In order to understand the benefits and drawbacks of the melt-flow-rate (MFR) test completely, it is essential to know something about how the test is carried out.
The methodology is included in ASTM D 1238, while the related international standard is ISO 1133. The approaches have slight differences between them; however, they typically carry out the same function.
Both determine the rate at which a polymer flows under very unique conditions using an instrument with a very specific geometry. For the ASTM technique, the diameter of the cylinder into which the material is filled is 0.376 inches, and there is a removable insert with a much smaller opening or orifice at the bottom of the cylinder, as it is generally assigned. While some materials are tested using a non-standard orifice, the standard opening has a diameter of 0.0825 in. + 0.00025 in. and a height of 0.315 in. + 0.001 in.
Importance of Flow Path Dimensions
The tolerances, in this case, imply that the dimensions of the flow path are considered vital and they certainly are. The MFR instruments are available with a go/no-go gauge for the orifice diameter that should be used constantly to make sure that the opening is as per the specification. Orifices come in a variety of materials and some are more robust than others, specifically against the impacts of fierce cleaning that can make the opening bigger. Furthermore, cleaning the bottom and top surface of the orifice can decrease the height. These factors can minimize the accuracy of the measurements.
Considering the physical equipment to be in good condition, the test involves first determining the ideal temperature for the material being tested. The recommended temperatures are polymer-specific: Polycarbonate (PC) is normally tested at 300 ○C, polyethylene at 190 ○C, etc. Certain polymers have two or even three standard conditions that may be used, and it is often the resin supplier who chooses which one will be used. Perhaps, ABS is the best example of this, where it is possible to use one of three different temperatures to carry out the test. Therefore, when conducting incoming quality-control tests, the same conditions that were used by the material supplier must be used in order to obtain the same results. Temperature calibration is also very essential just like orifice geometry.
The other important input parameter is the mass that is positioned on the material sample after it has been loaded into the cylinder and raised to the specific temperature. This is also a polymer-specific setpoint and it can be a single number stipulated by all, for example, 1.2 kg for PC, or it can be one of two or three values, for example, in the case of ABS. For each of the three temperatures that can be used to test ABS, there is a specific mass associated with that temperature. It is possible to use 200 ○C with a 5 kg load, 230 ○C with 3.8 kg, or 220 ○C with 10 kg. And, of course, each condition will provide different results for the same compound. The real MFR value that the test provides is expressed in grams/10 minutes and is controlled by the composition of the material being tested and the test conditions.
Important Aspect of the Test
Here is the key principle of this test: The load is the input that steers the material through the orifice; the flow rate is the output. As a result, the MFR test is a constant-shear-stress test, and not a constant-shear-rate test. As such, it is a pressure-limited configuration. With regards to this, it is different from a capillary rheometer, which is a device that measures the viscosity that can regulate and change the flow rate of the test during the measurement of the force needed to attain that flow rate.
Capillary rheometry, which is a controlled-shear-rate test, can give an actual measurement of viscosity, or resistance to flow. Moreover, since the viscosity of a polymer changes with flow rate, or shear rate, a full characterization of viscosity should enable measurements at multiple shear rates and the production of a graph that portrays this link.
Criticisms of the MFR Test
At this point enters one of the universal criticisms of the MFR test. Critics indicate that while capillary rheometry offers an entire depiction of the link between viscosity and shear rate across a broad variety of conditions that reflect several different processes, the MFR depicts only one point on the curve.
This is right. The question is, “So what?” This criticism implies that the MFR test was developed to offer some sign of processability. That was not its main function. Rather, it is designed to offer an easy way to measure the relative average molecular weight (MW) of the polymer. With the decrease in MW, there is an increase in MFR.
As MW weight boosts the performance in polymeric materials, this is something that should be important.
When a polycarbonate supplier makes a series of grades differentiated mainly by their MFR, the products are recognized as per their average MW. Molecular weight has an effect on fatigue resistance, impact performance, environmental stress-crack resistance, creep resistance, and barrier properties. With higher MW, the performance is enhanced. When a supplier determines a specification range around a known nominal MFR value for a grade, it may not do well as it is all about how the material will be processed in a specific piece of equipment. The supplier supervises the MFR, as it is known that this is an indicator that the average MW of the material is under control and within the stipulated range.
Indeed, the real MFR has connotations for processing. Nobody would pretend that a polycarbonate with an MFR of 4 g/10 minutes would flow and cover the same distance through the same flow path and under the same molding conditions as the one with an MFR of 20 g/10 minutes. However, the actual difference in viscosity is not as great as these numbers would imply; this is because the difference in the flow rate automatically implies a difference in shear rate, and as the shear rate increases, the viscosity decreases.
The shear rate at which an MFR test is conducted is, in fact, proportional to the MFR value itself. The shear rate at which the test was carried out can be obtained by multiplying the MFR by approximately 2.2. Therefore, a 4-melt material is tested at a shear rate of approximately 8.8 seconds−1, while the 20-melt material is tested at 44 seconds−1. In addition to being different, these shear rates do not portray the shear rates experienced by polymers under a majority of the melt processes.
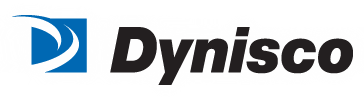
This information has been sourced, reviewed and adapted from materials provided by Dynisco.
For more information on this source, please visit Dynisco.