Although the melt flow rate test, or MFR test, is very useful, it is not widely applicable. Primarily, the objective of the test is to record the variations in molecular weight. The interpretation of the results can be made difficult by various factors. The first factor includes the polymers that do not break down initially via chain scission. The chain scission is the chemical reaction by which the polymer chains become shorter.
Examples of Factors Affecting the Interpretation of MRF Test results
PVC
One good example is PVC. Degradation in PVC starts with a process called dehydrochlorination, a striking term for the loss of hydrogen chloride. When the hydrogen and chlorine atoms detach from the polymer backbone, double bonds are created, which results in a change in color. However, the oxidation that triggers chain scission may not start until the loss of hydrogen chloride has advanced to a considerable degree. Thus, the polymer may have experienced substantial alteration without providing any signs of a decrease in molecular weight.
A second challenge is posed by competing reactions that can simultaneously increase and reduce the molecular weight of the polymer. Polymers like polyesters and nylons can experience a range of complex reactions that can result in this kind of behavior.
PBT Polyesters
The associated chart represents a comparison of two different PBT polyesters assessed in the melt state over time. The measurement of melt viscosity of the materials was taken periodically with the help of a capillary rheometer working at a constant shear rate. One of the materials exhibits outstanding stability and the viscosity varies very slightly over the course of the test. However, the other material first goes through a quick decline in viscosity, which is a characteristic of chain scission, followed by an increase in viscosity, ascribed to a process of crosslinking boosted by the oxidation that resulted in the initial degradation of the polymer chains.
MFR tests carried out on samples obtained from different points along this timeline would create extremely different impressions of the condition of the polymer. A sample taken at 20–25 minutes into the evaluation would exhibit major polymer degradation, a sample taken at 40 minutes would not exhibit any change, and a sample taken at 55 minutes would seem to indicate that the molecular weight had increased despite that a part molded from material in this condition would be very brittle.
Impact-Modified Materials
Even impact-modified materials can give a comparable effect for the same reason. Both EPDM rubber and butadiene rubber are generally used as impact modifiers. Both of these materials can experience crosslinking when subjected to increased temperatures. This can, in fact, reduce the MFR of these materials during processing, a behavior that is often seen in materials such as PPE/HIPS blends, ABS, and impact-modified nylon.
The response of the material to processing can be further complicated by other constituents such as flame retardants. Generally, if there are more ingredients in the compound, it is more difficult to make an easy interpretation of the MFR test results.
Impact of Fillers
The impact of fillers is one good example of this principle. Fillers tend to increase the melt viscosity of a polymer rather than melting at processing temperatures. This increase can be detected at any shear rate; however, it is more obvious at low shear rates where the lack of orientation makes the fibers or filler particles increasingly more resistant to flow. The issue with comparing the MFR results of parts and pellets when fillers are present relates to the impact of the process on the integrity of the filler. This is particularly true of reinforcements like glass fiber.
It is well-known that processing can reduce the length of the polymer chain, and this is the main area of interest when conducting MFR tests on molded parts and the associated raw materials. However, high-shear processes like injection molding also decrease the length of the fiber, and this decrease also contributes to the variation in the MFR measurement. Whenever MFR tests are conducted on glass-filled materials, the measurement is a combination of the response from the polymer and the fiber. With the increase in the fiber content, the contributions from this ingredient also become more significant.
Fiber Length Reduction
During molding, the reduction of fiber lengths by 50% is usual. When compared to the longer fibers in the original raw material, these shorter fibers flow more easily through the MFR tester. Therefore, the 40% rule discussed previously cannot be applied to filled materials. Before one could worry about polymer degradation, the increase in MFR may reach as high as 75% even at a 10% loading of glass fiber. The permissible MFR increase may reach as high as 200% by the time 30% glass content is achieved. The changes between these standards and the 40% value used for assessing unfilled materials are developed to make allowances for the impact that typical fiber-length reduction has on melt viscosity. When working with long glass fibers, the ambiguity becomes even greater, while particulate fillers such as talc may introduce a smaller variance from an unfilled product.
Preferably, MFR tests are not conducted on filled materials; instead, the solution-based measurements are used, which work by dissolving the polymer in a solvent and eliminating the filler so that only the polymer is being considered. However, the MFR test can be accessed and performed so easily that many suppliers of filled materials still employ MFR as their quality-control parameter for average molecular weight. Thus, it is useful to have a method of enabling the contribution of fiber-length reduction on the MFR of a filled material.
Acetal, more widely referred to as POM these days, poses a different issue. Usually, MFR is employed to distinguish between the grades of this material. Yet, it has been demonstrated that the MFR test is not helpful for detecting the degradation of process-induced polymer in POM/acetal. Actually, even more advanced methods such as gel permeation chromatography (GPC) do not frequently exhibit any measurable variation in the molecular weight (MW) of this polymer.
This is due to the fact that the rate of MW reduction in acetals is so fast at processing conditions that any polymer chains that start to unzip reach an MW that is so low that they do not impact the melt viscosity of the polymer anymore. A degraded acetal does not have a considerable amount of intermediate chain lengths. Although there are different analytical methods that can detect degradation in POM, common MW determinations such as solution viscosity, MFR, and GPC are ineffective.
However, degradation of acetal that takes place in the solid state occurs quite slowly to create a considerable amount of intermediate chain lengths. An excellent example is sustained exposure to hot water, specifically if the aqueous environment is slightly acidic. In this condition, the reduction in average MW is adequately slow to form the type of lower-MW components that the MFR test is intended to detect. In one instance, an acetal homopolymer showed a 100% increase in MFR from as-molded parts to parts that had been submerged in water at 90 °C for 1000 hours.
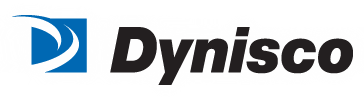
This information has been sourced, reviewed and adapted from materials provided by Dynisco.
For more information on this source, please visit Dynisco.