A few years back, the author got an indignant e-mail from someone challenging his statement that melt flow rate measurements typically offer a good evaluation of the relative average molecular weight of a polymer. They asked, how a flow-rate measurement given in units of grams/10 minutes could be converted to a measurement of molecular weight, which is expressed in grams/mole? Researchers have found an answer to this question.
Relationship Between Molecular Polymer Weight and Zero-Shear Viscosity
There is a strong link between what is called the weight-average molecular weight of a polymer and a parameter called the zero-shear viscosity. Although the correct link rather depends on the polymer, the prevalent equation that is available in the literature is:
h0 = kMw3.4
where h0 is the zero-shear viscosity, Mw is the weight-average molecular weight, and k is a constant that is specific to the polymer being assessed. The exponent 3.4 is not universally applicable; however, the values are likely to lie within the range of 3.2 to 3.9. In any case, this link evidently demonstrates that comparatively slight variations in molecular weight (MW) lead to great variations in melt viscosity when this viscosity is determined at a very low shear rate.
Zero-Shear Rate
Zero-shear rate is a concept that could only be loved by a mathematician. Practically, it is not possible to measure viscosity at a shear rate of zero since viscosity is a measurement of resistance to flow. Therefore, to measure the resistance to flow, the polymer flow must be created, and once it is done, the shear rate becomes some non-zero value. However, the logarithmic plots of viscosity versus shear rate are likely to stabilize as the shear rate reaches zero, therefore the curve can be extrapolated back to the y-axis to reach the value for zero-shear viscosity.
An actual viscosity/shear rate curve for a commercial acetal copolymer has a nominal melt flow rate (MFR) of 9 g/10 minutes and the measurements include shear rates from 1.4 to 1400 seconds−1. There is no change in the viscosity by a statistically considerable amount at shear rates between 1.4 and 7 seconds−1 before entering the so-called non-Newtonian region of the curve. The shear rate at which the MFR test is carried out on this material is around 20 seconds−1. It can be observed that the MFR test is carried out at a point very near to the plateau directing back to the zero-shear point on the curve.
Exaggerated Differences in Melt Viscosity
This shows the suitability of the MFR test in offering a relative measurement of the average MW of a polymer. As the MFR test is carried out at comparatively low shear rates, the outcomes approximate the zero-shear viscosity, measured at low shear rates, although the shear rate is not controlled. The shear rate is not controlled in an MFR test, suggesting that the test, in fact, exaggerates the real differences in melt viscosity that happen as a function of molecular weight.
This can be demonstrated by re-examining the viscosity versus shear rate curves for the two polypropylenes. It has been observed that the MFRs for the two materials usually indicate that the viscosity of the 4-MFR material is 5.5 times more than that of the 22-MFR resin.
However, if the viscosity of these two materials is compared at any particular shear rate, it can be observed that this is not the case. The major difference in viscosity between the two materials is witnessed at the lowest shear rate, and even at this point, the ratio of the two viscosities is hardly 3.5:1 (3460/1005 = 3.44).
It is important to note that with a higher shear rate, the difference in viscosity between the two materials reduces. At the highest shear rate on the graph of 10,000 seconds−1, the ratio has dropped to 18/13 or 1.38:1. As the materials flow faster, their viscosities appear to be more similar. This is due to the orientation of the long polymer chain, a phenomenon usually known as shear thinning. This behavior enables processors to move polymer melts to long distances through comparatively limiting flow paths, specifically in injection molding.
The MFR values imply a larger difference than those indicated by the viscosity measurements because the shear rate for the two MFR tests is different. The shear rates at which the MFR tests are carried out for the two materials are not controlled; they are a result of the rate at which the two materials flow under an unvarying load. However, as the shear rate for the test carried out on the 22-MFR material is considerably higher than that used for the 4-MFR material, the differences in viscosity are excessive. This is a known imperfection of the MFR test. However, it also portrays well the principle that variations in viscosity due to the changes in MW are most efficiently measured at low shear rates. With higher shear rates, materials with considerably different MW begin to look alike.
At the extreme values, commercial raw materials can be found with MFR as low as 0.1 g/10 minutes and as high as 500 g/10 minutes. However, for the large majority of commercial compounds with known MFR, the values lie within the range of 1 to 50 g/10 minutes. This implies that the shear rates of MFR tests normally lie within 2.2 and 110 seconds−1.
The overstated differences in melt viscosity yielded by the MFR test have an adverse impact on the processing community, specifically those processors involved with injection molding.
Processors are likely to think of the MFR values as being indicators of the real differences in the flow of the materials.
When molded parts fail to function as projected, one of the modifications that can be done to enhance performance is to increase the MW of the polymer being used to create the parts. In this case, a lower MFR material is used. Usually, this modification is ignored by the processor due to the expected increase in processing difficulty proposed by the difference in the MFR values. The viscosity curves indicate that the real differences in viscosity are not as great as those implied by the MFR values.
Conclusion
However, it is not easy to make people think outside of the MFR numbers. Several performance issues that could have been overcome with higher MW materials have rather been approached with complex modifications in part design and process conditions just because the MFR numbers seemed too daunting.
The reasons for the impression that MFR is a barrier to processing will be looked at and the reasons why processes that show sensitivity to lot-to-lot fluctuations in MFR have basic problems related to the molding machine or the way the process is set up will be explained.
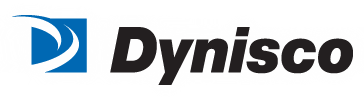
This information has been sourced, reviewed and adapted from materials provided by Dynisco.
For more information on this source, please visit Dynisco.