pay off in a short period of time.

This information has been sourced, reviewed and adapted from materials provided by Grabner Instruments.
For more information on this source, please visit Grabner Instruments.