Rechargeable batteries have a wide range of applications that have an impact on people’s quality of life; for example, these batteries are used in medical equipment, smartphones, electric vehicles, handheld tools, toys, and so on.
Increasing the total number of charge-discharge cycles, boosting energy density, and raising the safety aspects while reducing weight and cost constitute the sustained development of rechargeable batteries. To achieve these measures, novel materials and innovations are needed, like solid-state batteries that have to be subjected to stringent testing before being introduced into the production cycle.
This high energy density can be very dangerous, and it is one of the reasons that a majority of devices are forbidden on commercial aircraft. Moreover, mechanical damage, such as separator penetration and brittle failure of the electrodes, can lead to significant releases of stored energy, like battery fires (see Figure 1).
.jpg)
Figure 1. Example of battery failure leading to the rapid release of energy.
In addition, stresses arising from fabrication, mechanical (or ion)-induced stiffening and swelling, failures of coatings, and mechanical damage and stresses arising from numerous charge-discharge cycles represent considerable challenges in the development and integration of new devices. Therefore, for the sake of performance and safety reasons, it is essential to understand the mechanical performance of these devices, including every component at a suitable size scale.
Experiment
Since lithium has high electrode potential, it forms the core component in battery electrodes. Conversely, this element is highly reactive with nitrogen, oxygen, and water and will ignite in oxygen upon exposure to moisture or water. As a result, testing has to be performed in a regulated environment. Bruker’s Hysitron® TI 980 IO TriboIndenter®, which provides a controlled atmosphere with less than 1 ppm moisture and oxygen levels, was employed for these experiments (see Figure 2).
.jpg)
Figure 2. The Hysitron® TI 980 IO offers compatibility for most options, including a temperature from −80 °C to +800 °C, indentation at both low (sub 10 μN) and high (up to 10 N) loads, in a controlled gas environment.
Case A: Time-Dependent Deformation—Creep and Strain Rate Effects for 4N Lithium
When it comes to batteries, lithium metal is regarded as a suitable material because it has the lowest negative electromechanical potential and ultra-high theoretical specific capacity. Despite this, lithium is an exceptionally soft metal, showing time-dependent plastic deformation. In this regard, establishing the nanomechanical characteristics of battery materials, such as hardness and elastic modulus, and inferring nanomechanical behaviors, like the plastic flow of the emerging battery materials, are vital for failure analysis and hypothetical predictions.
Load-displacement curves were calculated under continuous loading strain rate conditions with pure lithium foil utilizing a diamond Berkovich indenter (see Figure 3a).
.jpg)
.jpg)
Figure 3. The effect of strain rate of 4N lithium. A strain rate exponent of 0.06 was calculated: (a) The effect of strain rate on the loading curve; (b) Viscoplasticity, resulting in creep on unloading. Even a 1-second unload from 5 mN results in this continued viscoplasticity. Even more rapid unloading rates, such as −50 mN/second, must be applied to use traditional unloading stiffnesses to calculate the reduced modulus.
This constant strain rate can be defined as
where δ is the depth and ɛ is the strain. Conversely, this can be simplified as
where P denotes the load, provided the material has constant hardness with regards to depth. The strain rate sensitivity exponent, in this case, is found to be 0.06 — 10 times that of large-grained copper and twice that of nanocrystalline copper.
Such indentation measurements, made on 99.99% lithium foil, also display viscoplastic properties on unloading effects, as illustrated in Figure 3b. This sustained plastic deformation, despite decreasing the applied load, offers a deeper understanding of the modes of deformation in these kinds of materials.
Case B: High-Speed Mechanical Property Mapping
Most often, the materials used for solid electrolytes, anodes, and cathodes are composites having microstructural heterogeneity. Here, mechanical stability has an important role to play in preventing the degradation of solid electrolytes as well as electrodes that can result in serious failure of batteries [1, 2]. For example, silicon electrodes can experience over 300% volume expansion at the time of cycling [3]. Therefore, studying mechanical properties, like the hardness (strength) and elastic modulus of battery materials, is important to understand the occurrence of mechanical degradation process of battery materials at the time of charging and discharging processes.
Figure 4 shows maps of hardness and modulus achieved for lithium deposited on a copper working electrode.
.jpg)
.jpg)
Figure 4. (a) Modulus and (b) hardness map showing variation in the electrodeposited lithium film on the copper working electrode.
It took 30 minutes to perform 625 indents across a 25 x 25 μm2 area using Bruker’s accelerated property mapping (XPM™) technique. In this example, the viscoplastic effect on the unloading slope was resolved using unloading times of 100 ms. The distribution of the modulus and hardness across the sample is shown by the indentation maps in Figure 4. This spatial precision is partly due to the reduced indentation depth when compared to the thickness of the film and the size of the heterogeneity. The statistical distribution of modulus and hardness is shown in Figure 5.
.jpg)
.jpg)
Figure 5. The distribution of (a) reduced modulus and (b) hardness of lithium deposited on copper electrode determined by 625 measurements.
Assuming numerous distributions, this data can be further examined to find out the average and also the maximum and minimum properties of the electrodeposited film.
Conclusions
Using Bruker’s Hysitron TI 980 IO testing suite, nanomechanical testing of battery materials was successfully carried out in a regulated, argon-filled environment. This initial study represents the instrument’s basic capabilities to enable mechanical characterization of emerging materials in a quantitative manner and also provides a better understanding to enhance mechanical performance.
References
- Müller, S., Pietsch, P., Brandt B., Baade P., Andrade, V., Carlo F., and Wood V., Nature Comm., 9 (2018), p. 2340.
- Xu R., Sun H., Vasconcelos L., and Zhao K., J. Elecrochem. Soc., 164 (2017), A3333.
- Kumar R., Lu P., Xiao X., Huang Z., and Sheldon B., ACS Appl. Mater. Interfaces, 9 (2017), p. 28406.
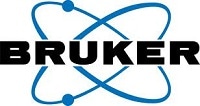
This information has been sourced, reviewed and adapted from materials provided by Bruker Nano Surfaces.
For more information on this source, please visit Bruker Nano Surfaces.