If you have spent hours looking at data sheets, you would have perhaps noticed a trend over the past several years in the way in which the melt flow rate (MFR) is reported. Instead of, or together with, the MFR, a new line item is present, known as the melt volume rate (MVR).
Value of Melt Volume Rate
While the MFR is given as a mass per unit time, such as grams/10 minutes, MVR is reported as a volume per unit time, such as cm3/10 minutes or, regrettably, inches3/10 minutes. It is unfortunate because one of the areas where the United States is out of step with the rest of the world is in its use of the ancient inch-pound system of units in contrast to the SI units or metric system. For the past two decades, billions of dollars have been spent in adopting ISO standards for just about everything done in the industry; however, all are not comfortable with leaving the very old system of units, with notable exceptions such as the automotive industry, where the change to SI units has been effectively mandated.
However, there are a few regions where everyone seems comfortable with the alternatives and one of them is the usage of grams as the unit for mass and g/cm3 as the unit for density. In a majority of the plants, while weighing parts, the results are recorded in grams. Moreover,and lists only the density of a material in a data sheet would be given in g/cm3. Therefore, it is rather a mystery as to why one would take an extra effort to return to a unit of flow that uses cubic inches instead of cubic centimeters. Think of the confusion that would happen if all of a sudden everyone starts reporting the density of polyethylene in lb/inches3 and a 0.955 density HDPE became a 26.437 HDPE. Inches3/10 minutes can be converted to cm3/10 minutes by just multiplying it with 16.4.
MFR to MVR Conversion
If the material supplier offers both MFR and MVR data, once this conversion is made, it can be noticed that the numbers are similar but usually not identical. The ratio of the two values—the MFR divided by the MVR — is a measure of the melt density of the material in g/cm3. This is a key property as it is a different number from the solid-state density that is usually given on the data sheets.
For instance, unpigmented or unfilled polycarbonate has a solid-state density of 1.20 g/cm3, whereas the melt density of the material is 1.08 g/cm3, or 90% of the solid-state density. This value is practically significant. Firstly, melt density is a property input for flow-simulation software. Furthermore, it is a key conversion factor for establishing the capacity of an injection unit on a molding machine. Most of the people in the industry know that the shot sizes are mentioned in terms of general-purpose PS.
However, when converting from PS to, for instance, PE, the trend is to multiply by the ratio of the density values given on the data sheet. Therefore, a 30 oz barrel would be assumed to hold 27.5 oz of 0.955 HDPE. However, these are solid-state densities and polymers are not solid when they are inside the barrel, or at least it is hoped not. As the melt density of HDPE is just 80% of the solid-state density, the barrel capacity in HDPE is, in fact, a bit less than 24.5 oz.
Reasons for Converting to MVR
There are some logical reasons for converting to MVR.Firstly, all of the equations in rheology that include a term for flow rate use a volumetric flow rate rather than using a mass flow rate. To be more practical, MFR — referred to as a melt mass flow rate by ISO standards — does not correct for the density of the material and so alters the real rate at which the material flows through the instrument. Denser materials seem to flow more rapidly just because the material obtained from the instrument is heavier.
Assume two PCs, one white and the other black. The white pigment may be TiO2 — a pigment with a density that is more than three times as high as that of the polymer. If it is added at a loading of 4%, it can increase the density of the final compound by around 10%. The black pigment is likely to be carbon black, which has typically the same density as the polymer and thus does not affect the density of the final compound. MFR tests that exhibit a 10% higher value for the white material would seem to imply that the white material is of a lower average molecular weight when actually the two materials would look similar when observed in terms of MVR.
For materials with a melt density of 1 g/cm3, the MFR and the MVR will be identical. However, this does not happen too often. Therefore, if a supplier for a particular material lists only MFR or only MVR, the melt density of the polymer must be known in order to convert.
Luckily, the MFR test, when operated in a specific way, can offer this property. The piston that is used to drive the material through the orifice has two scribes on it that are precisely 1 inch (2.54 cm) away. The instrument can be configured to start monitoring the test when the piston travel arrives at the first scribe line and the test will end when the piston arrives at the second line. As the diameter of the cylinder is closely specified at 0.95504 + 0.00254 cm, the volume related to this displacement can be easily calculated at 1.819 cm3.
The melt density of any material can be estimated by weighing the extrudate that comes out of the orifice at the time of this displacement. For instance, unpigmented, unfilled PC has a melt density of 1.08 g/cm3; therefore, the mass of material displaced by this 1 inch travel should be 1.965 g with allowances for slight changes because of the actual size of the bore and the precision of the operator carrying out the test.
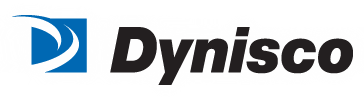
This information has been sourced, reviewed and adapted from materials provided by Dynisco.
For more information on this source, please visit Dynisco.