For almost 60 years heat shrink materials have been known and commercially available. Most people are familiar with “shrink wrap”, and a lot of us have even used heat shrinkable tubing for repairs on our car or around our home. The heat shrink materials industry has grown to a global enterprise whose value is in the billions of dollars (US) today, stemming from the observation of the peculiar effects of radiation upon plastics [1].
Heat shrinks are utilized for applications ranging from form-fitting wire insulation to food wrapping, sterilization protection and packaging, sensor and connector encapsulation, to aerospace and medical device industries.
Other than their copious uses, heat shrink materials have opened new avenues of discovery in both radiation effects and material behavior. Indeed, continued study has shown key insights that continue to be carried forward for today’s and the next generation’s advanced materials.
Origin and Invention
Heat shrink technology as it is known today can be traced back to the early post- World War II era. Scientists started to take notice of the effect of radiation on a variety of materials, including polymers, as nuclear energy programs sprang up in the United States and elsewhere during this time.
In the 1950s, one of these scientists was Paul Cook working out of Stanford University. He was especially interested in the effects of ionizing radiation upon plastics. Cook and some others found after being exposed to radiation, that some plastics took on a heat shrinkable quality [2, 3].
Cook soon commercialized his discovery by starting his own company (later to become Raychem). Whilst other researchers soon followed his invention, he is largely given credit for bringing heat shrinkable materials to a commercial market. Heat shrinkable tubings and wrapping were available to the public by the early 1960s. Numerous innovations and variations on heat shrinkable products have resulted in continuous growth in this industry ever since.
Technology Beginnings
Heat shrinkable materials are part of a bigger group of materials that display shape memory. These materials have the ability to change from a permanent (original) shape to a temporary (deformed) shape and then back to their permanent shape to varying degrees after the application of some stimulus [4, 5].
This feature is termed the shape memory effect (SME), and materials with this capability are collectively known as shape memory materials (SMMs). These materials were first detailed as early as the 1930s in metal alloys (later termed shape memory alloys – SMAs) [6]. Shape memory was discovered in polymers later in the 1940s, [7].
Interest in these shape memory polymers (SMPs) grew quickly in large part because of the easier processing of plastics and polymer-based materials compared to metals and the overall lower cost SMPs [8]. Interest in SMPs has thus surpassed that of SMAs leading to the vast commercial enterprise surrounding SMPs.
More on the Shape Memory Effect
After being deformed and after a particular stimulus is applied to the material, shape memory materials have the ability to go back to their original shape. The stimulus can be of a range of things including light (such as infrared or UV), chemical exposure (such as water or other liquid), or acid-base change (pH) [9-13].
The obvious stimulus is heat in the case of heat shrink tubing – a highly common shape memory application [4, 14, 15]. SMPs can also be designed to respond to more than a single stimulus [16]. In this way, SMPs supply an adept means to affect localized and acute stimulus to direct re-formation of the original shape.
General Mechanism
The process involved in heat shrinkable materials and SME is complex, but some commonalities can be discussed. Solid phase polymers possess crystalline and amorphous regions for heat shrink polymers (HSPs). HSPs are also almost always crosslinked to enhance their heat shrinkabilty.
SME and HSPs can be modeled as a two component system. The amorphous polymer chains represent an elastic component – because they are not constrained as those in the crystalline phase, and the crystalline regions represent a reversible transition component (Fig. 1) [17]. The material will not possess heat shrink qualities without elastic and rigid (transition) components [18].
Using naive heat shrinkable polymer tubing for example, the tubing is exposed to a crosslinking agent such as an electron beam (e-beam) after extrusion to crosslink individual polymer chains (Fig. 1A). Next, the tubing is heated to just over its melting temperature and mechanically expanded (deformed, radially) (Fig. 1B).
Expanding the tubing also generates some crystallite and amorphous chain alignment from being drawn radially. The tubing is held in its expanded state and cooled to room temperature quickly. The transition component reforms as crystallites as cooling takes place. The elastic component – the amorphous chains – are stretched in the expanded state, and the fast cooling results in confined or limited amorphous chain mobility.
The rapid cooling locks the tubing in its expanded state and provides it its ability to alter its shape [19]. This fixing of a new temporary shape of the tubing is known as the programming step. Crystallites melt along with the amorphous regions with subsequent heating to just over the melt temperature. Melting permits the elastic component – stretched and strained amorphous chains – to relax and revert to, or recover, their original shape (Fig. 1C).
The crystalline and amorphous regions become less oriented and more compact than in the expanded state [19]. Transition element crystallites are created more efficiently with the slower cooling further locking the shrunken or recovered tubing back in its original shape. (As a note, SME can also be triggered by the glass transition temperature, but this is not the mode for heat shrink materials.)
Thus, the temperature at which the tubing starts to return to its original shape is called its recovery temperature, and the reheating of the expanded heat shrink is called the recovery step. Together, the programming and recovery steps make up the shape memory cycle.

Figure 1. Transition and elastic components of HSPs. Using heat shrinkable tubing as an example, amorphous polymer chains (black lines) provide the elastic component for the expanded tubing. Elastic component energy is supported by crosslinking of polymer chains (blue dots). Crystallites (black rectangles) form the reversible transition component. (A) Unexpanded tubing shows only crosslinking. (B) Programming: The tubing is heated to just above its melt temperature and expanded. Held in its expanded shape, the tubing is then quickly cooled to lock the stretched polymer chains in place storing elastic energy. (C) Recovery: With the application of heat to the cooled and expanded tubing, the stretched amorphous chains are freed by melting and recover their original (unexpanded) permanent shape. In the recovered state, the polymer chains are more disordered and compact.
Crosslinking
A key factor that SMMs share is that to return them to their permanent shape from the deformed temporary shape they need a driving force. The transition from a temporary to a permanent shape can be seen as an energy barrier which must be overcome to affect the transition [20]. Heat shrink materials are similar to rubbers and elastics in this way.
This energy barrier is high for heat shrinks, which undergo a temporary-to-permanent transition; the energy barrier is low for rubbers and other more elastic-like materials [20]. For SMMs, and especially heat shrinkable materials, the driving force to return the deformed shape back to its permanent shape comes from the stretched amorphous chains – but with a variation.
Heat shrink materials, for example heat shrink tubing or wrap, feature their polymer chains crosslinked – adjacent chains connected to each other at the molecular level. Crosslinking gives greater elastic recovery force.
Crosslinking can be achieved in numerous ways. Very long chain polymers can experience entanglement from polymer chains crossing over one another resulting in a kind of physical crosslinking (Fig. 2A). Additionally, there is chemical crosslinking (Fig. 2B). Historically, the addition of chemical linkers or additives was needed to crosslink polymer chains using this method.
Yet, exposing polymers (plastics) to ionizing radiation also induces crosslinks in the chains; this was the observation made by scientists (ca. 1940s) as nuclear facilities became more available to research and public interests. The formation of covalent bonds in bulk material without a chemical additive and creation of crosslinked polymers was quite surprising to researchers at the time [21].
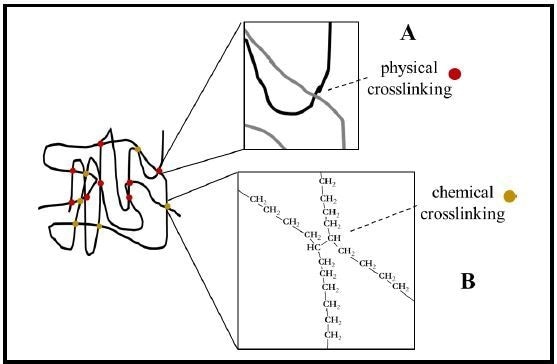
Figure 2. Crosslinking of HSP chains. Crosslinking provides the elastic recovery force for heat shrinkable materials such as tubing. Crosslinking may be either physical crosslinking (A and red dots) from overlapping polymer chains and entanglement or chemical crosslinking (B and gold dots) via a direct chemical bond between adjacent polymer chains. (Example shown: polyethylene).
Crosslinking of HSPs is crucial to impart heat shrinkability and supplies a number of benefits to the material. Crosslinking creates a denser polymer chain network, heightening the potential to store elastic energy. Crosslinking also stops long range chain slippage when under strain. Restricting chain slippage helps to ensure that any shape alteration is the result of entropy change, which is recoverable [18].
The greater the extent that chain slippage can be avoided (within the elastic range of the elastic component), the greater the potential HSP recovery. Crosslinked materials also usually show improved resistance to impact and stress cracking and may even exhibit better chemical resistance [22].
In particular, for heat shrink materials, the most typical technique for crosslinking is via radiation such as from an e-beam. Irradiating polymers induces the formation of radicals (unpaired valence electrons) resulting in the formation of covalent bonds between adjacent polymer chains (Fig. 3).
This type of radiation crosslinking is usually carried out under vacuum or in an inert atmosphere and has been proven to be particularly useful. (Irradiating in air or in the presence of oxygen can result in unwanted oxidative degradation.) E-beam crosslinking is both quick and uniform and is comparatively less expensive than utilizing chemical additives [23].
Radiation crosslinked polymers typically have more strength and preferred properties at higher temperatures compared to their non-crosslinked versions [22]. Crucially, effects upon polymers can be controlled by dose rate, radiation intensity, and exposure time permitting some tailoring of the crosslinked material properties.
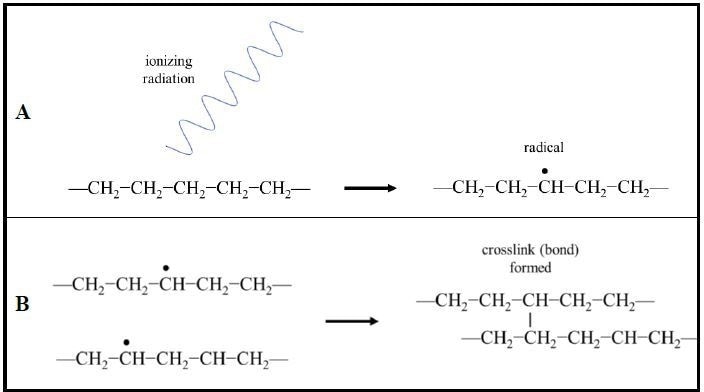
Figure 3. Radiation crosslinking of polymer chains. (A) Ionizing radiation induces the formation of radicals (unpaired valence electrons) in the polymer chains. (B) Radical electrons pair and form covalent bonds between neighboring polymer chains creating crosslinking. (Example shown: polyethylene).
Irradiating polymers can also have the opposite effect of crosslinking: chain scissioning. Crosslinking is necessary for heat shrink materials. For other applications, chain scission is the goal and has been utilized to significant advantage in the creation of materials with unusual or improved properties [22].
Some polymers are more predisposed to crosslinking whilst others tend towards chain scission, and some reference materials exist detailing these. (For polymers with double bonds, branching may also happen.) However, it is not unusual for crosslinking, scissioning, and oxidation to happen simultaneously during irradiation [24]. So, experimental and environmental factors, can be employed to influence the preferred outcome of the irradiation [22].
Practical Considerations
With a basic understanding of heat shrink materials, there are numerous factors that should be considered before use. For heat shrink tubing, the user should be well-versed in the application intent at the outset. A good understanding of the potential hazards that the heat shrink must endure is crucial for long usage and successful application.
Chemical hazards, including moisture, figure prominently in the choice of heat shrink material. Temperature tolerance, electrical aspects, and toughness of the material are also crucial. These and more should be explored carefully to choose a heat shrink which is most appropriate for the application.
Component Shape and Heat Shrink Ratio
A key consideration for a heat shrink tubing is the shape of the part or component to be covered. Heat shrink ratio – the ratio of the expanded inside diameter (ID) of the tubing compared to its final recovered ID – is important here.
Smooth, linear parts like wire splices or mandrels can use smaller shrink ratios than parts with more irregular and angular geometries. While some heat shrinks can be created with up to a 6:1 ratio, not all polymer materials are capable of a ratio this big. So, heat shrink ratio can be a limiting factor for the selection of heat shrink material and it should be weighed against part shape.
Shrinkage
Users should consider the final dimensions of the heat shrink product aside from the heat shrink ratio. Although heat shrink tubing is expanded radially imparting some radial polymer alignment within the material, recovery culminates in the loss of much of this alignment. So, in addition to the circumferential shrinkage, there is likely to be some longitudinal shrinkage.
Furthermore, shrinkage will affect wall thickness of the tubing. If wall thickness is not taken into account properly and an inappropriately thin walled heat shrink tubing is employed, as the material stretches over the covered component shrinkage may result in a recovered wall thickness approaching nil.
Electrical Considerations
A big part of the heat shrink tubing market is devoted to wiring and electrical applications. Users prefer heat shrink tubing that not only protects or secures wiring connectors and splicing but also gives some level of insulating capability. There will be regulatory provisions that must be met for applications where insulation is required.
These requirements also may be unrelated to insulation per se such as UL 94 flammability requirements when utilized over wires. For example, some polymer heat shrinks with the preferred electrical properties may not be permitted under certain regulatory guidelines. So, electrical considerations for heat shrinks may extend just beyond their dielectric properties.
Application Environment
One of the most important considerations for heat shrink materials is the environment where they will be deployed. Obvious elements such as the chemical environment and temperature are important but should not overshadow other factors. The applied heat shrink may be subjected to physical trauma such as abrasion, scraping, or vibration for example.
Rough handling and repeated deployments of the heat shrink covered components may also pose problems for the wear and tear on the heat shrink. Whether the working environment is brightly lit or dark or whether transparency or color coding is needed can also be significant concerns. Whether or not the heat shrink will be exposed to radiation is also important.
These factors and more highlight the importance of a thorough understanding of the environment before beginning the selection of the best heat shrink material.
Cost
The cost of heat shrink applications can also be a deciding concern. For some applications, it may be viable to sacrifice certain heat shrink performance attributes in exchange for a cheaper material. Yet, it may be advantageous in the long run to opt for a more expensive heat shrink to achieve better performance.
Factors such as frequency of use, the ability to redeem used heat shrink material through a recycler, and usage life, can influence the overall costs of a heat shrink application. Additionally, disposal costs may also factor into the selection of heat shrink.
As plastic waste continues to accumulate globally, steps that can mitigate this trend will pay dividends in the short and long term. These factors can have a huge impact on attaining a heat shrink that excels in the application at an optimal cost.
Optimizing Recovery
The importance of achieving optimal recovery is an often underappreciated matter for heat shrinkable material. Uniform heating is crucial in this regard. Heating techniques differ and have certain advantages and disadvantages. For example, ovens supply even heating but are only convenient for discrete lengths and are not portable.
On the other hand, heat guns, can be utilized in the field but can be challenging to attain uniform heating. To address uneven heating users regularly modify heat sources such as heat guns with attachments with varying degrees of success. Heat rings give uniform heating but are limited by their diameter and need stable positioning of the parts to be covered and the heat ring.
Traversing heat sources supply even and steady heating but are also limited in portability. To address these concerns any heat shrink application should start with a series of optimization trials. During the optimization phase allowance for waste should be incorporated. Adopting these first steps will significantly shorten the time to devise an optimum heat shrink recovery method for the application.
Summary
Heat shrinkable products have proven to be a boon not only economically but also to many innovative industries that have discovered new and creative ways to utilize them. The discovery of radiation-crosslinked polymers has broken new ground for the study of SMMs and HSPs. In very short order highly practical applications such as heat shrinkable wrap and tubing have become available commercially.
With their simpler processing needs over SMAs, HSPs and products proliferated permitting accelerated study into the structural rearrangement happening throughout the heat shrink recovery process. The essential nature of crosslinking helped to focus a mechanistic understanding of SME, in addition to the heat shrink recovery process.
HSPs can be described principally as a two component system possessing a reversible transition component and an elastic component. Irradiation of polymers is now commonplace not only to create heat shrink materials but also for increasing material properties for applications unrelated to heat shrinks.
With the plethora of heat shrinks now available, it is incumbent upon end users to understand their application intent, working environment, and how best to recover the heat shrink. Appropriate preparation at the start will go a long way towards maximizing the benefits of a heat shrink application.
References
1. Polyolefin (POF) Shrink Film Market Analysis By Product (General, Cross-linked), By Application (Food, Beverage, Industrial Packaging, Pharmaceuticals, Consumer Goods), By Region, And Segment Forecasts, 2018 – 2025. In.; 2017.
2. Makuuchi K, Cheng S: Radiation Processing of Polymer Materials and Its Industrial Applications: Wiley; 2012.
3. Charlesby AE: Atomic Radiation and Polymers. New York: Pergamon; 1960.
4. Wayman CM, Otsuka K: Shape memory materials Cambridge, New York: Cambridge University Press; 1998.
5. Lendlein A, Kelch S: Shape-Memory Polymers. Angewandte Chemie International Edition 2002, 41(12):2034-2057.
6. Chang LC, Read TA: Plastic Deformation and Diffusionless Phase Changes in Metals — the Gold- Cadmium Beta Phase. Journal Of Metals 1951, 3(1):47-52.
7. Vernon LB, Vernon HM: Process of manufacturing articles of thermoplastic synthetic resins. In: USPTO. USA: Vernon Benshoff Co.; 1941.
8. Huang WM, Ding Z, Wang CC, Wei J, Zhao Y, Purnawali H: Shape memory materials. Materials Today 2010, 13(7):54-61.
9. Huang WM, Yang B, Zhao Y, Ding Z: Thermo-moisture responsive polyurethane shape-memory polymer and composites: a review. Journal of Materials Chemistry 2010, 20(17):3367-3381.
10. Garces IT, Aslanzadeh S, Boluk Y, Ayranci C: Effect of Moisture on Shape Memory Polyurethane Polymers for Extrusion-Based Additive Manufacturing. Materials (Basel, Switzerland) 2019, 12(2):244.
11. Chen H, Li Y, Liu Y, Gong T, Wang L, Zhou S: Highly pH-sensitive polyurethane exhibiting shape memory and drug release. Polymer Chemistry 2014, 5(17):5168-5174.
12. Fang L, Fang T, Liu X, Ni Y, Lu C, Xu Z: Precise stimulation of near-infrared light responsive shape-memory polymer composites using upconversion particles with photothermal capability. Composites Science and Technology 2017, 152:190-197.
13. Landlein A, Jiang H, Junger O, Langer BR: Light-induced shape memory polymers, vol. 424; 2009.
14. Chatterjee T, Wiessner S, Bhardwaj YK, Naskar K: Exploring heat induced shape memory behaviour of alpha olefinic blends having dual network structure. Materials Science and Engineering: B 2019, 240:75-84.
15. Chatterjee T, Dey P, Nando GB, Naskar K: Thermo-responsive shape memory polymer blends based on alpha olefin and ethylene propylene diene rubber. Polymer 2015, 78:180-192.
16. Pilate F, Mincheva R, De Winter J, Gerbaux P, Wu L, Todd R, Raquez J-M, Dubois P: Design of Multistimuli-Responsive Shape-Memory Polymer Materials by Reactive Extrusion. Chemistry of Materials 2014, 26(20):5860-5867.
17. Wu X, Huang WM, Zhao Y, Ding Z, Tang C, Zhang JL: Mechanisms of the Shape Memory Effect in Polymeric Materials. Polymers 2013, 5(4):1160-1202.
18. Xie T: Recent advances in polymer shape memory. Polymer 2011, 52(22):4985-5000.
19. Wang F, Zhang R, Lin A, Chen R, Wu Q, Chen T, Sun P: Molecular origin of the shape memory properties of heat-shrink crosslinked polymers as revealed by solid-state NMR. Polymer 2016, 107:61-70.
20. Huang WM, Song CL, Fu YQ, Wang CC, Zhao Y, Purnawali H, Lu HB, Tang C, Ding Z, Zhang JL: Shaping tissue with shape memory materials. Advanced Drug Delivery Reviews 2013, 65(4):515-535.
21. Chapiro A: The contribution of arthur Charlesby to the radiation chemistry of polymers—personal experience. Radiation Physics and Chemistry 1998, 51(1):9.
22. Clough RL: High-energy radiation and polymers: A review of commercial processes and emerging applications. Nuclear Instruments and Methods in Physics Research Section B: Beam Interactions with Materials and Atoms 2001, 185(1):8-33.
23. Mishra JK, Chang Y-W, Lee BC, Ryu SH: Mechanical properties and heat shrinkability of electron beam crosslinked polyethylene–octene copolymer. Radiation Physics and Chemistry 2008, 77(5):675-679.
24. Spadaro G, Alessi S, Dispenza C: Ionizing radiation-induced crosslinking and degradation of polymers In: Applications of ionizing radiation in materials processing. Edited by Sun Y, Chmielewski AG, vol. 1. Warszawa: Institute of Nuclear Chemistry and Technology; 2017: 167-182.
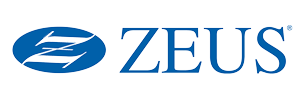
This information has been sourced, reviewed and adapted from materials provided by Zeus Industrial Products, Inc.
For more information on this source, please visit Zeus Industrial Products, Inc.